Injection Molding Materials
Harness decades of specialized expertise in advanced plastic injection molding materials and technologies, meticulously engineered by KingStar Mold, to transform your visionary concepts into tangible, precision-crafted products. Our team empowers you to leverage cutting-edge polymer science, industry-leading material formulations, and state-of-the-art manufacturing processes—ensuring every component meets exacting standards for durability, functionality, and aesthetic excellence. Whether you’re developing complex prototypes or scaling high-volume production, we collaborate closely with you to optimize design feasibility, material selection, and cost efficiency, turning imagination into reality. Trust KingStar Mold’s proven mastery in thermoplastics, elastomers, and engineered resins to deliver unmatched quality, consistency, and innovation for industries ranging from automotive to medical devices. Let’s pioneer solutions that exceed expectations, together.
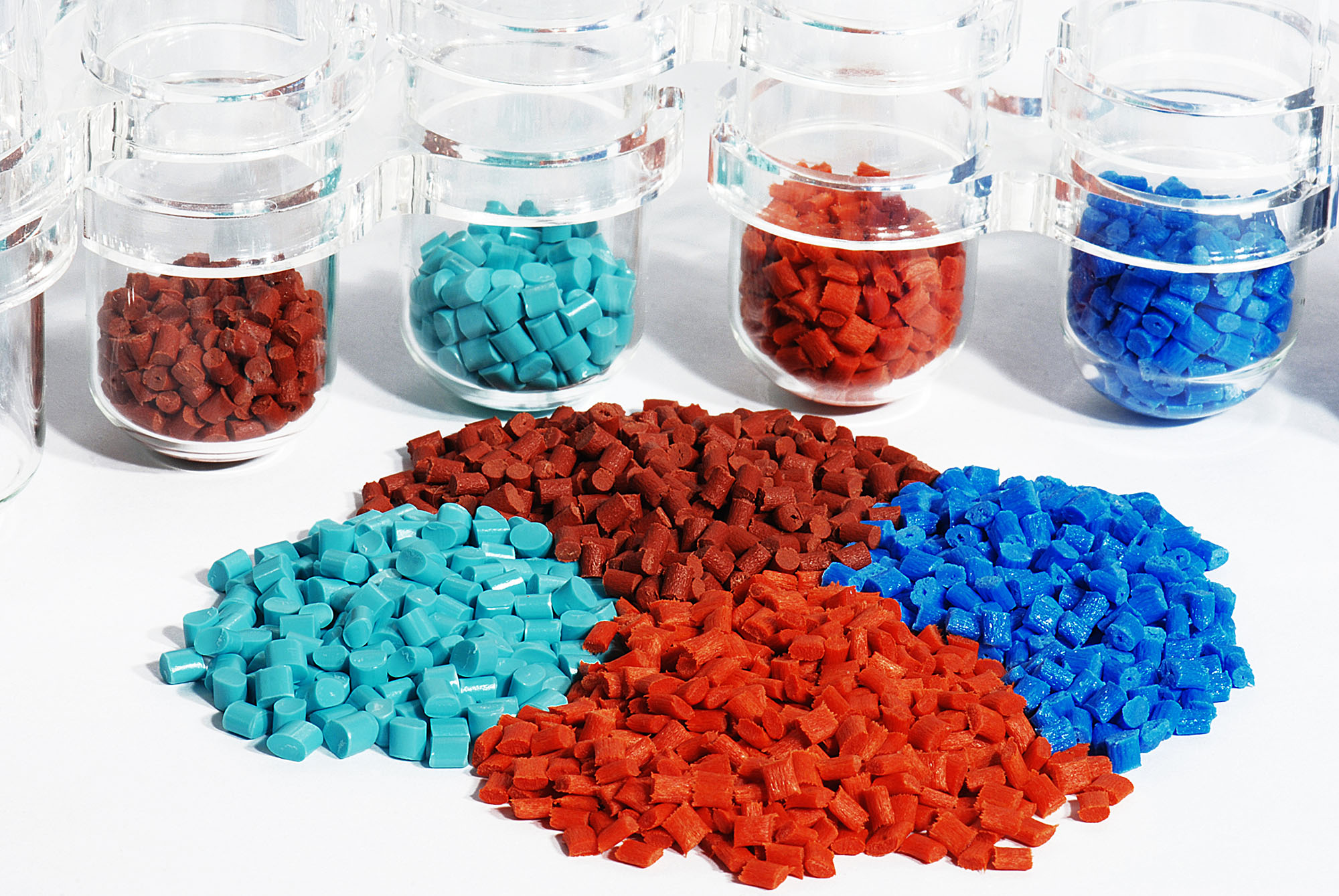
Diverse Material Options
Tailored Solutions for Optimal Performance
At KingStar Mold, we offer a broad selection of injection molding materials to meet the unique demands of various industries. From durable thermoplastics like ABS and polycarbonate to high-performance materials such as PEEK and PPS, we ensure that our clients have access to the right material for their specific application. Whether you require flexibility, high heat resistance, or strength, our diverse material range covers everything from standard plastics to specialized compounds.
Choosing the right material is critical for achieving optimal part performance and cost-efficiency. At KingStar Mold, we work closely with our clients to recommend the most suitable material based on their project requirements, such as mechanical properties, environmental resistance, and ease of processing. Our team is committed to providing expert guidance to help you select the perfect material that enhances the quality, durability, and functionality of your injection-molded parts.
Comparison Between Different Types of Materials
Material | Density (g/cm³) | Tensile Strength (MPa) | Yield Strength (MPa) | Hardness (Shore D) | Applications | Characteristics |
---|---|---|---|---|---|---|
ABS | 1.04 | 40-70 | 25-45 | 70-80 | Automotive, Consumer Goods | Good impact resistance, easy to process |
PA (Nylon) | 1.13 | 60-90 | 40-70 | 75-85 | Automotive, Industrial Parts | Strong, wear-resistant, high fatigue strength |
PBT | 1.31 | 55-75 | 40-60 | 80-90 | Electrical, Automotive | High heat resistance, low moisture absorption |
PC | 1.20 | 60-70 | 60-80 | 80-85 | Electrical, Optical | High transparency, excellent impact resistance |
PE | 0.94 | 20-40 | 15-30 | 60-70 | Packaging, Consumer Goods | Lightweight, good chemical resistance |
PMMA | 1.19 | 70-100 | 50-70 | 85-90 | Optical, Display Panels | Transparent, excellent UV resistance |
POM (Acetal) | 1.41 | 60-85 | 50-70 | 80-90 | Automotive, Industrial | Excellent dimensional stability, low friction |
PP | 0.90 | 30-50 | 20-40 | 70-80 | Packaging, Automotive | Light, chemically resistant, cost-effective |
PPS | 1.38 | 70-120 | 50-90 | 90-95 | Automotive, Electronics | High thermal stability, excellent chemical resistance |
PS | 1.05 | 40-60 | 30-50 | 70-80 | Consumer Goods, Toys | Rigid, easy to process, cost-effective |
TPU | 1.20 | 40-60 | 20-40 | 80-85 | Footwear, Medical | Flexible, excellent abrasion resistance |
PTFE | 2.20 | 25-40 | 20-30 | 60-75 | Automotive, Aerospace | High chemical resistance, low friction |
PPSU | 1.38 | 80-110 | 70-100 | 90-95 | Aerospace, Medical | High-temperature stability, excellent chemical resistance |
PVC | 1.40 | 40-60 | 25-40 | 70-80 | Plumbing, Electrical | Good chemical resistance, rigid |
PEEK | 1.30 | 90-120 | 70-100 | 85-90 | Aerospace, Medical | High strength, heat-resistant, expensive |
PEI (Ultem) | 1.27 | 90-130 | 70-110 | 85-90 | Aerospace, Electronics | High thermal stability, flame-retardant |
ABS/PC Blend | 1.12 | 60-80 | 50-70 | 75-85 | Automotive, Consumer Electronics | High impact resistance, heat resistance |
POM/PA Blend | 1.28 | 70-90 | 60-80 | 80-90 | Gears, Automotive Components | Low friction, high strength, wear resistance |
PBT/PC Blend | 1.25 | 70-90 | 60-80 | 80-90 | Electrical Connectors, Automotive | Strong, durable, high thermal stability |
PPS/PEEK Blend | 1.34 | 100-140 | 80-110 | 90-95 | Aerospace, High-performance Parts | Excellent chemical resistance, high thermal stability |
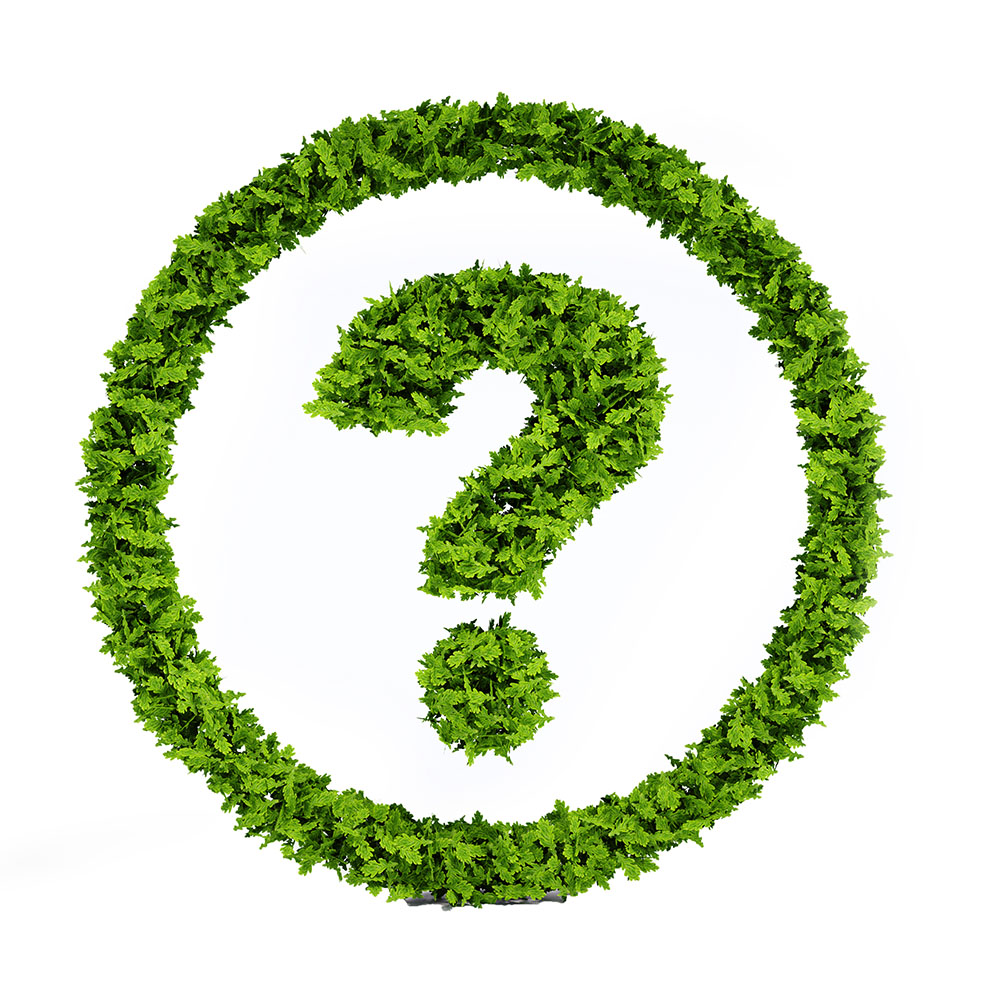
Materials like PEEK, PP, PVC, and PEI are frequently used for medical devices due to their biocompatibility, sterilization capabilities, and durability.
Yes, our experts will help guide you in selecting the most suitable material tailored to your specific project needs, ensuring both cost-effectiveness and performance.
Automotive parts often use materials like ABS, PBT, PA (Nylon), and PC for their impact resistance, durability, and heat tolerance.
KingStar Mold sources materials from reliable suppliers and conducts rigorous quality control to ensure they meet industry standards and performance requirements.
For high-temperature applications, materials like PEEK, PPS, and PEI are ideal due to their excellent heat resistance and thermal stability.
KingStar Mold’s team carefully reviews your project’s requirements to recommend the best material based on strength, flexibility, heat resistance, and chemical properties.
Injection molding materials are used in industries like automotive, electronics, medical devices, consumer goods, and packaging.
Thermoplastics can be re-melted and reshaped, while thermosetting plastics solidify permanently after molding. We offer both options based on your project needs.
We use a variety of materials, including thermoplastics like ABS, PA, PBT, PC, and PE, as well as high-performance materials such as PEEK, PPS, and PEI.
Key factors to consider include mechanical properties (strength, flexibility), environmental factors (heat, UV exposure), and the specific demands of your application, such as chemical resistance or biocompatibility.
Yes, for aerospace applications, we use high-performance materials such as PEEK, PPSU, and PEI, which offer superior strength, temperature stability, and chemical resistance.
Materials like PMMA (Acrylic) and certain grades of PC (Polycarbonate) offer excellent UV resistance, making them ideal for outdoor or UV-exposed applications.
Yes, we are equipped to handle both low-volume prototyping and high-volume production, ensuring consistent quality and efficiency throughout.
Our team works closely with you to understand the functional requirements of your part and recommends the best material based on mechanical strength, chemical resistance, and environmental conditions.
Yes, composite materials, such as glass-filled plastics, are commonly used in injection molding to enhance strength, stiffness, and thermal stability.
Yes, KingStar Mold offers the option of using recycled materials, such as recycled PET, or biodegradable plastics for environmentally conscious production.
TPU (Thermoplastic Urethane) is commonly used for flexible parts, offering excellent flexibility, abrasion resistance, and elongation.
Yes, KingStar Mold can provide certifications for certain grades, particularly for industries such as aerospace, medical, and automotive, ensuring compliance with relevant standards.