- 1. Introduction
- 2. What Determines Injection Molding Costs?
- 3. Mold Tooling Costs: The Foundation of Injection Molding Expenses
- 4. Material Costs
- 5. Injection Molding Machine and Equipment Costs
- 6. Labor and Setup Costs: The Hidden Expenses
- 7. How Part Design Influences Injection Molding Costs
- 8. Injection Molding Costs Across Different Production Volumes
- 9. Strategies to Reduce Injection Molding Costs
- Implementing Design for Manufacturing (DfM) Practices
- Simplifying Product Design to Minimize Mold Complexity
- Reducing the Number of Cavities in the Mold
- Strategic Material Selection Tactics
- The Advantages of Insert Molding and Overmolding
- How Self-Mating Parts Can Simplify Design and Reduce Costs
- Leveraging Rapid Tooling to Speed Up Production and Reduce Costs
- Adopting New Technologies to Reduce Costs
1. Introduction
Injection molding has become one of the most widely used manufacturing processes, especially for producing high-volume, complex plastic parts. It’s an cost-effective method that allows for precise replication of parts, making it ideal for industries like automotive, electronics, medical devices, and consumer goods. However, despite its advantages, injection molding can be a costly endeavor if not properly managed. Understanding the factors that contribute to injection molding costs is crucial for optimizing the process and ensuring that projects stay within budget.
Many factors influence the cost, including mold design, material choice, production volume, and machine setup. Without a clear understanding of these elements, projects can easily go over budget, resulting in unexpected costs that can impact timelines and profit margins. For example, an overly complex mold design might lead to higher initial costs and longer lead times, while choosing an expensive material could significantly inflate per-part costs.
By having a precise estimation of costs upfront, manufacturers can allocate resources more effectively, avoid potential delays, and ensure that the final product meets quality and budget expectations. As a custom plastic part injection molding company, this post concludes our experience on cost-saving while avoiding sacrificing product quality, if you’re interested, please read on.
2. What Determines Injection Molding Costs?
The cost of injection molding is influenced by several factors, each of which plays a crucial role in determining the overall expense of the process. Understanding how these elements interact can help manufacturers make informed decisions about how to optimize their production costs. In this section, we’ll break down the main cost factors in injection molding and explore how variables like material, mold, and labor impact the final price.
The Main Cost Factors in Injection Molding
Injection molding involves various components that can contribute to the cost of manufacturing a part. These include:
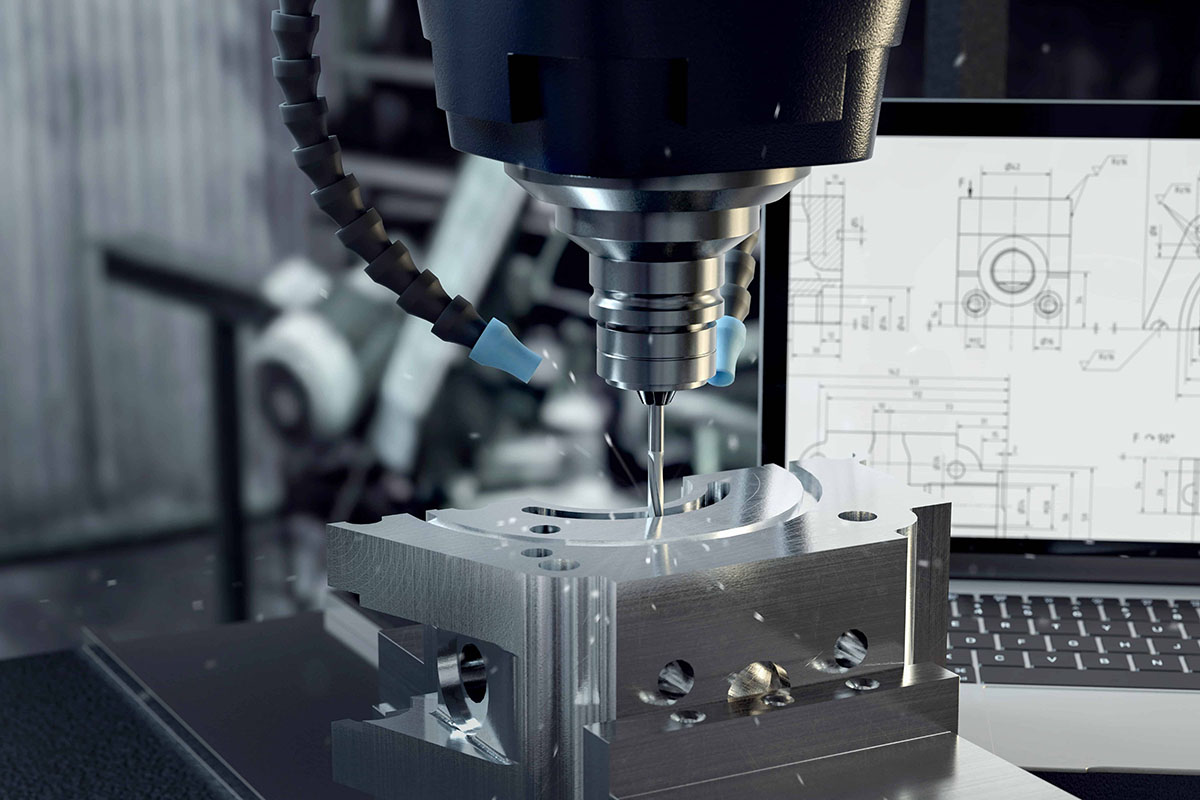
- Mold Design and Fabrication: The mold is one of the largest upfront costs in injection molding. A custom mold designed for a specific part can be expensive, especially if it’s complex and requires precision engineering. The material of the mold—usually steel or aluminum—affects its cost, as well as its longevity.
- Material Choice: The type of plastic material used in the injection molding process can have a significant impact on cost. Some materials are more affordable, while others are more expensive due to their unique properties or specialized requirements.
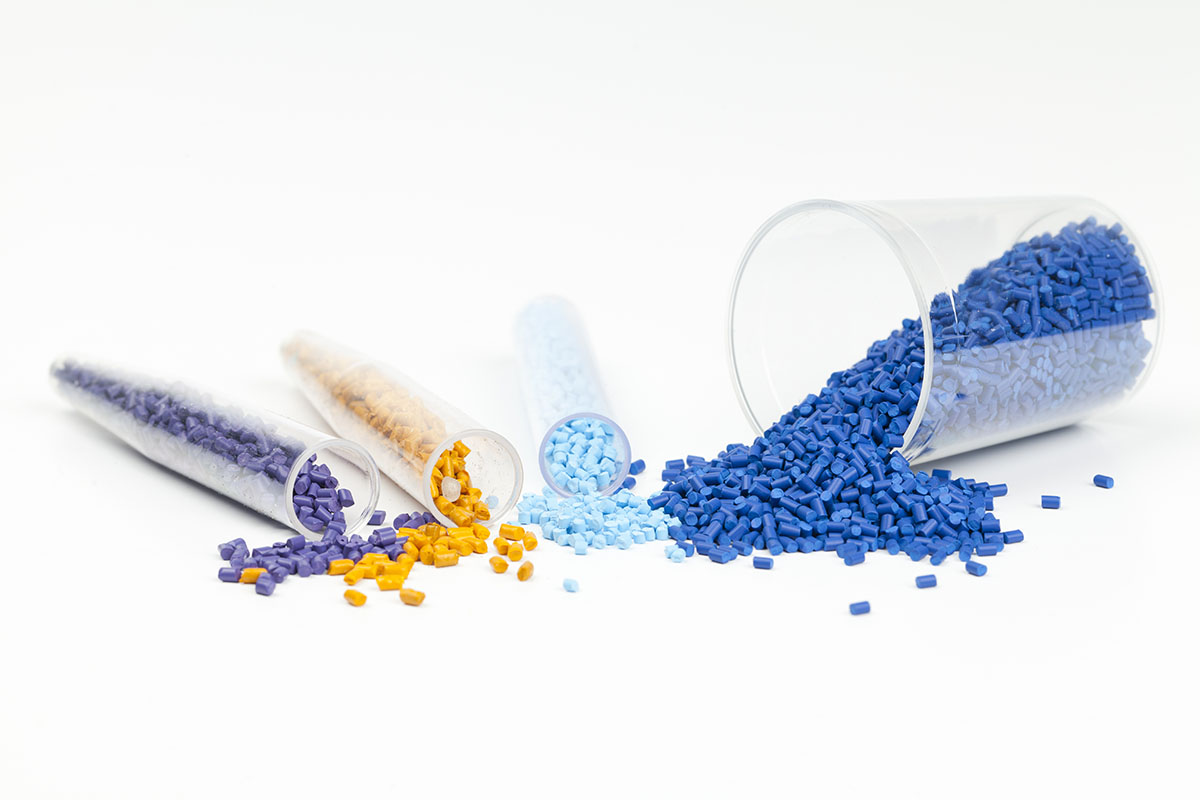
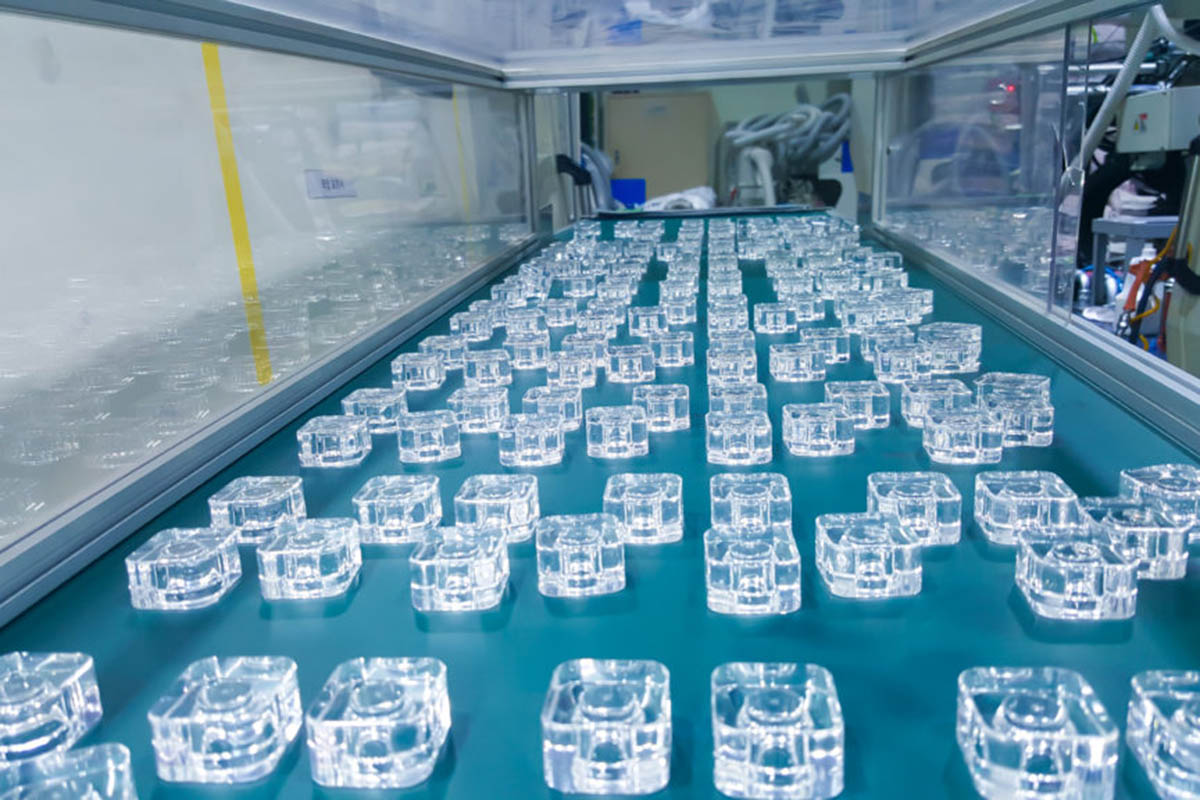
- Production Volume: The number of parts being produced plays a large role in the total cost. High-volume production typically reduces the cost per unit, as the fixed costs associated with mold creation and setup are spread over a larger number of parts.
- Machine and Equipment: The complexity and sophistication of the injection molding machine also contribute to the overall cost. High-precision machines or those used for specialized processes (such as multi-shot injection molding) are more expensive to operate and maintain.
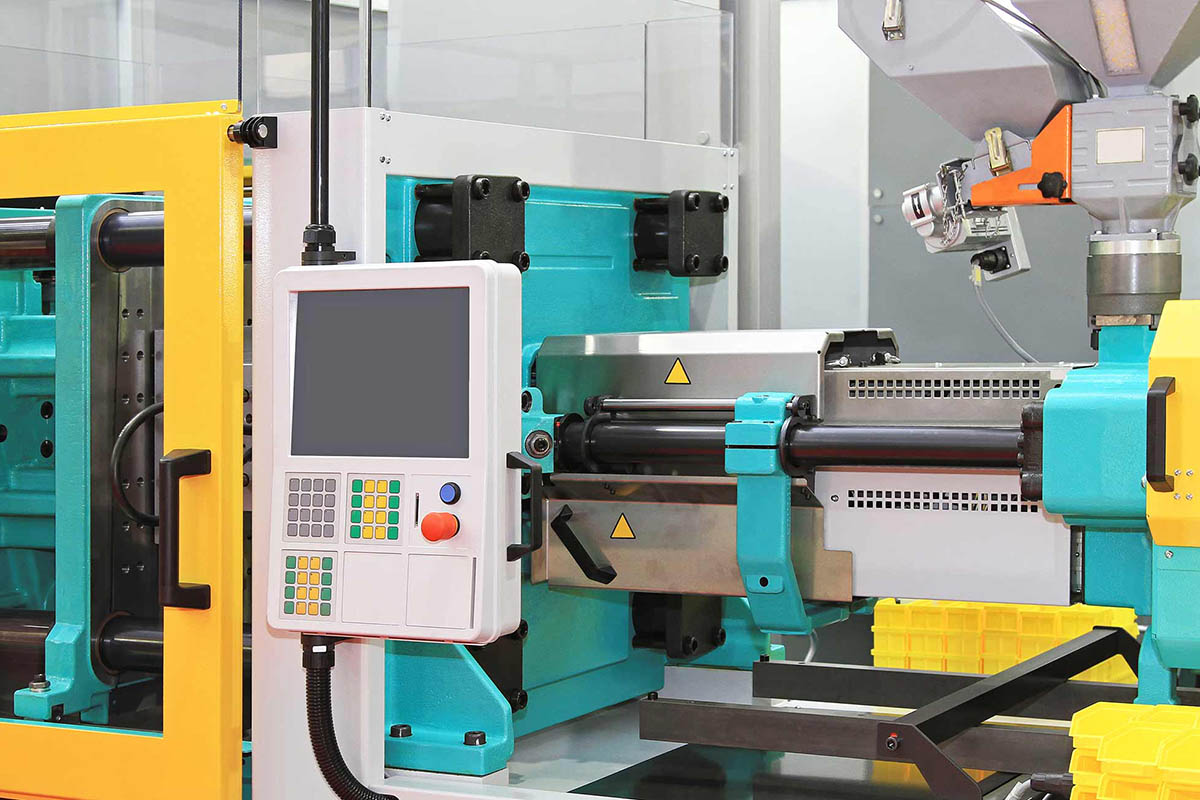
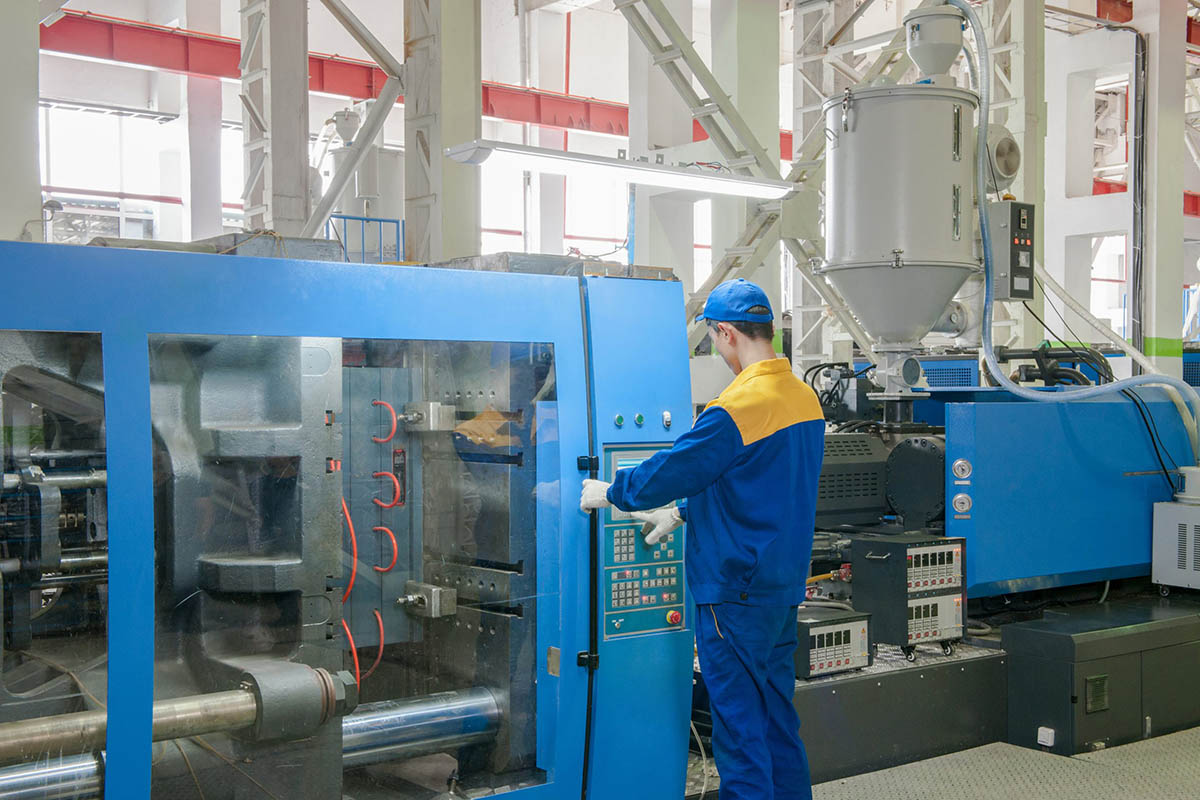
- Labor: While much of the injection molding process is automated, skilled labor is still required for machine setup, monitoring, and troubleshooting.
Understanding the Interplay Between Different Variables
One of the challenges in estimating injection molding costs is understanding how various factors interact with one another. For example, while using cheaper materials can reduce material costs, this might result in a lower-quality product or longer production time, ultimately driving up the total cost. Similarly, a complex mold design may improve the quality or functionality of the part, but it could also increase upfront costs.
By balancing these factors—such as material choice, mold complexity, and production volume—manufacturers can optimize costs and achieve the most cost-effective solution for their project. For instance, simplifying the design of a part can reduce the need for a complicated mold, which in turn reduces the cost of mold fabrication and the amount of material required for production.
Among these factors, four main cost drivers—material, mold, labor and equipment—are the key factors that manufacturers need to pay close attention to when planning an injection molding project. The production volume may have been determined based on your requirements initially and is difficult to change, but these four key factors can be adjusted flexibly according to the situation. Next, we will delve into each one (including production volume) in detail.
3. Mold Tooling Costs: The Foundation of Injection Molding Expenses
When it comes to injection molding, mold tooling is usually the biggest upfront investment – and (arguably) the most critical. It sets the stage for everything that follows, directly impacting both the quality of your final parts and the overall cost-effectiveness of your production run. In this section, we’ll break down the cost drivers: the types of molds available, how complexity hikes up the price, material choices, durability trade-offs, and the different ways of processing the molds.
Types of Molds: Custom vs. Universal Molds
Molds come in various configurations, each with its cost considerations:
- Custom Molds: Built for parts with specific designs, these offer top-notch precision and functionality with higher price. Designing and machining something unique takes time and specialized skill. Expect costs to climb based on how intricate your part is, the materials needed, and the sheer size of the mold itself.
- Universal Molds: Think of these as more adaptable workhorses. Designed to handle various parts (especially simpler, more generic ones), they lower initial costs and shorten turnaround times. Perfect for lower volumes or standard components where absolute precision isn’t the top priority.
So, which one wins? It boils down to your production volume, part complexity, and budget. High-volume, complex parts often justify the custom mold’s higher upfront cost over time. For shorter runs or simpler designs, a universal mold is usually the smarter, more economical pick.
The Impact of Mold Complexity on Cost
The complexity of a mold directly influences its cost. More intricate mold designs require additional materials, advanced machining techniques, and longer production times; And complex molds with multiple cavities, slides, or intricate cooling channels require more advanced tooling and precision, which all raise the upfront cost.
But don’t write off complexity entirely! A sophisticated mold can pay dividends through faster production cycles, superior part quality, and the ability to mold multiple features in single shot. The key is weighing that higher initial cost against potential savings in per-part manufacturing time and performance gains. Sometimes, spending more upfront saves a lot later.
Materials Used for Mold Creation and Their Cost Implications
Material choice for mold building is another key factor that can significantly influence tooling costs. Common materials used for molds include:
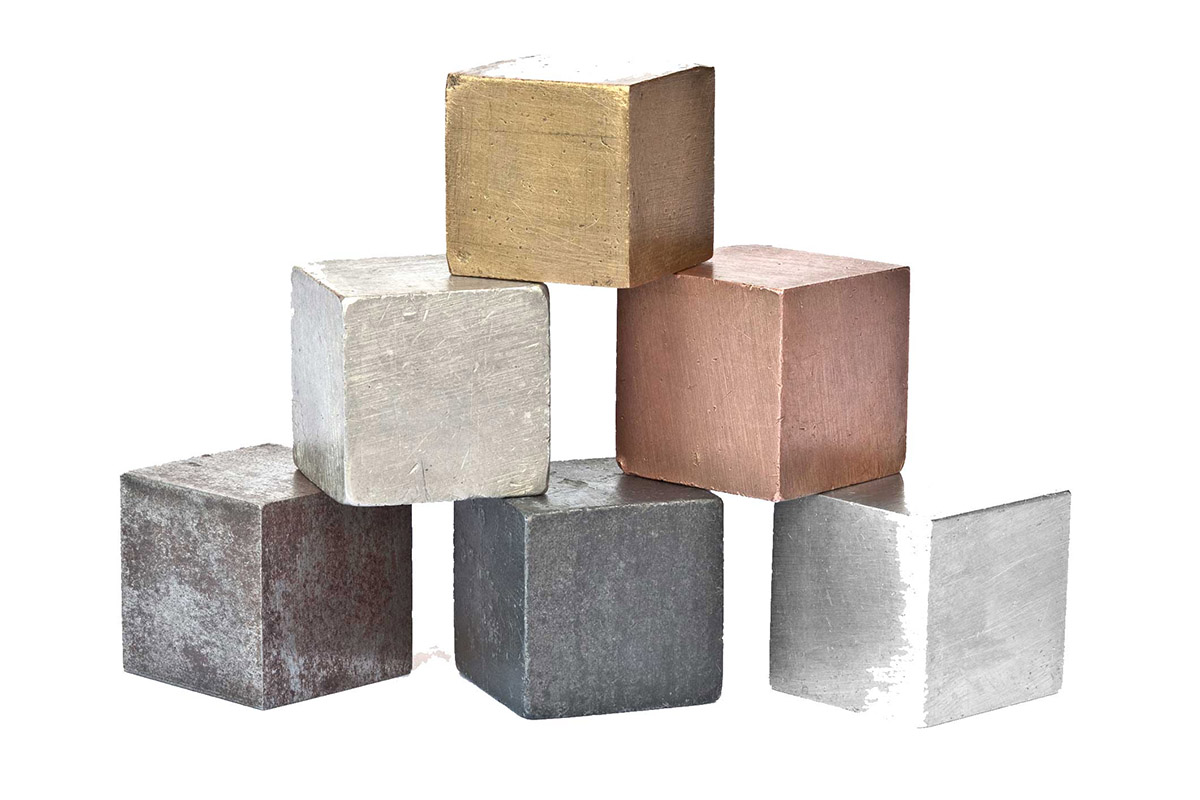
- Steel: A common choice for large production volume. Steel molds are tough cookies, built to endure the heat and pressure of countless cycles. The downside? They’re expensive. That investment only makes sense if you’re running huge volumes where the mold’s longevity pays off.
- Aluminum: Aluminum molds are less expensive than steel molds and are often used for low to mid-volume production. While they are less durable than steel, they offer faster lead times and lower initial costs. Aluminum molds are often used for prototypes or when a shorter production run is needed.
- Other Options (Beryllium, Copper Alloys): Sometimes niche materials offer specific perks, like better heat dissipation or extra durability. Just be prepared for a (may be a lot more) higher price than standard steel or aluminum.
Durability: Pay Now or Pay Later?
How long your mold lasts is crucial for long-term costs. A rock-solid, durable mold (like hardened steel) can crank out millions of parts, minimizing downtime for repairs or replacements. This translates to lower costs per part over massive runs.
However, for a quick prototype or a small batch, splurging on ultra-durability might be overkill. Be realistic about your production needs. An aluminum mold might be perfectly adequate and cost-effective for a limited run, while a massive, long-term project need the durability (and higher cost) of steel.
Cost Differences Between Different Mold Manufacturing Methods
The method used to create the mold has a significant impact on tooling costs. Different manufacturing techniques offer varying levels of precision, lead time, and cost-effectiveness:
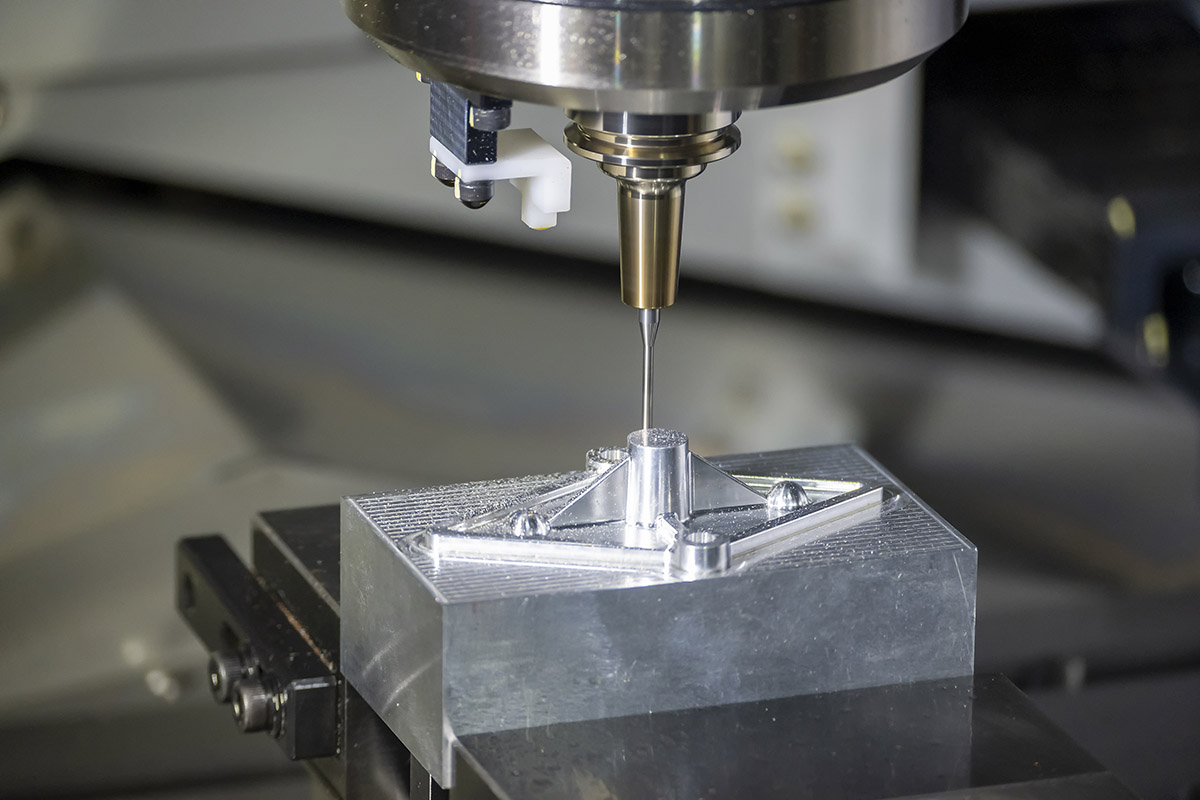
- CNC Machining: CNC machining is one of the most common methods for creating molds, especially when high precision is required, and is ideal for creating metal molds due to its ability to achieve high accuracy in detailed designs. However, while CNC machining offers excellent results for precise mold creation, it is relatively time-consuming, especially for more intricate mold designs. The cost of CNC machining is also influenced by the complexity of the mold and the time required for the process.
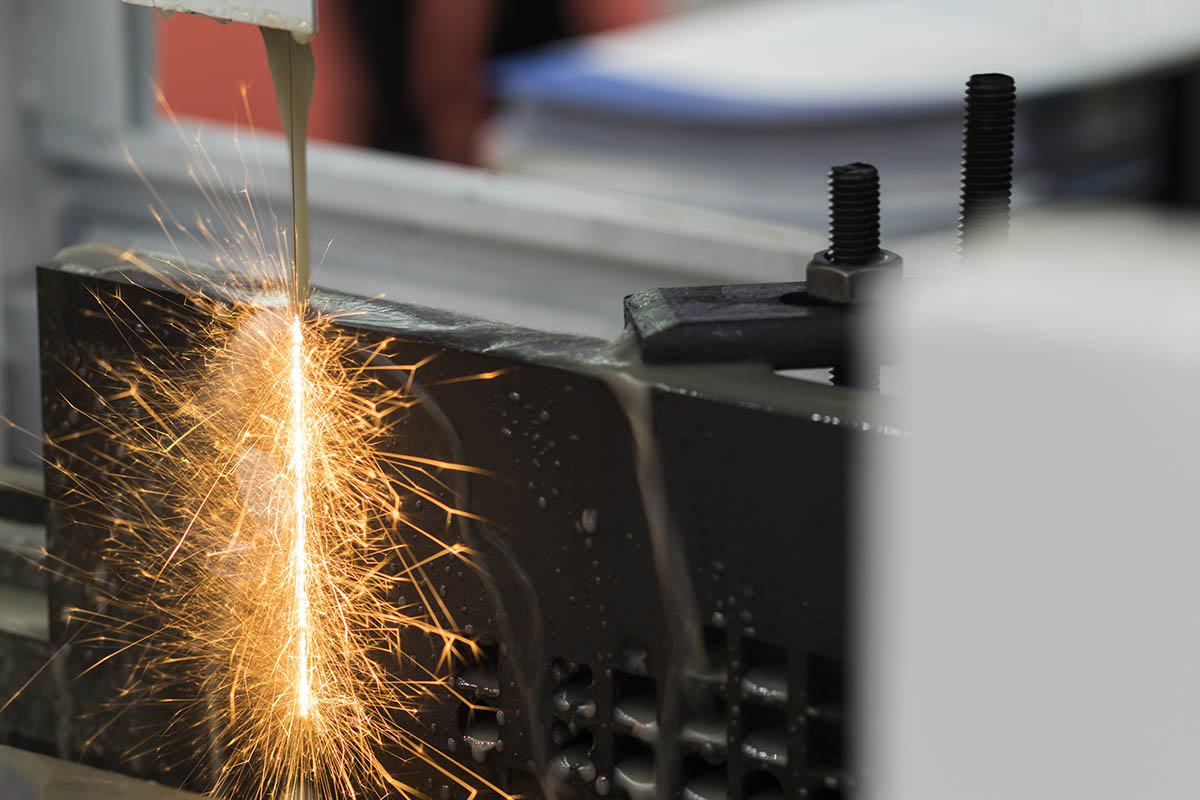
- EDM (Electrical Discharge Machining): Electrical Discharge Machining (EDM) is a specialized technique used to create molds with complex features and fine details. EDM uses electrical discharges to erode material from a metal workpiece, allowing for the creation of extremely intricate shapes with tight tolerances. This technique is particularly effective for very fine features or designs that are difficult to machine with traditional methods. It’s commonly used for creating molds from hard metals such as steel, making it suitable for industries requiring high-precision molds with detailed geometries.
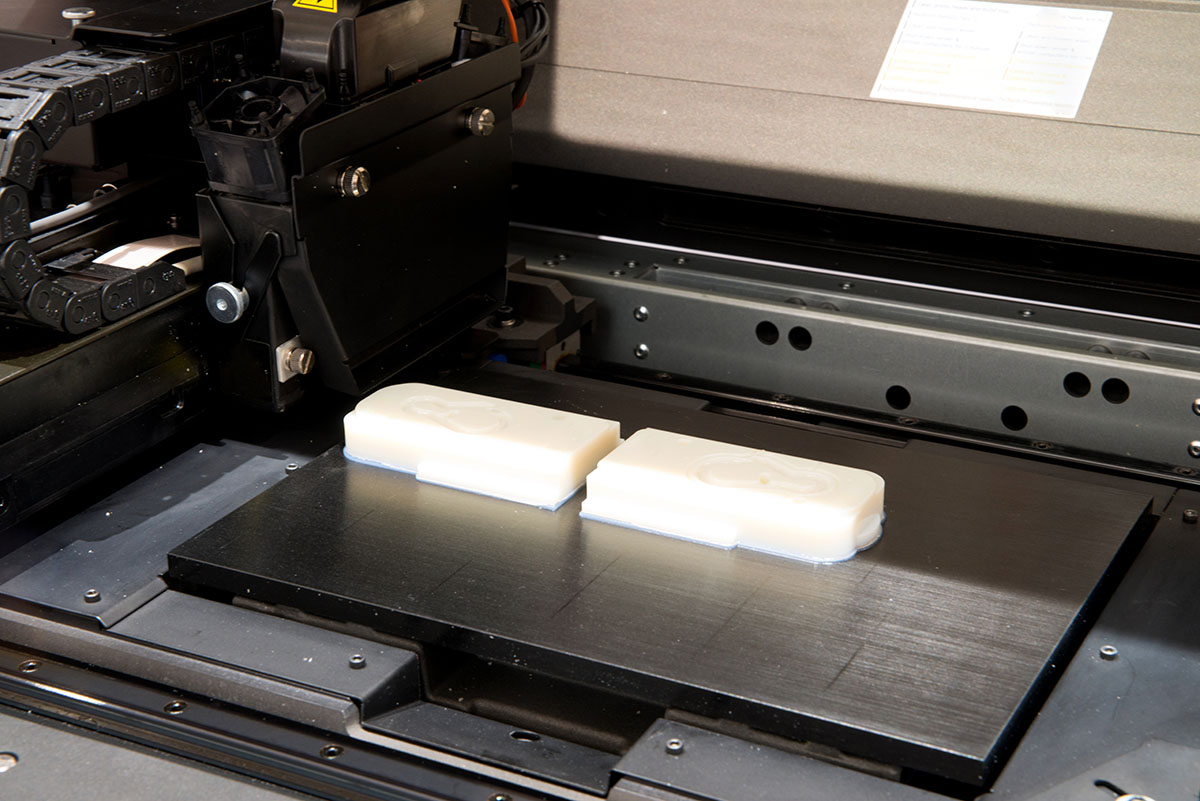
- 3D Printing: 3D printing is an increasingly popular method for mold creation, especially for low-volume production or rapid prototyping. It offers the advantage of significantly reducing lead times and initial mold costs, as it doesn’t require complex tooling or skilled labor. And it allows for quick adjustments to the mold design. However, 3D printed molds are typically limited by the size of the printer’s build platform, and the material strength and durability are generally not sufficient for high- or even medium-volume production runs. Additionally, the molds produced by 3D printing tend to shrink, so compared to other molds, the components manufactured by 3D-printed molds may not be as precise.
4. Material Costs
During more than 15 years of experience in optimizing injection molding projects, we have found that the selection of materials directly affects the budget. The cost of resin usually accounts for 30% to 60% of the total cost of the part, and the material selection decision will have a cascading impact on production efficiency, mold wear, and the performance of the final product.
Common Resins: Matching Properties to Practical Needs
We categorize resins by real-world application requirements rather than just chemical properties:
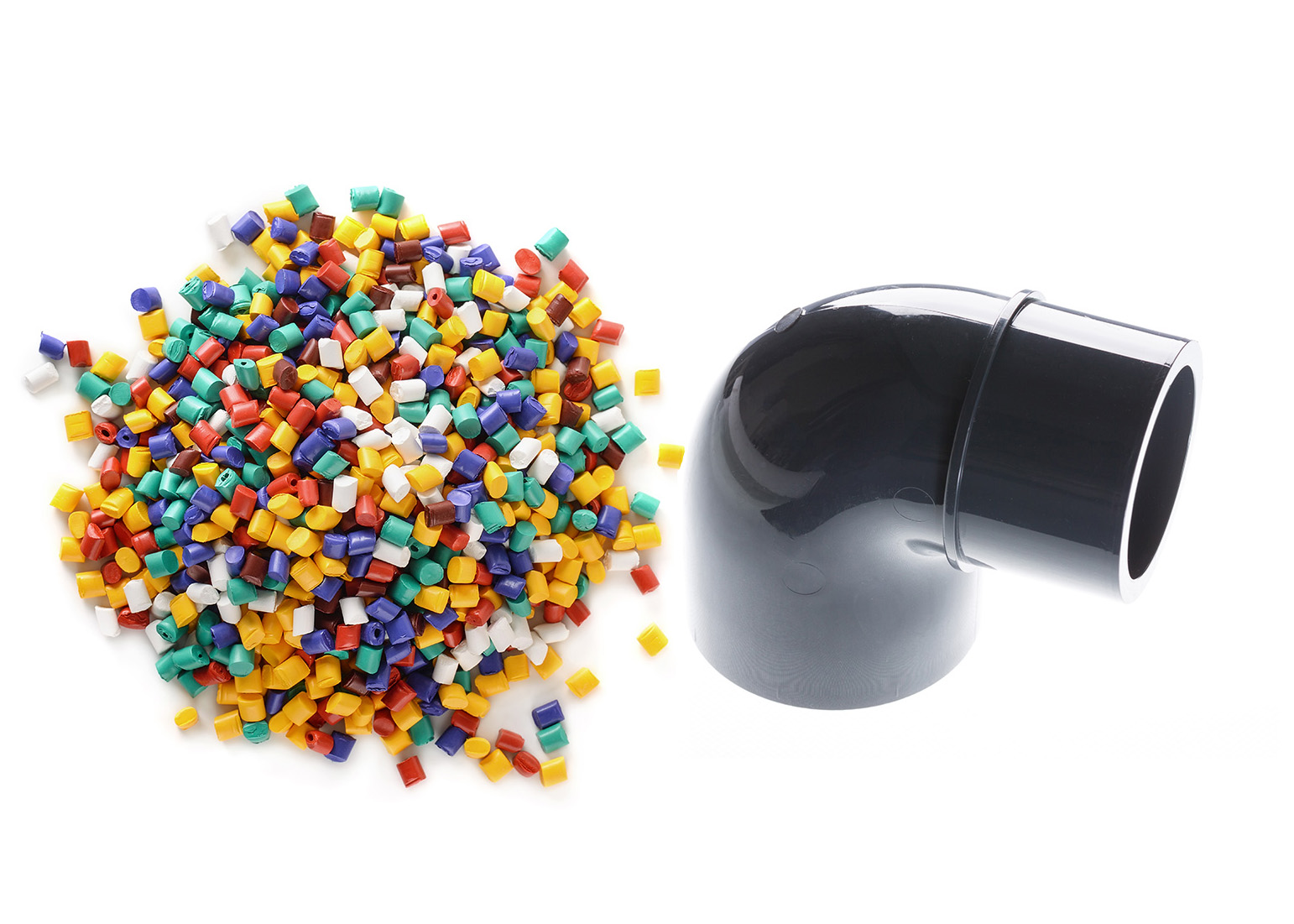
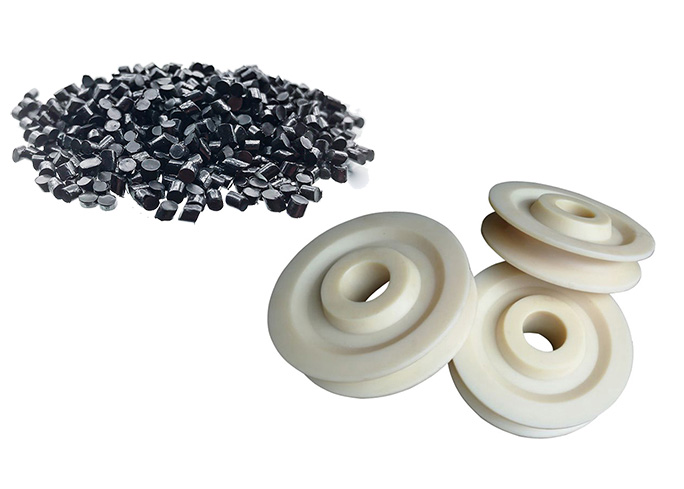
Workhorse Resins (ABS, PP, PE)
- Ideal for: Consumer goods, housings, containers
- Cost advantage: $1.50–$3.50/kg
- Trade-offs: Limited heat/chemical resistance
- Pro Tip: PP’s flexibility reduces ejection failures—saving costs on secondary operations.
Engineering-Grade (PC, Nylon, Acetal)
- Key applications: Automotive components, load-bearing parts
- Cost range: $4–$8/kg
- Hidden value: PC’s impact resistance often eliminates the need for metal reinforcements (e.g., a car manufacturer reduced part costs by 18% by replacing metal brackets with PC).
Specialty Performers (PEEK, PPSU, PTFE)
- Essential for: Medical implants, aerospace, extreme environments
- Cost reality: $80–$250/kg
- Strategic insight: We specify these only when regulatory compliance or performance demands justify 10–50x material cost premiums.
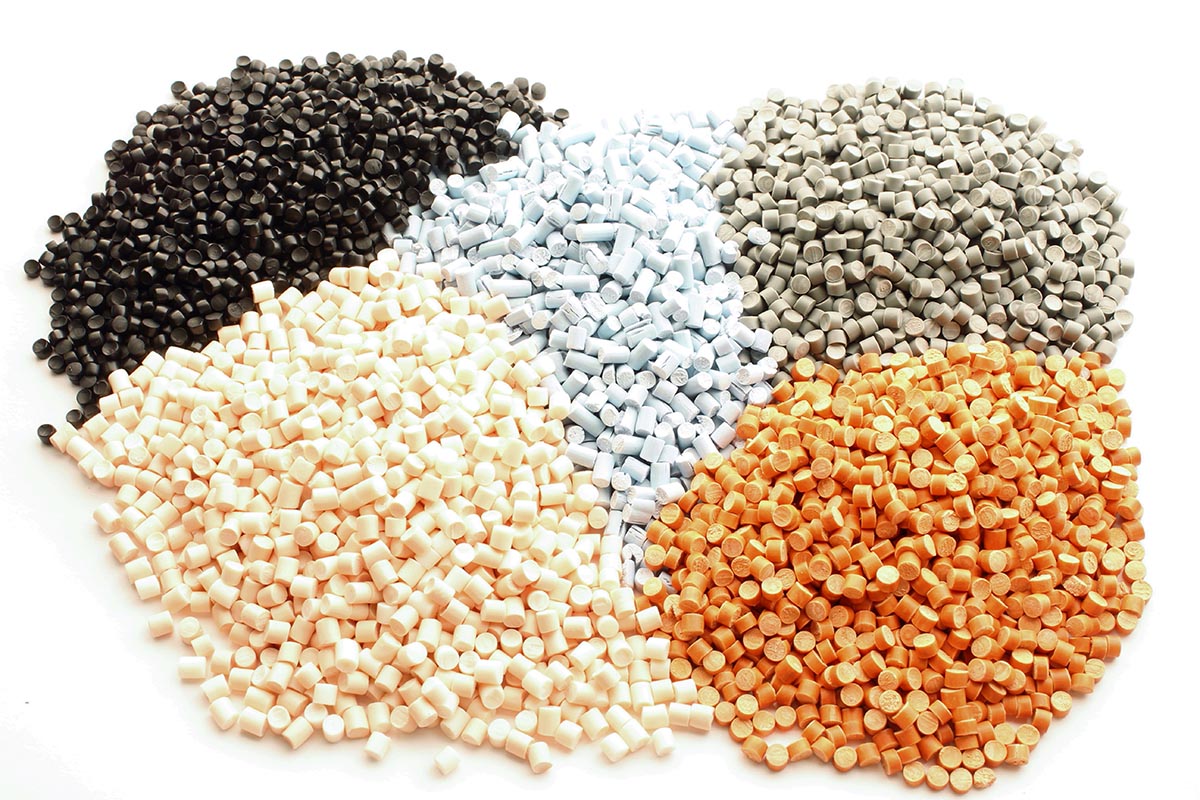
The Role of Additives: Fillers, Reinforcements, and Colorants
Additives are often used in injection molding to enhance material properties and reduce costs. They can alter the resin’s characteristics, making it more suitable for specific applications. Additives aren’t just ingredients – they’re cost levers:
Additive Type | Cost Impact | Performance Effect | When We Recommend |
Glass Fiber | +15-40% material cost | ↑ Stiffness ↑ Dimensional stability ↓ Impact toughness | Structural parts >10,000 cycles |
Mineral Fillers | +5-15% | ↓ Shrinkage ↓ Warpage ↓ Surface finish | Large flat components (e.g., panels) |
Flame Retardants | +20-60% | Enables UL94 compliance | Electronics/electrical enclosures |
Custom Colors | +$500-$5k setup | Brand alignment | Consumer-facing parts only |
Case study: We reduced a client’s project cost by 22% by switching from glass-filled PC to optimized-wall ABS with localized reinforcements—proving over-engineering additives drives exponential cost increases.
5. Injection Molding Machine and Equipment Costs
Selecting presses isn’t about specs – it’s about lifecycle economics. Here’s our breakdown from 200+ machine installations:
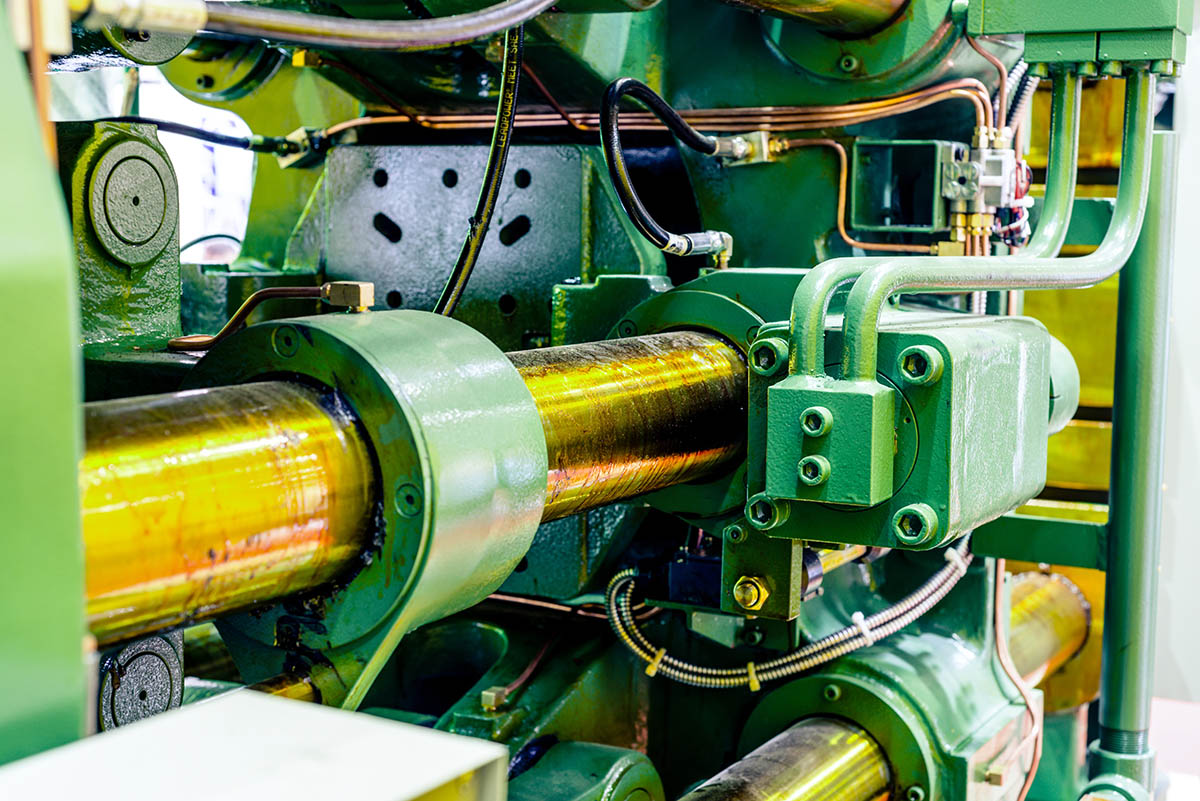
- Hydraulic Machines: Hydraulic injection molding machines utilize an oil-driven hydraulic system to achieve injection and clamping functions. These machines are renowned for their powerful performance and are suitable for production requiring greater force and more complex components, but they typically have lower energy efficiency and higher operating costs compared to electric or hybrid machines. Hydraulic machines are commonly used in industries such as automotive and heavy manufacturing.
- Electric Machines: Electric injection molding machines rely on electric motors to drive all functions, including injection, clamping, and ejection. These machines offer high precision, high energy efficiency, and faster production cycles. They are highly suitable for high-precision components with strict tolerance requirements and are widely used in medical, consumer electronics, and high-end automotive sectors. The initial cost of electric machines is usually higher than that of hydraulic machines, but their lower operating costs may make them more cost-effective in the long run compared to electric machines.
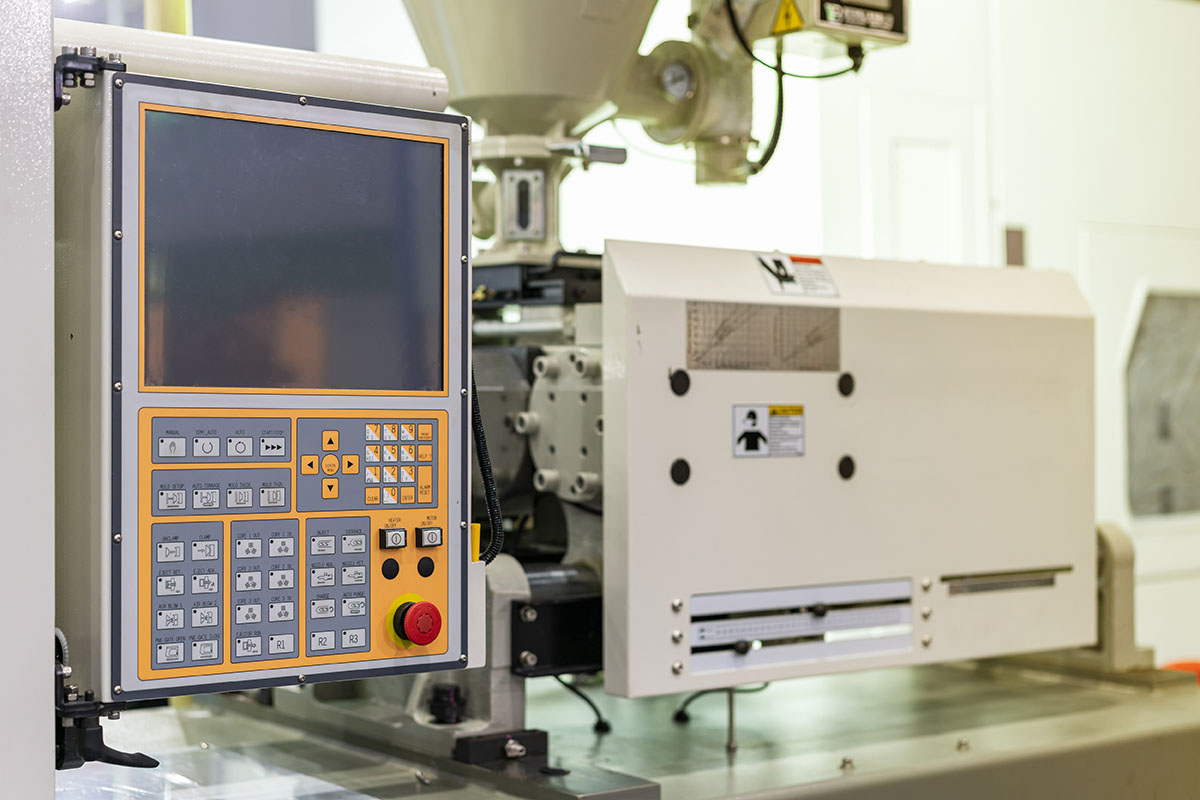
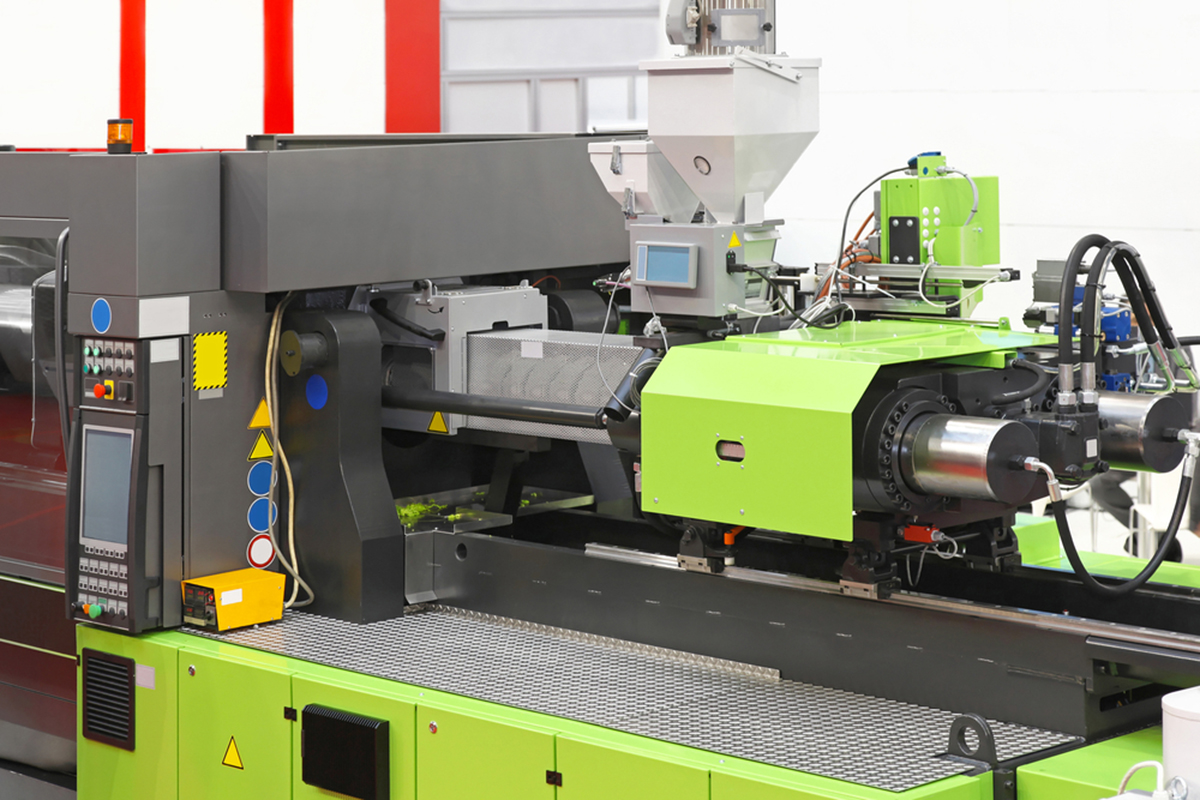
- Hybrid Machines: Hybrid injection molding machines combine the advantages of hydraulic and electric machines. These machines use electric drive for certain functions (such as injection and ejection), while maintaining hydraulic clamping for high-force operations. Hybrid machines achieve a balance in energy efficiency, precision, and power, making them suitable for a wide range of application scenarios. Compared to fully electric machines, they are usually cheaper, but still possess many advantages.
Feature | Hydraulic | Electric | Hybrid |
Upfront Cost | $ (50-100k) | $$$ (150-500k) | $$ (120-300k) |
Energy Cost | $$$ (0.8-1.2 kWh/kg) | $ (0.3-0.5 kWh/kg) | $$ (0.5-0.7 kWh/kg) |
Precision | ±0.5mm | ±0.02mm | ±0.1mm |
Maintenance | Weekly oil checks | Annual calibrations | Quarterly servicing |
Guidelines based on experience:
- For start-up enterprises: Lease electric equipment – reduce energy costs and ensure cash flow
- For traditional car manufacturers: Modify the hydraulic system and install servo pumps (can save 30% of energy)
- Medical regulations require: Only use electric equipment – particles generated by hydraulic leakage do not comply with ISO 13485 standards
Key Factors for Machine Selection
Selecting the right injection molding machine is a critical decision that can influence both initial costs and ongoing operational expenses. Here are some factors to consider:
- Part Size and Complexity: Larger parts need higher clamping force (hydraulic/hybrid), while precision parts require electric/hybrid machines (e.g., ±0.02mm tolerance for medical catheters).
- Production Volume: If a large quantity of components is to be produced, investing in a machine with higher production efficiency and a faster production cycle may be a wise choice. In this case, electric or hybrid machines may have an advantage due to their speed and energy efficiency. For small batch production, hydraulic machines can still provide reliable performance at a lower cost while ensuring quality control.
- Material Compatibility: The type of materials used in the injection molding process also affects the choice of machine. Some machines are more suitable for specific resins, such as thermoplastics, thermosetting resins, or elastomers. Ensuring that the machine can efficiently handle this material is crucial for cost and quality control.
- Automation Requirements: Some production lines require the automation of component handling, such as mechanical arms for component extraction or automated inspection systems. Machines with integrated automation functions may be more expensive in the initial stage, but in the long run, they can save costs by reducing labor and increasing production speed.
Cost Calculation Methods
- Clamping Force Formula:
Tonnage Required = Projected Area (in²) × Pressure (psi) ÷ 2000
*Under-spec = flash defects | Over-spec = $10k+ wasted capacity*
- Downtime Cost Calculator:
(Hourly Rate × MTTR) + (Scrap Rate × Part Price)
*Example: 4hr hydraulic repair @ $200/hr + 400 scrapped parts @ $5 = $2,800 incident*
- Energy Reality Check:
Electric machines pay back premium in 18-36 months at >100k annual volumes
How Machine Size and Capabilities Impact Costs
The size and capabilities of an injection molding machine have a direct impact on both initial purchase costs and ongoing production expenses. Here’s how machine specifications affect the overall cost structure:
- Clamping Force: The clamping force required during the forming process depends on the size of the part and the material used. Larger parts or those made of high-strength materials require greater clamping force, which will increase the size and cost of the machine. Machines with higher pressing force are usually more expensive to purchase and operate, but they are essential for specific applications.
- Shot Size: Shot size refers to the amount of material injected into the mold during each cycle. A larger shot size requires a more powerful machine, and such machines usually come at a higher price. However, in mass production, being able to efficiently produce larger-sized components may reduce the cost of each component over time.
- The lifespan condition of the machine: The lifespan condition of the machine also have an impact on the cost. Older machines may require more maintenance and energy to operate, resulting in an increase in ongoing costs. However, they are usually priced lower at the time of initial purchase. Newer machines, although having a higher initial cost, typically have better energy efficiency, a faster production cycle, and require less maintenance, thus resulting in lower long-term operating costs.
- Additional features: Some machines are equipped with advanced functions such as multi-material injection, gas-assisted injection, or precision molding. These features can enhance the performance of the machine, but they usually come with higher costs. Depending on the specific requirements of your project, these features may bring long-term cost savings by improving efficiency and part quality.
Ongoing Maintenance and Operational Costs for Injection Molding Machines
What many manufacturers often neglect is that, maintenance and operation of the machine fall under ongoing costs and must be included in the total cost of injection molding. Appropriate maintenance can ensure that the machine remains in optimal operating condition all along, reduce downtime, and extend its service life
- Routine Maintenance: Including regular cleaning, lubrication and calibration, is crucial for ensuring the operation of the machine. These tasks can be carried out on a weekly, monthly or annual basis depending on the task content and usage of the machine. The cost of maintenance services and the cost of replacing parts will accumulate over time.
- Repair: If the machine malfunctions or breaks down, the repair cost can be very high. Older machines may require more frequent repairs. It is important to make budget plans for possible repairs, especially if the machine is old or used frequently.
- Energy Consumption: The operating cost of an injection molding machine is affected by its energy consumption. Hydraulic machines typically have higher energy consumption than electric or hybrid power machines, which may result in higher electricity bills. Choosing energy-efficient machines over time can reduce operating costs.
- Labor Costs: Production operations require skilled technicians. Labor costs (including wages, training and overtime pay and more) should be included in the overall production cost. Machines with more automation features may reduce the demand for manual labor, thereby lowering operating costs.
6. Labor and Setup Costs: The Hidden Expenses
While the aforementioned machine and equipment ongoing maintenance also a part of labor cost, here lists a few more:
Mold Complexity | Amateur Setup | Our Standard | Savings |
Basic (2-plate) | 4.5 hours | 1.75 hours | $1,400/job |
Complex (slide) | 12+ hours | 4 hours | $3,200/job |
Hot Runner | 8 hours (+scrap) | 2.5 hours | $2,100/job |
(Documented from 37 Factory Audits)
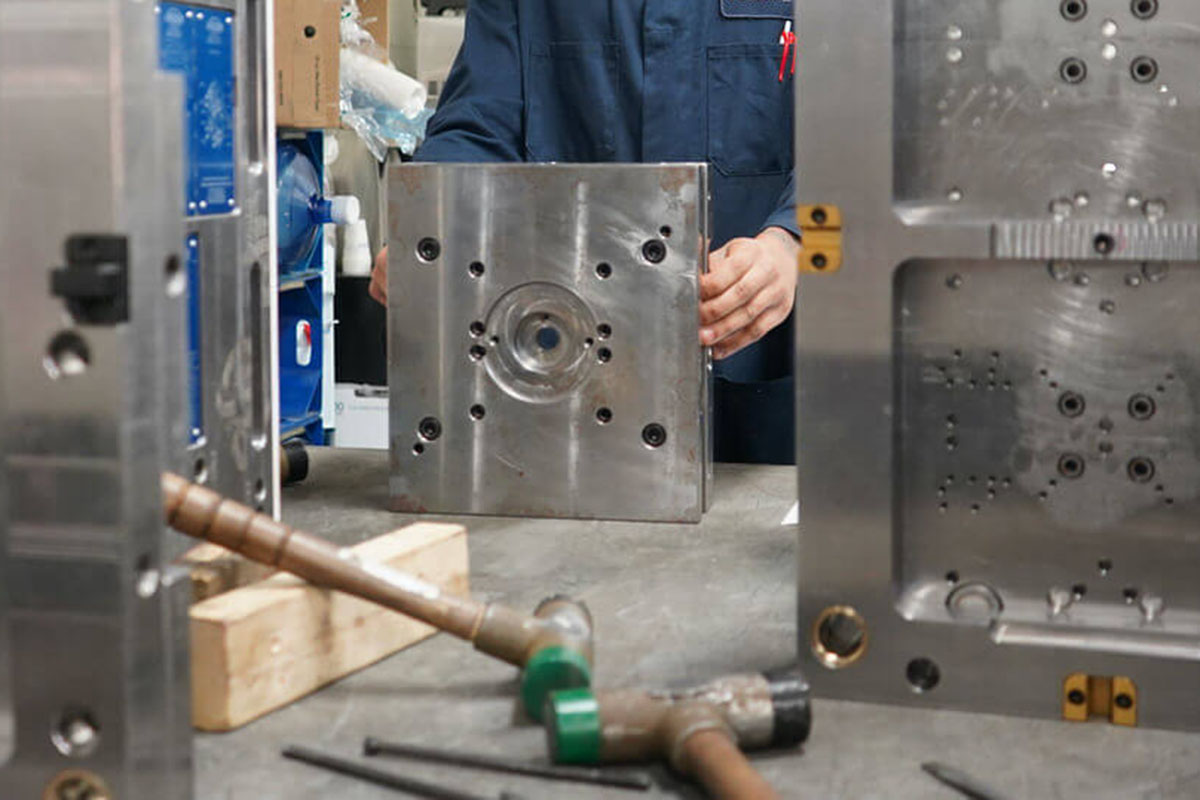
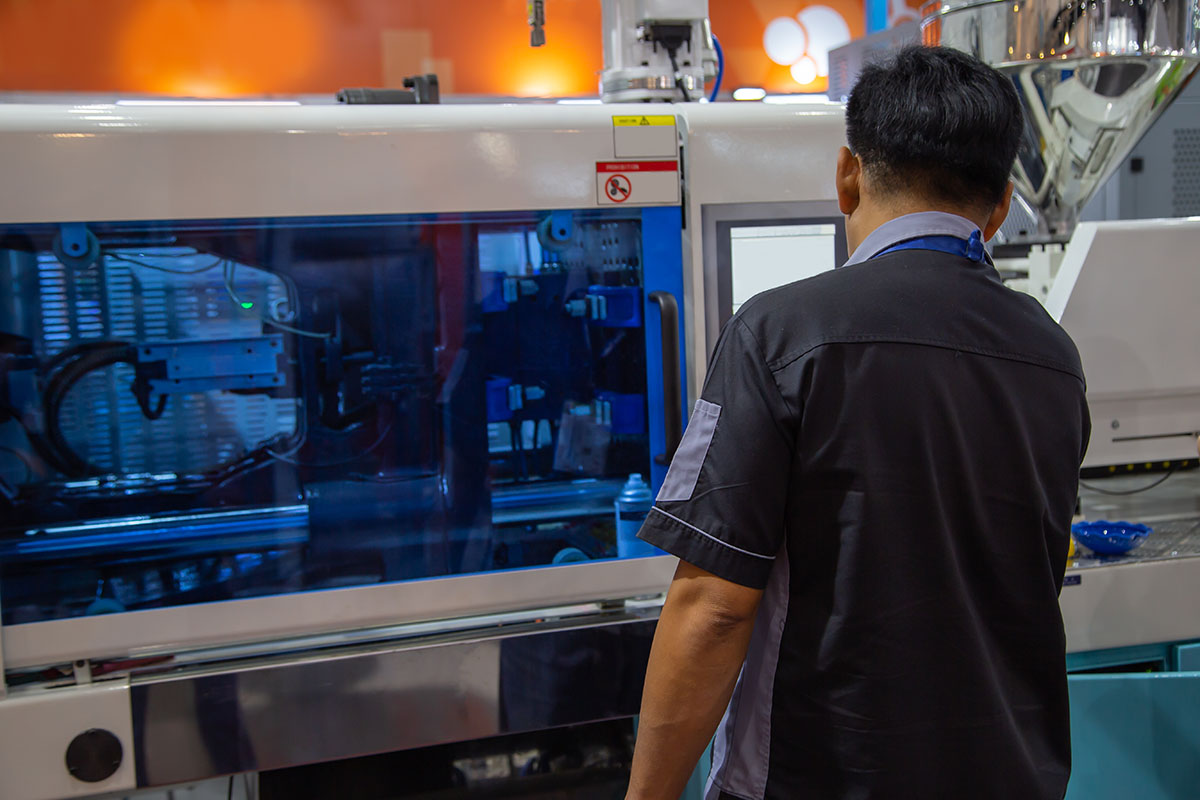
Proven Tactics:
- Preheated Tooling – Cuts 30% off start-up time
- Standardized Mounting – Uses ISO platens with quick-clamps
- Setup Kits – Pre-packed with specific bolts/spacers
- VR Training – New techs achieve 90% efficiency in 3 weeks
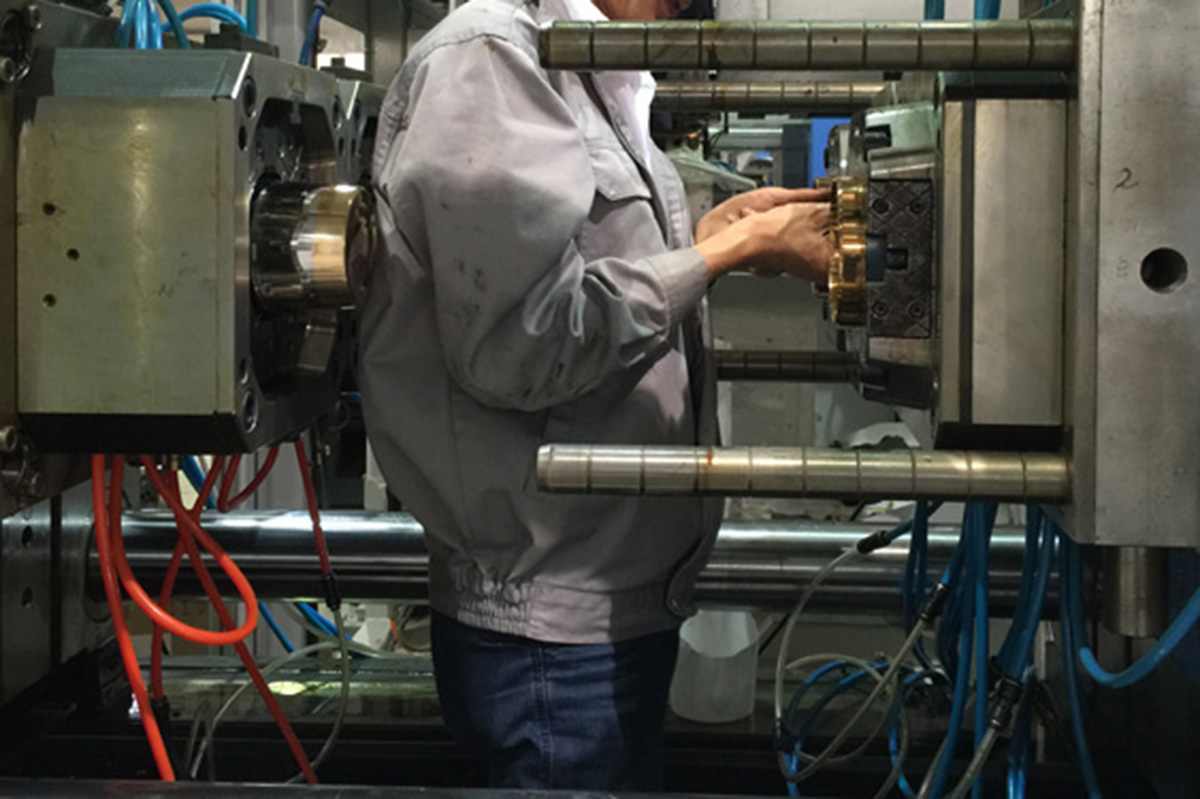
7. How Part Design Influences Injection Molding Costs
The design of the part affects from the complexity of the mold to the material utilization rate and the performance of the machine. By optimizing each element at an early stage in the design process, manufacturers can save time and money, and improve overall production efficiency. Let’s explore them one by one.
The Relationship Between Part Design and Mold Complexity
The complexity of the part design directly affects the mold design, which is one of the largest contributors to the overall production cost.
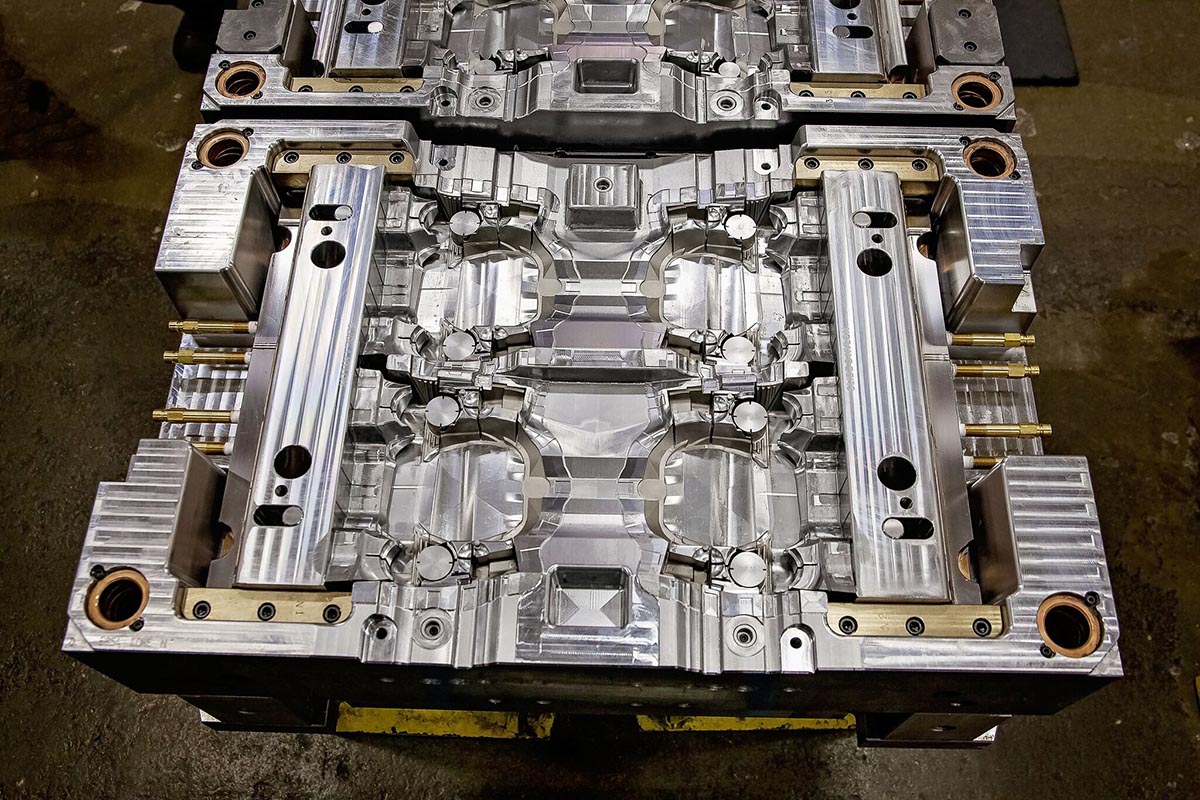
- Intricate Features: Parts with sharp internal corners, deep cavities, or undercuts require specialized tooling, which can significantly raise mold costs. Each additional feature adds a layer of complexity to the mold, requiring more precision and time to produce.
- Multi-Cavity Molds: If a design requires multiple cavities or a multi-part mold, this can increase both the cost of the mold and the production process. These molds demand more advanced technology and precise engineering to ensure all parts are produced accurately, raising the upfront costs.
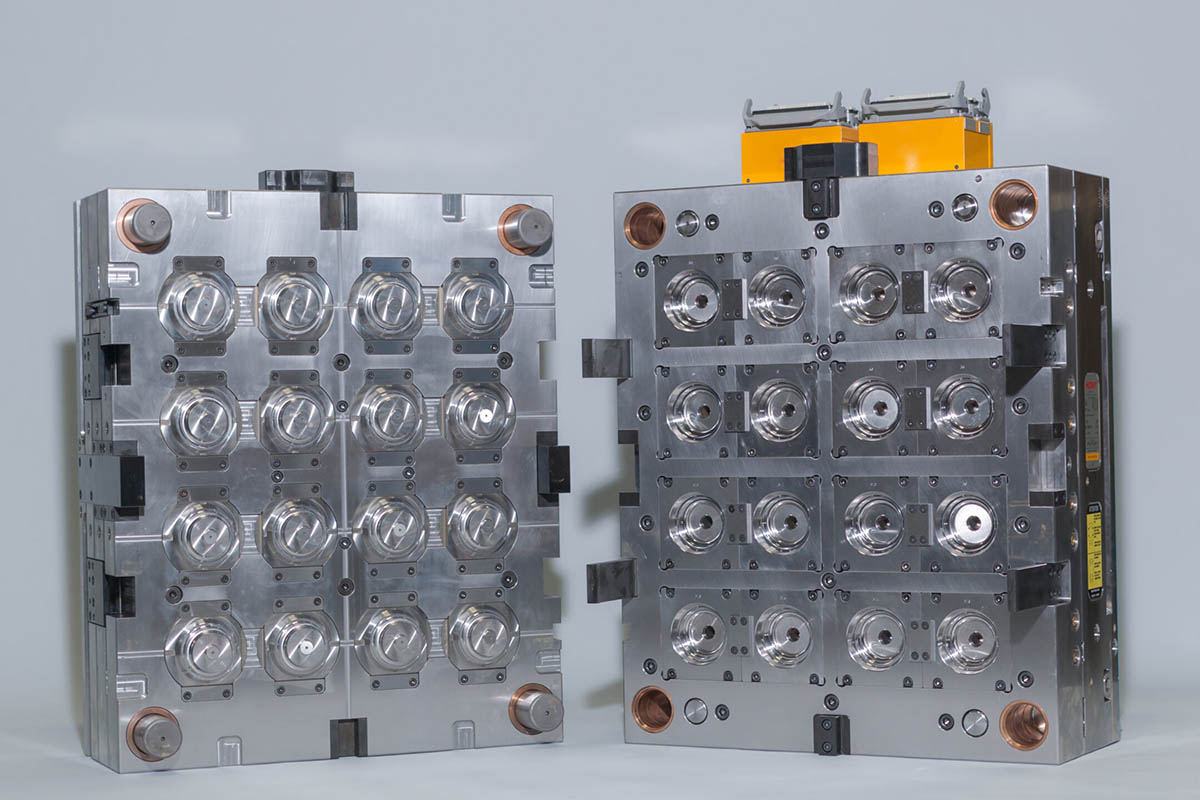
How Part Size Affects Material and Machine Costs
Part size is one of the most straightforward yet impactful factors in determining injection molding costs. Larger parts require more material, more machine capacity, and longer cycle times—all of which add to the overall cost.
- Material Usage: As the part size increases, so does the material required. The cost of materials—especially specialty resins—can skyrocket with larger parts. This directly affects the overall cost per part.
- Machine Size and Energy Use: Bigger parts need larger machines with more clamping force. These machines not only cost more upfront but also consume more energy during production. For large-volume production, this may be justified, but for smaller runs, it can significantly increase per-unit costs.
Reducing part size or designing parts with thinner walls can minimize material usage and machine requirements, ultimately reducing production costs.
Key Design Features for Injection Molding Parts
Part design features such as wall thickness, draft angles, undercuts, and other considerations can drastically affect the cost and feasibility of injection molding. These elements influence how easily parts can be molded, removed from the mold, and the overall efficiency of the manufacturing process.
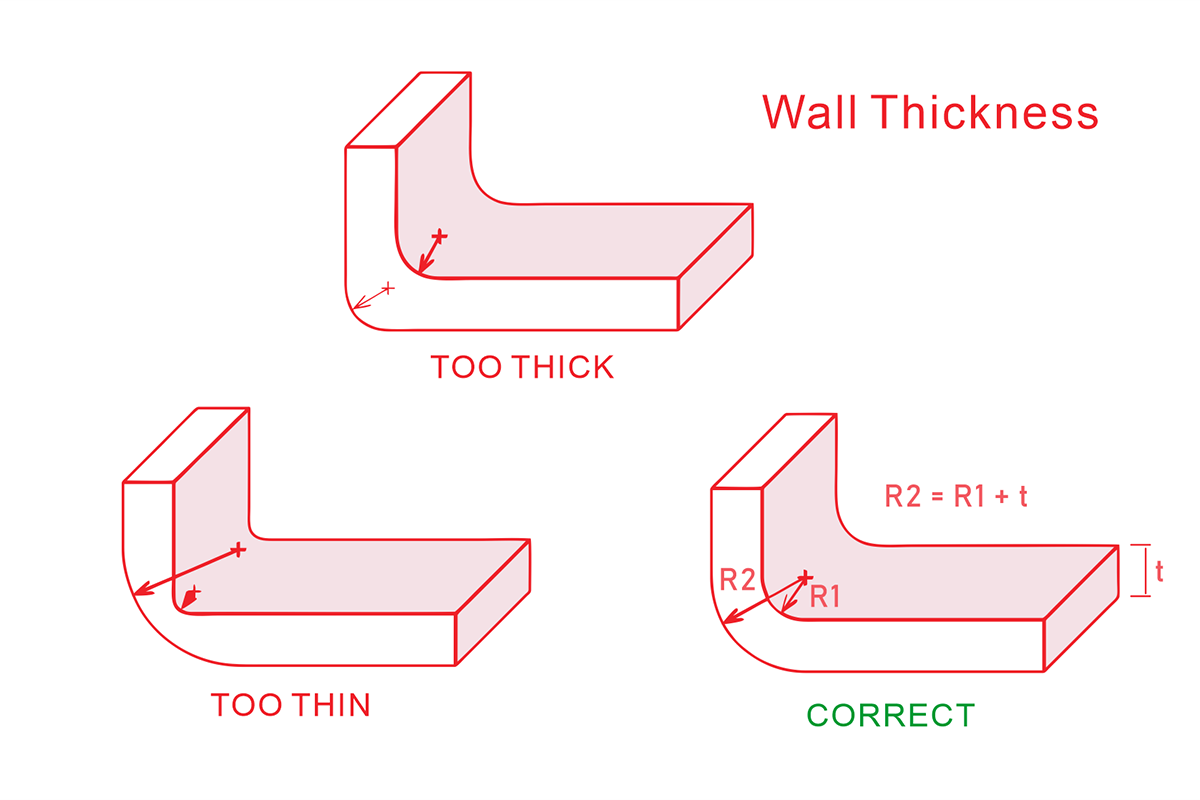
Wall Thickness
Maintaining consistent wall thickness is crucial for ensuring proper molding and cooling. Parts with varying wall thicknesses can result in uneven cooling rates, leading to warping or defects. Thicker walls require more material and longer cooling times, both of which increase the production cost. It’s ideal to design parts with uniform wall thickness to reduce waste and ensure a smoother molding process.
Draft Angles
Draft angles are necessary to facilitate the removal of parts from the mold without causing damage. Without sufficient draft, parts may get stuck, requiring more force or special tools to remove them. Draft angles should be designed to be as small as necessary to reduce mold complexity without sacrificing functionality. A slight taper—typically around 1 to 3 degrees—is often sufficient for most parts.
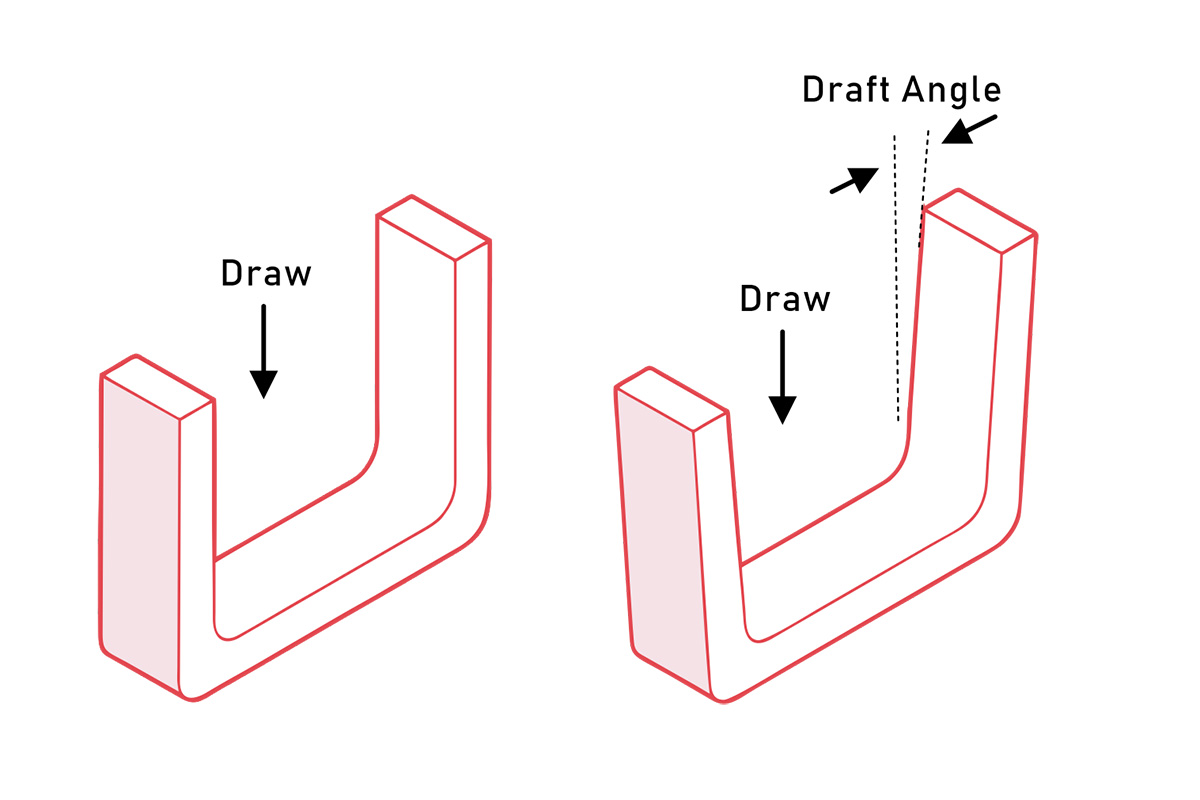
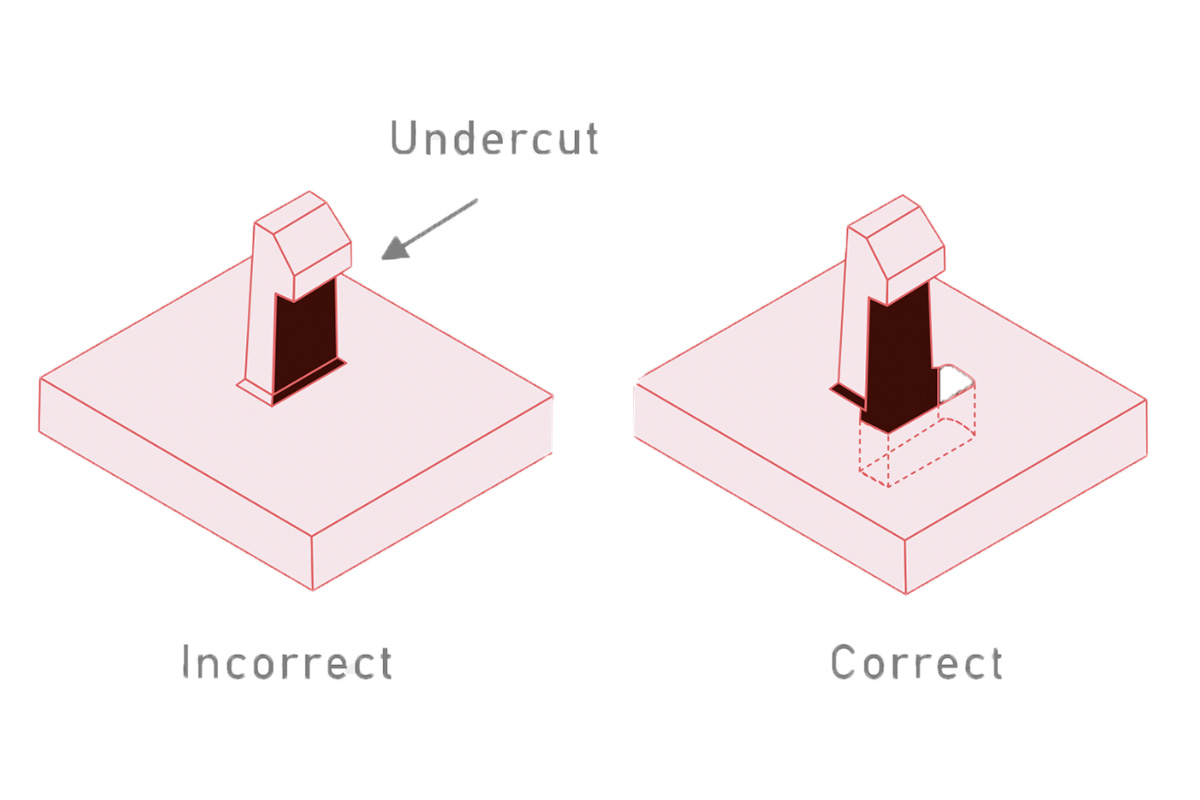
Undercuts
Undercuts are features that prevent a part from being ejected from the mold in a straightforward manner, typically requiring a more complicated mold design. To incorporate undercuts, manufacturers often need to use side actions or collapsible cores, which increase mold complexity and cost. Where possible, reducing or eliminating undercuts can help reduce mold complexity and production costs.
Rib Design
Ribs are commonly used to enhance the strength of components without significantly increasing the material usage or weight. However, improperly designed ribs may cause problems during production – overly thick or improperly positioned ribs can lead to uneven cooling, resulting in deformation or dents. Therefore, ribs with the correct thickness (usually half to one-third of the wall thickness) and the appropriate position must be designed to ensure smooth fluid flow and shorten the cooling time, thereby minimizing production defects and costs.
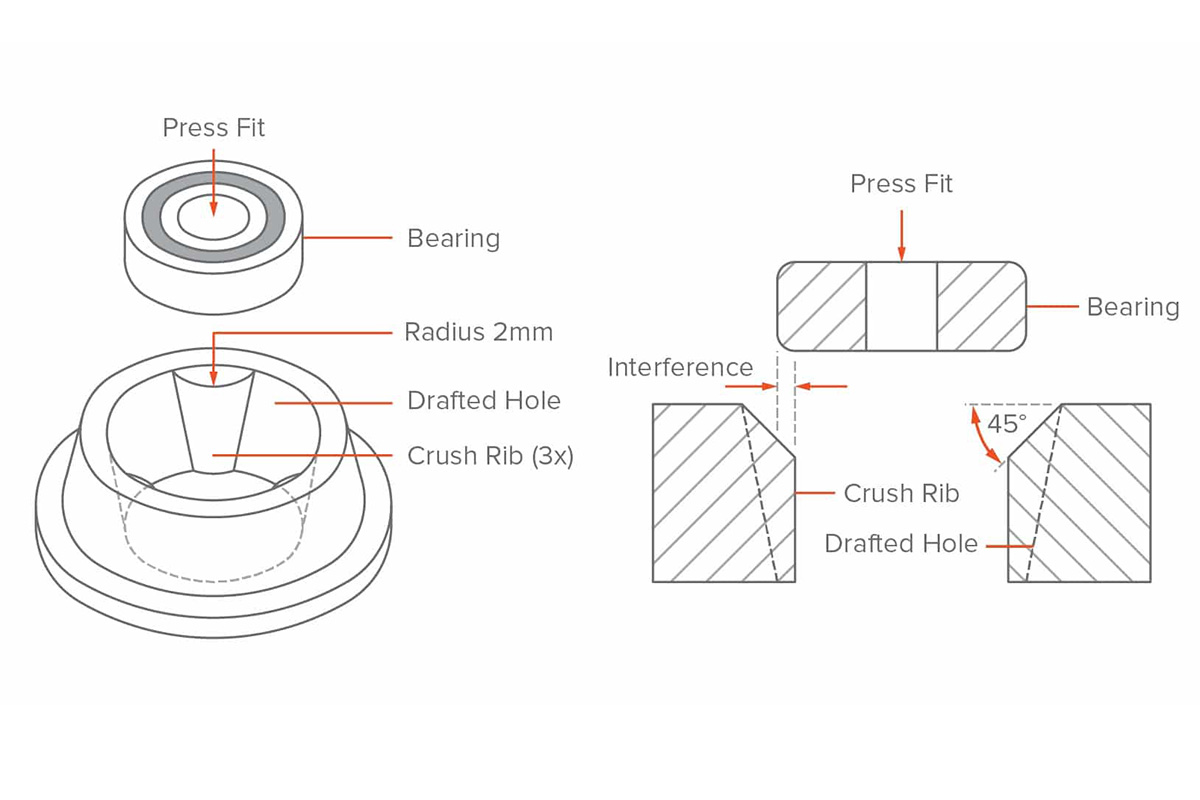
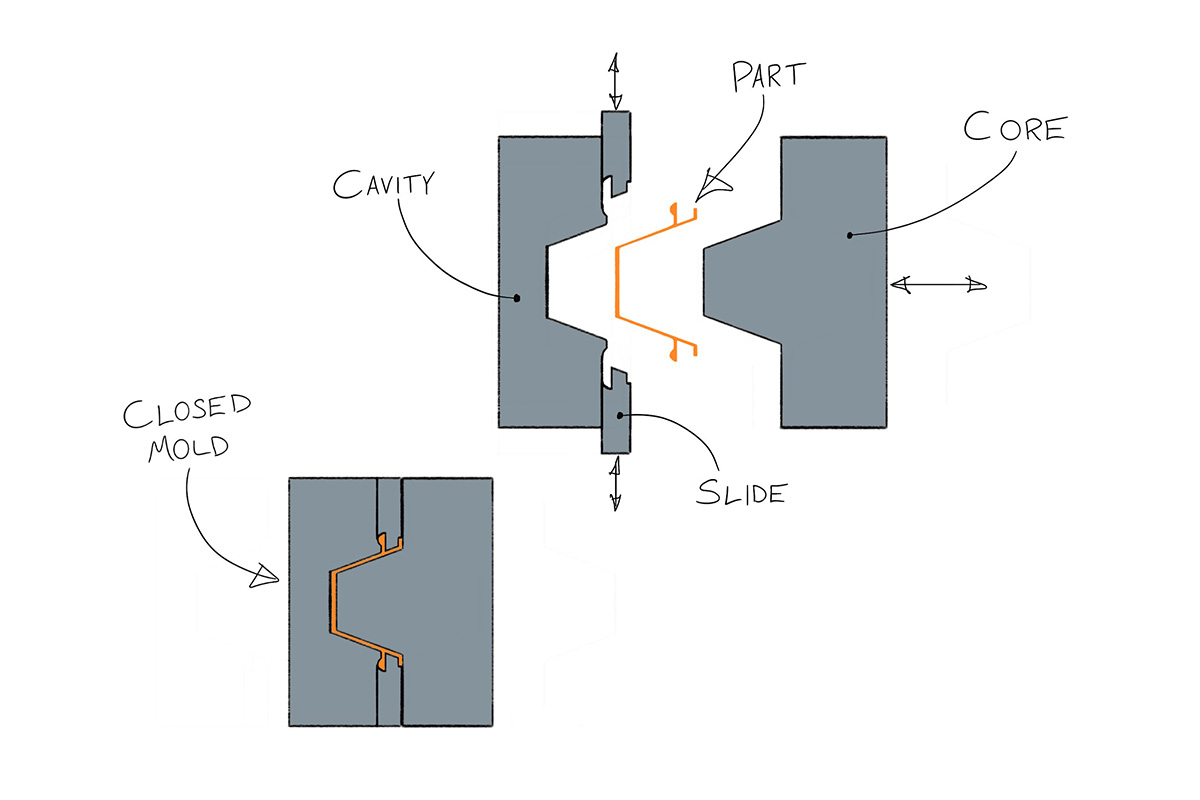
Parting Lines
Parting lines are the points where the two halves of the mold meet. The placement of parting lines significantly impacts the mold design and the aesthetics of the final product. If not carefully placed, parting lines can create cosmetic imperfections, and in some cases, they can affect the functionality of the part. Properly positioning parting lines where they won’t impact critical features or visual aspects can save time and money by reducing the need for additional finishing steps.
The Tradeoff Between Aesthetics and Production Costs
While aesthetic appeal is important, it often drives up production costs. Aesthetic design elements, like texture or multi-colored parts, can increase tooling complexity and cycle time.
- Complex Textures and Finishes: Parts that require intricate textures, glossy surfaces, or decorative features often need specialized molds or post-processing. These extra steps not only increase the mold cost but can also slow down the production process, raising per-unit costs.
- Multiple Colors or Decorations: Adding multiple colors or logos to parts may require extra steps in the injection molding process, such as color changes or specialized molds. These additional procedures increase both cost and cycle time.
Although aesthetics is important for consumer products, manufacturers need to balance them with cost efficiency. In some cases, opting for simpler designs or fewer steps of finishing may lead to a more cost-effective solution without sacrificing the product’s visual appeal that might be important for some industries.
8. Injection Molding Costs Across Different Production Volumes
Understanding how production volume affects the cost is crucial for making the right decisions for your project. Regardless of whether your production volume is low, medium, or high, each production scale presents different challenges and opportunities for cost management. Let’s delve into the cost differences under different production scales and explain the matters to be noted for each scale.
Low-Volume Production: When It Makes Sense and How to Estimate Costs
Low-volume production involves producing a small number of parts, typically for prototyping, testing, or small batch manufacturing. In this case, the main challenge is the high upfront costs related to tooling and mold creation. However, there are situations where low-volume production makes sense:
- Prototype Development: If you’re testing a new product or design, low-volume production allows you to quickly iterate and refine your parts before committing to a larger production run.
- Niche Markets: For products aimed at a limited audience or in industries where large production runs aren’t feasible, low-volume manufacturing is a cost-effective option.
- Tooling Costs: While high for low volumes, the cost can be reduced by using cheaper materials for molds or opting for methods like 3D printing for quick prototyping. Expect higher per-unit costs due to the low number of parts being produced.
- Material Costs: In small batches, raw material costs are higher per unit. Additionally, any material wastage becomes more significant in low-volume production.
Low-volume production is suitable when precision is required but you can manage the tradeoff between high upfront costs and smaller quantities.
Mid-Volume Production: Balancing Cost Efficiency and Speed
Medium-volume production usually involves hundreds to thousands of components. This approach offers a more balanced solution in terms of cost and speed. Its main goal is to optimize the production process in order to achieve a balance between tool investment and faster delivery times.
- Tooling Investment: The tooling cost per part is still significant but less impactful than in low-volume production, allowing for cost savings without a massive investment in molds.
- Material Costs: Mid-volume production benefits from some bulk purchasing discounts on materials. Though not as low as in high-volume runs, material costs start to become more manageable.
- Labor and Setup Costs: While still higher than high-volume production, labor and setup costs are spread over more parts, which helps reduce costs per part. Optimizing machine setups and minimizing downtime is essential to improve cost efficiency in mid-volume production.
- Cycle Time: Cycle times tend to be faster than in low-volume runs, reducing overall production time and allowing for a better per-unit cost.
Mid-volume production offers flexibility, enabling you to meet demand without committing to the high costs of mass production, and it’s often the most cost-effective for moderately complex products.
High-Volume Production: Achieving the Lowest Cost Per Part
High-volume production refers to the manufacturing of thousands to millions of parts. This is where the true economies of scale come into play. The cost per part continues to decrease as production volume increases, making it ideal for mass-market products. Key considerations for high-volume production include:
- Tooling Costs: Upfront tooling costs are significant, but they are minimized per unit as the number of parts produced increases. The investment in molds is spread across a large number of units, bringing down the cost.
- Material Costs: High-volume production benefits the most from bulk material purchasing, reducing the per-unit cost of raw materials. Manufacturers can negotiate better prices for large orders.
- Machine Efficiency: Machines are running more consistently, which helps reduce cycle times and the energy needed for each part. Automation and optimized workflows can lower labor costs and improve throughput.
- Labor Costs: With high-volume runs, automation can be used to reduce labor costs by limiting the need for manual intervention and decreasing human error.
High-volume production is the best option for industries where cost per part is critical, such as automotive, consumer goods, and electronics.
For your convenience, this is a comparison table with assumption data that more directly shows the cost differences between productions of different volumes:
Production Volume | Low-Volume (100 – 1,000 parts) | Mid-Volume (5,000 – 10,000 parts) | High-Volume (100,000 – 300,000 parts) | ||
Number of Parts | 100 – 1,000 | 5,000 – 10,000 | 100,000 – 300,000 | ||
Mold Cost | $100 – $1,000 | $2,500 – $5,000 | $25,000 – $75,000 | ||
Raw Material Cost per Part | $0.50 | $0.50 | $0.50 | ||
Total Material Cost | $50 – $500 |
|
$50,000 – $150,000 | ||
Labor Cost per Part | $3 | $2 | $1 | ||
Total Labor Cost | $300 – $3,000 | $10,000 – $20,000 | $100,000 – $300,000 | ||
Total Process Cost | $450 – $4,500 | $15,000 – $30,000 | $175,000 – $525,000 | ||
Cost per Part | $4.50 | $3 | $1.75 |
9. Strategies to Reduce Injection Molding Costs
Optimizing the cost of injection molds is of vital importance for enhancing the profitability of the manufacturing industry. Based on over 15 years of practical industry experience, the following are actionable strategies applicable at various production stages, which are based on real case studies and practical insights:
Implementing Design for Manufacturing (DfM) Practices
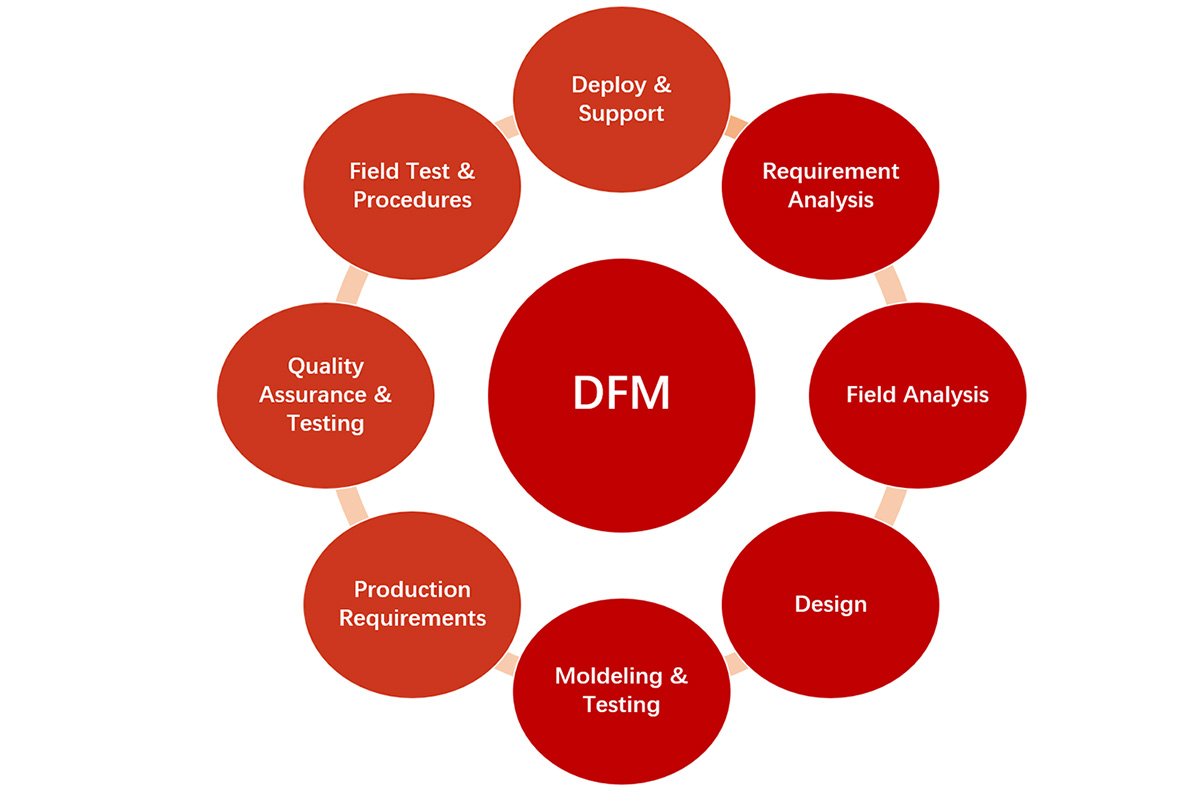
DfM transforms product design to align with manufacturing feasibility. Next we’ll illustrate some key approaches with real-world examples for your reference.
- Simplified Geometry Overhaul: A consumer electronics brand found us to adjust their mold design. After evaluating the problem, we managed to reduce shell mold costs by 34% by eliminating 5 unnecessary grooves and replacing sharp corners with radiuses. This method cut machining time by 28% and reduced trial molding cycles from 5 to 2.
- Material Cost Engineering: An industrial handle manufacturer swapped nylon 6 for 15% glass-filled PP, slashing material costs by 22%. The modified PP withstood 100,000 fatigue tests without failure, matching the original design’s strength specs.
- Assembly Integration Strategy: A home appliance OEM merged 3 separate control panel components into a single overmolded part, eliminating 2 screws and 1 welding step. This reduced assembly time from 75 seconds to 38 seconds per unit.
Simplifying Product Design to Minimize Mold Complexity
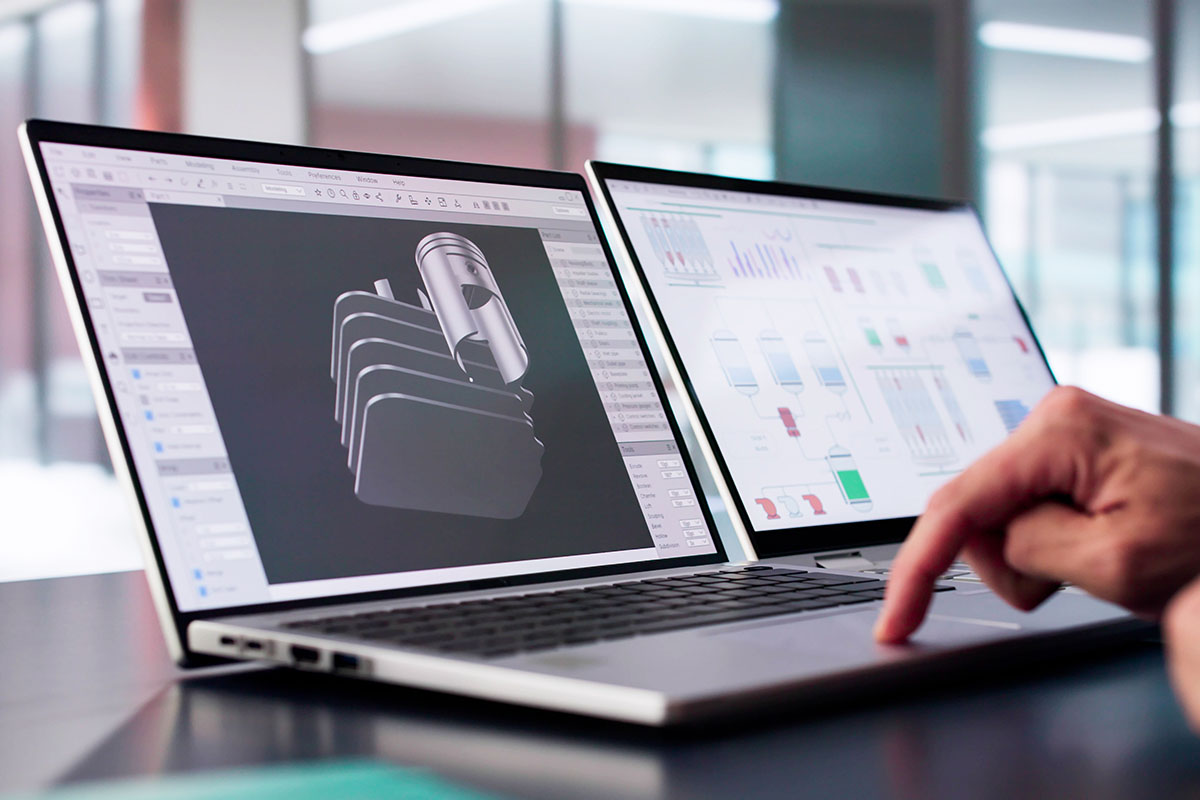
Mold simplicity directly impacts tooling expenses. Effective tactics include:
- Uniform Wall Thickness Redesign: A automotive interior supplier revised a door panel from 2.5-4mm variable thickness to 3mm uniform walls. This cut cooling time by 17%, reduced warpage defects from 11% to 3%, and saved $29,000 annually in rework costs.
- Undercut Elimination Techniques: A medical device firm replaced a 4-side undercut design with angled lifters, eliminating the need for 2 slide cores. The mold cost dropped by 27%, and ejection failures fell from 8% to <1%.
- Surface Finish Rationalization: Not every part needs a mirror finish – cut surface finishing processing at the right time can simplify production and reduce cost. An outdoor equipment brand changed a housing’s surface spec from Ra0.8 to Ra3.2, cutting post-molding steps from three to one. Finishing costs? Down 45%.
Reducing the Number of Cavities in the Mold
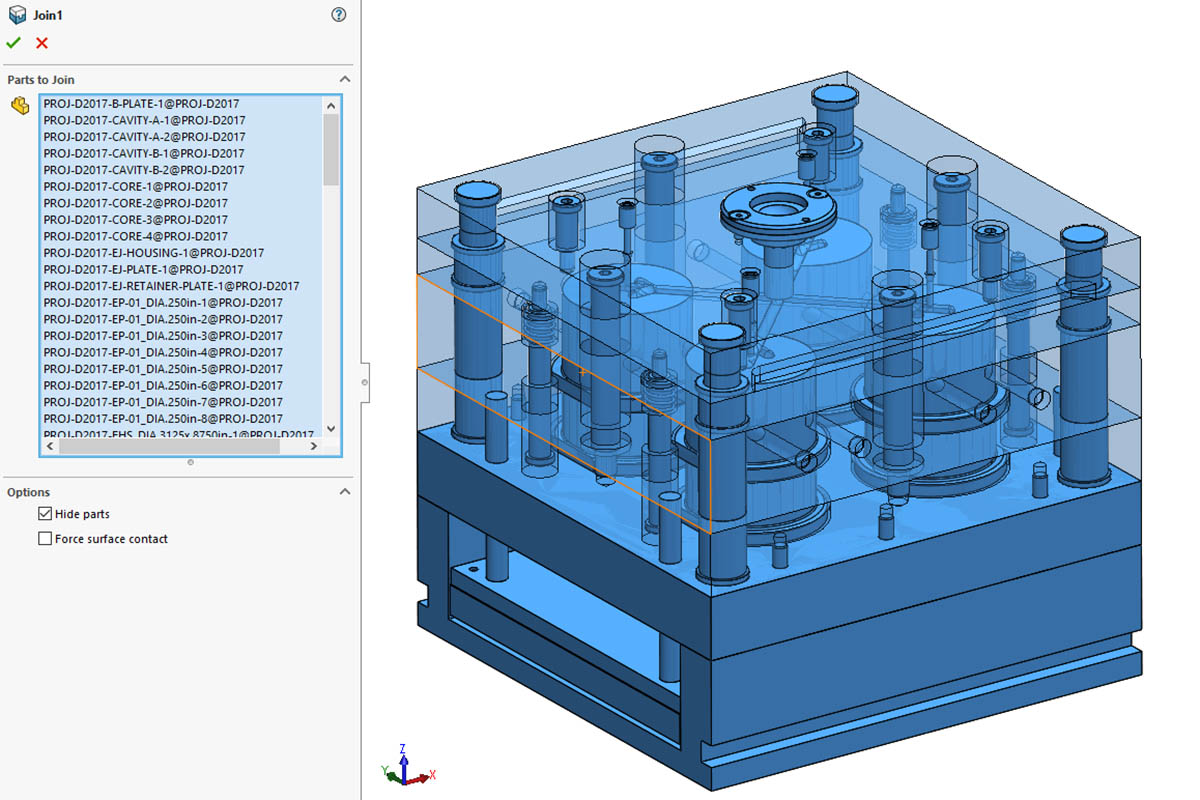
Cavity number must align with production volume, these are experiences from our clients or industry peers:
- Low-Volume Cavity Strategy: A startup producing 2,000 units/year opted for a single-cavity aluminum mold instead of a 4-cavity steel mold, saving $48,000 in initial tooling costs. The per-part cost remained competitive at $1.20 vs. $0.95 for high-cavity tools.
- Precision Cavity Optimization: A medical syringe manufacturer used a 2-cavity hot runner mold for 50,000 units/year, achieving ±0.02mm tolerance on the plunger fit. This reduced scrap to 0.3% versus 5% with multi-cavity tools.
- Maintenance Cost Forecasting: A 4-cavity mold for automotive brackets required $6,200/year in maintenance, 62% less than an 8-cavity mold’s $16,500 annual upkeep (based on 3-shift operation).
Strategic Material Selection Tactics
Balancing performance and cost requires:
- Commodity Resin Upgrades: A packaging company switched from HDPE to a metallocene-catalyzed PP grade, improving flow by 25%. This allowed reducing wall thickness by 18%, saving $17,000/year in material costs while maintaining drop test performance.
- Recycled Material Integration: An electronics enclosure manufacturer used 40% post-industrial recycled PC/ABS for non-visible parts, achieving 21% material cost savings. The recycled material met UL94 V-0 flammability standards with no impact on mechanical properties.
- Additive Cost Engineering: A furniture manufacturer added 20% talc to PP for table legs, reducing shrinkage from 2.5% to 1.2%. This eliminated the need for post-molding annealing, saving $9,500/year in energy costs.
The Advantages of Insert Molding and Overmolding
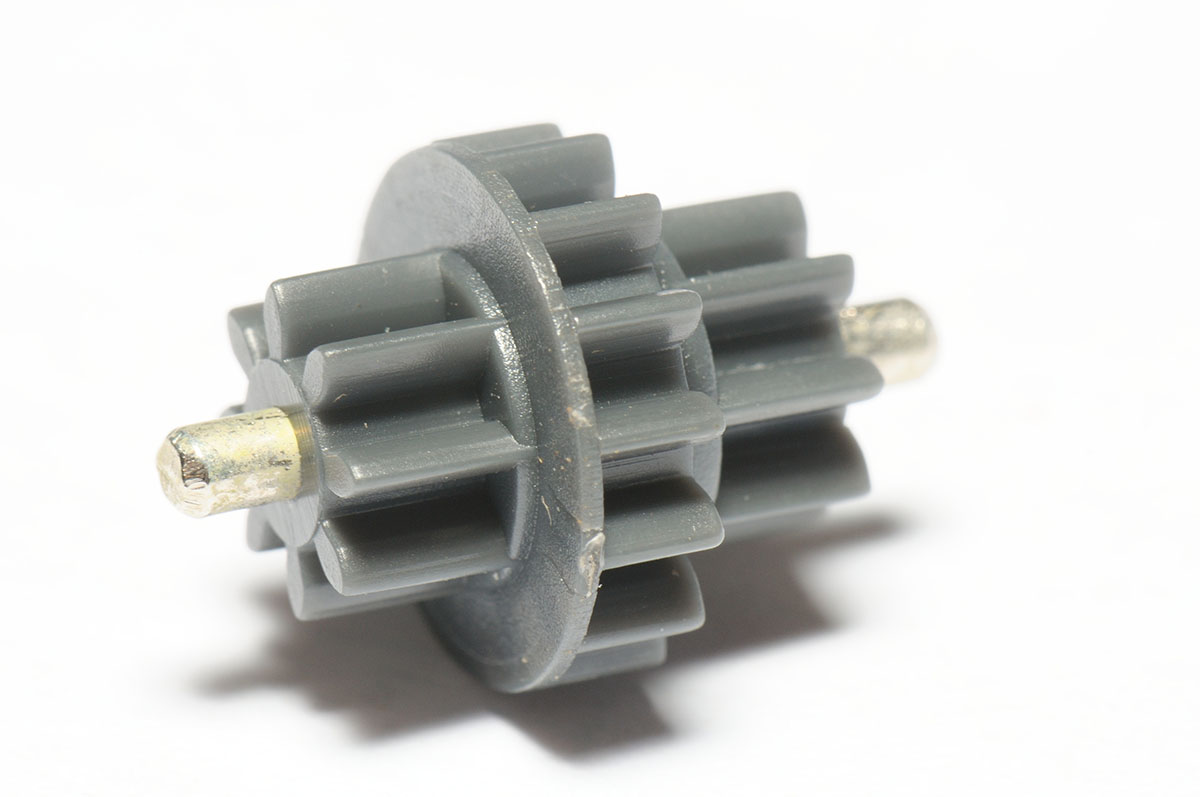
- Insert Molding Case Study: A power tool manufacturer embedded metal threads directly into plastic housings, eliminating 4 manual tapping steps. This reduced cycle time from 42 seconds to 29 seconds and saved $3.20 per unit in labor costs.
- Overmolding Efficiency Gains: A garden tool handle used TPE overmolding on a PP core, achieving non-slip grip in one step. Compared to adhesive bonding, this reduced production steps from 5 to 2, lowering costs by 38%.
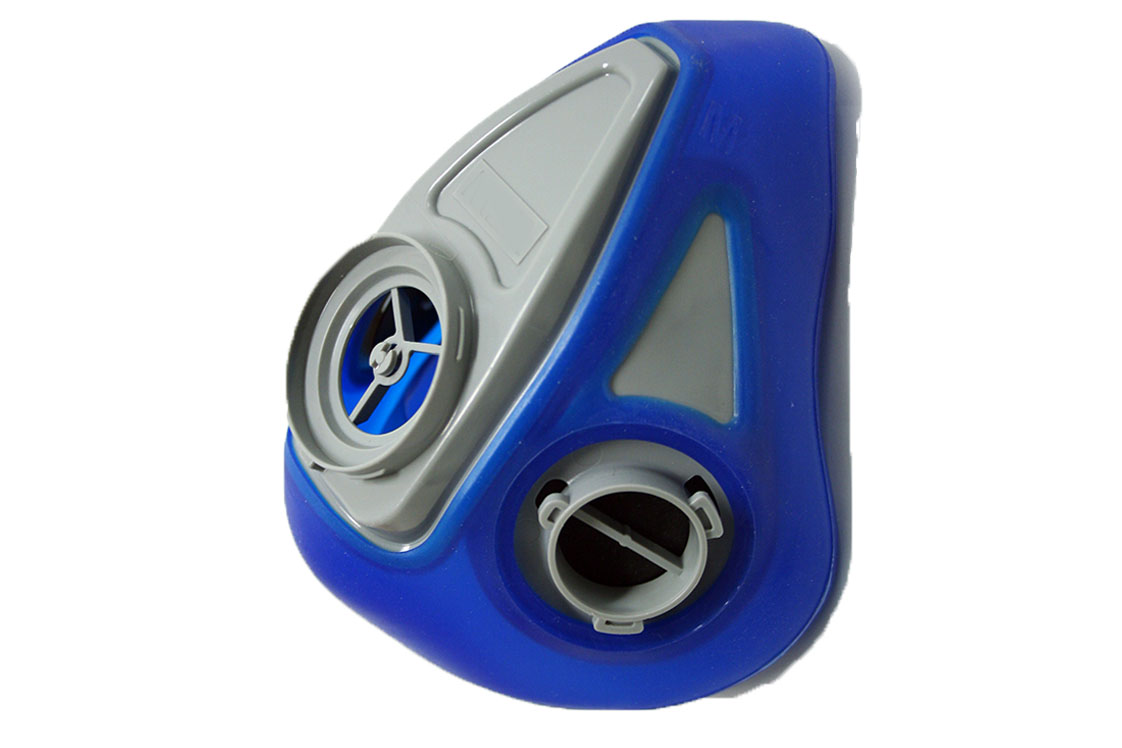
How Self-Mating Parts Can Simplify Design and Reduce Costs
Self-mating parts are designed to lock into place without the need for additional fasteners or assembly tools. This can help simplify the entire production process.
- No need for additional fasteners: By eliminating screws, clips, or rivets, manufacturers can save on parts and assembly labor.
- Faster assembly process: Self-mating parts reduce assembly time, directly lowering labor costs.
- Reduced part count: Fewer components mean less storage and handling, reducing logistics and inventory costs.
These design features lead to significant savings in both material costs and labor costs throughout production.
Leveraging Rapid Tooling to Speed Up Production and Reduce Costs
Rapid tooling methods allow for quicker mold production, especially for low-volume and prototype runs, which can be a huge cost saver in the early stages of product development.
- Quick mold creation: Techniques like 3D printing or aluminum tooling can create molds quickly, reducing lead times and speeding up production.
- Lower initial tooling costs: Rapid tooling methods can be significantly less expensive than traditional steel molds, making them ideal for short production runs.
- Fast prototyping: This method allows for quick iteration of product designs, ensuring that any issues can be identified and addressed before mass production begins.
Adopting New Technologies to Reduce Costs
In addition to traditional cost-reduction strategies, adopting new molding technologies can offer significant savings by improving efficiency and reducing production times.
a. Assisted Molding Technologies
Utilizing technologies such as gas-assisted, liquid-assisted, steam-assisted, and micro-foam injection molding can help enhance production efficiency and reduce material costs.
- Gas-assisted molding: Reduces the material used in parts by creating hollow sections, lowering material costs and cycle times.
- Liquid-assisted molding: Improves the uniformity of complex parts, reducing the need for secondary operations and improving overall part quality.
- Steam-assisted molding: Offers faster cooling times, reducing cycle times and energy consumption, which can contribute to lower production costs.
b. Unitary Molding Solutions
Unitary molding solutions aim to eliminate intermediate manufacturing steps, thus reducing costs and production time.
- Streamlined process: Directly integrates multiple steps (such as assembly and part joining) into the molding process, eliminating the need for extra operations.
- Fewer components: Reduces the number of parts that need to be handled, stored, and assembled, further cutting down on logistics and labor costs.
c. New Mold Technologies
Adopting advanced mold technologies can increase efficiency and lower tooling costs.
- In-mold welding: Allows for the joining of parts within the mold, reducing post-production assembly steps.
- In-mold spraying: Applies coatings during the molding process, enhancing part functionality and reducing secondary operations like painting or coating.
- In-mold assembly and decoration: These techniques integrate additional components or aesthetic features during the molding process, reducing the need for later assembly or decoration.
Sustainable cost reduction in injection molding requires a synergistic approach. That might be hard for some manufacturers, but don’t worry, at KingStar Mold, our 300+ projects demonstrate that balanced cost-quality solutions are possible. A medical client reduced costs by 31% through strategic cavity optimization and material substitution, maintaining ISO 13485 compliance.
No matter what production volume you want, contact us to develop a tailored cost roadmap for your specific manufacturing needs.
Note: All examples are drawn from actual projects, with numbers adjusted to protect client info while keeping the economics real.