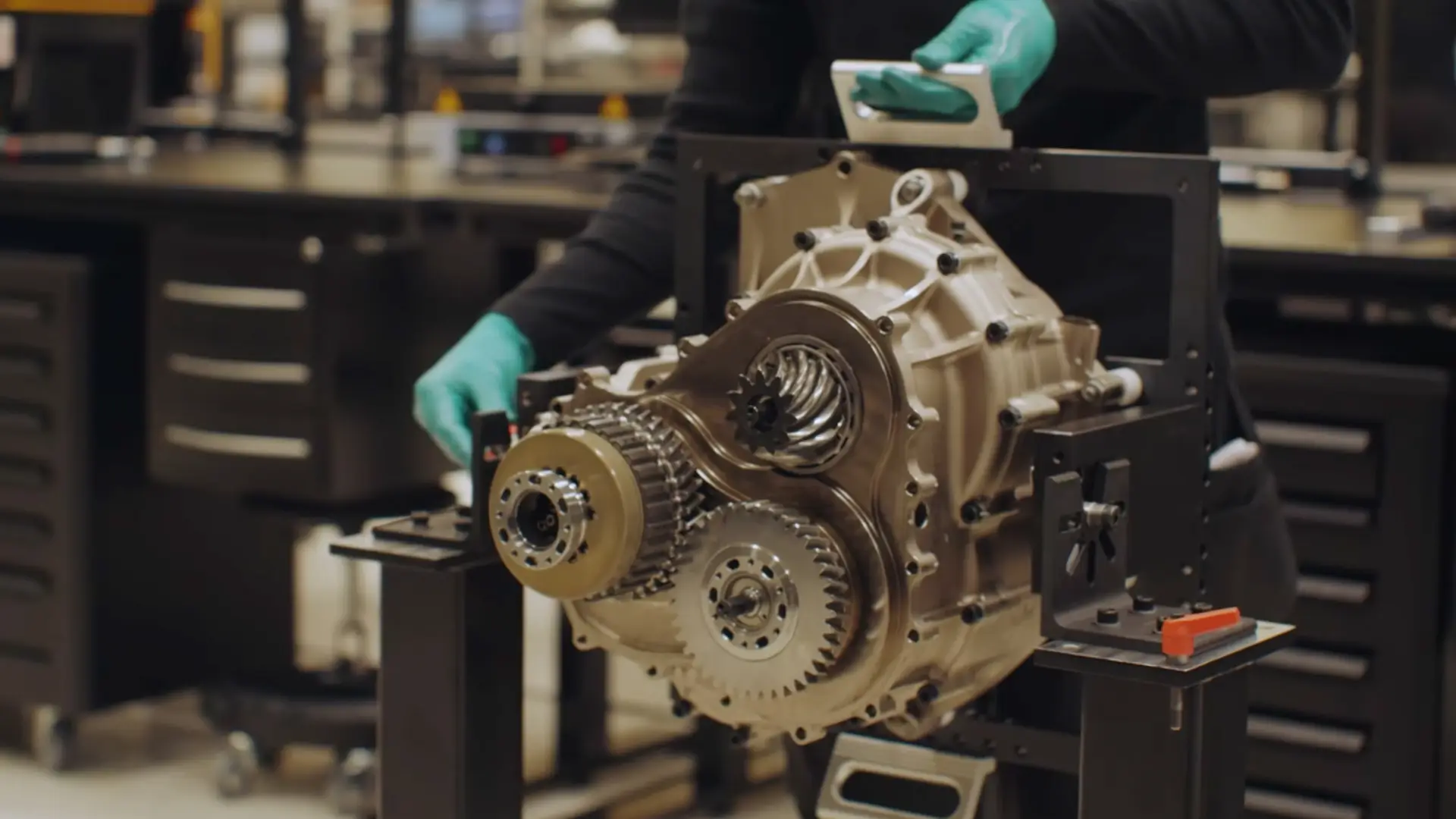
Properties of Inconel 718
Resolution | Condition | Ultimate Tensile Strength | Hardness | Elongation | Yield Stress |
---|---|---|---|---|---|
20 μm | Stress Relieved | 143 ksi / 986 Mpa | 33 HRC | 36% | 98 ksi / 676 Mpa |
30 μm | Stress Relieved | 144 ksi / 993 Mpa | 30 HRC | 39% | 91 ksi / 627 Mpa |
30 μm | Solution & Aged per AMS 5663 | 208 ksi / 1434 Mpa | 46 HRC | 18% | 175 ksi / 1207 Mpa |
60 μm | Stress Relieved | 139 ksi / 958 Mpa | 27 HRC | 40% | 83 ksi / 572 Mpa |
60 μm | Solution & Aged per AMS 5663 | 201 ksi / 1386 Mpa | 45 HRC | 19% | 174 ksi / 1200 Mpa |
Automotive
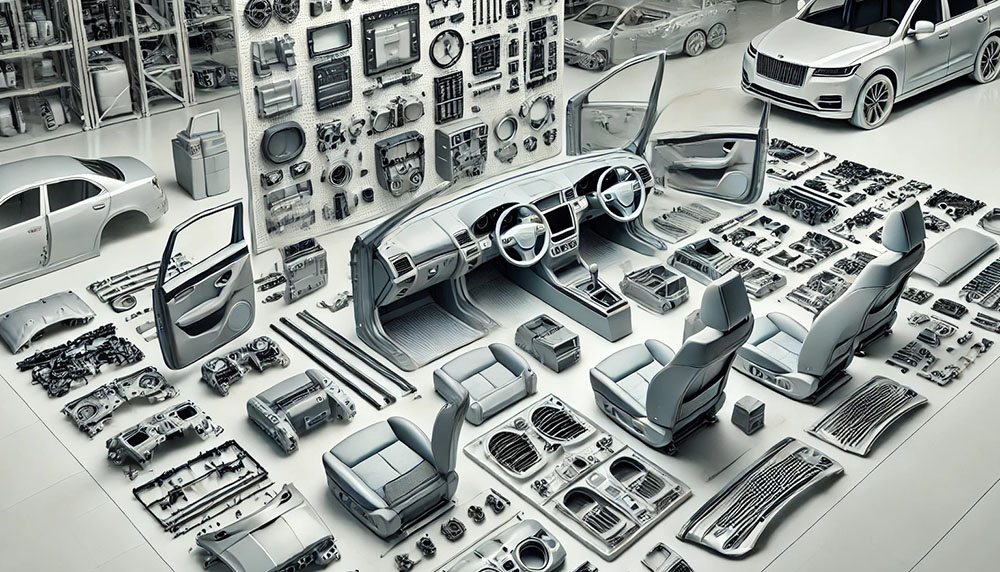
Aerospace
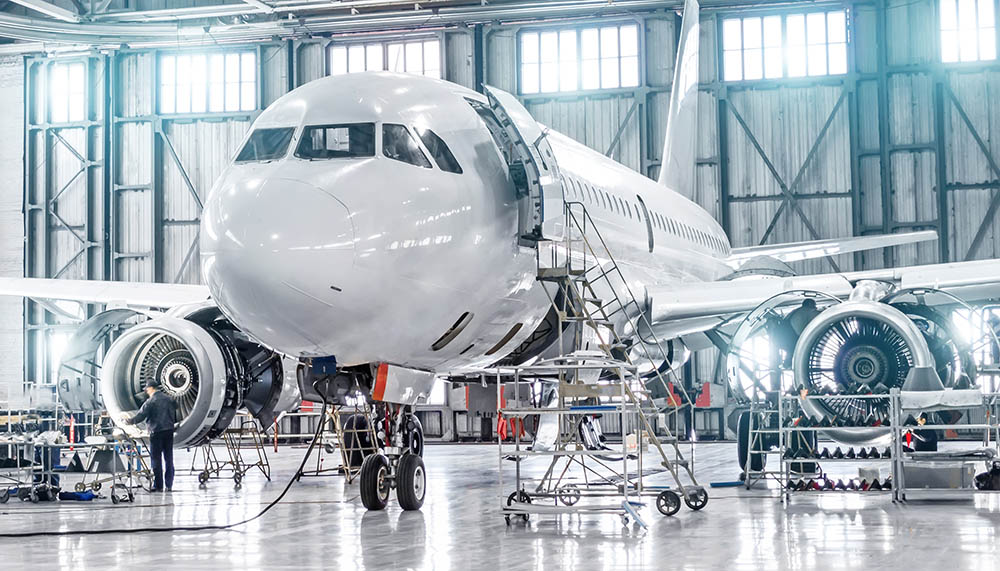
Industrial Equipment
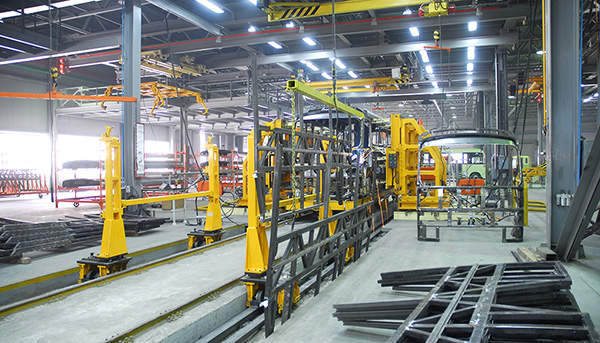
Energy
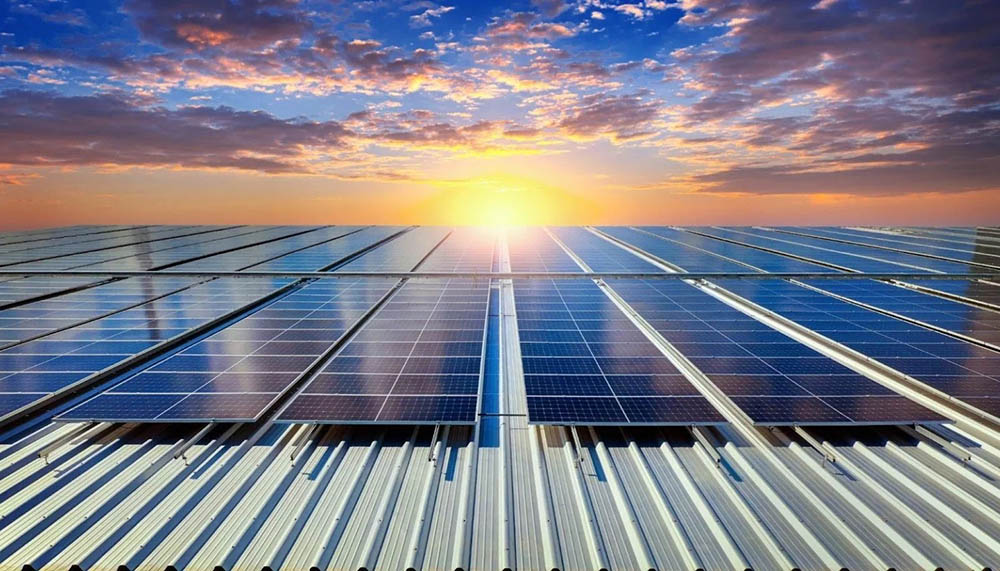
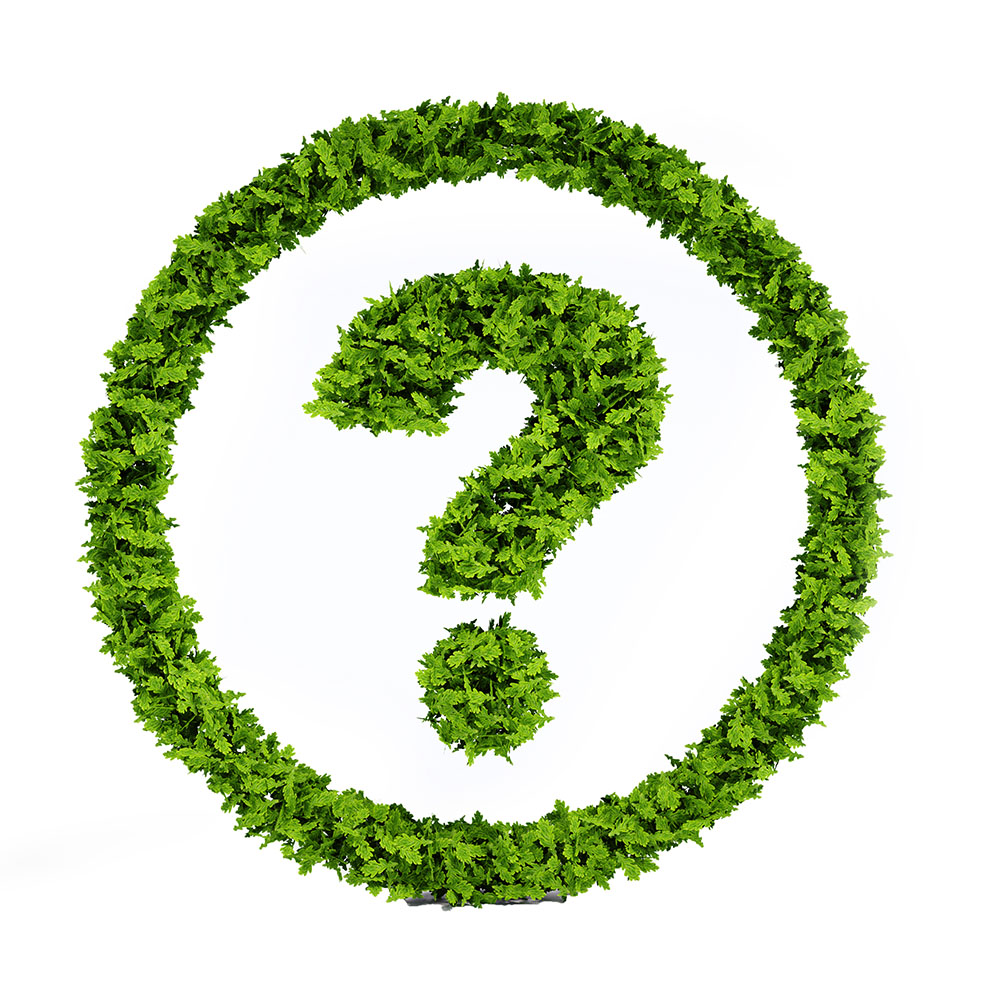
Inconel 718 parts typically require stress relief, solution annealing, and aging processes to enhance tensile strength and hardness.
KingStar Mold employs precise manufacturing techniques, including stress relief and post-processing, to ensure high-quality Inconel 718 parts that meet stringent performance standards.
The maximum part size for Inconel 718 3D printing is 31.5″ x 15.7″ x 19.7″ (800mm x 400mm x 500mm).
Inconel 718 is commonly used in aerospace, automotive, energy, and industrial applications due to its high strength and resistance to extreme temperatures.
Inconel 718 is commonly used to create turbine blades, exhaust components, heat exchangers, and other high-stress, high-temperature parts.
Yes, KingStar Mold can produce large Inconel 718 parts with high precision, making it ideal for manufacturing components for aerospace and energy applications.
Inconel 718 excels in environments with high temperatures and mechanical loading, making it ideal for critical applications.
Inconel 718 offers exceptional oxidation and corrosion resistance, along with high-performance tensile, fatigue, and creep strength.