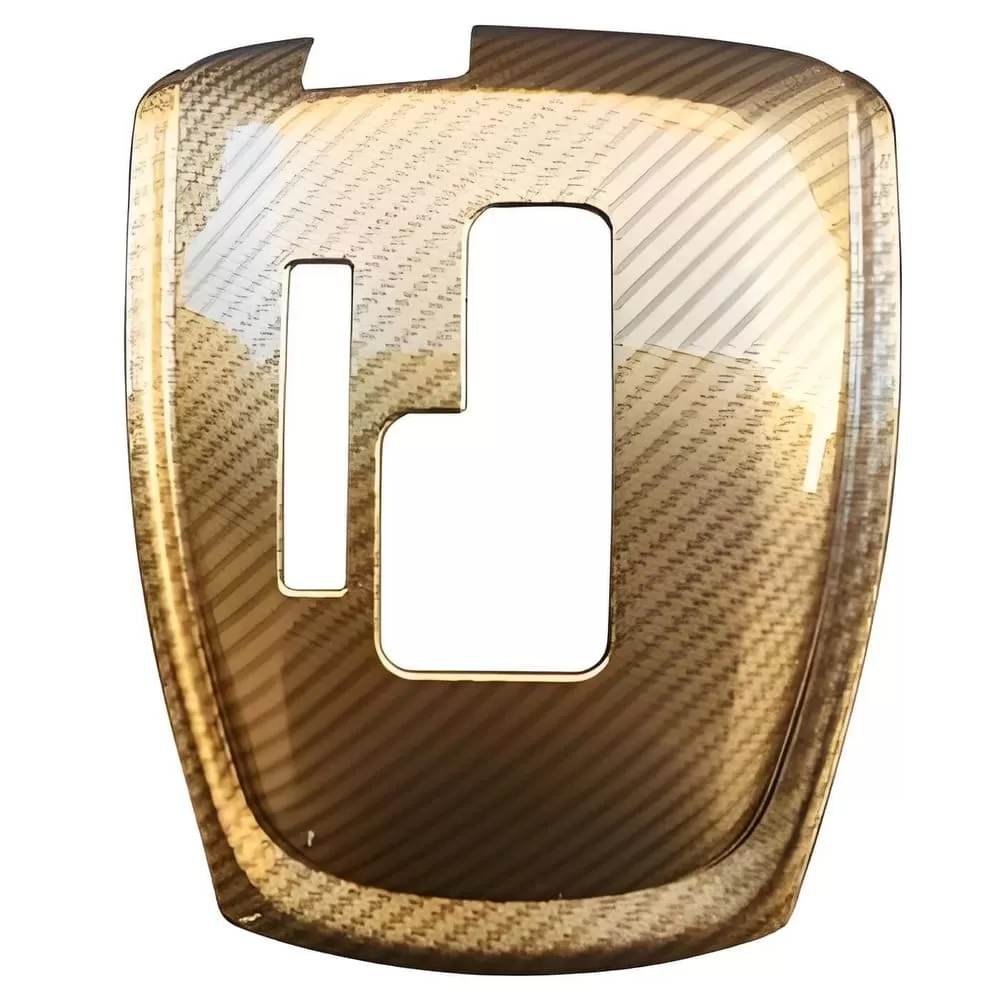
-
Resources for The Guide Throughout the Whole process to PVC Injection Molding
What is IMD?
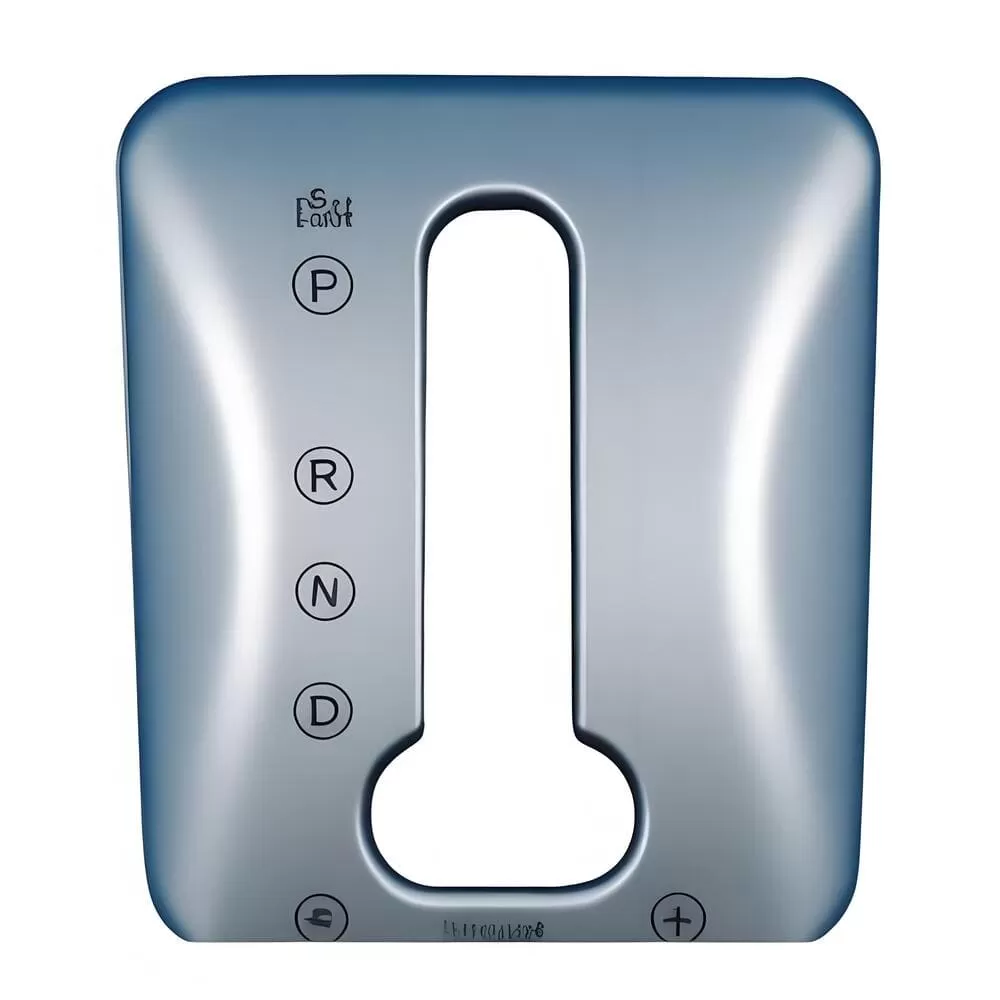
The guide of IMD injection mold design and molding process.
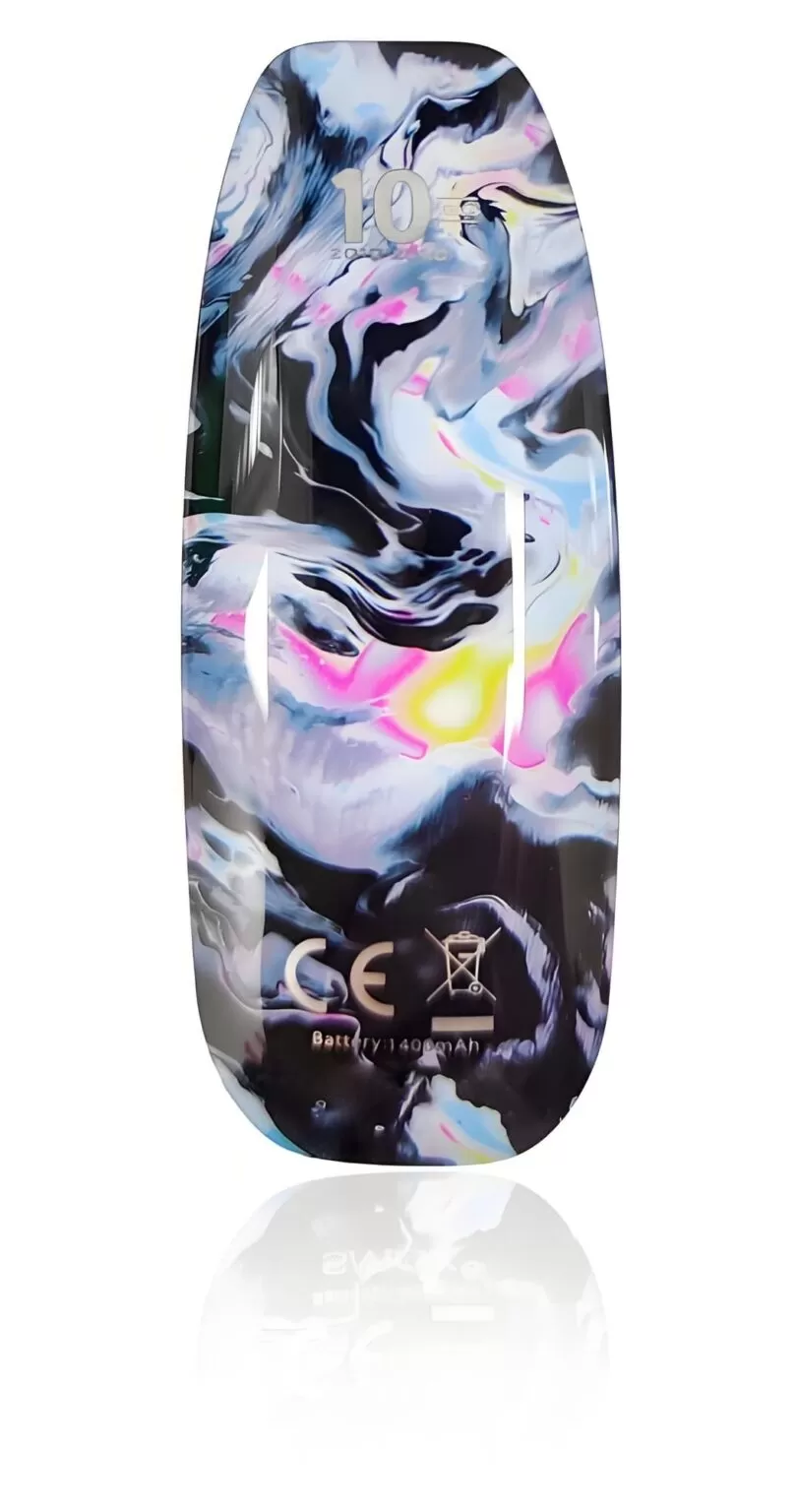
b. Pre-Made Sheets (Thermoforming, Cutting, and more)
The Overall Process Workflow for pre-made sheets involves the following steps:
- Printing
- Tools: Film, screen printing machine.
- Key Points:
- Selecting appropriate ink for durability and adhesion.
- Ensuring accurate sheet positioning for precise results.
- Apply Protective Film
- Purpose: To safeguard the sheet and prevent dust contamination.
- Material: PE film is commonly used.
- Shape Punching
- Tool: Die.
- Key Points: Accurate sheet positioning to ensure uniform punching.
- Apply Protective Film
- Reapplied to protect the sheet during subsequent processes.
- Heat Setting
- Tool: Heat setting machine.
- Key Points:
- Precise temperature control to prevent deformation and minimize scrap rates.
- Upper and lower molds equipped with heating plates to maintain a consistent temperature.
Detailed Heat Setting Process:
- The sheet is placed on the heat setting machine.
- The movable heating plate moves over the sheet to preheat and soften it.
- Once preheated, the mold closes for heat setting, shaping the sheet into the desired form.
Proper handling of the heat setting process is crucial to achieve high-quality results and avoid unnecessary waste.
c. Fitting Between Sheet and Cavity
- Sheet Size Principle: The sheet must be slightly smaller than the final part size.
- Reason: This allows the sheet to fit easily into the mold cavity and ensures full stretching during the molding process. If the sheet is too large, it may cause wrinkles, resulting in defective products.
2. Mold Shrinkage
- Typical Shrinkage Rates:
- ABS and PMMA generally shrink by 0.5%.
- In IMD molds, due to the PET film layer on the product’s surface, shrinkage is reduced.
- IMD Mold Consideration:
- Shrinkage for IMD-produced parts is usually 0.3%, as the PET sheet wrapping the plastic substrate during injection molding limits shrinkage. This is lower than the shrinkage for ordinary molds.
3. Sheet Forming Mold Design
- a. Sheet 3D Model:
- Use product images in Pro/E or similar 3D software.
- Offset the product surface inward by the sheet’s thickness to create a 3D model of the sheet.
- b. Die and Film Creation:
- Based on the 3D sheet drawing, unfold it to create the necessary tools, such as dies and films, for sheet punching.
- c. Mold Separation:
- Separate the mold into parts based on the 3D sheet design.
- d. Mold Manufacturing:
- Manufacture the mold components to the specified design.
By adhering to these steps and principles, you can ensure high-quality sheet forming and injection molding for IMD applications.
What are the characteristics of IMD injection molding?
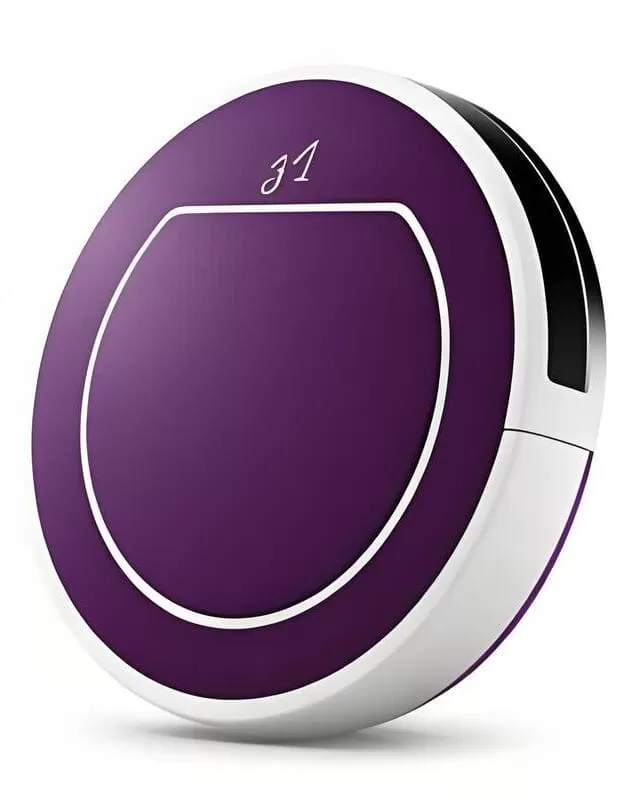
① The product offers exceptional durability and scratch resistance.
② Complex visual designs can be easily achieved with consistent results, something other processes cannot match.
③ It supports a wide range of colors, even in small production runs, including the ability to print over four colors and metallic inks.
④ Design changes can be made without requiring additional molds, leading to substantial cost reductions.
⑤ One-piece molding exclude the need for color separation and disassembly, accelerating the design and development process.
⑥ The product features high color contrast, and the plastic material allows light transmission, making it ideal for screens and light guide columns.
⑦ The product has excellent chemical resistance due to its extremely durable and flexible surface printing. The image is actually printed on the inside of the film.
⑧ Plastics and films can be recycled and reused.
⑨ The product can meet precision requirements and enable efficient mass production through automation.
The top tips for IMD injection molding
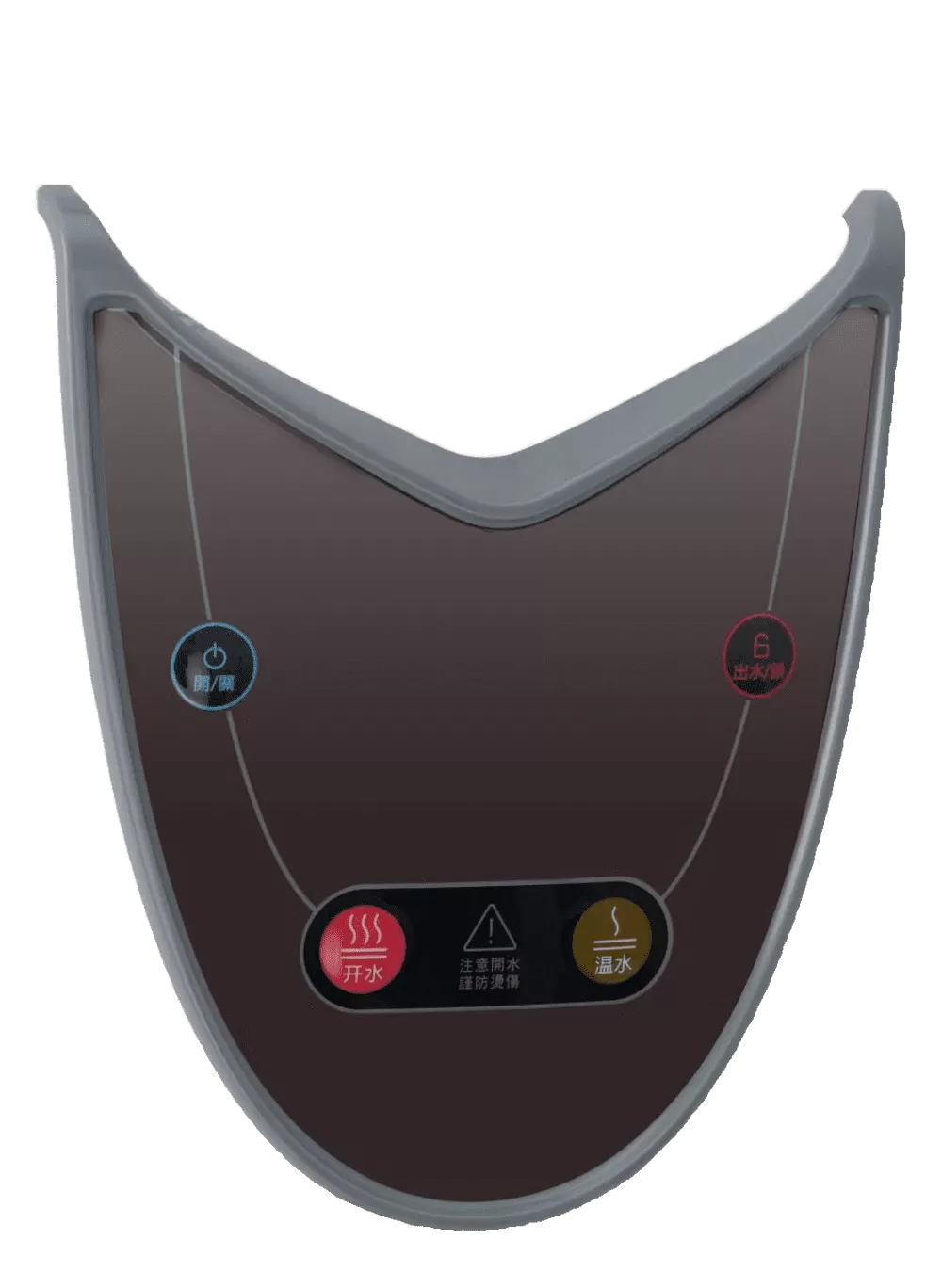
① A shorter runner design is preferable, with hot runners being the ideal choice.
② Consider increasing the gate area or using multi-point gates.
③ Opt for plastics that have better flow and inject them at a lower temperature.
④ To prevent ink from being flushed out, add it at the gate.
⑤ Ensure that the IMD injection mold cavity and mold shape align properly.
⑥ Avoid selecting the highest stretch points for the injection material, usually at the four corners, as these areas are thinner, expand and contract more, and are prone to wrinkles.
⑦ Since IMD injection conditions tend to be consistent, using an injection molding machine with superior control is recommended. Additionally, the plastic’s physical properties should be uniform.
⑧ Since the FILM expands and contracts with temperature changes, the mold temperature should not be too high during molding. Using a mold temperature machine is a good approach.
⑨ The presence of film inside causes thicker areas to shrink more. Traditional methods like holding pressure and overpacking won’t solve the shrinkage issue. The solution lies in reducing the material and making the part hollow.
IMD Injection Molding: Common Problems and Solutions
IMD (In-Mold Decoration) injection molding is a sophisticated process that demands accurate control over multiple variables to achieve optimal results. Here are some common challenges encountered in IMD injection molding and their corresponding solutions:
Common Problems | Causes and Solutions |
The pattern ink is scattered (washed) away during IMD injection molding | IMD ink is dry and doesn't let anything through. It has leftover solvents and air bubbles. When you're injection molding, the ink spreads and doesn't stick to the sheet as well. |
IMD silver ink takes longer to dry | |
As the IMD sheet gets thicker, the area where the ink spreads out gets bigger. | |
It depends on whether the gate design has a good structure, shape, and distribution. | |
It depends on the plastic temperature. When the injection resin temperature goes up, the area that gets washed away goes down. The temperature setting depends on the plastic type and injection mold structure. | |
IMD ink layer printed too thin | |
IMD ink itself is not resistant to high temperatures | |
Failure to dehumidify the plastic before injection molding leads to the formation of bubbles during the process. | |
Incorrect viscosity adjustment of the ink prior to screen printing causes pinholes and uneven leveling in the ink layer. |
|
IMD doesn't stick very well and the sheet comes apart easily. | There is residual solvent in the ink |
The pressure, temperature, and cooling system of the injection molding machine are not properly regulated. | |
The silver ink is either overly saturated or incompatible with the injection molding process. | |
The ink doesn't stick to the substrate very well. | |
No printed IMD water-based adhesive | |
Mirror ink is too close to the curved edge | |
The plastic has moisture in it. | |
The adhesion of ink is related to the temperature of injection resin | |
Mirror ink has no mirror effect | The sheet (substrate) can't handle the solvents in the mirror ink. |
It should be dried immediately after printing | |
Mirror ink should be printed with water-based adhesive | |
To make the ink stick better and get a mirror effect, add a hardener to the water-based adhesive. But use it all up within two hours of adding the hardener. | |
When embossing, the ink breaks | The corner of the punch is too sharp and should have a certain arc. |
The ink isn't soft enough. | |
Improper viscosity adjustment of the ink can lead to issues... For instance, ink that dries too slowly may cause smudging during the process. |
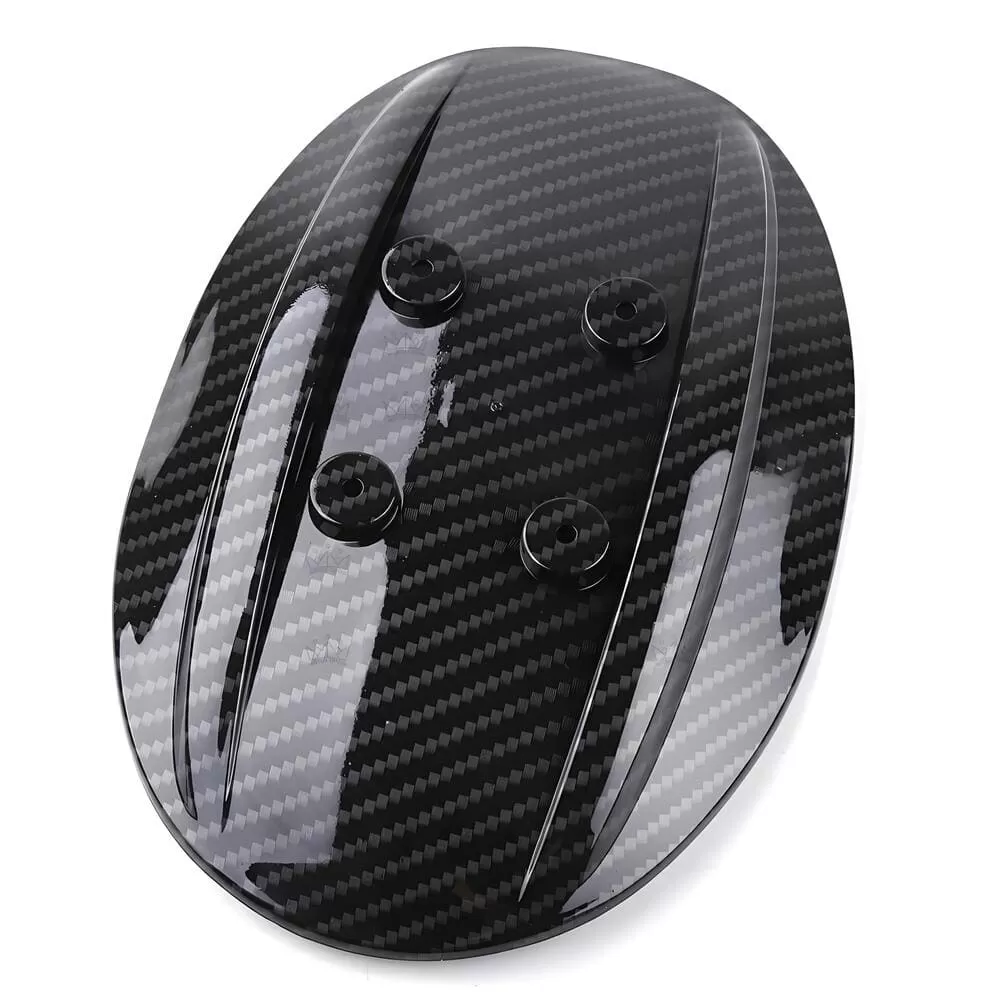
What are the characteristics of IML process?
IMD/IML products offer several advantages, including high definition, excellent three-dimensional effects, scratch-resistant surfaces, and the flexibility to change design patterns. They enhance the product’s appearance and reflect its perfect special-shaped structure. These technologies are widely used in applications such as mobile phone lenses and casings, where 3D design is crucial. IMD/IML overcomes the limitations of acrylic flat panels by enabling special-shaped effects and multiple color applications that were previously difficult to achieve.
In-mold decoration has become an excellent alternative to many traditional processes, such as thermal transfer, direct surface printing, direct electroplating, surface spraying, , and two-color injection molding. It is particularly suited for 3D products, especially those requiring consistent color registration, backlighting, multiple colors, and decoration on curved, cambered, or inclined surfaces.
IML Injection Molding VS IMD Injection Molding
IMD Injecton Molding | IML Injecton Molding |
IMD is suitable for large batches (100,000 or more) | IML production batch quantity is very flexible |
IMD products with three-dimensional molding height of IMD pattern not exceeding 1.5MM | IML technology is capable of handling diverse and intricate 3D productions, including flat surfaces, curved designs, and hemming applications. The molding height for 3D patterns can extend up to 40mm. |
IMD products, because the ink is screen-printed on the surface, the fonts are not easily touched. | IML ink is screen-printed in the middle layer, so the appearance is smooth and beautiful, the more you touch it, the brighter it becomes. It has excellent scratch resistance, and the pattern and color can be changed at any time during production. |
IMD can only screen print the same process as hot stamping paper, and cannot change its screen printing color. | IML's ink colors are unlimited, and the screen printing color can be changed at will in the same batch of production. |
IMD cannot make button products | IML can make products with buttons |
IML has a relatively short development cycle, as molds for shaping, cutting, and injection can be developed concurrently alongside auxiliary processes. This efficiency allows for the simultaneous production of multiple components, reducing overall costs. Moreover, the absence of hooks enables the creation of thinner products. | The overall development time of IMD is longer |
What are the advantages and disadvantages of IML process
In-Mold Labeling (IML) is a widely used packaging technology in industries such as food, beverage, cosmetics, and pharmaceuticals. Below are the advantages and disadvantages of the IML process:
Advantages | Disadvantages |
Film production cycle is short and can express multiple colors | Long initial period |
Patterns and colors can be changed at any time during production | It is easy to cause the film to fall off, twist and deform, etc. |
The outermost layer of IML is FILM, and the ink is screen-printed on the middle layer. The appearance is smooth and beautiful, the more you touch it, the brighter it becomes, and it has excellent scratch resistance. | During the production process, the product defect rate is high |
IML production batch quantity is very flexible and suitable for small-volume production of multiple varieties |
The complete guide to IML injection molding
⑩ Rounded Corner Design:
- IMD/IML molding cannot create sharp edges. The appearance outline should avoid sharp corners, and all corners must have a rounded radius of at least 0.3R.
⑪ Hemming Issue:
- Hemming refers to the edge where the film and plastic meet, which may not be very clean after injection molding. To address this, the product design can incorporate plastic parts to cover the edge where the film and plastic connect.
⑫ Requirement for Surface Wear Resistance Hardness:
- The product surface must achieve a wear resistance hardness rating of above 3H to guarantee long-term durability.
How to test and verify IML products?
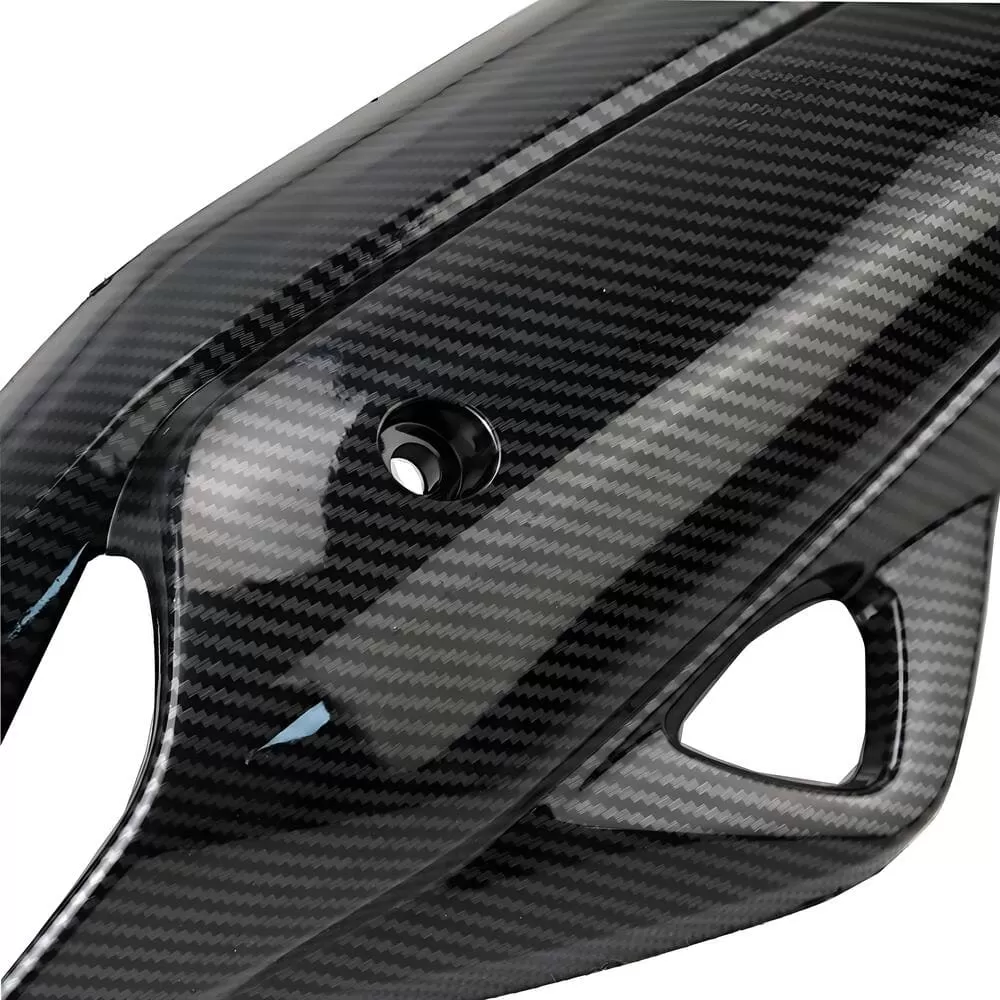