Selecting the right sheet metal material is a crucial step in product design, especially for sheet metal fabrication, as it directly impacts various aspects of manufacturing and the performance of the end product. The material you choose will determine the strength and durability of the final product, as well as how it will perform under different conditions, such as exposure to heat, moisture, or stress.
The choice of material affects several key factors:
- Cost: Materials with higher strength or specialized properties may increase manufacturing costs, while more common materials may reduce expenses.
- Durability: The material’s ability to withstand wear, corrosion, and environmental factors ensures that the product performs well over time.
- Manufacturability: Some materials are easier to process and work with during fabrication, which can reduce production time and complexity.
In this guide, we’ll explore key sheet metal materials used in product design and highlight their strengths, weaknesses, and typical applications. This knowledge will help you make informed decisions, optimizing both the performance and cost-efficiency of your product.
- 1. Key Factors to Consider When Selecting Sheet Metal Materials
- 2. Cold Rolled Close Annealed Steel (CRCA)
- 3. Galvanized Iron (GI)
- 4. Aluzinc Steel
- 5. Aluminum Alloys
- 6. Stainless Steel
- 7. Comparison Table: Material Properties at a Glance
- 8. Material Selection Process in Sheet Metal Design
- 9. Tips to Optimize Material Usage
- Conclusion
1. Key Factors to Consider When Selecting Sheet Metal Materials
When choosing sheet metal materials for a project, several factors must be evaluated to ensure that the material will meet both the performance and cost requirements of the design. Here are the key considerations:
1.1 Mechanical Loads and Structural Requirements
The material must be able to withstand the mechanical loads that the product will experience during its use. This includes factors like tension, compression, shear, and bending forces. Materials with higher tensile strength, such as stainless steel, are ideal for parts that will bear heavy loads or endure high-stress conditions. Evaluating the specific mechanical needs of the product will help you select the material with the appropriate strength and rigidity.
1.2 Weight Considerations in Product Design
The weight of the material can significantly affect the product’s performance, especially for industries like automotive or aerospace. Lightweight materials, such as aluminum, are preferred when weight reduction is a key factor, as they help improve fuel efficiency or ease of handling without sacrificing strength. On the other hand, if weight is not a concern, heavier materials might be used for their strength or other properties.
1.3 Corrosion Resistance Based on Environmental Exposure
Exposure to moisture, chemicals, or extreme weather conditions can cause materials to degrade over time. Therefore, the environment where the product will be used should dictate the choice of material. For example, stainless steel or galvanized steel offers superior corrosion resistance, making them ideal for outdoor or marine applications. Materials with poor corrosion resistance might need additional coatings or treatments, adding complexity and cost.
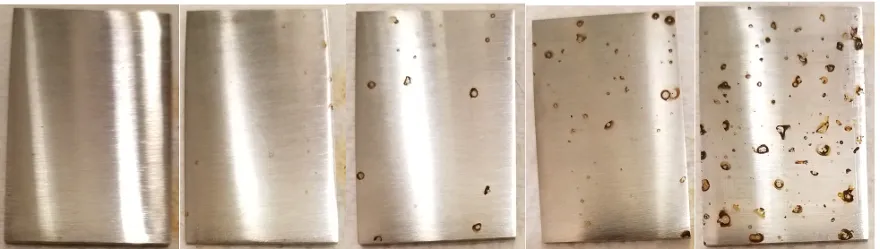
1.4 Manufacturing Process Compatibility (Bending, Welding, etc.)
Different sheet metal materials react differently to various manufacturing processes, including bending, welding, and punching. Materials like aluminum are easier to bend, while steel might require more force and specialized tools. Consider the processes that will be used in fabrication and how the material behaves under those conditions. For instance, some metals may be prone to cracking or warping during welding, which could require additional steps to mitigate these issues.
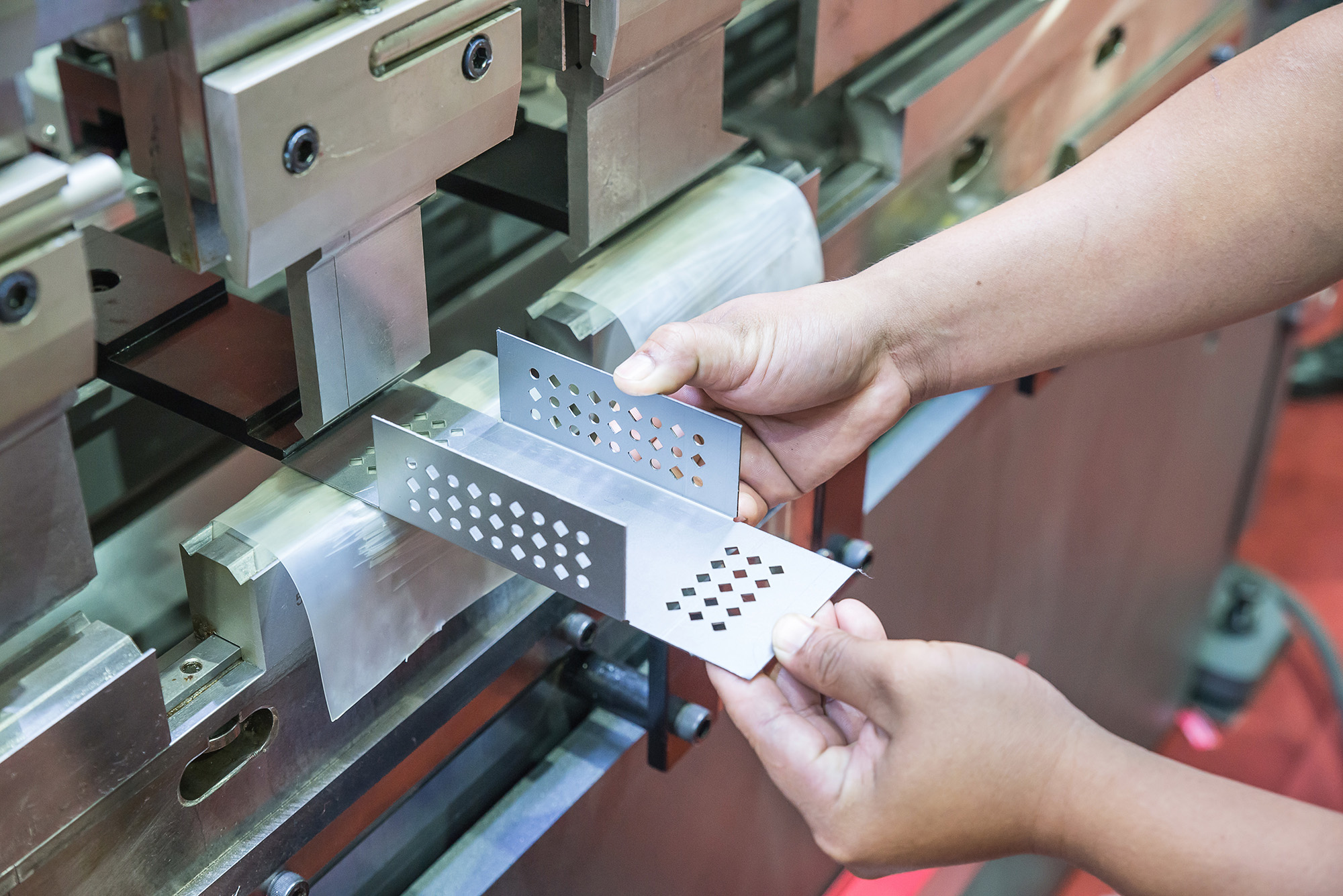
1.5 Cost and Availability Balance
While performance is important, cost is a significant factor when selecting materials. Some high-strength or specialized materials may be more expensive, and availability can vary based on location or market demand. Balancing the material’s performance with its cost and availability is key to ensuring that the final product meets budget constraints without sacrificing quality. In some cases, using a less expensive material might be acceptable if it can be treated or coated to meet required performance standards.
2. Cold Rolled Close Annealed Steel (CRCA)
Cold Rolled Close Annealed Steel (CRCA) is a type of steel that undergoes a cold rolling process followed by an annealing treatment, which enhances its properties and makes it ideal for various manufacturing applications. Here’s a closer look at the material:
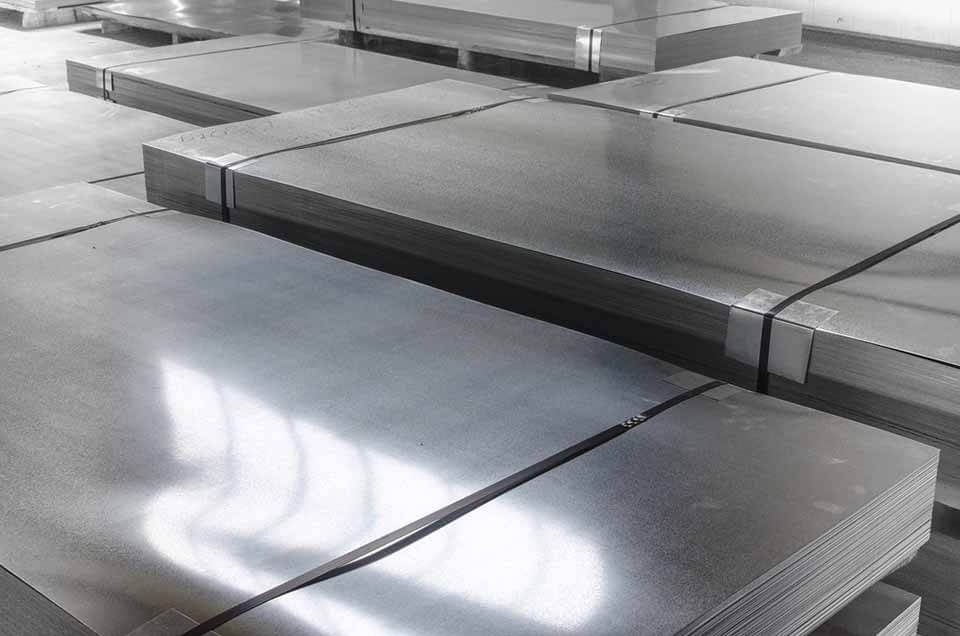
2.1 Material Characteristics and Performance
CRCA steel is known for its excellent surface finish, dimensional accuracy, and improved mechanical properties. The cold rolling process reduces the thickness of the steel and refines its structure, resulting in a smooth, glossy surface and enhanced strength. The annealing process that follows helps relieve stresses induced by the cold rolling, improving ductility and formability. However, CRCA steel does not have inherent corrosion resistance, making it less suitable for outdoor or harsh environments without additional treatment.
2.1.1 Pros: Surface Finish, Strength, Cost
- Surface Finish: CRCA steel is prized for its smooth, uniform surface that makes it ideal for applications where aesthetic appearance or precise dimensions are critical. The process leaves minimal imperfections, which is highly desirable for products with visible surfaces or those requiring secondary treatments like painting or coating.
- Strength: The cold rolling process imparts higher strength compared to hot-rolled steel, making it more durable for many structural applications. It offers good tensile and yield strength, making it capable of handling moderate loads without permanent deformation.
- Cost: CRCA steel is relatively inexpensive compared to other materials like stainless steel. Its lower cost, combined with good mechanical properties, makes it an economical choice for many industries, especially where corrosion resistance is not a primary concern.
2.1.2 Cons: Corrosion Issues, Needs Coating
- Corrosion Issues: One of the primary downsides of CRCA steel is its lack of natural resistance to corrosion. Without a protective coating, the steel can rust quickly when exposed to moisture, chemicals, or other corrosive elements. This makes it less suitable for outdoor use or environments where exposure to water or chemicals is frequent.
- Needs Coating: To enhance its corrosion resistance, CRCA steel typically requires an additional coating or treatment, such as galvanization (zinc coating) or painting. This increases the total cost and production time but is necessary to ensure the steel lasts in various applications.
2.2 Typical Applications
CRCA steel is widely used in a range of industries due to its cost-effectiveness and strong performance in many applications:
- Automotive industry: For making parts like body panels, frames, and structural components.
- Home appliances: Used in the manufacturing of refrigerator panels, washing machine components, and other household items.
- Furniture manufacturing: Often used in the production of metal furniture frames, shelves, and supports.
- General manufacturing: CRCA steel is used in many general manufacturing applications, especially where a smooth surface and high strength are needed, but corrosion resistance is managed through coatings.
In summary, CRCA steel is an excellent choice for cost-effective, high-strength applications, especially in controlled environments or where additional coatings can be applied to prevent corrosion.
3. Galvanized Iron (GI)
Galvanized Iron, commonly referred to as GI, is steel or iron that’s been treated with a zinc coating to enhance its resistance to rust and environmental damage. The zinc acts as a shield, helping the base metal withstand harsh or humid conditions. Thanks to this added protection, GI is a go-to option in many sectors that need affordable yet durable sheet metal. Here’s what makes it stand out:
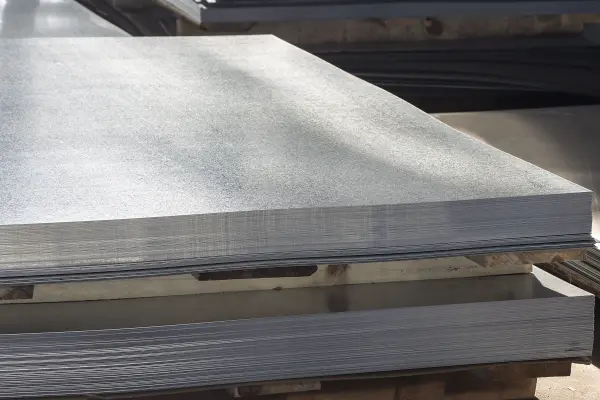
3.1 Protective Zinc Coating Benefits
The primary benefit of GI is the zinc coating, which acts as a protective barrier against corrosion. The zinc layer forms a sacrificial coating, meaning it corrodes first, protecting the underlying iron or steel from rust and deterioration. This makes GI highly resistant to environmental factors such as moisture, salt, and air, which are common causes of metal degradation.
3.1.1 Pros: Corrosion Resistance, Formability
- Corrosion Resistance: One of the standout features of galvanized iron is its excellent resistance to corrosion. The zinc coating ensures the material remains protected even in harsh conditions, such as high humidity or coastal environments where salt exposure is prevalent. This makes GI ideal for outdoor and exposed applications.
- Formability: GI maintains good formability despite the zinc coating. It can be easily cut, bent, and shaped, making it suitable for manufacturing various products, including panels, roofing materials, and structural components. The galvanization process does not significantly affect the material’s ability to be processed, which is a key advantage in manufacturing.
3.1.2 Cons: Zinc Layer Damage Risk
- Zinc Layer Damage: Although the zinc coating provides effective corrosion protection, it is not indestructible. The coating can be damaged during handling, cutting, or welding, which exposes the underlying iron or steel to corrosion. Care must be taken to avoid scratching or nicking the zinc layer during manufacturing processes, or it may compromise the material’s durability in the long run.
3.2 Use Cases and Environments
Galvanized iron is commonly used in applications where corrosion resistance is a priority, and the material will be exposed to the elements:
- Construction: GI is frequently used in roofing, siding, gutters, and downspouts, where its ability to resist the elements is crucial for long-term durability.
- Automotive: It is used for parts exposed to weathering, such as body panels, bumpers, and undercarriages, where protection from rust is essential.
- Agriculture: GI is used for making fences, storage tanks, and equipment exposed to moisture and outdoor conditions.
- Outdoor Furniture and Appliances: GI is often found in garden furniture, grills, and outdoor appliances, where corrosion resistance is required for prolonged outdoor use.
In conclusion, galvanized iron is an excellent choice for applications where corrosion resistance is needed, particularly in outdoor and exposed environments. While the zinc coating provides substantial protection, it’s important to handle GI materials carefully to maintain the integrity of the protective layer.
4. Aluzinc Steel
Aluzinc steel is a type of steel coated with a mixture of aluminum and zinc, offering enhanced durability and resistance compared to regular galvanized steel. The coating is typically made up of 55% aluminum, 43.4% zinc, and 1.6% silicon, providing a unique combination of properties. Let’s explore its features:
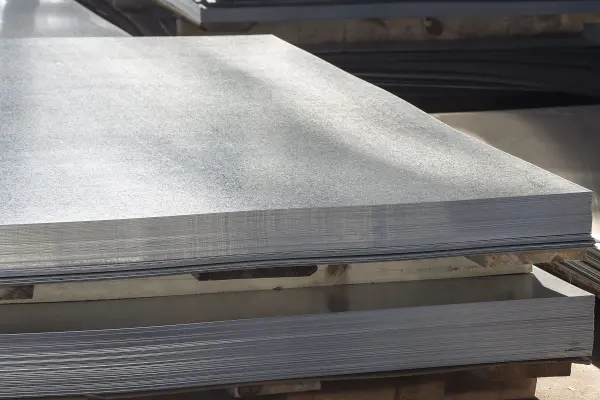
4.1 Material Composition and Coating Type
Aluzinc steel features a coating of aluminum-zinc alloy that covers the base steel. This coating provides superior protection against corrosion, particularly in harsh environments. The aluminum component of the coating contributes to the material’s high-temperature resistance and reflects heat, while the zinc component offers the traditional corrosion protection seen in galvanized steel. The addition of silicon helps in the formation of a robust and durable coating.
4.1.1 Pros: Corrosion and Heat Resistance
- Corrosion Resistance: One of the biggest advantages of aluzinc steel is its superior corrosion resistance. The aluminum-zinc alloy coating protects the underlying steel from rust and degradation much more effectively than galvanized steel, especially in environments where moisture and high temperatures are prevalent.
- Heat Resistance: Aluzinc steel also performs better than galvanized steel in high-temperature environments. The aluminum in the coating enhances heat resistance, making the material ideal for applications where exposure to heat or elevated temperatures is expected. This feature is especially beneficial in industries like construction, automotive, and roofing, where materials are subjected to both weather elements and heat.
4.1.2 Cons: Higher Cost Than GI
- Higher Cost: One of the main drawbacks of aluzinc steel is its higher cost compared to galvanized iron (GI). The manufacturing process, which involves a specialized aluminum-zinc coating, is more expensive than the traditional galvanization process. As a result, aluzinc steel may not always be the most cost-effective option for all applications, particularly for projects with tighter budgets or where the superior properties of aluzinc are not absolutely necessary.
4.2 Preferred Applications
Aluzinc steel is preferred in applications where both corrosion resistance and heat resistance are critical:
- Roofing and Siding: Due to its ability to withstand extreme weather conditions and high temperatures, aluzinc steel is commonly used for roofing and siding in areas with harsh climates, including coastal and industrial regions.
- Automotive Industry: It is also utilized in the automotive sector for parts that need to endure both weathering and high temperatures, such as engine components, exhaust systems, and underbody parts.
- Construction: Aluzinc is used in the construction of HVAC systems, building facades, and structural components where both durability and resistance to heat and corrosion are essential.
- Industrial Equipment: Aluzinc is employed in manufacturing equipment and machinery that are exposed to high-temperature environments, such as heat exchangers, pipes, and storage tanks.
5. Aluminum Alloys
Aluminum alloys are widely used in sheet metal applications due to their lightweight nature and excellent corrosion resistance. These alloys come in various grades, each offering specific advantages for different industries. Let’s delve into the key features of aluminum alloys for sheet metal work:
5.1 Grades Suitable for Sheet Metal Work
Aluminum alloys are classified into different series, with the most common grades for sheet metal applications being:
- 1000 Series: Composed of 99% or higher purity aluminum, these alloys are known for their excellent corrosion resistance and high formability. They are often used in applications requiring good conductivity, such as electrical and chemical equipment.
- 3000 Series: Primarily made of aluminum and manganese, these alloys offer moderate strength and good corrosion resistance. They are commonly used in roofing, siding, and cooking utensils.
- 5000 Series: This series contains aluminum and magnesium, offering excellent resistance to corrosion, especially in marine environments. It is ideal for applications in the transportation and marine industries.
- 6000 Series: Contains aluminum, magnesium, and silicon, making it ideal for structural applications. It offers good weldability, corrosion resistance, and moderate strength, making it popular in the automotive and aerospace industries.
- 7000 Series: Known for high strength and used primarily in aerospace and military applications. This series, including the popular 7075 grade, offers superior strength but is less corrosion-resistant than other alloys.
5.1.1 Pros: Lightweight, Corrosion-Resistant
- Lightweight: Aluminum alloys are significantly lighter than steel, which makes them ideal for applications where weight reduction is important, such as in the automotive, aerospace, and transportation industries. Reducing weight can lead to improved fuel efficiency and easier handling.
- Corrosion Resistance: Aluminum naturally forms a protective oxide layer on its surface, providing excellent resistance to corrosion, especially in humid or salty environments. This makes aluminum alloys ideal for outdoor applications, such as roofing, marine equipment, and chemical processing.
5.1.2 Cons: More Expensive, Harder to Weld
- More Expensive: While aluminum alloys offer superior properties, they tend to be more expensive than other sheet metal materials such as mild steel or galvanized iron. The cost is driven by the extraction and processing of aluminum, which requires more energy compared to other metals.
- Harder to Weld: Aluminum alloys can be more difficult to weld compared to other metals like steel. Aluminum’s low melting point and high thermal conductivity require specialized welding techniques and equipment, making the process more time-consuming and costly. Additionally, the alloys are prone to cracking during welding, which may require more advanced skill and preparation.
5.2 Industries and Parts Using Aluminum
Aluminum alloys are used across a wide range of industries and applications due to their unique properties:
- Aerospace: The aerospace industry relies heavily on aluminum alloys for making structural components, such as aircraft fuselages, wings, and engine parts, due to their lightweight and strength-to-weight ratio.
- Automotive: In the automotive industry, aluminum is used for engine components, body panels, wheels, and heat exchangers. The lightweight nature of aluminum helps reduce vehicle weight, leading to improved fuel efficiency and handling.
- Construction: Aluminum is used in construction for window frames, doors, roofing, and cladding due to its corrosion resistance and aesthetic appeal.
- Marine: Aluminum alloys are ideal for marine applications such as boat hulls, pontoons, and offshore platforms because they resist corrosion in salty water environments.
- Electronics: The electronics industry uses aluminum for heat sinks and enclosures, taking advantage of its lightweight and thermal conductivity properties.
- Packaging: Aluminum is widely used in the packaging industry for making cans, foils, and other containers, offering excellent protection against moisture and contamination.
In summary, aluminum alloys are favored for sheet metal applications due to their lightweight, corrosion-resistant properties. While they come with higher costs and challenges in welding, their benefits in industries such as aerospace, automotive, construction, and packaging make them indispensable for various applications where performance, durability, and weight savings are crucial.
6. Stainless Steel
Stainless steel is a highly versatile material, known for its strength, durability, and resistance to corrosion. It is commonly used in industries requiring high-performance materials that can withstand harsh environments. Let’s explore the key aspects of stainless steel in sheet metal applications.
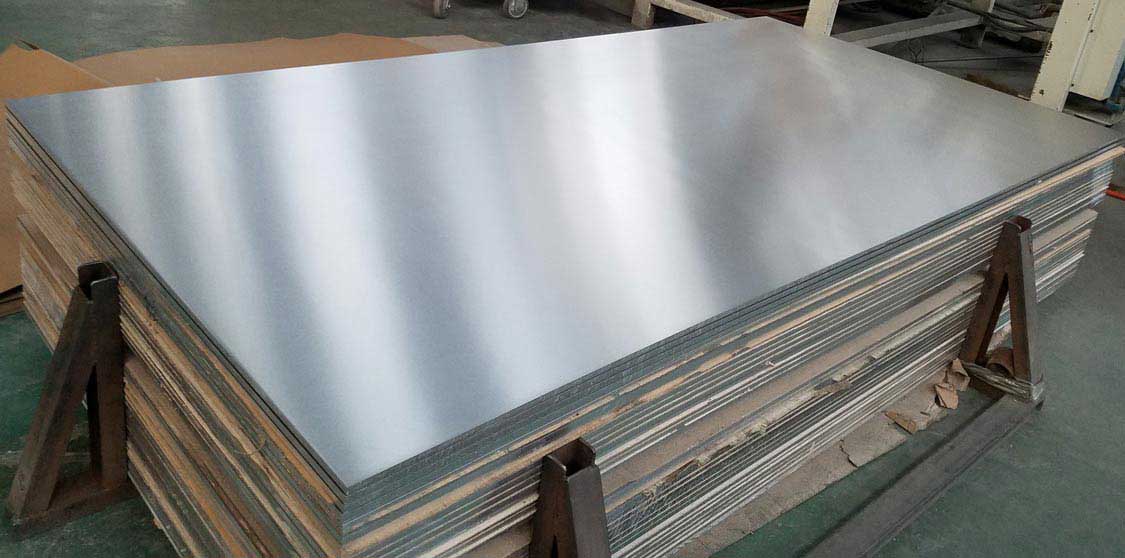
6.1 Grades Like SS304 and SS316 for Different Environments
Stainless steel comes in various grades, with SS304 and SS316 being two of the most widely used in sheet metal applications:
- SS304: This is the most common grade of stainless steel, containing approximately 18% chromium and 8% nickel. It offers excellent resistance to corrosion in a wide range of environments, making it ideal for applications in food processing, architecture, and general industrial use. SS304 is particularly effective in indoor applications or environments with mild exposure to corrosive elements.
- SS316: Known for its superior corrosion resistance, SS316 contains molybdenum, which enhances its resistance to chloride corrosion, making it ideal for marine environments and applications exposed to chemicals or saltwater. It’s commonly used in the pharmaceutical, chemical, and marine industries.
6.1.1 Pros: Strength, Corrosion Resistance, Aesthetics
- Strength: Stainless steel is renowned for its high tensile strength, making it suitable for structural applications. Its strength allows it to withstand heavy loads and stress, making it ideal for critical components in construction, automotive, and aerospace industries.
- Corrosion Resistance: One of the most significant advantages of stainless steel is its exceptional resistance to corrosion. Its chromium content forms a passive oxide layer that protects the material from rust and degradation in harsh environments. This makes stainless steel a go-to choice for industries exposed to moisture, chemicals, and high temperatures.
- Aesthetics: Stainless steel also has a sleek, shiny appearance that is highly valued in architectural, design, and consumer product applications. Its visual appeal, along with its strength and resistance, makes it popular for items like kitchen appliances, elevators, and medical equipment.
6.1.2 Cons: Higher Cost and Fabrication Difficulty
- Higher Cost: Stainless steel tends to be more expensive than other sheet metals such as mild steel or aluminum. The higher material costs, combined with the expense of manufacturing processes, contribute to the overall cost. The added expense can be a factor to consider in projects with tight budgets.
- Fabrication Difficulty: While stainless steel is an excellent material in many ways, it can be more challenging to fabricate compared to other metals. It requires special equipment and techniques for cutting, welding, and forming due to its hardness and tendency to work-harden. Additional challenges in bending and forming require skilled labor and increased manufacturing time, contributing to higher costs.
6.2 Where Stainless Steel Is Most Effective
Stainless steel excels in environments that demand superior strength and resistance to corrosion. Some of the most effective uses include:
- Food and Beverage Industry: SS304 and SS316 are commonly used in the food processing industry due to their resistance to corrosion and ability to meet stringent hygiene standards. Stainless steel is used for equipment like storage tanks, pipes, and kitchen appliances.
- Medical and Pharmaceutical: Stainless steel’s biocompatibility, cleanliness, and corrosion resistance make it essential for medical devices, surgical instruments, and pharmaceutical equipment.
- Construction and Architecture: Stainless steel is popular in building facades, staircases, railings, and other architectural elements because of its strength and aesthetic appeal. It’s also used in roofing and cladding materials for buildings exposed to the elements.
- Marine Industry: SS316 is particularly effective in the marine industry, where it is used for boat hulls, offshore structures, and other equipment exposed to saltwater. Its resistance to corrosion in harsh, salty environments is a critical factor for longevity.
- Automotive and Aerospace: Due to its strength and resistance to high temperatures, stainless steel is used in exhaust systems, engine components, and various structural elements in both automotive and aerospace applications.
In conclusion, stainless steel is an invaluable material in sheet metal design, offering strength, exceptional corrosion resistance, and aesthetic benefits. While it comes with higher costs and fabrication complexities, its superior properties make it ideal for applications in food processing, medical, marine, architecture, and more.
7. Comparison Table: Material Properties at a Glance
Since KingStar has already posted a detailed datasheet comparing various materials (click here), we can focus on how to utilize that resource for making informed material choices. Instead of repeating the details, this section will emphasize how to efficiently use the material properties datasheets available on the website to guide your selection process.
7.1 Key Properties to Compare:
When selecting a material for sheet metal applications, refer to the datasheet for in-depth information on the following properties:
- Strength: Understand the tensile and yield strengths of different materials, which determine how well they can withstand mechanical loads and stress without deformation.
- Corrosion Resistance: Evaluate how well a material resists rust and deterioration when exposed to various environmental factors like moisture, chemicals, and temperature extremes.
- Weight: Consider the material’s density and how it affects the overall weight of the product. Lighter materials may be ideal for applications where weight reduction is crucial, while heavier materials might be necessary for strength and stability.
- Cost: Material costs vary, so assess the pricing information available on the datasheet to balance your budget against the required material properties.
- Weldability: Check the ease with which a material can be welded. Some materials, such as certain aluminum alloys, may require specialized welding techniques, whereas others like mild steel are easier to weld.
7.2 How to Use the Datasheets:
- Access the Material Properties: Visit the KingStar website’s datasheets section, where you’ll find detailed comparisons for each material, including cold rolled steel, galvanized iron, stainless steel, aluminum, and others. These datasheets provide comprehensive data on mechanical properties, chemical composition, and recommended applications.
- Make Informed Decisions: Use the datasheets to make side-by-side comparisons of material properties. This will help you quickly identify which material meets your specific design, performance, and budgetary requirements.
- Visual Aid: The datasheets often include charts, graphs, and tables that clearly highlight the differences between materials, making it easier to visualize which option is best suited for your needs.
8. Material Selection Process in Sheet Metal Design
Selecting the right material for sheet metal applications is a critical process that requires careful consideration of various factors to ensure both functionality and cost-effectiveness. The following steps outline an effective material selection process:
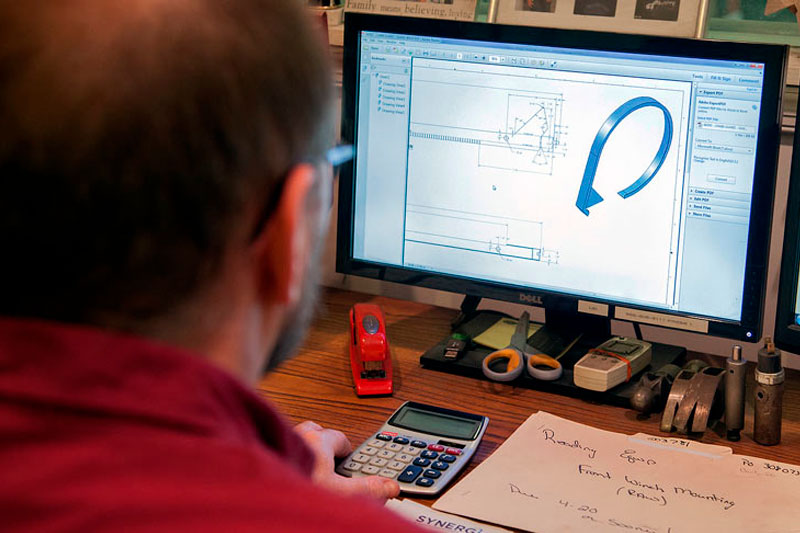
8.1 Define Functional and Environmental Requirements
Before choosing a material, clearly define the functional requirements of the part or product. Consider the following:
- Mechanical Load: Will the material need to withstand high stress or heavy loads?
- Durability: What is the expected service life of the part?
- Corrosion Resistance: Will the part be exposed to corrosive elements such as moisture, chemicals, or extreme temperatures?
- Aesthetic Requirements: Does the appearance of the material matter (e.g., polished finishes or color)?
- Formability and Fabrication: Can the material be easily processed through bending, welding, or punching?
In addition to functional needs, consider the environmental conditions the material will be exposed to, such as humidity, temperature, and exposure to chemicals or outdoor elements.
8.2 Shortlist and Evaluate Potential Materials
Once the requirements are clear, research and shortlist materials that meet the essential criteria. For example:
- Corrosion Resistance: If corrosion is a concern, materials like stainless steel, aluminum, or galvanized steel may be preferable.
- Strength and Durability: For applications with high mechanical stress, you may need high-strength alloys such as stainless steel or hardened steel.
- Cost Efficiency: If budget constraints are critical, mild steel or cold-rolled steel may provide a more cost-effective option.
Evaluate each shortlisted material based on its mechanical properties (strength, hardness), environmental resistance (corrosion, temperature tolerance), and formability. Use datasheets and material property comparison tools to compare them side-by-side.
8.3 Prototype Testing and Validation
After narrowing down the material choices, the next step is to prototype the design using the selected materials. Prototyping allows you to test:
- Formability: Does the material perform well during bending, stamping, or cutting?
- Strength: Does the material support the intended load without deformation or failure?
- Corrosion Resistance: Does it hold up against environmental factors as expected?
- Weldability: Can the material be welded effectively, if necessary?
Prototyping helps identify any issues with the material selection early in the design phase, reducing the risk of costly rework later on.
8.4 Final Selection Based on Performance/Cost Trade-offs
After testing the prototype, evaluate the materials based on their performance and cost trade-offs. The final material selection should balance:
- Performance: The material must meet the functional and environmental requirements of the project.
- Cost: The material should be within budget, taking into account the cost of procurement, manufacturing, and potential lifecycle costs.
Consider factors such as ease of fabrication, availability, and long-term durability. At this stage, you may also consider potential upgrades or substitutions if the initial material doesn’t perform as expected.
By following this structured selection process, you can ensure that the material you choose is optimized for your specific design needs, while also remaining cost-effective and manufacturable.
9. Tips to Optimize Material Usage
Optimizing material usage not only helps reduce costs but also improves overall sustainability in manufacturing processes. Here are several strategies to ensure the most efficient use of materials in sheet metal design:
9.1 Use Coated Materials Where Full Stainless Steel is Not Needed
If corrosion resistance is a primary concern, but the application does not require the full strength and cost of stainless steel, consider using coated materials. For instance:
- Galvanized Steel: Steel coated with zinc offers good corrosion resistance at a lower cost compared to stainless steel.
- Aluzinc Steel: This offers excellent protection against corrosion and heat while being more cost-effective than full stainless steel.
By selecting coated materials, you can maintain adequate durability and corrosion resistance without the expense of stainless steel.
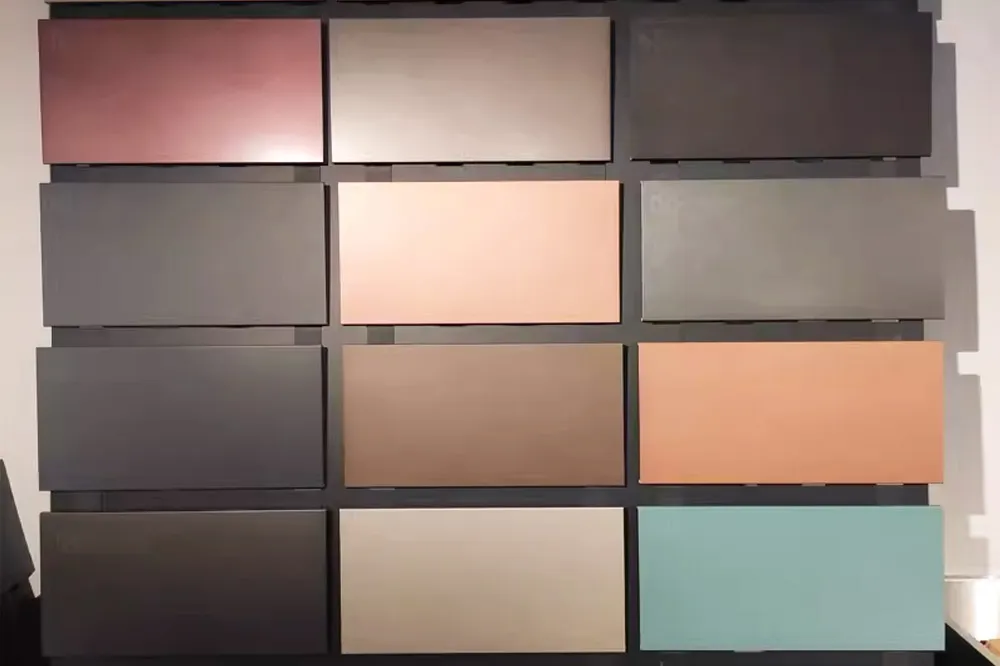
9.2 Consider Hybrid Materials or Layered Structures
In some applications, using hybrid materials or layered structures can provide a balance of properties, such as strength, weight, and corrosion resistance, without the need for a single expensive material. For example:
- Composite Materials: Layering different materials such as aluminum with a protective coating can offer benefits like weight reduction and durability without the need for heavier metals.
- Multi-layer Structures: Materials like steel with an aluminum or zinc layer offer the benefits of each material’s properties (e.g., aluminum’s corrosion resistance and steel’s strength).
Using hybrid materials or layered structures can result in more cost-effective, high-performance designs.
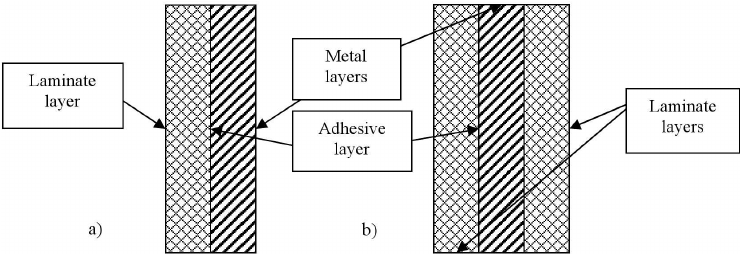
9.3 Minimize Thickness Without Compromising Strength
A key goal in sheet metal design is to minimize the material thickness while still ensuring the part can handle the required loads and stresses. Thin materials reduce weight and cost, but they must be strong enough for the intended application. Consider:
- Designing for strength: Use reinforced areas (such as ribs) where additional strength is needed, allowing for thinner overall material use.
- Optimization tools: Use advanced design software and simulations to ensure that parts are as thin as possible while still meeting performance standards.
By carefully managing material thickness, you can reduce waste and lower manufacturing costs without sacrificing quality.
9.4 Collaborate with Suppliers for Availability Insights
Suppliers often have valuable insights into material availability, cost fluctuations, and manufacturing constraints. Collaborating with them early in the design process can help:
- Identify alternative materials: Suppliers may suggest alternative materials that offer similar properties at a lower cost or with better availability.
- Understand material lead times: Material availability can affect production schedules. Suppliers can provide accurate lead times and help you avoid delays.
- Optimize supply chains: Suppliers may offer discounts for bulk purchases or provide advice on sourcing materials more efficiently.
Conclusion
Selecting the right sheet metal material is a crucial decision that impacts not only the functionality and durability of the final product but also production costs and efficiency. By carefully considering factors such as mechanical loads, environmental exposure, and manufacturing compatibility, designers can optimize performance while minimizing costs.
Early-stage consideration of material properties can prevent costly revisions and production delays, ensuring that the selected material aligns with both functional requirements and budget constraints. As material options continue to evolve, staying informed about the latest innovations and processes is essential for achieving the best results.
At KingStar, we leverage our extensive experience to guide clients in choosing the most suitable materials for their product needs. Whether it’s advising on the best material for durability, cost-effectiveness, or ease of fabrication, our expertise ensures that your designs are both high-quality and optimized for production. We’re committed to delivering tailored solutions that help you succeed in today’s competitive market.