As a global leader in wholesale custom storage bin manufacturing, KingStar Mold receives daily inquiries about production timelines and costs. This article highlights the key cost factors involved in plastic injection molding and mold building, offering an estimated breakdown of expenses for manufacturing custom plastic storage boxes.
1. Material Costs
- Raw Material Type:
- Virgin plastics (PP, HDPE, PET) offer better durability but are more expensive, making up 30%-50% of total costs.
- Recycled plastics reduce costs but may compromise quality.
- Special additives (anti-static, UV-resistant) increase material costs.
- Material Usage:
- Larger storage bins require more raw material, directly increasing costs.
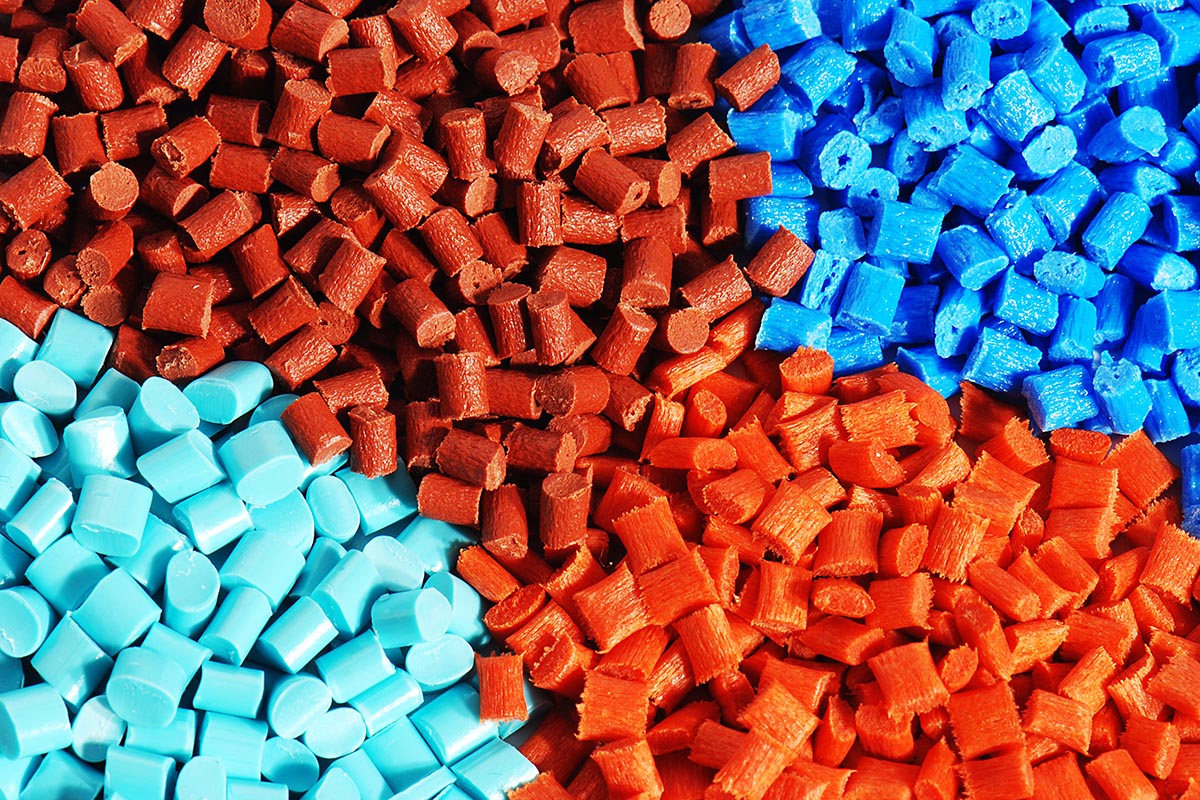
2. Production Scale
- Mold Costs:
- Injection mold development: Ranges from $5,000 to $100,000+, depending on complexity.
- Higher production volumes reduce per-unit mold cost (e.g., for 1 million units/year, mold costs become negligible).
- Unit Cost:
- Small batch production: $5–50 per unit (mold costs significantly impact price).
- Mass production: As low as $1–10 per unit due to economies of scale.
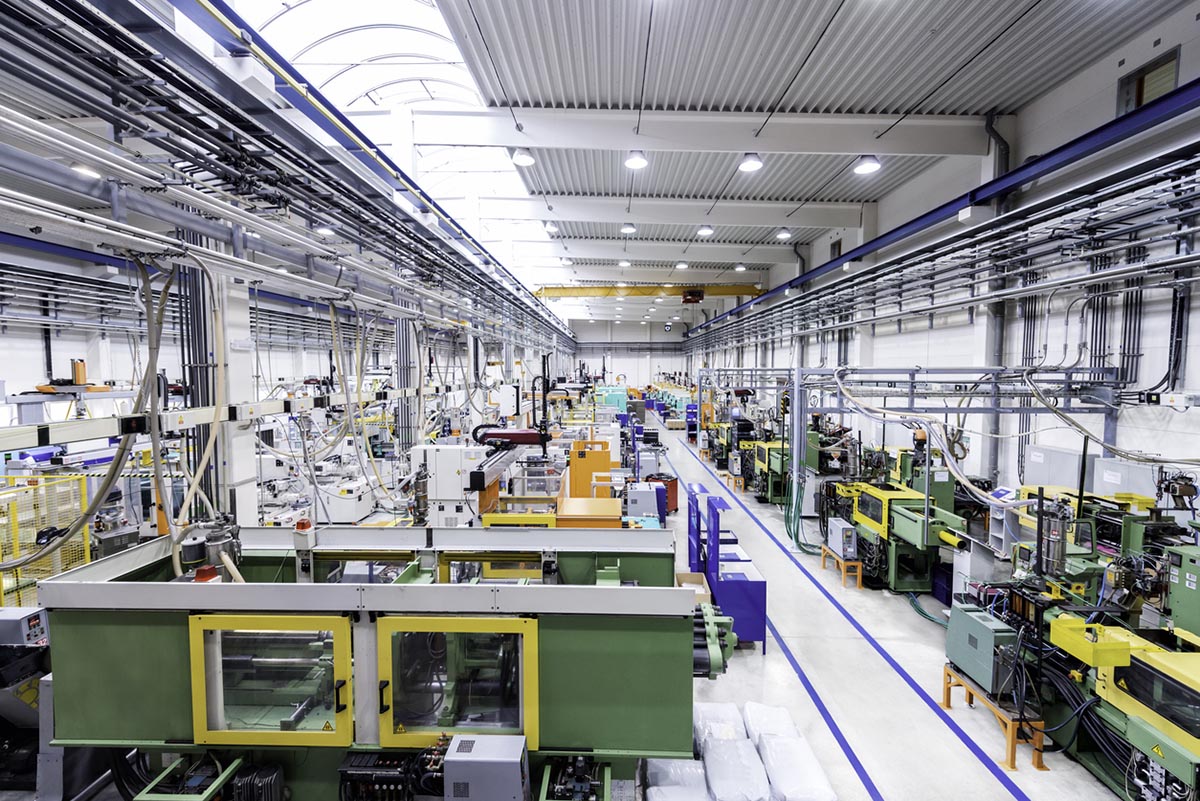
3. Customization Requirements
- Design Customization:
- OEM/ODM services (custom shapes, brand logo printing) increase costs by 10%-30%.
- Additional Features:
- Foldable structure, wheels, sealing strips, or other accessories add extra costs.
- Custom Packaging:
- Branded labels or customized packaging boxes further raise costs.
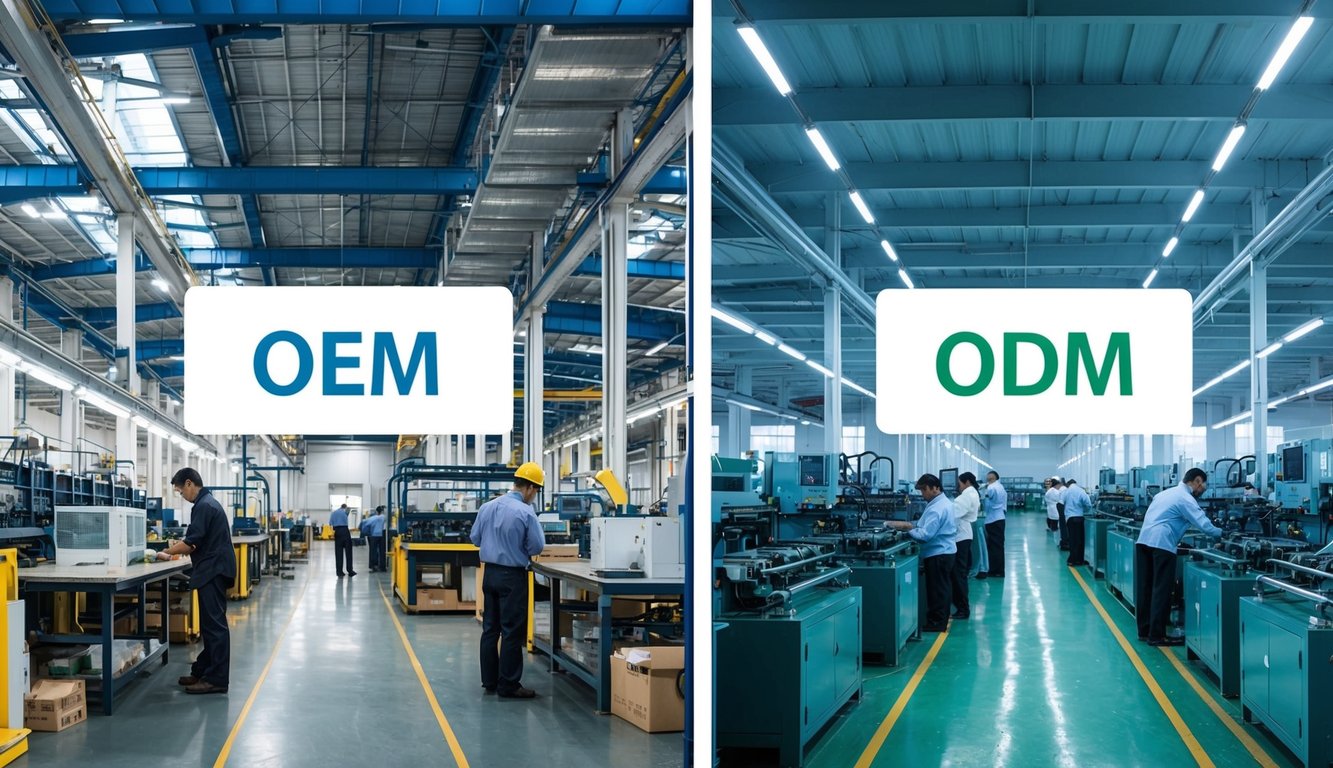
4. Production Location & Manufacturing Process
- Regional Cost Differences:
- China-based factories have lower labor and operational costs, reducing unit prices by 30%-50% compared to Western manufacturers.
- Shipping & logistics costs must be considered for exports.
- Working with large manufacturers like KingStar Mold or Silver Basis ensures worldwide door-to-door delivery services.
- Manufacturing Techniques:
- Injection molding is the most efficient and cost-effective method for standardized production.
- Blow molding & thermoforming costs vary depending on equipment and production requirements.
- High automation lowers long-term production costs.
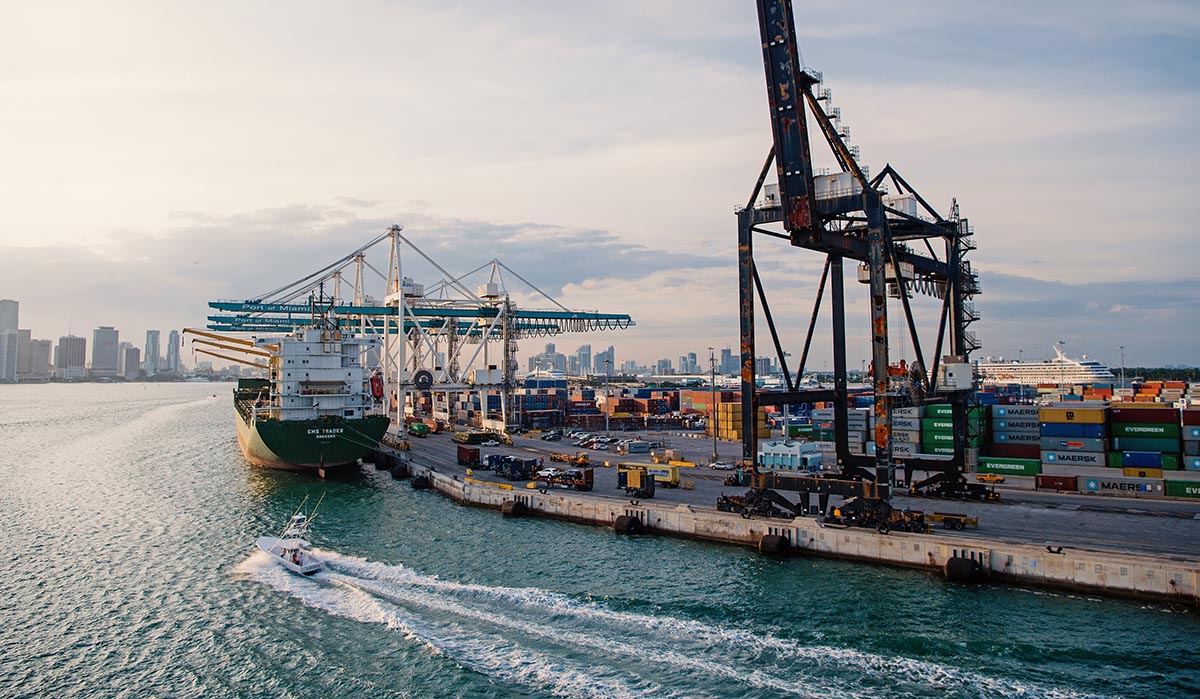
5. Additional Costs
- Shipping & Warehousing:
- International freight & storage costs depend on destination and volume.
- Quality Control:
- Strict testing (drop tests, weight load tests) increases labor and time costs.
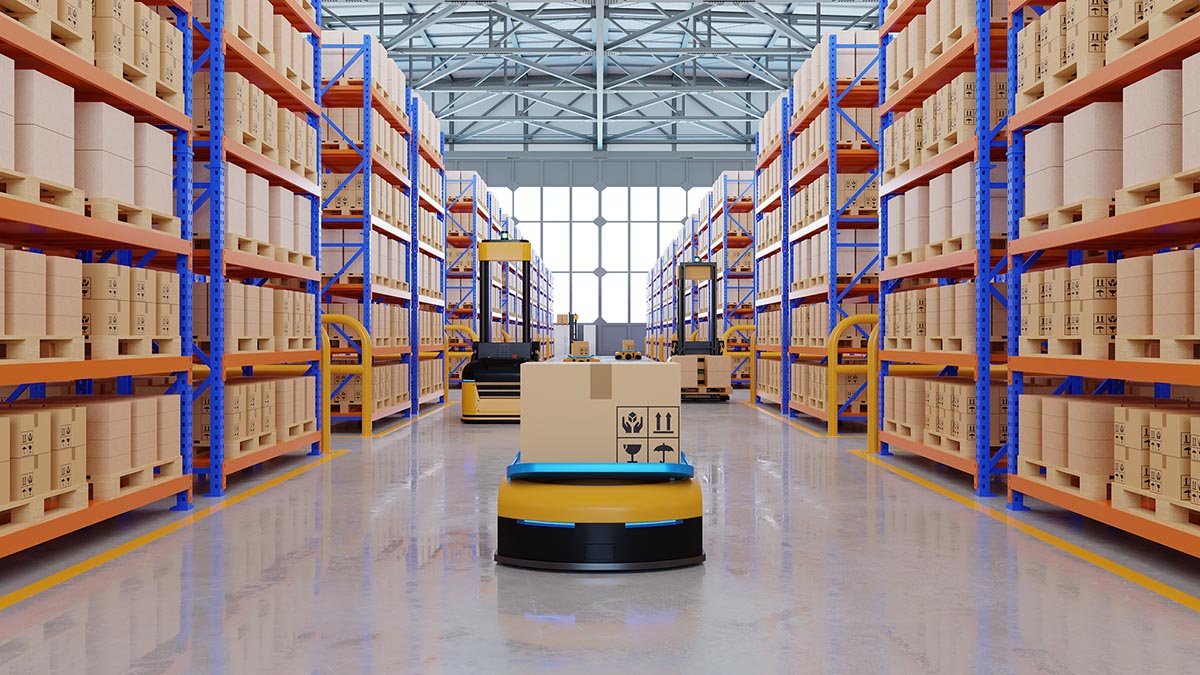
Comprehensive Cost Breakdown for Custom Plastic Storage Bins
The cost of manufacturing custom plastic storage bins varies based on production volume, material choices, mold investment, labor, and additional expenses. Below is a detailed cost table outlining key cost components and influencing factors.
Unit Cost Breakdown by Production Scale
Production Scale | Order Volume | Material Cost (USD/unit) | Mold Amortization (USD/unit) | Labor + Equipment (USD/unit) | Other Costs (USD/unit) | Total Cost Range (USD/unit) | Key Influencing Factors |
---|---|---|---|---|---|---|---|
Small Batch Production | 1,000–5,000 units | $0.70–$2.10 | $1.40–$4.20 | $0.42–$1.12 | $0.28–$0.98 | $2.80–$8.40 | - High mold cost per unit (50%+ of total cost) - Frequent manual adjustments for customization |
Medium Batch Production | 5,000–50,000 units | $0.56–$1.68 | $0.28–$1.12 | $0.28–$0.70 | $0.14–$0.42 | $1.26–$3.92 | - Partial mold cost amortization - Improved production efficiency with standardization |
Mass Production | 50,000+ units | $0.42–$1.12 | $0.07–$0.28 | $0.14–$0.42 | $0.07–$0.28 | $0.70–$2.10 | - Mold cost becomes negligible (million-unit annual output) - Fully automated production reduces costs |
Detailed Cost Component Breakdown
1. Material Costs
- Virgin Plastics (PP/HDPE): $1.12–$1.68 per kg, with each storage bin requiring 0.3–1 kg.
- Recycled Plastics: 20%-40% cost reduction, but may affect aesthetics and strength.
- Special Additives: $0.14–$0.42 per unit for anti-static, UV resistance, or aging-resistant materials.
2. Mold Amortization (Reduced If Using Existing Molds at KingStar Mold)
- Simple molds: $700–$2,800
- Complex molds (multi-cavity, high precision): $7,000–$14,000
- Cost per unit formula: Mold cost ÷ Order volume
- Example: A $14,000 mold used for 10,000 units = $1.40/unit.
3. Labor & Equipment Costs
- Labor: $0.07–$0.28 per unit in China (lower in highly automated facilities).
- Equipment Depreciation & Energy Consumption: $0.07–$0.42 per unit for injection molding machines.
4. Additional Costs
- Quality Control: $0.07–$0.14 per unit for sampling and testing.
- Packaging: $0.14–$0.42 per unit for carton boxes or plastic wrapping.
Case Comparison
Case 1 (Small Batch):
- Order Quantity: 3,000 units
- Specification: 30L with custom logo
- Total Cost per Unit: Approximately $3.45
- Material: $1.11
- Mold Allocation: $2.49
- Labor: $0.55
- Other: $0.69
Case 2 (Large Batch):
- Order Quantity: 100,000 units
- Specification: Standard 50L without accessories
- Total Cost per Unit: Approximately $0.97
- Material: $0.69
- Mold Allocation: $0.07
- Labor: $0.14
- Other: $0.07
Cost Reduction Suggestions
- Simplify Design: Reduce wall thickness and avoid complex structures like clips and moving parts.
- Bulk Purchasing: Secure lower raw material prices through bulk orders (e.g., PP granules can be 10%-20% cheaper when bought in large quantities).
- Choose Chinese Factories: Compare suppliers in Jiangsu and Zhejiang, where costs are 30%-50% lower than in the US and Europe.
- Mold Optimization: Use shared molds or standard sizes (e.g., a unified box body with interchangeable lids).
For a more detailed cost analysis based on specific specifications like capacity and wall thickness, feel free to provide exact parameters.
Conclusion & Suggestions
Contact Manufacturers for Quotes: Provide specific requirements (dimensions, materials, quantity) to get an accurate quote, such as from KingStar Mold, Silver Basis, etc.
Optimize Design: Simplify structures and reduce material usage (e.g., wall thickness) to significantly lower costs.
Choose Location: The Chinese supply chain offers better cost-effectiveness, but delivery time should be considered.
For a more accurate quote, please leave a message online or email us at sales@kingstarmold.com with your storage bin specifications (e.g., capacity, thickness) and expected order volume. We will respond within 24 hours.