As a leading custom plastic injection molding company, KingStar Mold receives multiple inquiries daily from various industries regarding mold building and injection molding projects. Some projects have incomplete designs, while others lack finalized production quantities. For such cases, providing an exact mold development cost is challenging, and only a rough estimate can be given.
To help design engineers, procurement specialists, and project managers get a general idea of individual mold costs, KingStar Mold has prepared this article along with a detailed cost reference table.
Core Components of Plastic Injection Mold Costs
1. Mold Design Costs
- Complexity & Work Hours: The complexity of the mold structure (e.g., multi-cavity, slider mechanisms, core-pulling design) directly affects design time. For instance, medical device molds require precision engineering, with design fees ranging from $700–$2,800, while simpler molds may only cost $140–$700.
- Software & Simulation: 3D modeling (UG, SolidWorks) and mold flow analysis (Moldflow) add extra costs, typically 10%–20% of the total design fee. (If you choose KingStar Mold as your plastic injection molding supplier, we waive the mold design fee.)
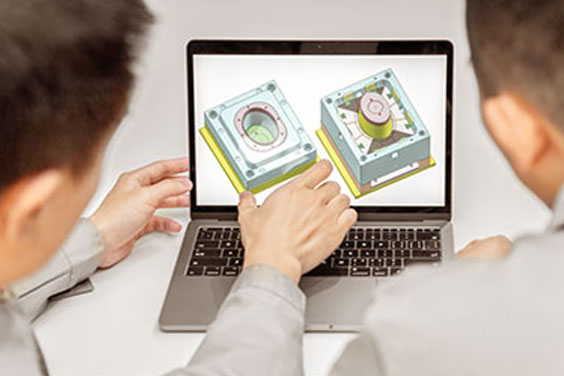
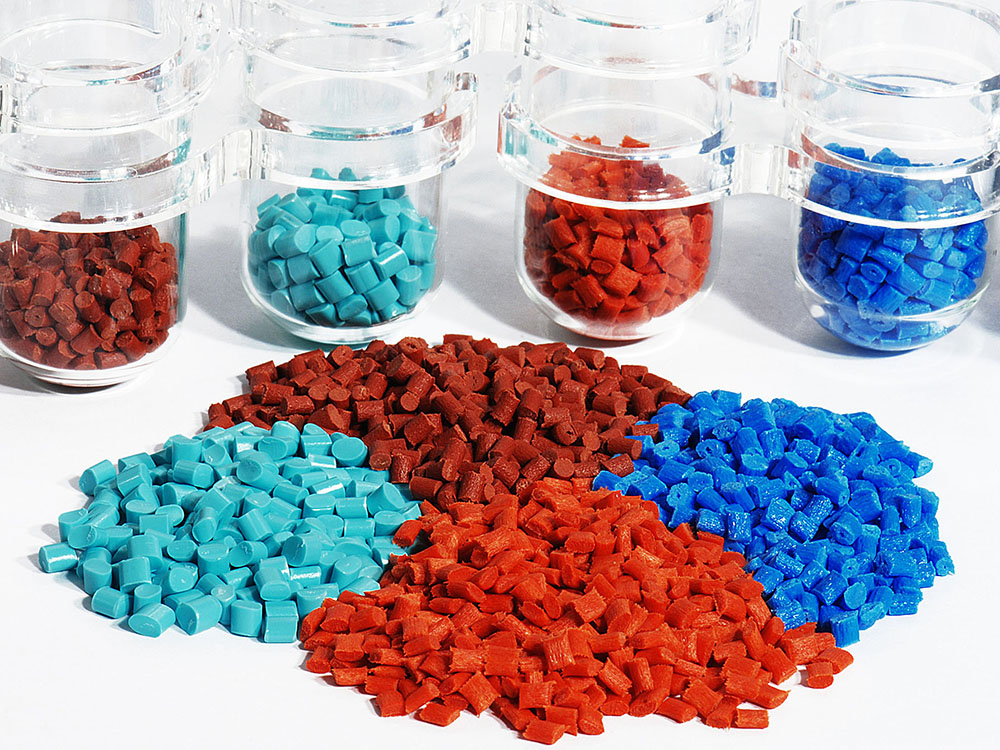
2. Material Costs
- Mold Steel Selection:
- Standard Steel (P20, 718): $11–$21/kg, suitable for general industrial parts, with a lifespan of 50,000 cycles.
- High-Hardness Steel (H13, S136): $28–$56/kg, offering high-temperature and corrosion resistance, ideal for medical and automotive molds, with a lifespan of 500,000 cycles.
- Aluminum (7075): More affordable at $7–$14/kg but with a limited lifespan of 3,000–5,000 cycles, best for low-volume prototyping.
- Plastic Compatibility: High-temperature plastics like PPSU and PEEK require heat-resistant mold steel, increasing material costs by 20%–30%.
3. Manufacturing Process Costs
- CNC Machining: Precision machining costs $42–$113/hour. Complex cavities requiring multi-axis machining can double the cost.
- EDM (Electrical Discharge Machining): Used for deep holes or intricate textures, costing $14–$42/hour.
- Surface Treatments:
- Mirror polishing for improved aesthetics: $70–$280
- Nitriding for wear resistance: $140–$700
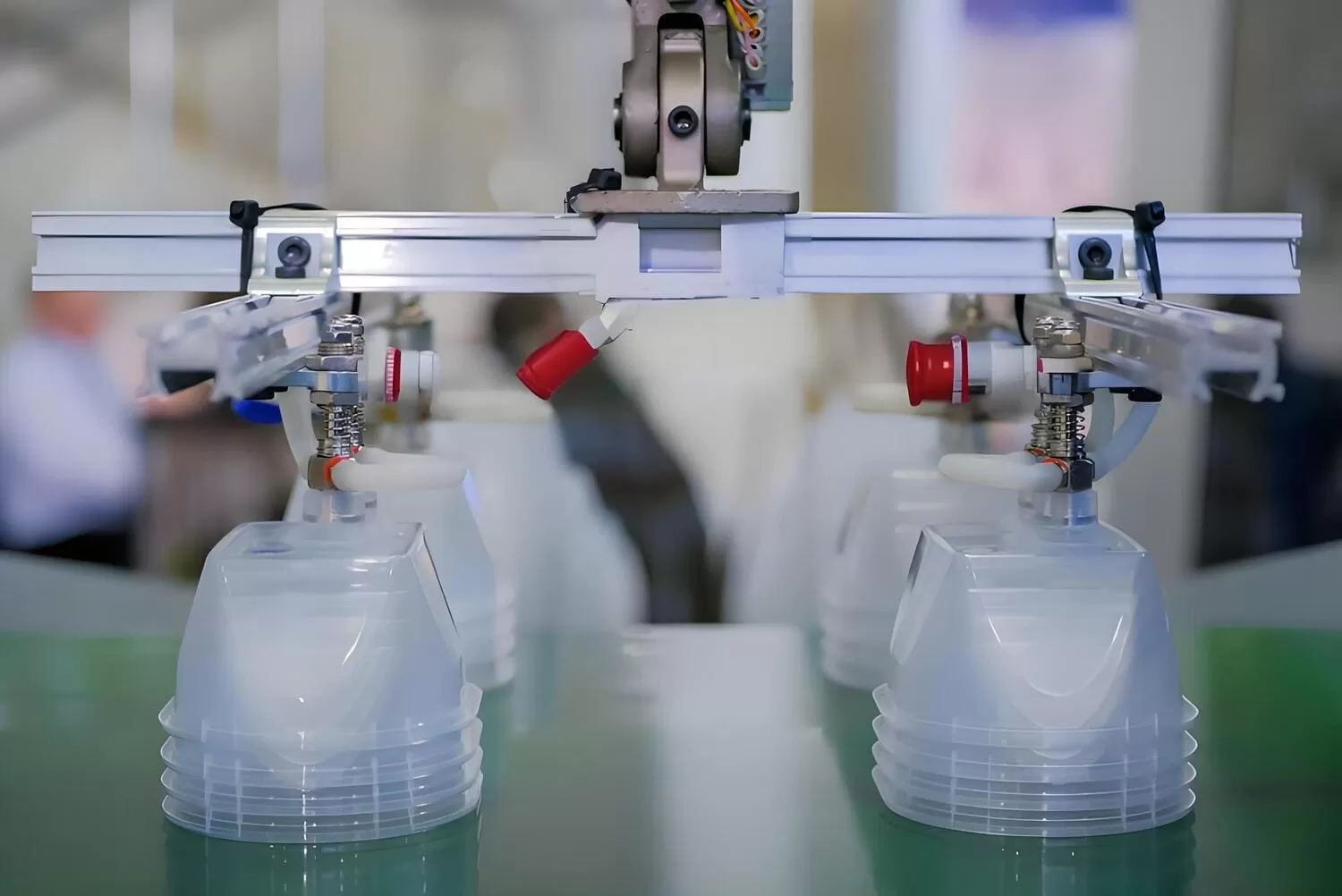
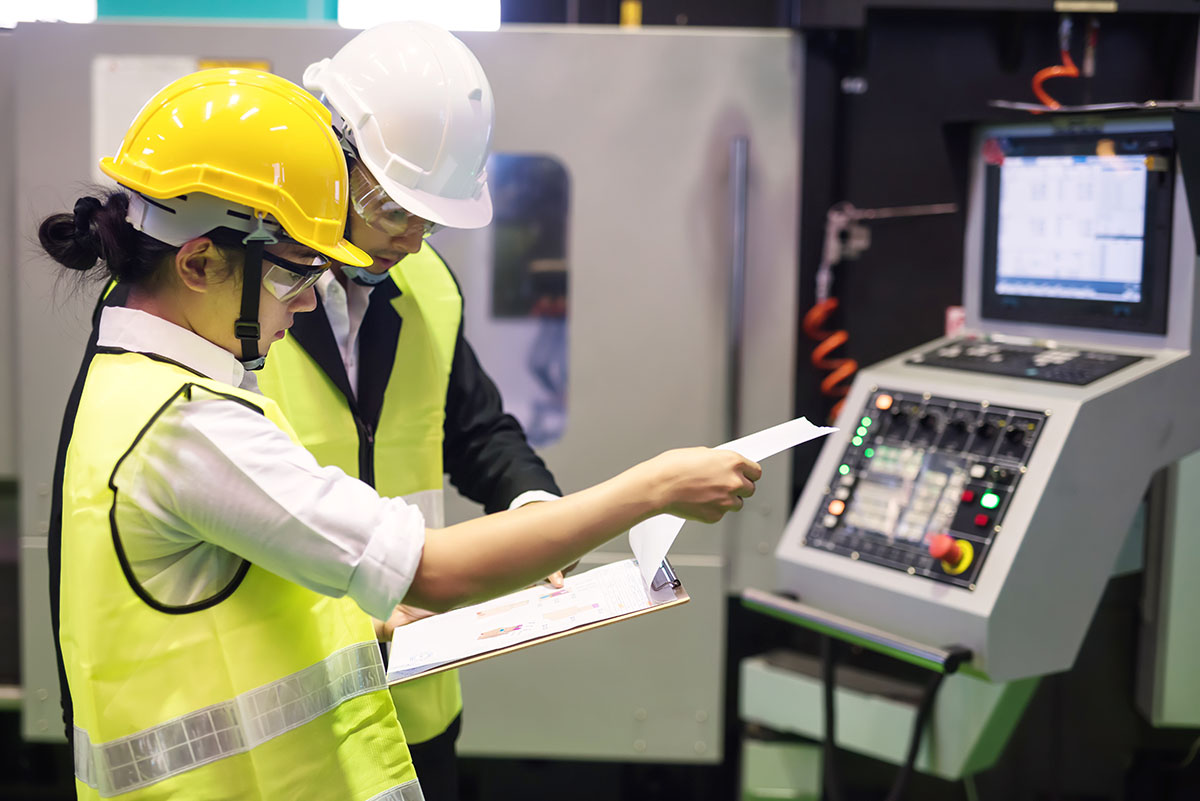
4. Industry Certification & Testing
- Medical-Grade Molds: Must comply with ISO 13485 and FDA standards, requiring material validation and documentation, adding $1,400–$4,200 in costs.
- Automotive Molds: Undergo 100,000 open-close cycle tests, with strict durability requirements increasing costs by 15%–25%.
Mold Price Range and Application Scenarios
Mold Type | Material Selection | Price Range (USD) | Application Scenarios | Lifespan (Cycles) |
Basic Aluminum Mold | 7075 Aluminum Alloy | $700–$2,800 | Low-volume prototyping, rapid validation | 3,000–5,000 |
Standard Steel Mold | P20 Steel, 718 Steel | $2,800–$11,000 | Household appliances, consumer electronics | 50,000–100,000 |
Precision Steel Mold | H13, S136 Steel | $11,000–$70,000 | Medical devices, high-precision automotive parts | 500,000+ |
Multi-Cavity Mold | High-Hardness Steel + Hot Runner System | $14,000–$140,000 | High-volume production (e.g., bottle caps, connectors) | 1,000,000+ |
Comprehensive Considerations for Material Selection
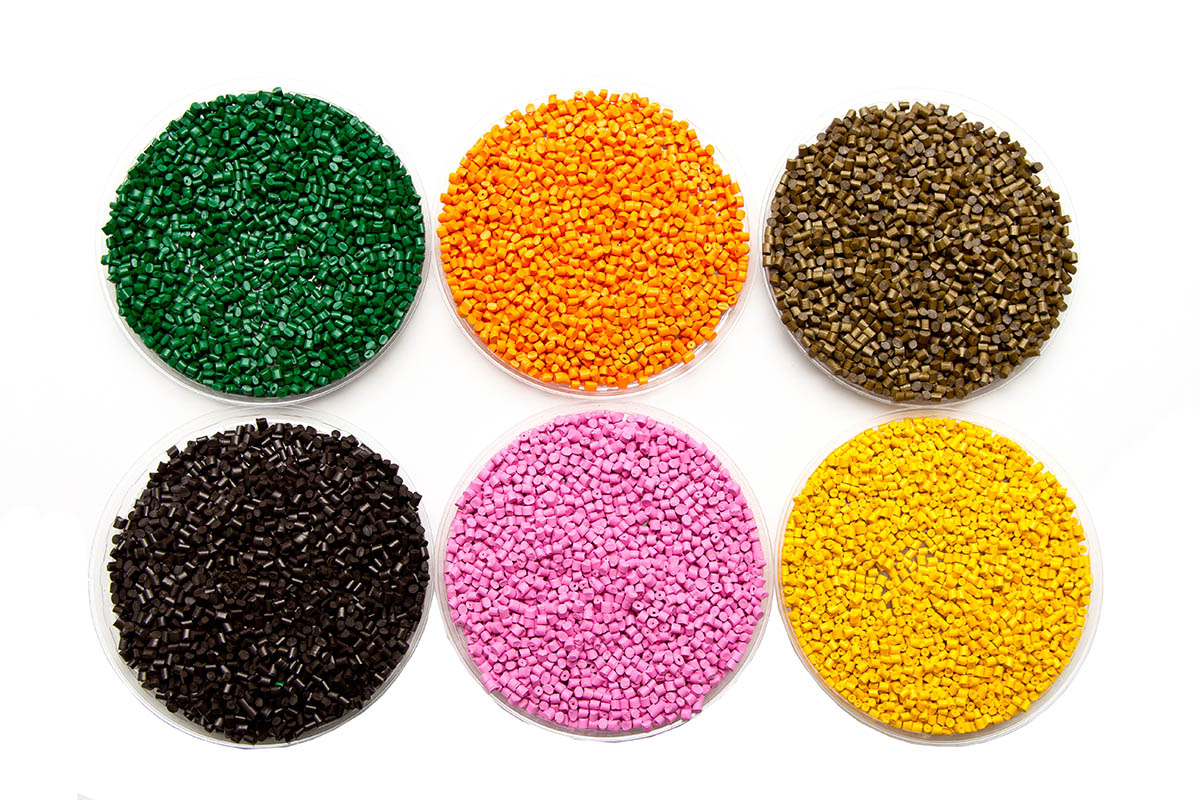
1. Choosing Materials Based on Application
- Medical & Food-Grade: Requires resistance to high-temperature steam sterilization (above 121°C) and FDA certification. Preferred materials include S136 or titanium alloy (TC4), which cost 30%–50% more than standard steel.
- Automotive & Industrial-Grade: Needs wear resistance and impact resistance. Common choices include H13 steel or glass fiber-reinforced materials (e.g., PA66+GF).
- Consumer Electronics: Prioritizes surface smoothness. 718 steel with mirror polishing is the mainstream choice.
2. Balancing Material Performance and Cost
- Wear Resistance: Steel hardness (HRC 48-52) directly affects mold lifespan. High-hardness steel has a higher initial cost but lower per-unit amortization.
- Corrosion Resistance: Corrosive plastics like PVC require S136 steel or chrome plating, increasing costs by 10%–15%.
- Thermal Conductivity: Aluminum alloys conduct heat better than steel, enabling faster cooling for small molds but require more frequent replacements.
Impact of Manufacturing Processes on Cost
1. Injection Molding Process Selection
- Standard Injection Molding: The most cost-effective option, suitable for standard part production with simple mold designs.
- Two-Shot Injection Molding: Requires specialized molds and two-shot injection machines, increasing mold costs by 50%–100%, but eliminates the need for assembly.
- Microcellular Foam Injection Molding: Reduces material usage but requires gas-assisted equipment, increasing initial investment by 20%–30%.
2. Process Optimization
- Rapid Prototyping (3D Printing): Used for prototype validation, with costs ranging from $140–$700. It helps avoid the risk of failures when directly creating steel molds.
- Standardized Mold Frames (LKM, DME): Reduces customization costs, saving 10%–20%.
Cost Optimization Strategies
1. Design Stage Optimization
- Simplifying Structure: Reduce undercuts, slide mechanisms, and rationalize parting line design to lower processing complexity.
- Mold Flow Analysis: Predict filling defects in advance to reduce the number of trial molds, which cost $280–$700 per attempt.
2. Supply Chain Management
- Location Selection: Mold manufacturers in regions like Dongguan and Ningbo offer quotes that are 30%–50% lower than those in Europe and the US, with convenient logistics.
- Volume Discount Negotiation: Produce multiple sets of the same mold (e.g., for automotive parts) to reduce the cost per set by 10%–20%.
3. Lifecycle Cost Control
- Maintenance: Regular cleaning and lubrication can extend mold lifespan by 20%–30%.
- Mold Repair Budget: Set aside 5%–15% of the initial cost for future adjustments (e.g., parting line wear repair).
Case Analysis
1. Medical-Grade PPSU Mold
- Requirements: Must withstand high-temperature steam sterilization, feature mirror polishing, and meet FDA standards.
- Cost: Precision multi-cavity molds range from $28,000–$70,000, with mold amortization accounting for 30%–40% of the unit cost.
2. Consumer Electronics ABS Enclosure Mold
- Requirements: Surface free from weld lines and high dimensional stability.
- Cost: Standard steel molds range from $11,000–$21,000, with mold amortization accounting for 5%–10% of the unit cost.
Important Considerations
1. Sample Testing
It is recommended to first create an aluminum mold or 3D-printed prototype to validate the design’s feasibility.
2. Environmental Compliance
Electroplating processes may be restricted, so alternative solutions (e.g., PVD coating) should be planned in advance.
Summary and Recommendations
The cost of plastic injection molds varies greatly (from $700 to over $140,000), and decisions should be based on specific needs (material, precision, production volume):
- Accurate Quotation: Search on Google or Bing and contact 3–5 suppliers, providing 3D drawings to obtain detailed quotes.
- Preferred Regions: Choose suppliers locally or from China to balance cost and quality.
- Long-Term Planning: Allocate 10%–15% of the budget for 3D printing prototypes and design changes to mitigate risks in mass production.
Appendix
Below are tables compiled by KingStar Mold based on years of experience. They cover key dimensions such as mold costs, material selection, manufacturing processes and so on to help you quickly compare and understand mold development costs.
Table 1: Mold Types and Cost Comparison
Mold Type | Applicable Scenarios | Material Selection | Price Range (USD) | Lifespan (Cycles) | Core Cost Drivers |
---|---|---|---|---|---|
Basic Aluminum Mold | Low-volume prototyping, quick validation | 7075 Aluminum | $700–$2,800 | 3,000–5,000 | Low material cost, short processing time |
Standard Steel Mold | Household appliances, consumer electronics | P20 Steel, 718 Steel | $2,800–$11,300 | 50,000–100,000 | Steel material cost, medium precision machining |
Precision Steel Mold | Medical, automotive, optical components | H13 Steel, S136 Steel | $11,300–$70,500 | 500,000+ | High-hardness steel material, complex processing |
Multi-Cavity Mold (8+ Cavities) | High-volume production (e.g., bottle caps, connectors) | High-hardness Steel + Hot Runner System | $14,000–$140,000 | 1,000,000+ | Increased cavities, hot runner system cost |
Table 2: Mold Steel Selection and Costs
Steel Type | Material Type | Hardness (HRC) | Corrosion Resistance | Polishability | Applicable Plastics | Market Price (USD/ton) | Processing Difficulty | Heat Treatment Requirements | Mold Life (100,000 cycles) | Key Advantages & Limitations |
---|---|---|---|---|---|---|---|---|---|---|
P20 | Low-Alloy Pre-Hardened Steel | 28-32 | Average | Good | PE, PP, ABS, PS, etc. | $730–$1,230 | Low | No heat treatment needed | 20–30 | Low cost, easy to process, but poor wear resistance. |
718 | P20 Improved (Nickel Added) | 30–33 | Medium | Excellent | PS, ABS, PC, etc. | $1,230–$1,423 | Medium | Pre-hardened | 30–40 | High polish, suitable for complex molds, but more expensive than P20. |
S136 | Stainless Steel (High Chromium) | 48–52 | Excellent | Excellent | PVC, PA+GF, PMMA, etc. | $2,050–$3,076 | High | Complex heat treatment needed | 50–80 | Excellent corrosion resistance, mirror finish, but expensive and difficult to process. |
H13 | Hot Work Tool Steel | 48–52 | Medium | Good | PA, POM, high-temperature plastics | $2,556–$3,076 | High | Quenching and tempering | 80–100 | High temperature, wear-resistant, suitable for high-volume production. |
9SiCr | Alloy Tool Steel | 18–22 (Annealed) | Low | Average | General engineering plastics | $1,077–$1,423 | Medium | Salt bath furnace heat treatment | 10–20 | Low cost, but short lifespan, suitable for low-precision molds. |
T7A | Carbon Tool Steel | 60–64 | Low | Poor | Non-corrosive plastics | $924–$981 | High | Quenching and low-temperature tempering | 5–10 | High hardness but brittle, prone to deformation. |
Cr12MoV | Cold Work Tool Steel | 58–62 | Medium | Average | High-wear plastics (e.g., glass-filled) | $2,041–$2,308 | High | Vacuum heat treatment | 30–50 | Excellent wear resistance, but lacks corrosion resistance. |
Table 3: Processing Cost Details
Processing Stage | Cost Range (USD/hour or per mold) | Time Required (hours) | Application | Key Equipment/Technology |
---|---|---|---|---|
CNC Rough Machining | $28–$56 per hour | 20–100 | Initial cavity forming | 3-axis CNC machine |
CNC Precision Machining | $56–$113 per hour | 10–50 | Precision structures (±0.01mm tolerance) | 5-axis CNC machine |
EDM (Electrical Discharge Machining) | $14–$42 per hour | 10–30 | Deep holes, complex textures | Precision EDM machine |
Mirror Polishing | $70–$280 per mold | 5–20 | Transparent/appearance parts (e.g., phone cases) | Manual + mechanical polishing |
Nitriding Treatment | $140–$700 per mold | 2–5 | Increased wear resistance (e.g., automotive molds) | Ion nitriding furnace |
Table 4: Mold Cost Cases in Different Industries
Industry | Typical Product | Material/Process Requirements | Mold Cost Range (USD) | Per-Unit Mold Depreciation Cost (for 100,000 pcs) (USD/pc) |
---|---|---|---|---|
Medical Devices | Surgical Instrument Shell | S136 steel + mirror polishing + FDA certification | $28,000–$70,000 | $0.07–$0.14 |
Consumer Electronics | Phone Casing | 718 steel + high-gloss finish | $11,000–$21,000 | $0.014–$0.042 |
Automotive Parts | Dashboard Bracket | H13 steel + hot runner system | $42,000–$113,000 | $0.042–$0.11 |
Food Packaging | Bottle Caps (32-cavity mold) | Multi-cavity mold + standard steel | $21,000–$42,000 | $0.003–$0.007 |
Table 5: Cost Optimization Strategies and Effects
Optimization Area | Specific Measures | Cost Savings (%) | Potential Risks |
---|---|---|---|
Design Optimization | Reduce sliders/core pull mechanisms | 10%–20% | May limit product functionality |
Material Substitution | Use aluminum molds instead of steel (for prototyping) | 50%–70% | Short lifespan, unsuitable for mass production |
Process Simplification | Eliminate mirror polishing (for non-appearance parts) | 5%–15% | Surface roughness may not meet requirements |
Regional Supply Chain | Choose suppliers in Jiangsu/Zhejiang/Shanghai, China | 20%–30% | Strict factory audits needed to ensure quality |
Mass Production | Use the same mold for multiple production runs (auto parts) | 10%–20% | Requires stable order volume |
Table 6: Additional Costs and Long-Term Maintenance
Item | Cost Range (USD) | Description |
Trial Mold Costs | $280–$700 per test | Verifies mold design (usually requires 2–3 trials). KingStar Mold does not charge extra for this. |
Mold Repair Costs | 5%–15% of initial cost | Covers wear on parting lines, ejector pin adjustments, etc. If KingStar Mold is your plastic injection molding supplier, we cover this cost. |
Environmental Compliance | $140–$1,400 | Includes electroplating wastewater treatment, exhaust filtration systems. KingStar Mold does not charge extra for this. |
Mold Maintenance | $70–$280 per year | Regular lubrication and cleaning extend mold lifespan by 20%–30%. If KingStar Mold is your plastic injection molding supplier, we cover this cost. |
Usage Recommendations of Tables Above
- Quick Reference – Use Table 1 and Table 2 to identify the appropriate mold type and material based on product requirements.
- Budget Allocation – Factor in Table 3 and Table 6 to set aside 15%–20% of the total budget for trial molding, maintenance, and other costs.
- Optimization Decisions – Refer to Table 5 to balance cost and risk (e.g., aluminum molds for small-batch prototyping, steel molds for mass production).