Plastic storage bins are everywhere—from your garage to warehouse shelves. But have you ever wondered why some bins last for years while others crack after a few months? The secret lies in how they’re made. As a leading custom wholesale plastic storage box manufacturer, we provide this guide for:
- Students/everyday users: This guide breaks down the “journey” of a plastic bin, from raw materials to finished product, in simple terms.
- Buyers: You’ll learn which manufacturing steps directly affect durability, safety, and cost—so you can pick the right bins for your needs.
- Professionals: We’ve included detailed process parameters, testing standards, and equipment specs to support technical evaluation.
So let’s get started.
- 1. Plastic Storage Bin Manufacturing Process Flowchart
- 2. Detailed Manufacturing Steps
- 3. Quality Testing Protocols
- 4. Packaging & Logistics
- 5. Compliance & Certifications: Built for Global Markets and Sustainability
- Conclusion
1. Plastic Storage Bin Manufacturing Process Flowchart

The birth of the plastic storage box involves 7 core steps: selecting materials → preparing resins for use → injection molding → optional post-processing → assembly → quality inspection → packaging – each step directly affects the durability, safety and compliance of the finished product.
In the following section, we will explain these steps one by one.
2. Detailed Manufacturing Steps
Producing high-quality plastic storage bins (or any other plastic boxes) requires a precisely controlled, multi-step process to ensure durability, consistency, and compliance with industry standards. From material selection to final inspection, each stage is carefully executed using advanced technology and rigorous quality controls. Our vertically integrated approach allows us to optimize efficiency, reduce waste, and maintain strict tolerances throughout production.
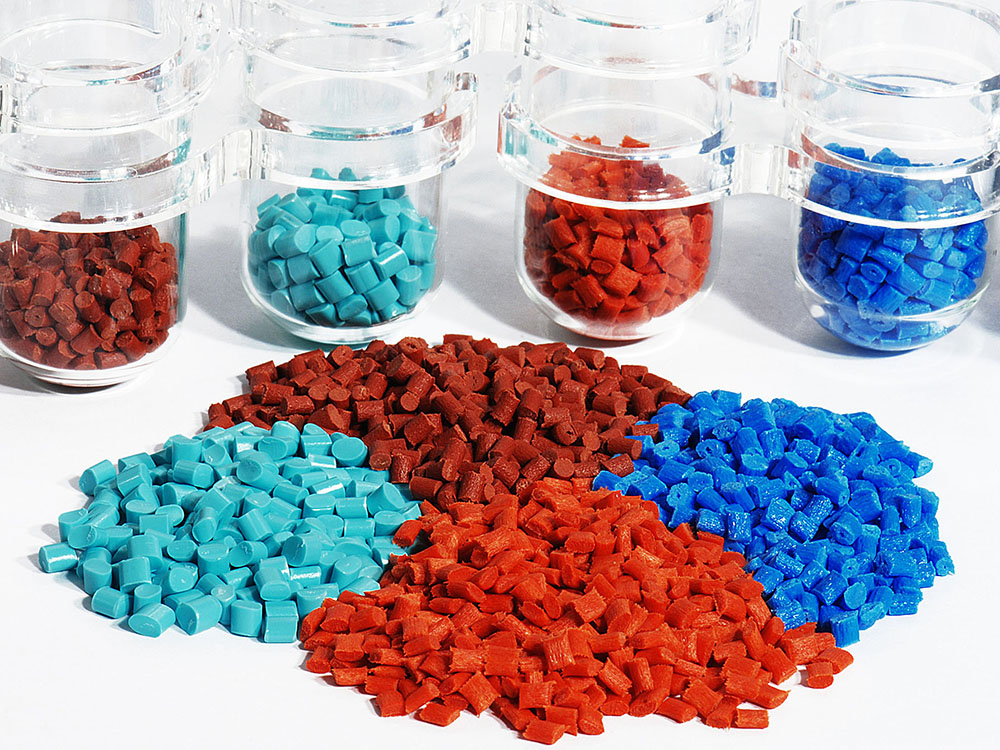
2.1 Raw Material Selection
Choosing raw materials isn’t just about specs—it’s about avoiding the mistakes we’ve learned the hard way. Early in our journey, a batch of household bins cracked in winter deliveries because we overlooked material behavior in cold temperatures. Now, every material undergoes a “two-layer filter”: matching real-world use cases and industry standards to ensure durability.
2.1.1 Three Core Plastics, Each Solving a Specific Problem
We lean on three core materials, but their strengths shine in different scenarios:
- Polypropylene (PP) is our pick for everyday toughness—think kids’ toy bins or garage storage. Its MFI of 10–25 g/10min (230°C/2.16kg) balances flexibility and strength, so it resists cracks when dropped but stays rigid enough to stack. We once had a client swap from cheaper PP (with MFI outside this range) and saw winter breakages drop by 90%—proof that the right specs matter.
- High-Density Polyethylene (HDPE) handles chemicals and moisture, making it ideal for bins holding cleaners or liquids. With a density of 0.941–0.965 g/cm³ (per ASTM D1505), it stands up to acids and oils—unlike a batch we tested years ago that warped after 30 days of holding industrial degreaser.
- ABS steps in when rigidity is critical, like fire-retardant industrial toolboxes. It’s stiffer than PP or HDPE but costs more, so we use it sparingly—usually for custom orders where bins need to hold heavy gear without bending.
2.1.2 Two Quality Checks: Stopping Problems Before They Start
Raw materials don’t just “pass inspection”—we test them like they’re about to fail. Here’s how:
- Certificate Audits
First, we verify RoHS, REACH, and FDA compliance (critical for food-contact bins or exports to Europe/North America). This isn’t just paperwork—we once caught a supplier trying to pass off industrial-grade PP as food-safe. Catching that early saved a potential recall. For kitchen storage bins, FDA 21 CFR 177.1520 compliance is non-negotiable—no one wants chemicals leaching into their cereal.
- Batch Testing
We run every batch through a Tinius Olsen MP600 MFI Analyzer to spot “hidden risks.” For example, if PP’s MFI drifts below 10, the resin flows too sluggishly—molds won’t fill completely, leaving bins with weak corners. If it jumps above 25, the plastic cools too brittle. By testing, we catch these issues early (e.g., adjusting injection pressure for off-spec batches) and avoid full production failures.
2.2 Resin Preparation
Of course, some manufacturers may choose to purchase the available resin directly. However, we offer a complete service from raw materials to the final product. And here is our experience: proper resin prep is like baking: if your ingredients aren’t right, the final product fails.
2.2.1 Drying: Remove Moisture, Prevent Bubbles
Even slight moisture causes cracks or surface defects, therefore, before the injection molding process begins, it is necessary to remove as much moisture as possible from the resin, and here’s our standard process:
- Equipment: Motan LUXOR M20 Dehumidifier (dual-stage desiccant)
- Typical Settings:
- PP: 90°C ±5°C for 3 hours
- HDPE: 80°C ±5°C for 2.5 hours
- Goal: Moisture ≤0.02% (verified by Sartorius MA35 analyzer).
2.2.2 Mixing: Adding What the Bin Needs Most
This is where we “customize” the plastic. Depending on what the bin will do, we mix in additives: maybe colorant to match a brand, UV stabilizers if it’ll live outdoors (to prevent fading or cracking in sunlight), or even special compounds for food-contact bins (to meet safety standards).
The amount of each additive varies—more UV stabilizer for bins for outdoor uses, and less for indoor storage; the content of the colorant is adjusted according to the different levels of color vividness. We use specialized mixing equipment to make sure these additives spread evenly, so every part of the bin gets the same protection or color.
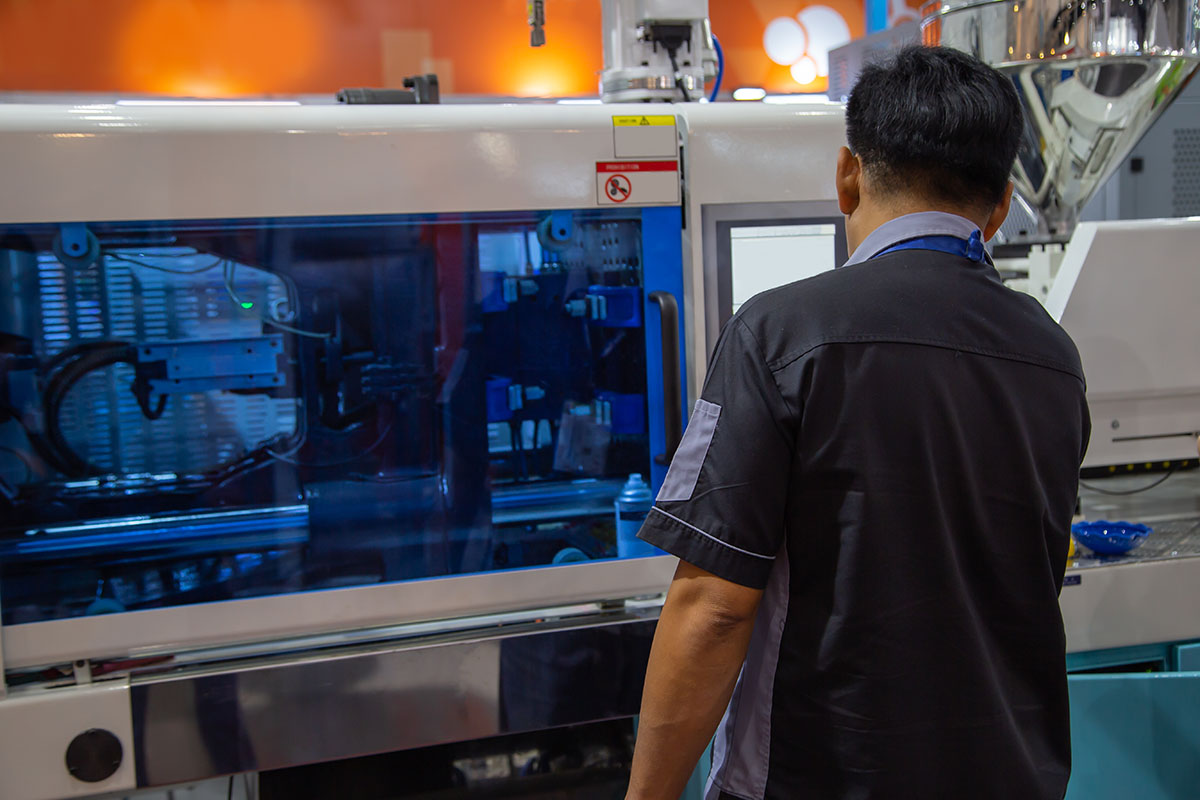
This is where prepared resin transforms into a storage bin—think of it as the “sculpting step,” turning molten plastic into a precise, repeatable shape. For us, injection molding isn’t just a process—it’s a core specialty, honed over years of refining how to get crisp edges, consistent thickness, and reliable performance in every bin.
2.3.1 The Basics: How It Works
First, the prepped resin (dried and mixed with additives) feeds into the machine, where it’s heated until it melts into a smooth, flowable state with just the right thickness to fill every nook of the mold.
Once molten, the machine uses high pressure to push the plastic into a steel mold, which is shaped exactly like the final bin. The mold clamps shut tight to keep the plastic from leaking, then cools the plastic just enough to harden it into the mold’s shape. When it’s set, the mold opens, and the bin is gently ejected.
2.3.2 Our Parameters
Next, we present the equipment, molds and process parameters that we used in our previous project for your reference.
- Core Equipment:
- Haitian Mars Series 1300T Injection Molding Machine (Clamping force: 1,300 tons).
- Mold Material: P20 pre-hardened steel with hardened cavities (HRC 28–32) for 500,000+ cycles.
- Process Parameters:
Parameter | PP Values | HDPE Values |
---|---|---|
Melt Temperature | 230–260°C | 190–220°C |
Injection Pressure | 1,000–1,200 bar | 800–1,000 bar |
Holding Pressure | 70% of injection pressure | 60% of injection pressure |
Cooling Time | 30–60 sec (wall thickness: 2–5mm) | 25–50 sec (wall thickness: 2–4mm) |
- Key Controls:
- Screw Speed: 50–80 mm/s during plastication.
- Mold Temperature: 40–60°C maintained via Regloplas Thermolator (Model TIO 200).
Since injection molding is core to what we do, we’ve unpacked the details in a full guide: What Is Plastic Injection Molding? Dive into that if you want to learn more about the science behind melt flow, mold design, or how we troubleshoot tricky parts.
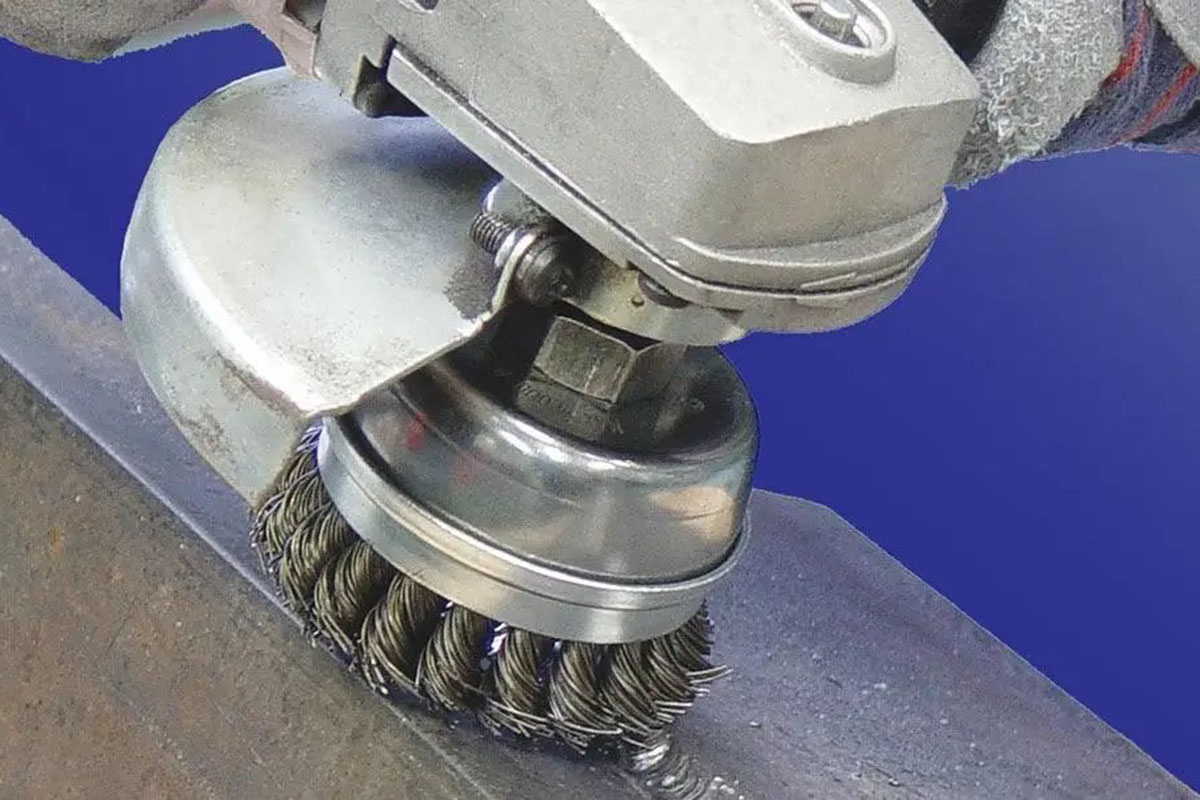
2.4 Post-Processing
After molding, post-processing isn’t just about fixing flaws—it’s about tailoring the bin to its job. While basic bins might skip extra steps, these common surface treatments add durability, grip, or branding that makes a bin feel “custom-built.”
2.4.1 Our Most Requested Surface Treatments
We offer a range of tweaks, depending on whether you need better grip, weather resistance, or a branded look:
- Deflashing: A must for safety. Robotic trimmers (like the ABB IRB 4600) shave off tiny plastic “flash” (sharp edges) to 0.5mm or less—no more scratched hands when moving bins.
- Anti-Slip Texturing: Critical for stacked bins. Options include:
- Laser etching (Trumpf TruMark 6230) for precise, shallow grooves (0.2–0.5mm deep) that grip when stacked.
- EDM-machined textures (Ra 3.2–6.3μm roughness) for a matte, rubbery feel—great for toolboxes or medical bins that get frequent handling.
- Paint or Coating: Boosts longevity, especially for outdoor bins. We use UV-resistant acrylic paints or clear coats that:
- Prevent fading from sunlight (so garden storage bins stay vibrant).
- Add a glossy or matte finish (for a polished look in commercial spaces like offices).
- Screen Printing: Perfect for branding. Using mesh stencils, we apply ink to print logos, warning labels, or serial numbers—durable enough to withstand repeated cleaning (ideal for warehouse bins or retail displays).
- Frosting/Matte Finishing: Reduces glare and hides scratches. A chemical etch or sandblasting creates a soft, non-reflective surface—popular for indoor bins in kitchens or offices, where shiny plastic might look cheap.
- Anti-Static Treatments: For industrial use. A specialized coating (or additive mixed into the plastic) dissipates static, preventing dust buildup or damage to electronics stored in the bins.
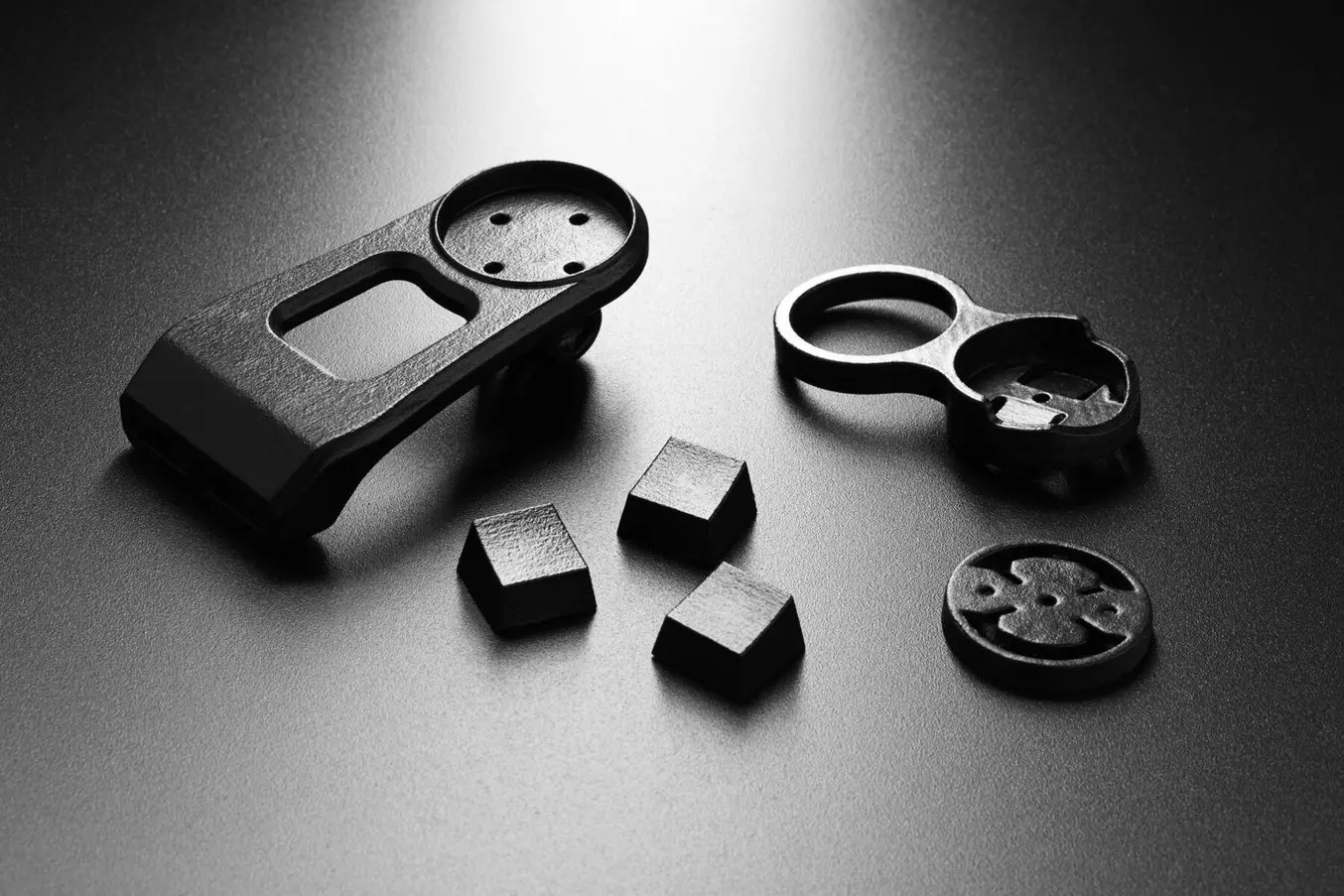
2.5 Assembly
Assembly keeps things straightforward—our focus is on adding components that boost usability, like handles or wheels, while other details are streamlined for efficiency.
For handle assembly, we use two reliable methods:
- Ultrasonic Welding: For lightweight to medium bins, handles are fused to the bin’s sides with ultrasonic vibrations—no screws, just a seamless, durable bond that won’t loosen over time.
- Screw-Mounted Handles: For heavy-duty bins (e.g., those holding tools or industrial parts), we pre-drill reinforced holes and secure handles with corrosion-resistant screws. This ensures they can bear weight without cracking the bin’s walls.
And for bins that need to roll (easier to move like a small cart), we often add plastic casters with snap-fit bases—they lock into pre-molded slots on the bin’s bottom, making installation quick (no tools needed).
Other assembly details stay simple too: Flip-top lids use basic plastic or metal hinges, often pre-molded into the bin during shaping, while bins with adjustable compartments have interior slots—dividers slide right in without extra hardware.
Quality isn’t just checked at the finish line—it’s built into every step of production. We’ve woven rigorous checkpoints throughout the manufacturing process to catch issues early, ensuring consistency from start to finish:
- Resin Preparation: Moisture content is strictly limited to ≤0.02% (per ASTM D6980) to avoid defects in molding.
- Injection Molding: Every 50 cycles, a short-shot test verifies the mold fills completely, preventing misshapen bins.
- Post-Processing: 100% inspection with Mitutoyo Contracer CV-3200 ensures no burrs or rough edges slip through.
- Final Assembly: Hinges and latches undergo functional testing to EN 12521:2015 standards, guaranteeing smooth, durable operation.
For readability, we’ve first walked through the production steps before highlighting these checks—but rest assured, quality management runs parallel to every stage, not just at the end. This approach keeps small issues from becoming big problems, so the bins that reach you are reliable, every time. Here is a test form attached for your reference:
Test Category | Test Item | Objective | Method/Equipment | Acceptance Criteria | Reference Standard |
---|---|---|---|---|---|
Appearance Testing | Surface Defects | Verify aesthetic quality | Keyence CV-X200 Vision System (10MP camera, 2,000 lux LED); 360° automated scan | 0 critical defects (Class A); ≤3 minor defects (Class B) | ASTM D2561-17 |
Dimensional Accuracy | Ensure size consistency | Mitutoyo Digital Caliper (±0.01mm), Zeiss CONTURA G2 CMM; measures length/width/height, wall thickness | Critical dimensions: ±0.5mm; Non-critical: ±1.0mm | ISO 2768-1 (Medium grade) | |
Performance Testing | Load Capacity Test | Validate structural integrity under load | Instron 5967 Universal Testing Machine (50kN load cell); applies 150% rated load for 24h | Permanent deformation < 2% of bin height | - |
Drop Test | Assess impact resistance | Custom drop tester (0-3m height, concrete surface); 1.5m drops on corners/edges/base (3x each) | No through-wall cracks; volumetric loss ≤ 1% | ASTM D5276 | |
Reliability Testing | Thermal Cycling Test | Evaluate durability under extreme temperatures | ESPEC PH-032 Walk-in Chamber; 50 cycles (-20°C for 2h → +60°C for 2h) | Deformation ≤ ±1.5mm; residual strength ≥85% of initial | - |
Chemical Resistance Test | Test resistance to corrosive substances | Immersion in 5% NaOH/HCl (40±1°C) for 48h; measured via weight/color change | Weight change ≤ 0.5%; color shift (ΔE) ≤ 3.0 | ISO 175 | |
Hinge Durability Test | Verify hinge longevity under repeated use | TEKMAK HDT-1000 Tester; 10,000 cycles (0°→110°→0°), 30 cycles/min | No fracture/deformation; torque fluctuation ≤ ±15% of initial | - |
For data management, we have:
- Test Records: Q-DAS quality analysis software generates tamper-proof PDF reports (timestamped with operator e-signatures).
- Sample Retention: 2 units per batch archived for ≥5 years (23°C/50% RH controlled storage).
- Traceability: Laser-marked QR codes (SIC Marking QUBE) on each bin link to full production/test data.
For more information, please check our earlier post: Quality Inspection Standards for Plastic Products
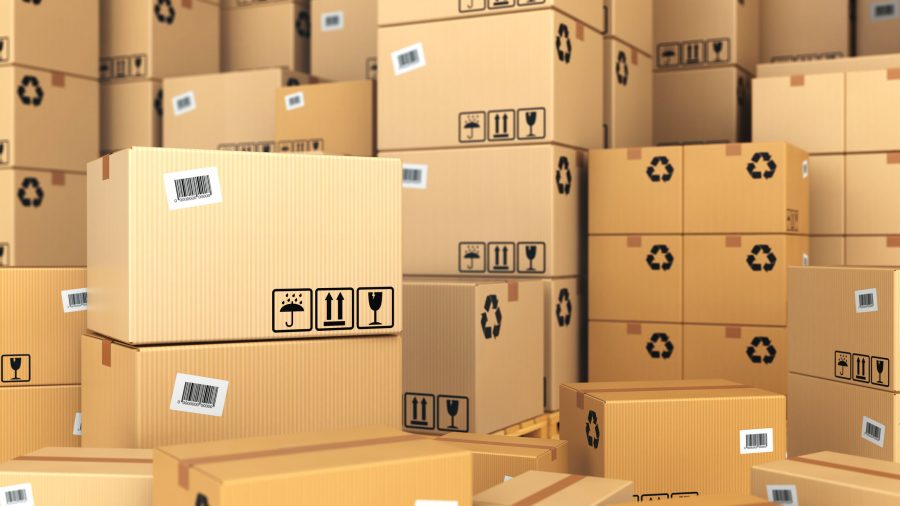
4. Packaging & Logistics
We keep packaging and logistics flexible to fit your needs.
For packaging, we offer custom solutions—whether you need branded boxes, protective inserts, or eco-friendly materials—tailored to protect your bins during transit and align with your branding (e.g., logo printing, specific sizing).
On the logistics side, we adapt to your preferences: choose from sea, air, or land freight, and we’ll coordinate with your preferred carriers or our trusted partners to meet delivery timelines.
5. Compliance & Certifications: Built for Global Markets and Sustainability
We design our bins to meet strict standards—whether that’s passing international safety regulations, aligning with eco-goals, or supporting your brand’s compliance needs. Here’s how we deliver:
5.1 Meeting Global Safety Standards
Ever had a bin get held up at customs because it didn’t meet local rules? We avoid that by designing for global standards from day one.
If you’re selling bins for kitchen use (think cereal, snacks), they’ll pass FDA 21 CFR 177.1520 checks—meaning no weird chemicals leach into food. We once had a small food brand panic because their old supplier’s bins failed this test; switching to ours let them restock without a hitch.
For Europe, we hit EU Regulation 10/2011 standards, so retailers in Germany or France won’t bat an eye. And for China, our bins meet GB/T 28798-2012—tough enough to handle warehouse stacking without cracking (we test impact resistance to at least 8 kJ/m², which matters when someone drops a full bin).
Need something specific? Like UKCA marks for Britain or KC marks for Korea? We’ve helped dozens of clients tweak formulas or paperwork to clear those hurdles—no last-minute scrambles.
5.2 Sustainability That Goes Beyond Compliance
We blend performance with eco-responsibility, backed by verified initiatives:
- Recycled materials: Up to 40% post-industrial recycled (PIR) content in HDPE/PP bins (validated by UL ECVP 2809), with options for ≥30% post-consumer recycled (PCR) material (SCS certified) — ideal for brands marketing “green” products.
- Waste reduction: In-house regrind systems cut production waste by 98%, and our ISO 14001:2015 certification ensures energy-efficient manufacturing (≤0.45 kWh/kg) and 85%+ wastewater recycling.
- Carbon-neutral options: Add optional shipping offsets via Gold Standard VERs to reduce your supply chain’s carbon footprint.
For more information about plastic industry trend against restriction, please check our post: Trend Report: Injection Molding Industry Amid Plastic Restrictions
5.3 How This Benefits You
- Risk reduction: A 10-year warranty covers material defects like cracking or UV degradation, so you avoid costly replacements.
- Audit support: We provide full supplier qualification packages (SQP) with test data, making audits for retailers like Walmart or Target straightforward.
- Brand alignment: Whether you need eco-certifications for marketing or region-specific marks for distribution, we tailor compliance to fit your brand’s goals.
Conclusion
So, what does it really take to make a plastic storage bin? As this guide has laid out, it’s a journey—one that starts with choosing the right resin (PP for toughness, HDPE for chemicals), prepping it to avoid flaws (drying, mixing in additives), shaping it with precision injection molding, refining it with post-processing (if needed), and ensuring it holds up through rigorous testing (drops, loads, extreme temps). Every step, from the first grain of plastic to the final package, matters.
This guide was meant to demystify “how it’s made”—but the real value? Knowing that behind every bin is a process rooted in precision, quality, and adaptability. Need to tweak a step for your unique needs? Want to dive deeper into a specific stage (like injection molding or compliance testing)? We’re here to walk through it with you.
After all, making a great plastic storage bin isn’t just about following steps—it’s about understanding why each step matters. And that’s what we bring to every project. Ready to turn your idea into a bin that lasts? Let’s start with the first step, contact us at: