How Are Cooler Boxes Made? As the world’s leading hard cooler manufacturer, KingStar receives emails asking this question every week. This question is raised by our customers, consumers, and college students.
Cooler boxes are an essential part of modern outdoor living. Whether you’re headed to the beach, planning a weekend camping trip, or simply transporting groceries, a reliable cooler keeps your food and drinks cold and fresh. But beyond their practical function, cooler boxes have evolved into highly engineered products designed to withstand harsh environments, retain ice for days, and offer added convenience features.
So, how exactly are these versatile boxes made? Understanding the manufacturing process isn’t just for engineers—it helps you make smarter buying decisions. From performance and durability to cost and weight, the way a cooler is built directly affects how well it works and how long it lasts.
Contrary to what some might think, cooler boxes aren’t just hollow plastic containers. They’re precision-built using advanced materials, specialized molding technologies, and layered insulation systems. In this guide, we’ll walk through what goes into making a cooler box—from raw materials to final assembly—so you can appreciate what’s behind the cold.
- 1. What Makes a Cooler Box Work?
- 2. Essential Materials Used in Cooler Manufacturing
- 3. Rotomolding Process: Heavy-Duty Coolers
- 4. Injection Molding Process: Lightweight Efficiency
- 5. The Role of Insulation in Cooler Performance
- 6. Additional Design Features in Modern Cooler Boxes
- 7. Quality Control and Testing
- 8. Environmental and Manufacturing Considerations
- 9. Choosing the Right Cooler Box for Your Needs
1. What Makes a Cooler Box Work?
At its core, a cooler box is a thermal barrier designed to slow down the transfer of heat from the outside environment to its cold interior. But to achieve that, it needs more than just thick walls—it relies on a thoughtful combination of materials, insulation techniques, and design details that all work together to preserve low temperatures for as long as possible.
The main goal of any cooler box is to retain cold and prevent heat from entering. Cold doesn’t “leak out”—rather, heat “creeps in” through conduction, convection, and radiation. A well-designed cooler delays this heat transfer, extending ice life and protecting perishable contents even in hot weather.
1.1 Basic Components of a Cooler Box
A standard cooler box typically consists of four key parts:
- Outer shell: Made from durable plastic (usually polyethylene), this forms the structural backbone and protects against impacts.
- Insulation core: Often polyurethane foam or expanded polystyrene (EPS), the core slows heat transfer by trapping air and reducing conduction.
- Inner liner: A food-safe, often smoother plastic layer that lines the cooler’s interior and resists stains and odors.
- Gaskets and seals: High-quality rubber gaskets around the lid form an airtight seal, reducing heat infiltration through gaps.
Each of these elements plays a critical role. If one underperforms—say, a flimsy seal or low-density foam—it can compromise the cooler’s entire effectiveness.
1.2 Key Performance Factors
The real performance of a cooler box comes down to a few essential qualities:
- Insulation efficiency: High-density foams offer better thermal resistance and longer ice retention.
- Material strength: The outer shell needs to resist impacts, UV degradation, and rough handling without warping or cracking.
- Design features: Lid latches, drain plugs, non-slip feet, and ergonomic handles all contribute to usability—but they also need to be engineered to avoid introducing heat leaks or weak points.
In short, a good cooler isn’t just a box—it’s a well-balanced system engineered to keep cold in and everything else out.
2. Essential Materials Used in Cooler Manufacturing
The performance and longevity of a cooler box are heavily influenced by the materials used in its construction. Each component—from the outer shell to the tiniest gasket—plays a role in insulation efficiency, structural durability, and user experience. Here’s a closer look at the essential materials that go into making a high-quality cooler.
2.1 High-Density Polyethylene (HDPE)
HDPE is the go-to material for rotomolded cooler exteriors, and for good reason. It offers:
- Superior impact resistance, which makes the cooler rugged enough for outdoor and industrial use.
- UV resistance, helping it withstand long sun exposure without cracking or fading.
- Moldability, which allows for seamless, thick-walled structures that minimize weak points.
This material is ideal for premium, heavy-duty coolers meant to handle rough conditions while maintaining excellent insulation.
2.2 Polypropylene & ABS Plastics
In injection molded coolers, lighter and more cost-effective plastics are often used:
- Polypropylene is valued for its chemical resistance and light weight, making it easy to carry while still being reasonably durable.
- ABS (Acrylonitrile Butadiene Styrene) provides added rigidity and strength, often used for internal linings or handles where toughness and precision are important.
These plastics enable complex shapes and sleek designs, especially in consumer-grade models where weight and affordability are top priorities.
2.3 Polyurethane Foam (PU)
At the heart of every effective cooler lies its insulation, and polyurethane foam is the industry standard:
- Offers high thermal resistance (low thermal conductivity), meaning it effectively slows heat transfer.
- Fills the space between inner and outer walls, expanding to form a dense, continuous insulation barrier.
- Ensures longer ice retention, keeping contents cold for days under the right conditions.
PU foam’s high performance is a major reason why both rotomolded and injection molded coolers rely on it for internal insulation.
2.4 Silicone or Rubber Seals
No insulation system is complete without a tight seal:
- Silicone or rubber gaskets around the lid form a compressible, airtight barrier.
- They prevent warm air from sneaking in and cold air from escaping, significantly boosting ice retention performance.
- Quality seals are especially important in rotomolded coolers, which often feature freezer-grade gaskets for extreme efficiency.
These sealing materials might seem like a small detail, but they’re critical for the cooler’s overall thermal integrity.
3. Rotomolding Process: Heavy-Duty Coolers
Rotational molding, or rotomolding, is the gold standard for crafting ultra-durable, high-performance cooler boxes. This method is especially favored in the production of coolers built for the toughest environments—whether that’s a construction site, a fishing boat, or a multi-day backcountry trip.
3.1 What Is Rotomolding and How Does It Work?
Rotomolding is a low-pressure, high-temperature process that slowly rotates a mold while it’s being heated. The goal is to create a seamless, hollow body with thick and evenly distributed walls.
The key difference from other plastic forming techniques? The absence of pressure. Instead of being injected into the mold, plastic powder is heated and slowly coats the interior surface of the rotating mold. This gradual process is what gives rotomolded coolers their signature strength and uniformity.
3.2 Step-by-Step Breakdown of the Rotomolding Process
- Mold Loading
A precise amount of powdered plastic (typically HDPE) is loaded into an aluminum mold shaped like the final cooler body. - Heating & Rotation
The mold is placed in an oven and rotated bi-axially (on two axes). As the mold heats up, the plastic begins to melt and evenly coat every internal surface. - Cooling Phase
Once the plastic has fully melted and adhered to the mold walls, the mold is moved to a cooling station. Air or water is used to slowly reduce the temperature, allowing the plastic to solidify while maintaining its shape. - Part Removal
After cooling, the mold is opened and the newly formed cooler body is removed. At this stage, insulation foam is usually injected into the cavity between inner and outer walls.
3.3 Why Rotomolding Stands Out
Rotomolded coolers are prized for:
- Uniform wall thickness, which means no weak spots and more predictable performance
- High durability, capable of withstanding drops, UV rays, and harsh handling
- Seamless corners and edges, reducing the chance of cracking or water leaks
- Excellent insulation, thanks to thick walls and the ability to inject dense polyurethane foam
This method may take longer and cost more than alternatives, but it produces some of the most reliable, long-lasting coolers on the market.
3.4 Where Rotomolded Coolers Excel
Rotomolded coolers are commonly found in:
- Outdoor adventure gear (camping, fishing, hunting)
- Marine applications where saltwater and sun exposure are concerns
- Professional work environments like job sites or emergency services
Their rugged construction makes them ideal for users who need their cooler to function perfectly in demanding situations—where failure isn’t an option.
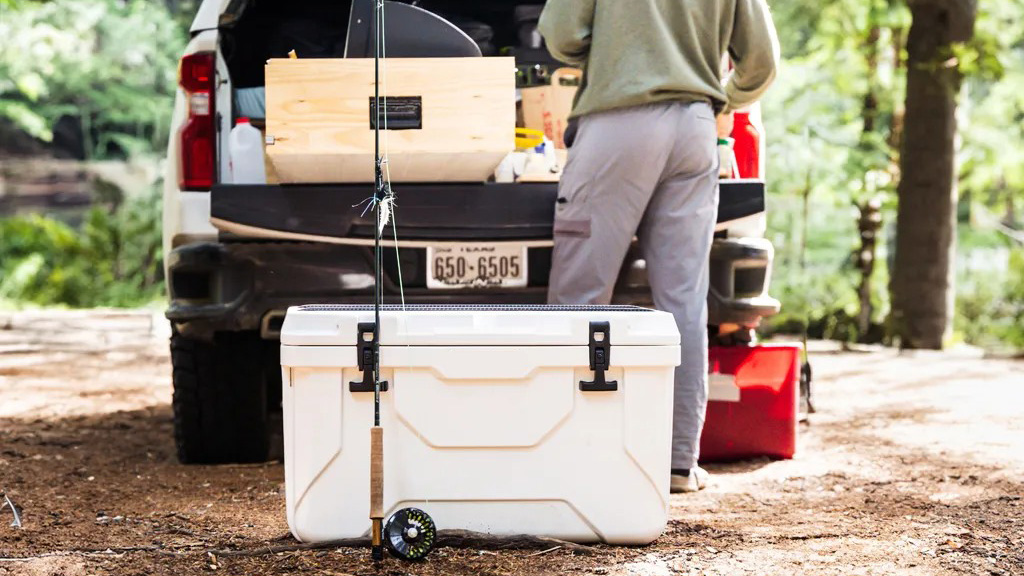
4. Injection Molding Process: Lightweight Efficiency
While rotomolding focuses on ruggedness and endurance, injection molding brings speed, flexibility, and cost-efficiency to cooler box manufacturing. This process is widely used for producing lightweight, stylish, and affordable coolers, particularly those intended for everyday or lifestyle use.
4.1 What Is Injection Molding?
Injection molding is a high-pressure manufacturing method that injects molten plastic into precision-engineered molds. The technique is ideal for creating products with complex shapes and fine details—which explains its popularity in mass-market consumer goods.
Unlike rotomolding, this process separates the inner and outer walls of a cooler. The two shells are formed independently and later assembled with insulation in between.
4.2 Step-by-Step Breakdown of the Injection Molding Process
- Mold Design and Setup
The process starts with a steel or aluminum mold that defines the cooler’s shape and surface details. These molds are more expensive but allow for high-volume production. - Plastic Injection
Plastic pellets (typically polypropylene or ABS) are heated until molten, then injected into the mold under very high pressure. This ensures the material fills even the smallest features of the mold. - Cooling and Ejection
Once the plastic fills the mold, it’s cooled rapidly to harden into shape. The mold then opens, and the formed plastic part is ejected. - Dual-Wall Assembly and Insulation
The inner and outer shells are assembled into a hollow body. Polyurethane (PU) foam is then injected between the walls and expands to fill the cavity, providing insulation.
4.3 Why Injection Molding Is Efficient
Injection molded coolers offer several clear benefits:
- Lightweight construction, often 20–30% lighter than rotomolded options
- Faster production cycles, ideal for large-scale manufacturing
- Design flexibility, allowing for detailed textures, built-in handles, cup holders, and even built-in bottle openers
- Lower material use, helping reduce costs and environmental impact
These advantages make injection molding a go-to method for cooler brands targeting urban users, occasional adventurers, or cost-sensitive consumers.
4.4 Where Injection Molded Coolers Fit Best
You’ll find injection molded coolers in:
- Everyday family outings or road trips
- Backyard parties and tailgating
- Retail chains offering stylish coolers with trendy colors or branding
- Budget-conscious markets, where affordability is prioritized
While they may not survive a grizzly bear encounter like rotomolded versions, these coolers more than meet the needs of the average consumer.
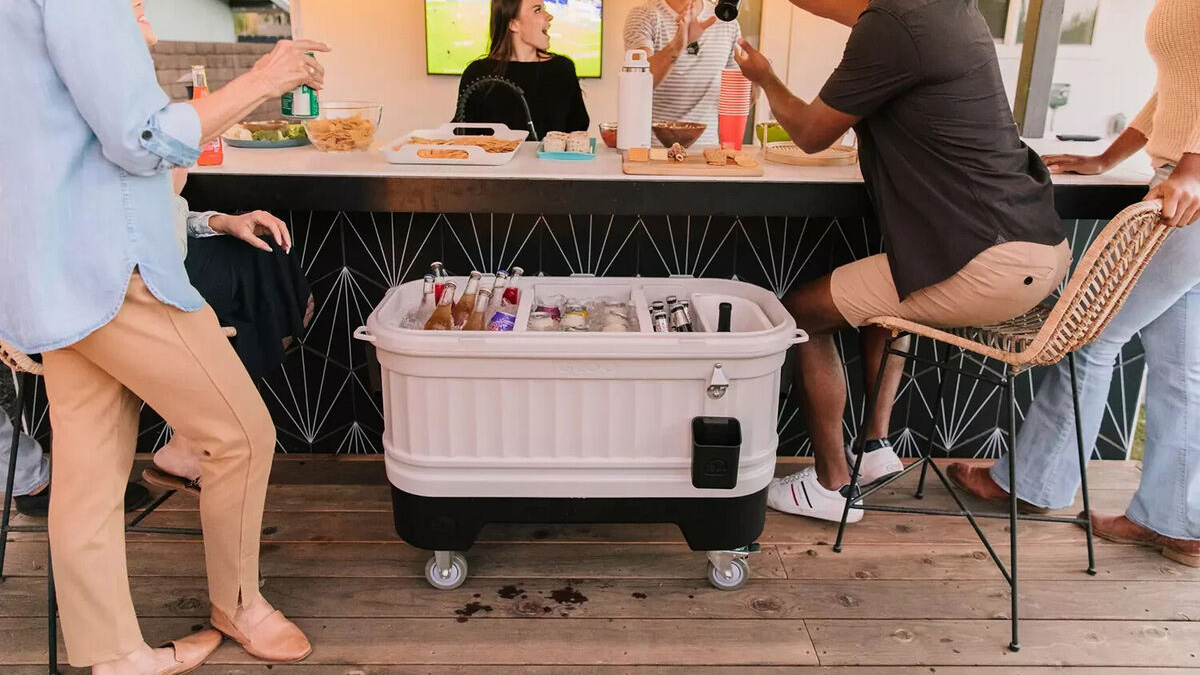
5. The Role of Insulation in Cooler Performance
The insulation in a cooler is its secret weapon, ensuring that your drinks stay chilled and your ice lasts longer. But how does it work? Simply put, insulation’s job is to prevent heat from entering the cooler, maintaining a cold internal environment despite external temperature fluctuations.
5.1 How Insulation Slows Down Heat Transfer
Heat transfer occurs in three main ways: conduction, convection, and radiation. In a cooler, insulation reduces all of these forms of heat transfer, allowing the cooler to preserve the cold temperature inside.
- Conduction is the transfer of heat through materials. A well-insulated cooler will have materials that resist heat flow, keeping the interior temperature stable.
- Convection is the movement of air or liquid. Insulation helps trap cold air and prevent the warm external air from circulating inside.
- Radiation is the emission of heat in the form of electromagnetic waves. Quality insulation materials reduce the impact of radiant heat as well.
The effectiveness of insulation in a cooler ultimately determines how long it will retain ice, which is why selecting the right material is crucial.
5.2 Polyurethane Foam vs. Other Fillers
When it comes to insulating coolers, polyurethane foam is the gold standard. But why is it so widely preferred over other fillers like polystyrene?
- Polyurethane Foam:
- Known for its high thermal resistance, making it extremely effective at slowing heat transfer.
- Expands and solidifies inside the cooler walls, creating a continuous, air-tight barrier that resists heat flow.
- Provides superior insulation while keeping the cooler’s walls thick and sturdy, without adding too much weight.
- Polystyrene:
- Often used in cheaper or less durable coolers.
- While it can provide decent insulation, it doesn’t compare to polyurethane in terms of thermal efficiency and durability.
- Can crack or break more easily under pressure or impact, reducing the cooler’s longevity.
Polyurethane is preferred for high-end models, particularly rotomolded coolers, where maximum ice retention is a top priority.
5.3 Ice Retention Times: What Insulation Thickness and Material Can Do
The thickness and quality of insulation directly influence how long a cooler can retain ice. Cooler manufacturers typically advertise ice retention times as a key selling point, and it can range anywhere from 2 days to a week or more, depending on insulation.
- Thicker Insulation:
- The more insulation there is, the better the cooler can keep the heat out. Premium coolers can have up to 3–5 inches of polyurethane foam in their walls, ensuring longer ice retention.
- Insulation Materials:
- Polyurethane (as mentioned) is the top performer in retaining cold for extended periods.
- Polyethylene and polystyrene are more common in lower-end coolers but still offer some insulation.
Manufacturers often recommend that consumers choose coolers based on how long they intend to keep their contents cold. For extended trips, thick insulation with high-quality foam will always deliver the best performance.
6. Additional Design Features in Modern Cooler Boxes
While the core function of a cooler box is to keep contents cold, modern coolers are often equipped with a variety of additional design features that enhance convenience, functionality, and durability. These features are not just add-ons—they’re integral to how well the cooler performs in different environments.
To improve user experience, coolers often come with built-in features that add to their ease of use:
Many high-end coolers come with molded, ergonomic handles that make transporting the cooler easier, even when it’s full of ice and beverages. These handles are designed for comfort and durability, preventing strain during transport.
Many models feature molded cup holders on the lid or sides, providing a convenient place to hold drinks while enjoying outdoor activities. This simple feature makes the cooler even more versatile during picnics, beach trips, or tailgating.
Coolers are designed with drain plugs to facilitate the removal of water and melted ice. These plugs help maintain cleanliness and prevent unwanted messes, making coolers much easier to manage in between uses.
And in order to ensure optimal insulation and prevent cold air from escaping, modern coolers include advanced latching mechanisms and gasket seals:
Heavy-duty latches are often used to ensure the cooler’s lid stays securely closed. These latches help create an airtight seal, preventing air and heat from infiltrating and compromising ice retention.
Some premium coolers feature gasket seals made from materials like rubber or silicone around the cooler lid. These seals are essential in creating a tight, waterproof seal, further enhancing the cooler’s ability to keep contents cold for extended periods.
The combination of latches and seals provides a strong, secure closure that helps preserve the cooler’s internal temperature.
For coolers that are often used outdoors, UV inhibitors and fade-resistant pigments are essential in ensuring the cooler’s durability and aesthetic appeal over time:
- UV Inhibitors: UV rays from the sun can cause plastics to degrade, weakening the material and compromising its structural integrity. To counter this, many coolers are made with UV inhibitors integrated into the plastic. This helps protect the cooler from sun damage and ensures it lasts longer in outdoor environments.
- Fade-Resistant Pigments: Outdoor use can cause colors to fade, especially under constant exposure to the sun. Coolers are often made with fade-resistant pigments that keep the cooler looking new for longer, making them an excellent investment for regular outdoor use. These pigments help maintain the cooler’s visual appeal, even after exposure to harsh conditions.
7. Quality Control and Testing
To ensure cooler boxes deliver on their promises of durability, performance, and efficiency, manufacturers employ a rigorous series of quality control and testing protocols. These tests are critical for verifying that the coolers meet industry standards and can withstand real-world use. Let’s break down some of the common tests and benchmarks.
7.1 Leak Testing and Pressure Testing
A fundamental aspect of cooler quality control is leak testing. Ensuring that coolers remain airtight is essential for ice retention and preventing any unintended water loss.
- Leak Testing:
- Manufacturers use various methods to test the cooler’s airtight seals. Common techniques include water immersion tests or using pressurized air to detect leaks. Any gaps or weaknesses in the seal are addressed before the cooler is sent to market.
- Pressure Testing:
- In addition to testing for leaks, coolers undergo pressure testing to check that they can withstand external pressures without compromising their integrity. This is particularly important for coolers used in more rugged conditions, such as marine environments or high-altitude activities.
7.2 Ice Retention Benchmarking
Ice retention is one of the most critical performance metrics for cooler boxes, and rigorous testing is used to assess how long a cooler can keep ice intact under different conditions. These tests are conducted in both controlled lab environments and in real-world scenarios.
- Lab Testing
In the lab, coolers are often tested under ideal conditions, where temperature and humidity can be precisely controlled. The cooler is filled with ice, and the time it takes for the ice to melt is recorded. This provides a standardized measure of performance.
- Real-World Testing
To better reflect actual use, real-world testing also takes place. For instance, coolers might be exposed to extreme outdoor conditions, such as direct sunlight, high temperatures, or being placed in a hot vehicle. These tests give more practical insights into how a cooler will perform in everyday settings.
7.3 Durability Tests
To ensure that coolers can endure the rigors of outdoor use, manufacturers perform a series of durability tests that simulate real-world abuse.
- Drop Tests:
Drop tests are conducted by repeatedly dropping the cooler from a specified height to simulate rough handling. This helps determine how well the cooler’s shell and seals hold up to impacts. The goal is to ensure that the cooler remains functional and intact after drops, especially when it is full or when it experiences heavy outdoor use.
- Hinge Cycle Tests:
The hinges and latches are crucial for the cooler’s longevity and ease of use. Hinge cycle tests involve opening and closing the cooler’s lid thousands of times to ensure that the hinges remain intact and that the lid continues to operate smoothly without failure.
- Lid Strength:
The lid strength test ensures that the cooler’s lid can withstand pressure without bending or breaking. This is especially important for coolers used in transporting heavy objects or those that might be exposed to weight or stacking. Ensuring the lid’s durability is key to maintaining the cooler’s performance over time.
8. Environmental and Manufacturing Considerations
As with many products, the manufacturing of cooler boxes comes with its own set of environmental and sustainability challenges. From the raw materials used to the energy required for production, manufacturers are increasingly being called upon to adopt greener practices. Here’s a look at some of the critical environmental and manufacturing considerations in cooler production.
8.1 Waste Management and Plastic Recycling
Plastic is one of the primary materials used in cooler manufacturing, but it also presents a significant environmental challenge when it comes to waste.
- Waste Management:
In cooler production, plastic waste is generated in the form of excess plastic, flashings, and scrap material. Many manufacturers have adopted closed-loop systems that allow for the recycling of these materials, ensuring that the waste doesn’t end up in landfills. This recycling process not only helps reduce waste but also reduces the need for virgin plastic.
- Plastic Recycling:
The recycling of plastic in the cooler industry has gained momentum in recent years. Many companies are now using recycled HDPE (High-Density Polyethylene) for manufacturing rotomolded coolers, reducing their dependence on newly produced plastics. Furthermore, cooler manufacturers are working towards recycling entire units when they reach the end of their life cycle, contributing to a circular economy.
8.2 Energy Consumption in Rotomolding vs. Injection Molding
The energy requirements for the production of coolers vary significantly between rotomolding and injection molding processes. Both methods have unique environmental impacts.
Rotomolding is an energy-intensive process, particularly due to the slow heating and rotation required to melt and mold the plastic. The cooling phase also takes longer compared to injection molding. While the process is highly effective for creating durable and well-insulated coolers, its energy consumption is relatively high compared to other manufacturing processes. Companies can mitigate this by using more energy-efficient equipment and optimizing their heating and cooling cycles.
Injection molding typically consumes less energy than rotomolding due to its faster production times and the high-pressure injection of molten plastic into molds. The process is more automated, requiring less time and labor, which makes it more energy-efficient overall. However, the trade-off is that injection molding often uses stronger molds, which need to be produced at a higher cost, and the resulting coolers tend to be lighter but less rugged than those made via rotomolding.
8.3 Innovations: Recycled Plastics and Biodegradable Insulation
As demand for sustainable products grows, cooler manufacturers are looking for innovative solutions to reduce their environmental footprint. Two key areas of innovation in cooler production are the use of recycled plastics and biodegradable insulation materials.
A growing trend is the incorporation of recycled plastics in cooler production. Not only does this help reduce plastic waste, but it also minimizes the environmental impact of producing new plastic. By utilizing post-consumer recycled (PCR) plastics in the construction of cooler shells, manufacturers can reduce their reliance on virgin plastic and reduce their carbon footprint.
Another innovation is the development of biodegradable insulation materials. Traditionally, polyurethane foam has been the go-to material for insulation, but its environmental impact at the end of its life is significant. Manufacturers are now exploring alternatives, such as biodegradable foams made from plant-based materials. These new insulation options offer similar thermal performance to polyurethane while being more eco-friendly.
9. Choosing the Right Cooler Box for Your Needs
Selecting the right cooler box can make a huge difference in ensuring that your food and drinks stay fresh and cool during your outdoor adventures or for everyday use. With various types of coolers designed for different purposes, it’s essential to consider factors like use case, size, capacity, and the balance between weight and durability.
9.1 Comparing Cooler Types by Use Case
Cooler boxes come in a variety of designs, each tailored to specific needs. Here’s how they stack up across different use cases:
- Camping: For camping trips, you’ll need a cooler with excellent ice retention capabilities and durability to withstand outdoor conditions. Rotomolded coolers are ideal for this because of their superior insulation and rugged construction. These coolers can retain ice for several days, making them perfect for extended camping trips.
- Fishing: A fishing cooler requires great ice retention for keeping catch fresh, as well as durability to handle rough terrain and potential saltwater exposure. Many coolers designed for fishing include added features like fish rulers, bait storage compartments, and drain plugs for easy cleaning. Rotomolded coolers, with their sturdiness and ability to handle extreme conditions, are the preferred choice.
- Picnics: For short, casual outings like picnics, a lightweight cooler with adequate cooling performance is usually sufficient. Injection molded coolers are a great choice here, as they offer a balance of portability and efficient insulation. These coolers are typically more affordable and easier to carry around without sacrificing much in terms of ice retention.
- Delivery: Coolers used for delivery, especially for food and beverages, require an emphasis on temperature control and ease of access. These coolers often feature dual-wall construction for better insulation and are typically equipped with airtight seals to maintain the contents’ freshness. Insulated boxes used for delivery services are commonly injection molded for efficient and cost-effective mass production.
9.2 Size and Capacity Considerations
Choosing the right size and capacity of your cooler box is crucial, as it directly affects both performance and convenience. Here’s what to keep in mind:
Consider how much food or drink you need to store and for how long. A small cooler may suffice for a day trip or a picnic, but larger coolers are better suited for camping or extended fishing trips. Too large a cooler can be unnecessarily heavy and cumbersome, while a too-small cooler won’t hold enough to meet your needs.
Cooler capacity is typically measured in quarts or liters. A 20-30 quart cooler is typically enough for a small group, while 50-70 quarts are better for larger gatherings. For longer trips, a 100-quart or more cooler may be necessary. Be sure to account for the number of people, the length of your trip, and how much you need to store.
9.3 Weight vs. Durability Trade-Offs
When choosing a cooler box, you’ll inevitably need to balance weight and durability. Here’s what to consider:
- Weight: Injection molded coolers tend to be lighter because they use less material in the production process. These are ideal for those who need portability, such as for casual picnics or short trips. However, lighter coolers may not provide the same level of durability and can be more prone to damage under rough conditions.
- Durability: Rotomolded coolers are much heavier due to their thicker walls and more robust construction. While they may be harder to carry, they offer superior durability and ice retention. If your cooler needs to endure harsh conditions or extended outdoor use, the added weight is a worthwhile trade-off.
At KingStar, we take pride in our expertise in both rotomolding and injection molding techniques, ensuring high-quality and customizable coolers that meet your specific needs. Whether you need OEM or ODM solutions, we offer factory-direct pricing with strict quality assurance processes. Our global supply capacity and years of experience in the industry make us a reliable partner for durable, high-performance coolers at competitive prices.
If you’re looking for a trusted manufacturer to supply high-quality coolers tailored to your requirements, KingStar is here to help. Contact us today for cost-effective and customizable cooler solutions that meet your exact specifications. Leave an online message or send email to sales@kingstarmold.com, you will get reply within 24 hours.