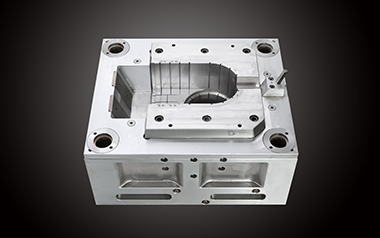
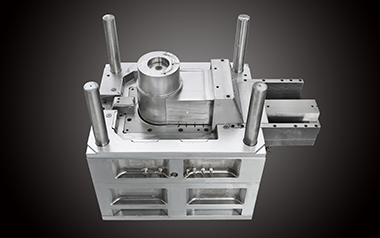
Plastic Injection Molding for Home Appliances
KingStar Mold’s Injection Molding Services
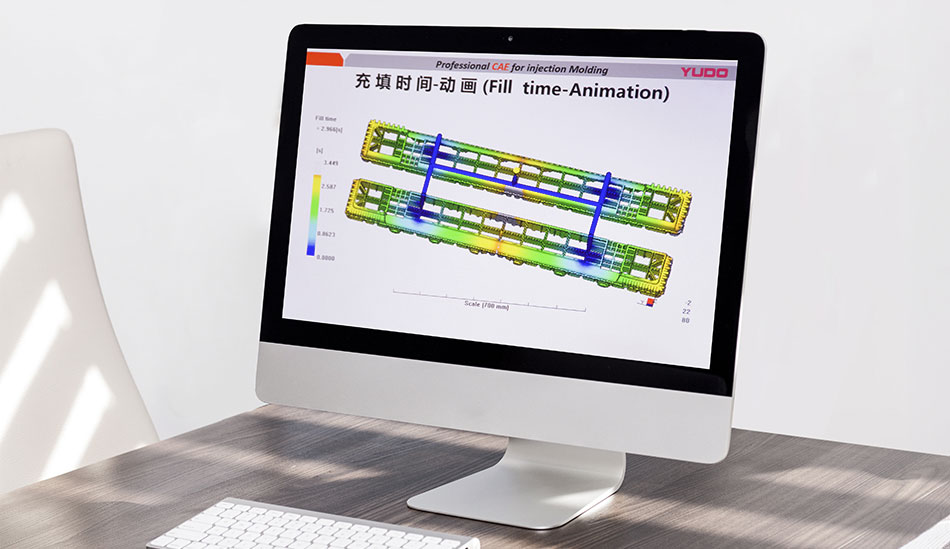
CAD Engineering
KingStar Mold offers advanced CAD engineering services to create precise 3D models and prototypes for home appliances. Our team utilizes cutting-edge CAD software to design and optimize components for enhanced performance and manufacturability.
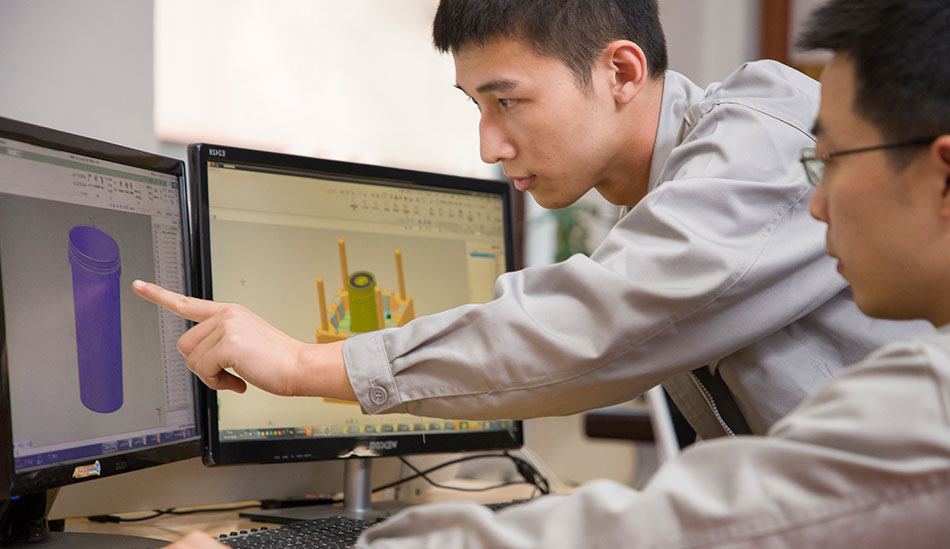
Mold Flow Analysis
Our mold flow analysis service simulates the injection molding process to identify potential defects and optimize design efficiency. By using state-of-the-art mold flow analysis, we ensure the perfect distribution of materials and prevent issues like warping and air pockets.
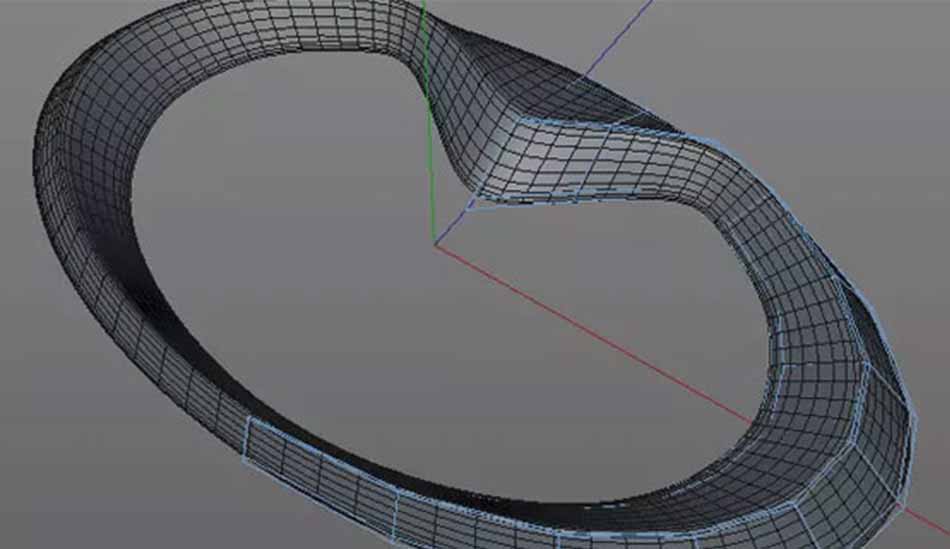
3D Printing
We use 3D printing technology to rapidly prototype and test home appliance components before full-scale production. 3D printing allows for high-precision, complex designs, accelerating the development of home appliance components with reduced lead times.
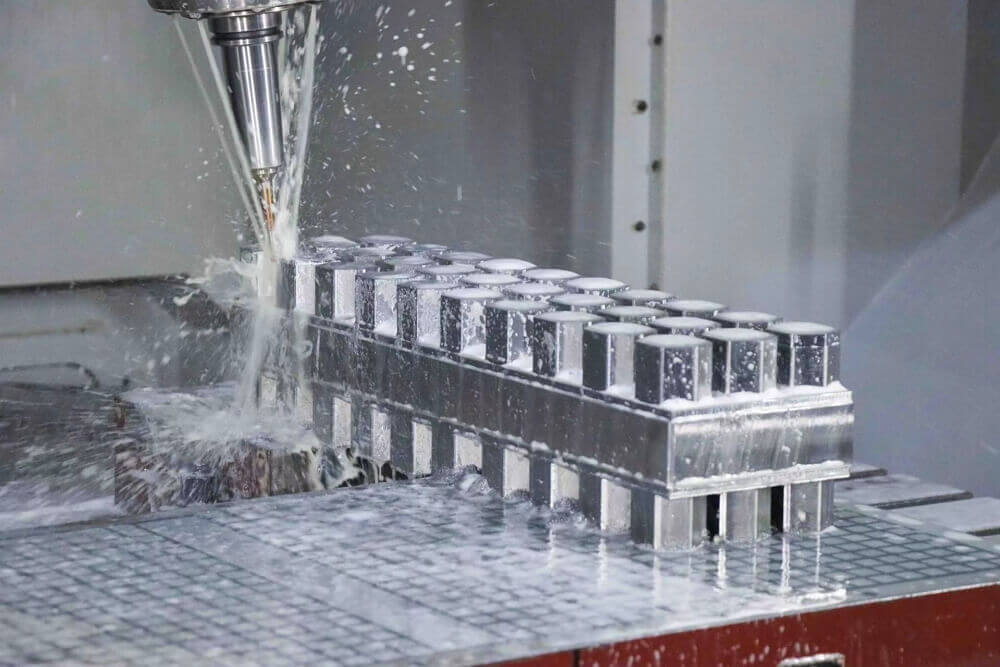
CNC Machining
KingStar Mold provides CNC machining services that produce high-precision, complex home appliance components with tight tolerances. Our CNC machining capabilities ensure consistent quality and efficient production of metal and plastic components for the home appliance industry.
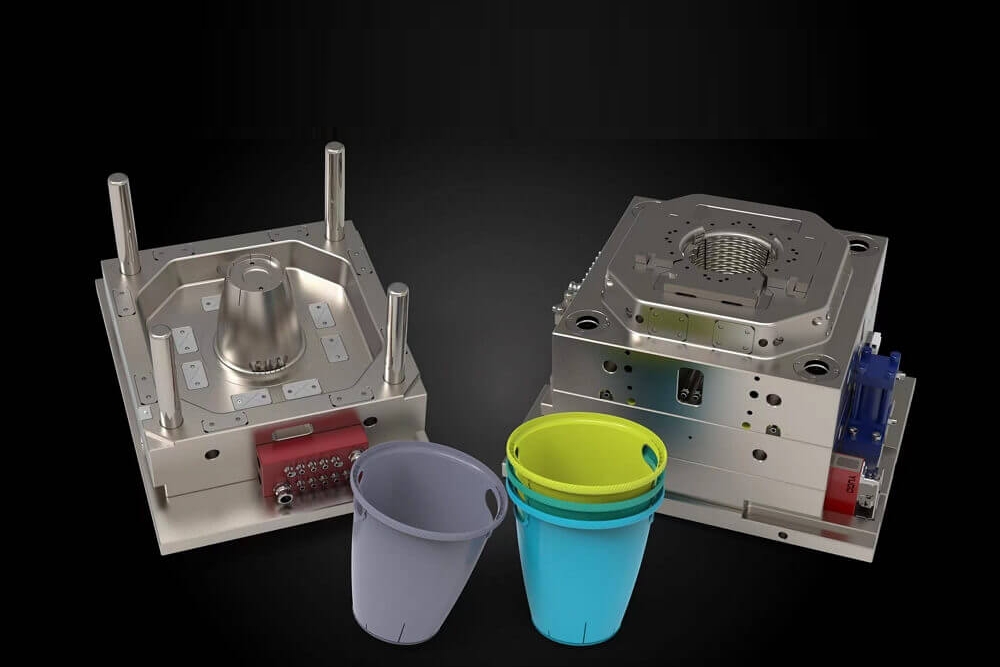
Injection Molding
Our injection molding services allow for the mass production of high-quality home appliance parts with complex shapes and fine details. We specialize in delivering fast and cost-effective solutions for producing durable, high-volume automotive components.

Surface Finishing & Assembly
We offer a range of surface finishing services, including polishing, coating, and more, to enhance the performance of home appliance parts. Our assembly services ensure that all components are accurately assembled and ready for integration into the final product design.
Orders Workflow
Initial Consultation & Design Review
We begin by discussing your project’s goals and reviewing the design to ensure it’s optimized for the specific manufacturing process. At this stage, we suggest improvements or adjustments to enhance efficiency, functionality, and manufacturability.
Material Selection
Our experts assist in selecting the right materials for your product based on performance requirements and compatibility with the manufacturing process. The correct material choice ensures durability, cost-effectiveness, and the desired product functionality.
Design & Engineering
Using advanced CAD and simulation tools, we develop a custom design for your project. This step ensures precise details and identifies potential challenges early in the process, optimizing the design for efficient manufacturing.
Prototyping & Sample Testing
A prototype or sample is created to verify design accuracy, functionality, and performance. Rigorous testing is conducted to ensure the product meets your specifications before moving into full-scale production.
Production Setup & Initial Production
We set up the required machines, molds, or tools for the manufacturing process. The initial production run is performed to confirm the setup, assess quality, and fine-tune settings for optimal results.
Final Production & Quality Control
After final approval, we proceed with full-scale production, ensuring continuous quality checks. Comprehensive inspections at each stage ensure that every part meets the highest standards before delivery.
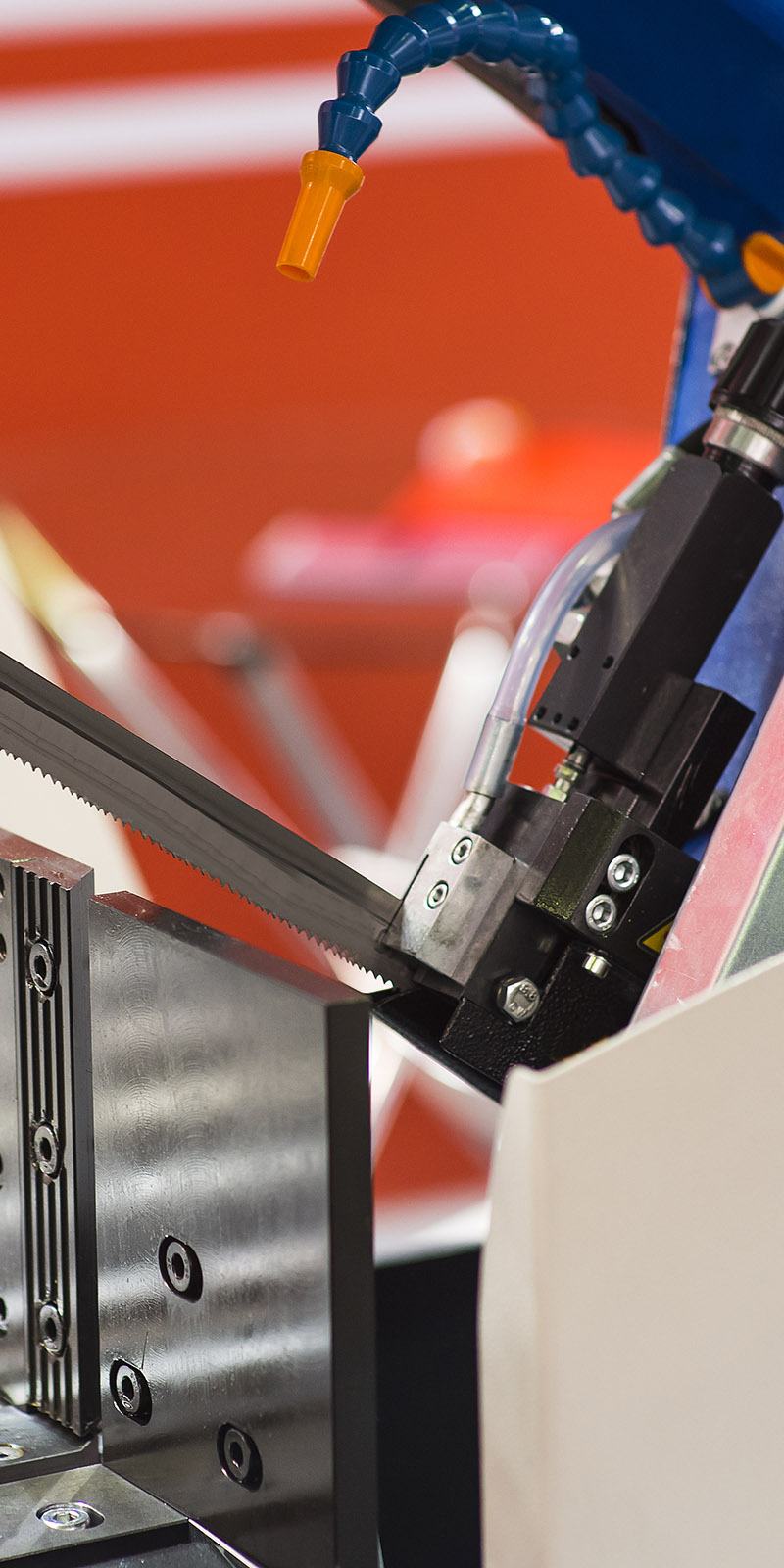
Why Choose Us
We Believe You Will Choose Us Again
Only companies with extensive market experience and a deep understanding of customer needs can offer the best service.
Skilled
High-precision production equipment, skilled production staff, and guaranteed delivery times.
Experienced
Over ten years of industry experience, with a mature quotation system and technical support.
Thoughtful
Customized processing options that save time and effort, with active support throughout pre-sales and post-sales.
Equipped
Engineers review designs to identify and resolve potential issues, backed by advanced testing equipment.
Why Choose Injection Molding For Home Appliances Manufacturing?
One key benefit of our injection molding technology is the rapid production of prototypes. By utilizing both 3D printers and CNC machines, we ensure your home appliance prototypes are created in the shortest time frame possible.
We take pride in being able to produce over 600 set molds in a year. This has garnered us a reputation for being able to fulfill any order, no matter how big it is. No matter how large the scale of the order, we are more than capable of fulfilling it.
KingStar Mold always adheres to a high standard of control. We follow the strictest quality control, and any plastic parts that we distribute, are tested by our specialized team of experts. Rest assured, any product you get from KingStar Mold is of the best quality possible.
By utilizing injection molding for your home appliances, you are assured that you will be saving money. Just one injection mold could be used to create a myriad of parts. This means that you will save on both material and production costs.
With over a decade of experience in plastic injection molding, KingStar Mold has refined and streamlined its processes to deliver exceptional results. Our extensive industry expertise allows us to provide unparalleled solutions. Here are some key applications we have mastered over the years.
Electrical box molds are designed to enclose and protect electrical components, preventing damage and theft. Using our advanced injection technology, we can customize electrical box molds to match your specific design requirements.
Electrical Box
Refrigerator
Washing Machine
Air Conditioner
Hair Dryer
Telephone Case
Previous Injection Molded Home Appliance Projects

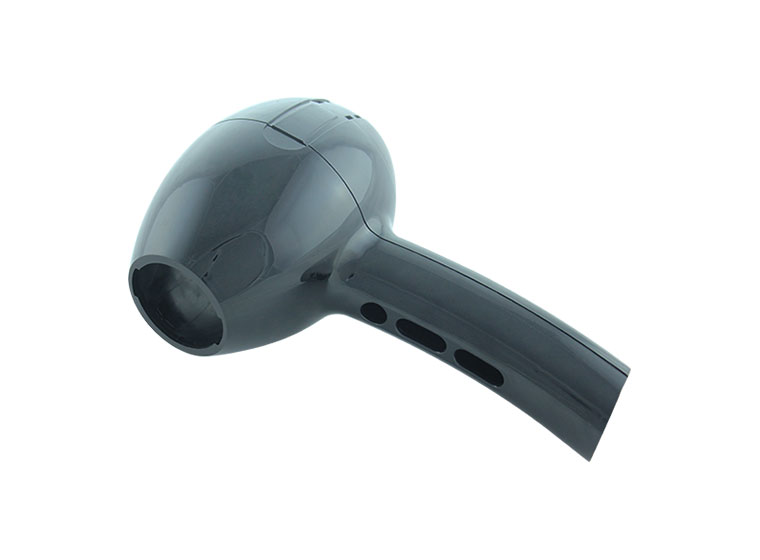
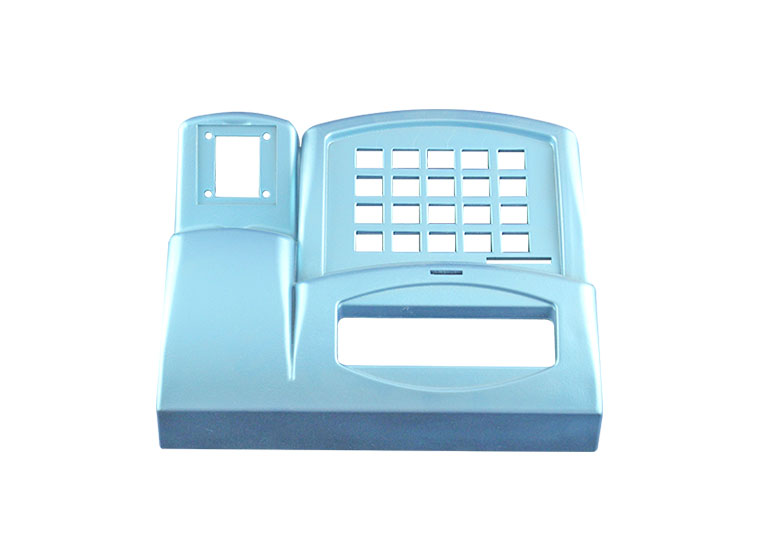
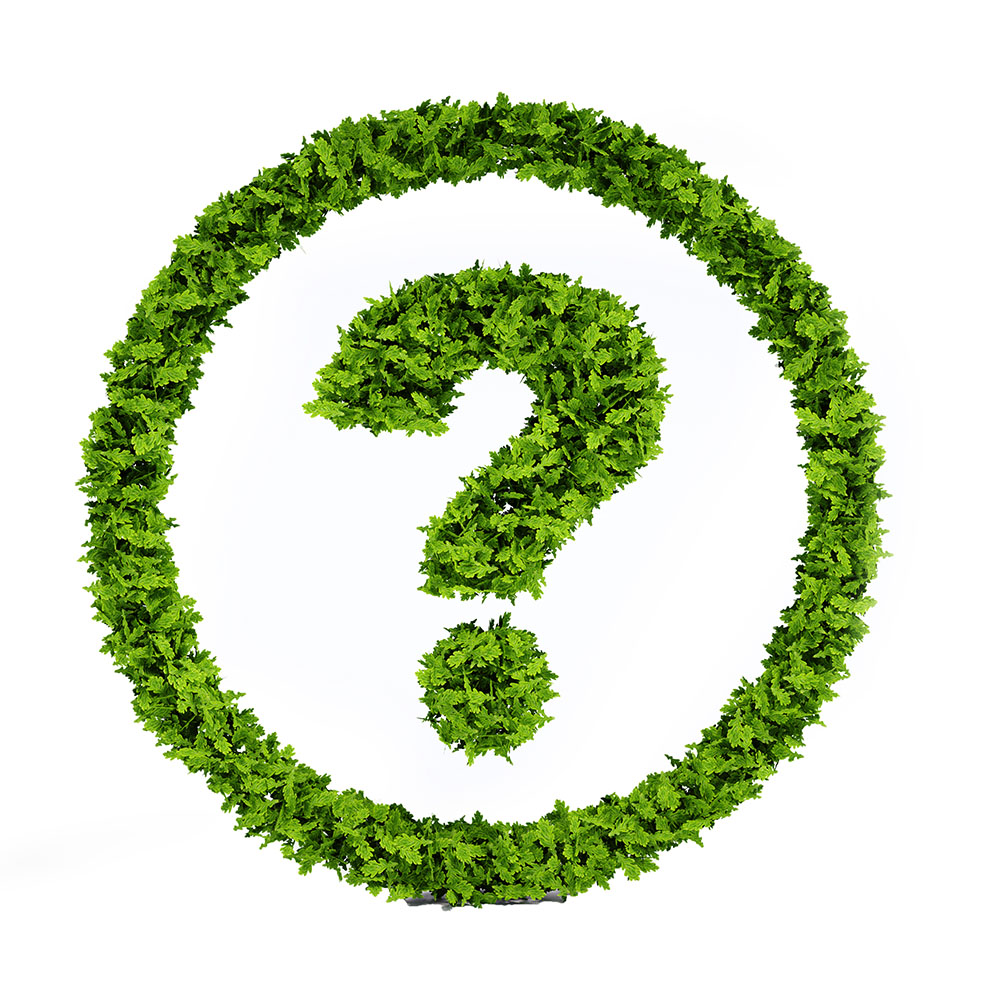
Yes, we provide secure packaging solutions, including plastic bags, cardboard boxes, and wooden crates, to ensure safe delivery of your products.
Yes, our products comply with international safety and performance standards and are TUV Certified for quality assurance.
Yes, we can manage both small-batch orders and large-scale production, offering flexibility to accommodate varying project sizes.
Our minimum order quantity is 2 pieces, ideal for prototype testing or small batch production.
Yes, we provide custom design services and prototypes tailored to meet the specific needs of your home appliance products.
We use high-quality materials such as ABS, POM, PP, and PVC to ensure durability and optimal performance.
We accept both 2D (PDF/CAD) and 3D (IGES/STEP) files for accurate design communication and prototyping.
Yes, KingStar Mold specializes in both plastic injection molding and CNC machining for metal parts, catering to all home appliance manufacturing needs.
KingStar Mold provides manufacturing solutions for various industries, including consumer electronics, automotive, and home appliances.
We implement strict quality control procedures, including material inspection, in-process testing, and final product evaluation, to ensure high standards.
Yes, KingStar Mold specializes in custom design, prototyping, and manufacturing, offering end-to-end solutions for home appliance parts.
Production lead times vary depending on the complexity of the project but typically range from 2 to 6 weeks.