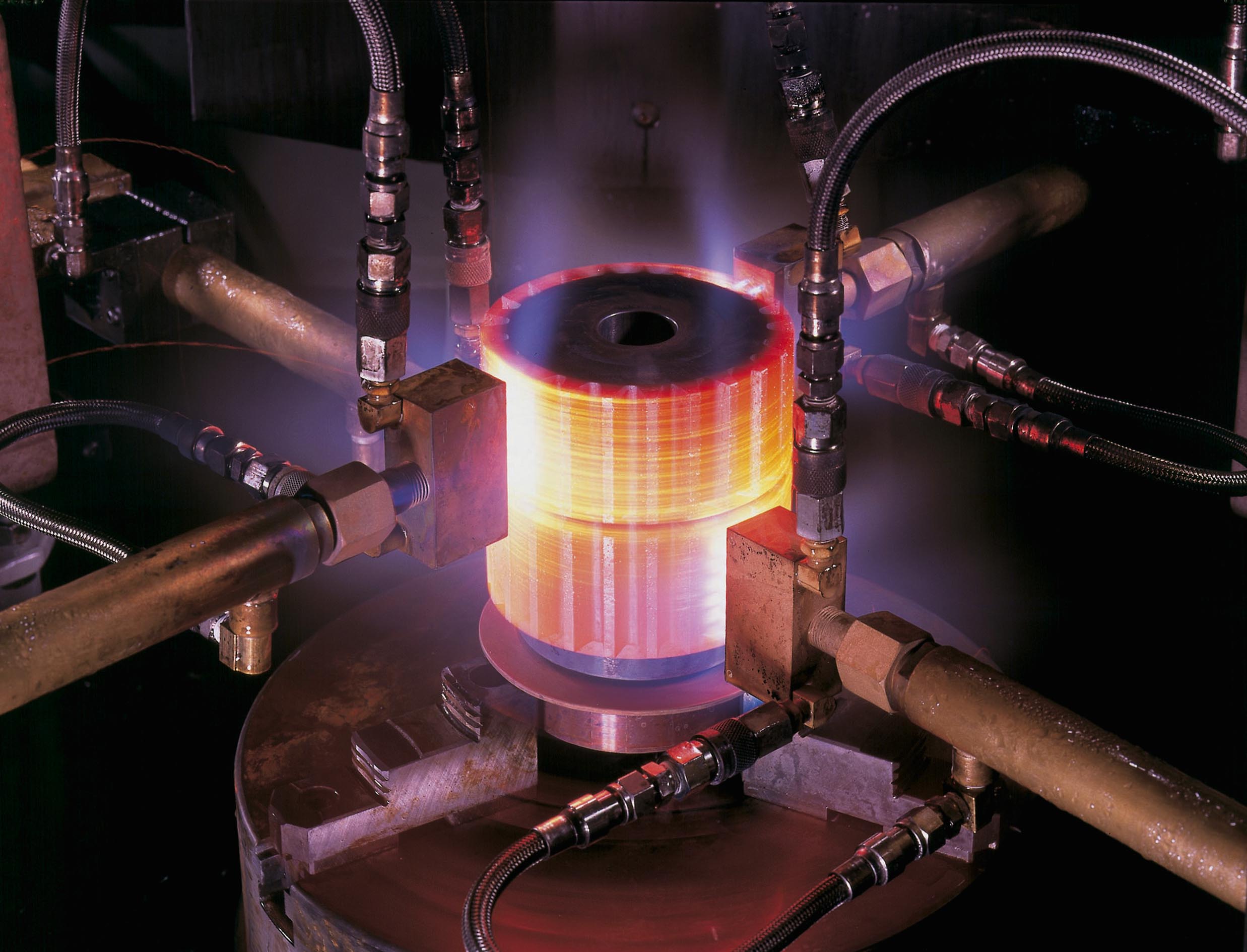
What Is Heat Treatment Finish?
Heat treatment is a precision-controlled thermal process used to alter the internal structure and surface properties of metal components. While traditional methods like annealing, tempering, and normalizing focus on internal strength, ductility, and stress relief, many industrial applications require surface-specific enhancements. That’s where advanced heat surface treatment services like carburizing, nitriding, carbonitriding, and induction hardening come in—each engineered to strengthen the surface without compromising core properties, improving wear resistance, fatigue strength, and dimensional stability.
Unlike general heat treatment that treats the entire part uniformly, surface-focused processes are more targeted. Techniques such as flame hardening or ferritic nitrocarburizing selectively harden the outer layer, while cryogenic treatment and vacuum heat treating refine microstructures with minimal distortion or oxidation. These specialized services are critical for components like gears, shafts, and high-precision tools—anywhere high-performance surfaces are required without sacrificing the part’s integrity.
Manufacturing Gallery
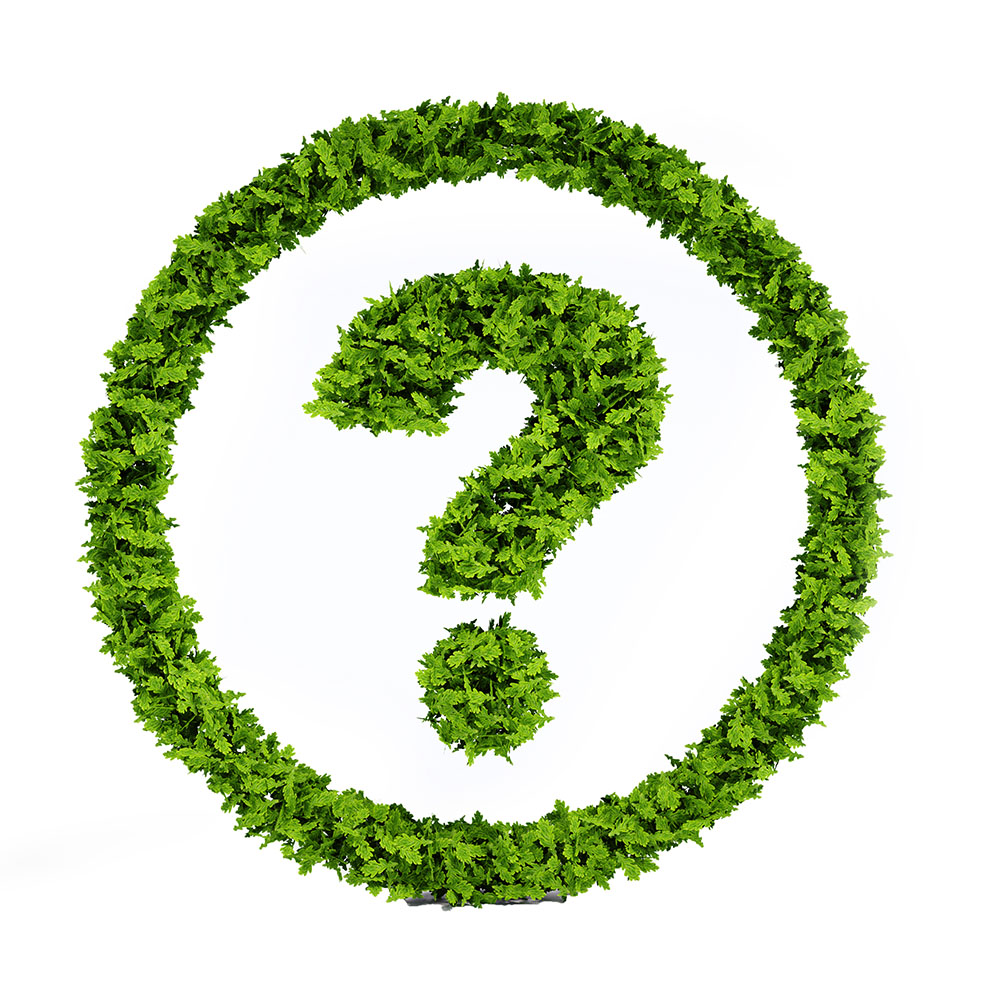
Frequently Asked Questions
Yes—KingStar Mold supports both low-volume prototyping and high-volume production, including integrated heat treatment services. Whether you need a single test piece or thousands of finished parts, we ensure consistent quality through every stage, from DFM analysis to surface hardening and final assembly.
KingStar Mold not only provides advanced surface-focused heat treatment solutions, but also delivers complete end-to-end manufacturing support. Our services go beyond heat treatment to include design review (DFM), material selection, sheet metal fabrication, CNC machining, post-processing, assembly, OEM/ODM services and global logistics. With strict process control, fast turnaround times, and expert technical support, we ensure every part meets both surface and structural performance requirements—seamlessly integrated from concept to delivery.
Yes—KingStar Mold’s experienced engineering team will evaluate your part geometry, base material, and performance requirements to recommend the most suitable heat treatment process to optimize surface durability and cost-efficiency.