KingStar Mold’s Injection Molding Services
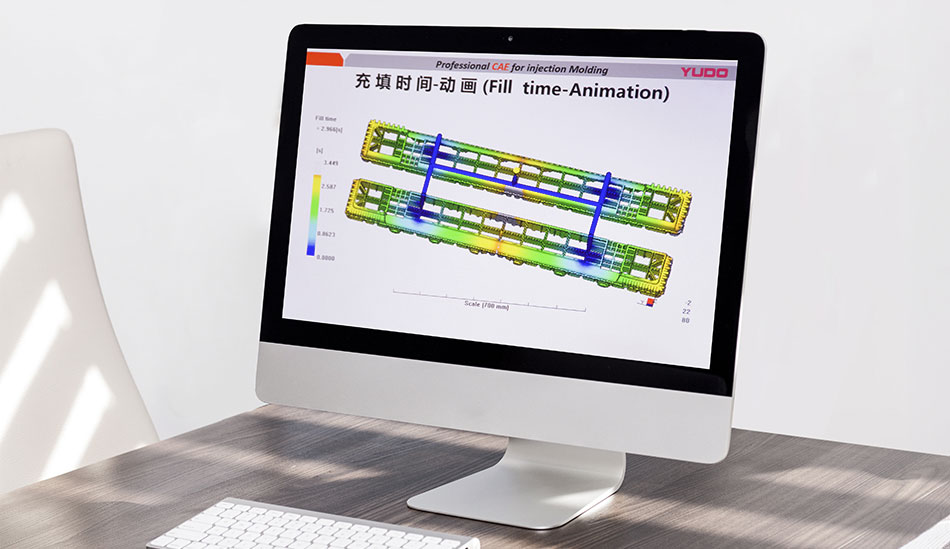
CAD Engineering
KingStar Mold offers advanced CAD engineering services to create precise 3D models and prototypes for hardware components. Our team utilizes cutting-edge CAD software to design and optimize components for enhanced performance and manufacturability.
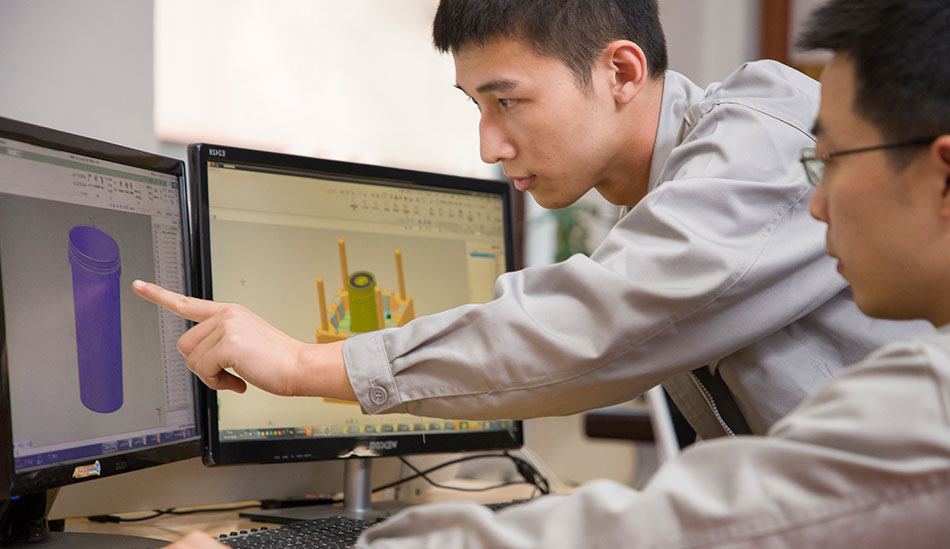
Mold Flow Analysis
Our mold flow analysis service simulates the injection molding process to identify potential defects and optimize design efficiency. By using state-of-the-art mold flow analysis, we ensure the perfect distribution of materials and prevent issues like warping and air pockets.
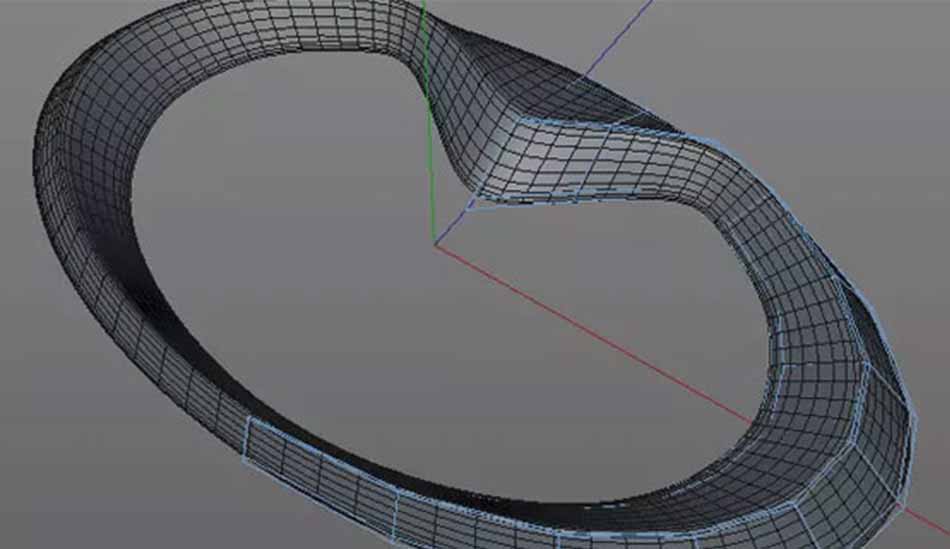
3D Printing
We use 3D printing technology to rapidly prototype and test mold parts before full-scale production. 3D printing allows for high-precision, complex designs, accelerating the development of hardware components with reduced lead times.
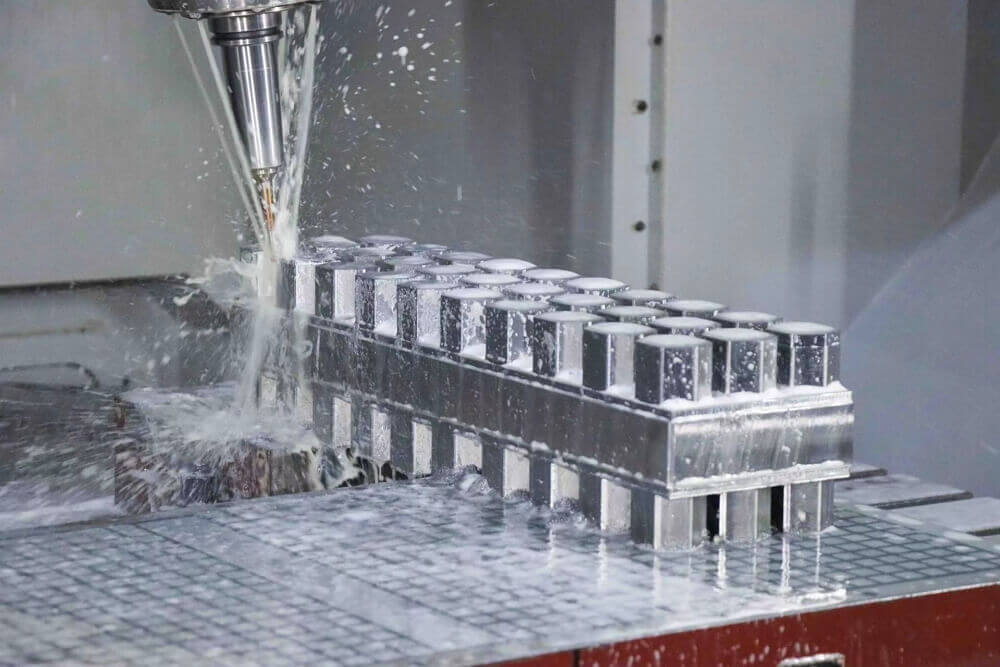
CNC Machining
KingStar Mold provides CNC machining services that produce high-precision, complex hardware parts with tight tolerances. Our CNC machining capabilities ensure consistent quality and efficient production of metal components for the architectural industry.
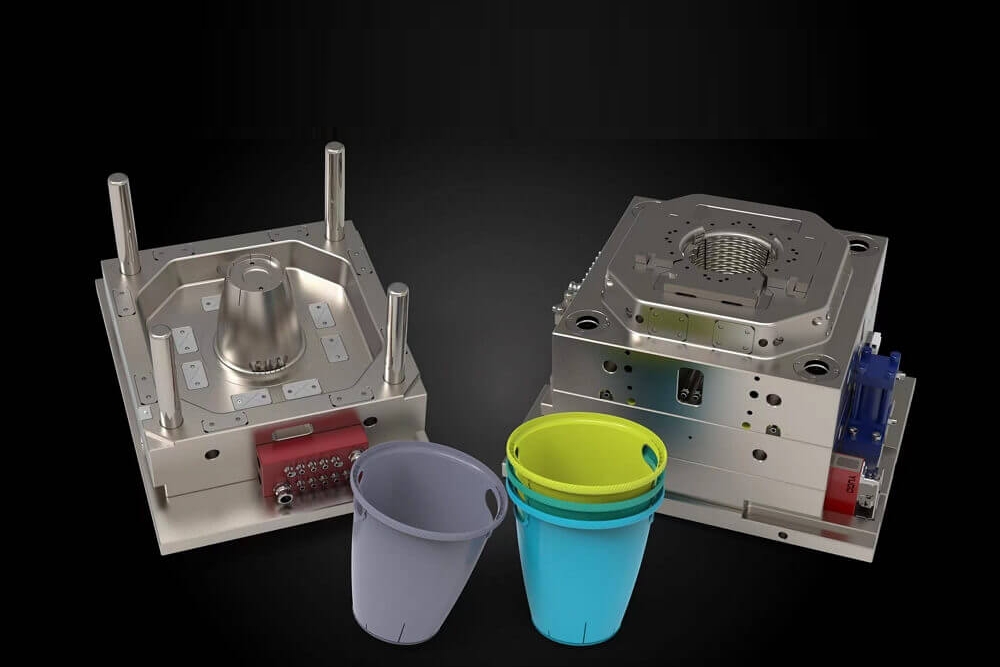
Injection Molding
Our injection molding services allow for the mass production of high-quality plastic mould parts and cnc-machined metal parts with complex shapes and fine details. We specialize in delivering fast and cost-effective solutions for producing durable, high-volume metal components for architectures.

Surface Finishing & Assembly
We offer a range of surface finishing services, including polishing, coating, and more, to enhance the performance of mold and cnc-machined parts. Our assembly services ensure that all components are accurately assembled and ready for integration into the final product design.
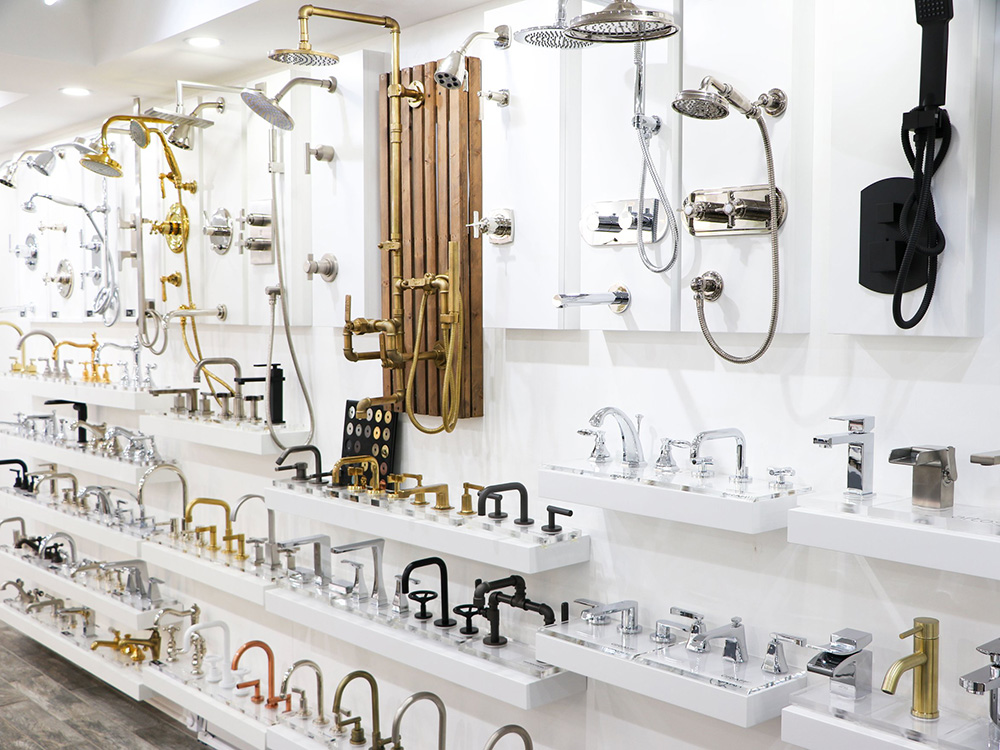
Custom Hardware Components Expertise
At KingStar Mold, our team of experts is dedicated to delivering high-quality services, including product design, mold design, injection molding, CNC machining, and other advanced manufacturing techniques. We provide a comprehensive, one-stop solution for all your hardware component needs, offering both plastic molds and precision metal CNC-machined parts.
We specialize in a variety of custom solutions for hardware products, including:
Orders Workflow
Initial Consultation & Design Review
We begin by discussing your project’s goals and reviewing the design to ensure it’s optimized for the specific manufacturing process. At this stage, we suggest improvements or adjustments to enhance efficiency, functionality, and manufacturability.
Material Selection
Our experts assist in selecting the right materials for your product based on performance requirements and compatibility with the manufacturing process. The correct material choice ensures durability, cost-effectiveness, and the desired product functionality.
Design & Engineering
Using advanced CAD and simulation tools, we develop a custom design for your project. This step ensures precise details and identifies potential challenges early in the process, optimizing the design for efficient manufacturing.
Prototyping & Sample Testing
A prototype or sample is created to verify design accuracy, functionality, and performance. Rigorous testing is conducted to ensure the product meets your specifications before moving into full-scale production.
Production Setup & Initial Production
We set up the required machines, molds, or tools for the manufacturing process. The initial production run is performed to confirm the setup, assess quality, and fine-tune settings for optimal results.
Final Production & Quality Control
After final approval, we proceed with full-scale production, ensuring continuous quality checks. Comprehensive inspections at each stage ensure that every part meets the highest standards before delivery.
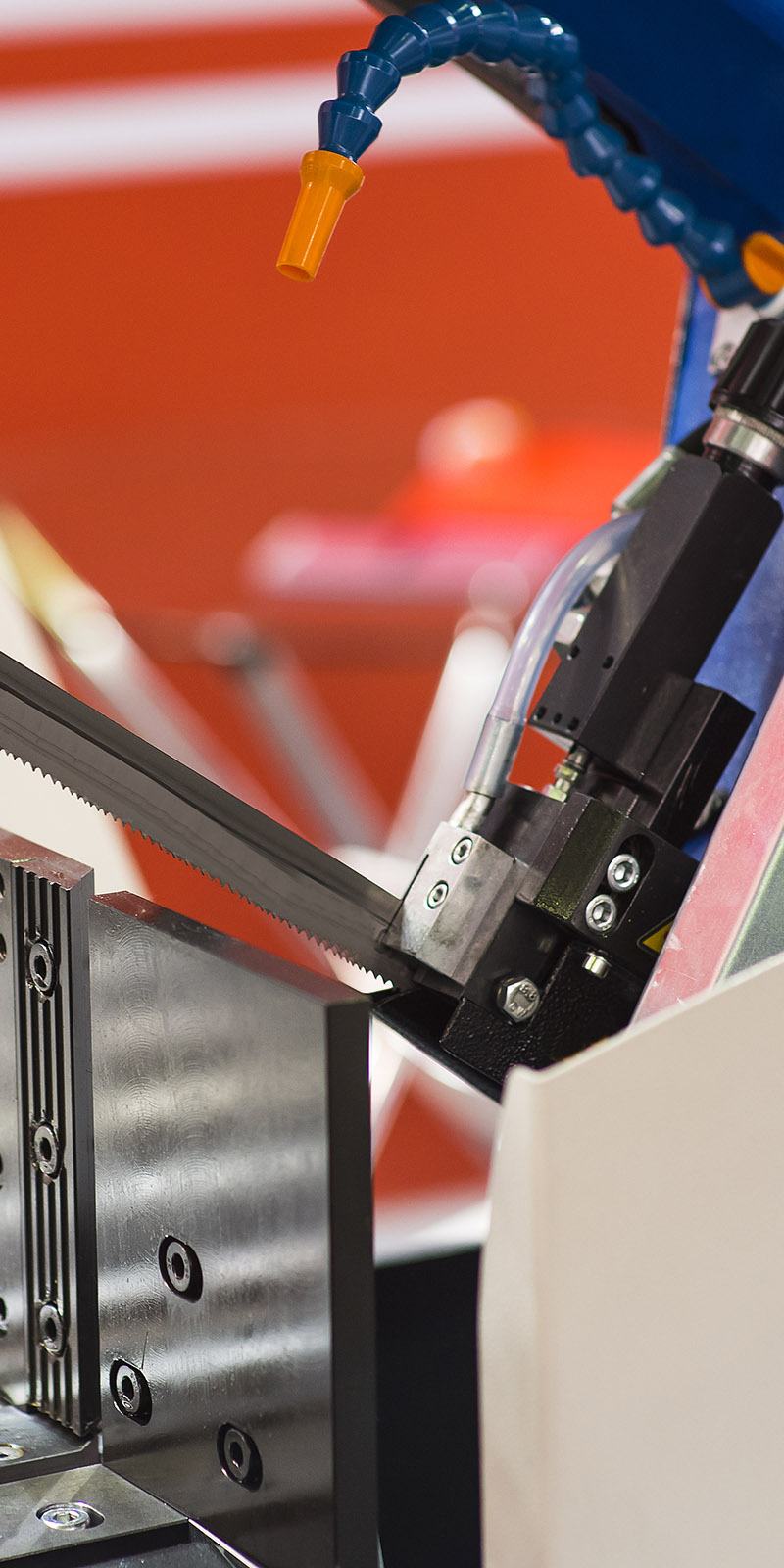
Why Choose Us
We Believe You Will Choose Us Again
Only companies with extensive market experience and a deep understanding of customer needs can offer the best service.
Skilled
High-precision production equipment, skilled production staff, and guaranteed delivery times.
Experienced
Over ten years of industry experience, with a mature quotation system and technical support.
Thoughtful
Customized processing options that save time and effort, with active support throughout pre-sales and post-sales.
Equipped
Engineers review designs to identify and resolve potential issues, backed by advanced testing equipment.
Why Choose Injection Molding and CNC Machining For Hardware Manufacturing?
Injection molding and CNC machining offer exceptional precision, ensuring every hardware component meets strict design specifications and high tolerances.
Both processes support a wide range of materials, from durable plastics to metals, providing flexibility for various hardware applications.
Injection molding allows for complex shapes, while CNC machining provides fine detail and the ability to create intricate features for customized hardware components.
Injection molding is highly efficient for mass production, while CNC machining optimizes cost-efficiency for both small and large batches of hardware parts.
Recommended Materials for Hardware Manufacturing
Plastic Materials | Description | Metal Materials | Description |
---|---|---|---|
ABS | Durable, impact-resistant, and easy to mold, ideal for consumer electronics and automotive parts. | Aluminum | Lightweight, corrosion-resistant, and strong, used for high-performance hardware and enclosures. |
PA (Nylon) | Excellent strength, wear resistance, and low friction properties, commonly used in mechanical parts. | Steel (Stainless) | High strength, corrosion-resistant, suitable for industrial components and structural parts. |
PBT | High thermal stability, great for electronic and automotive parts. | Copper | Excellent electrical conductivity, commonly used for connectors and electrical parts. |
PC | Strong, transparent, and heat-resistant, perfect for electrical enclosures. | Brass | Corrosion-resistant and ideal for hardware that requires excellent machinability and appearance. |
PP | Lightweight and resistant to chemicals, used for automotive and home appliance parts. | Titanium | Strong, lightweight, and resistant to corrosion, used for aerospace and high-performance components. |
PTFE | Non-stick and high thermal resistance, excellent for seals and gaskets. | Zinc Alloy | Cost-effective, durable, and suitable for die-casting in hardware products. |
With more than 10 years of experience as a hardware components manufacturer and injection mold expert, KingStar Mold has developed molds and cnc-machined parts for a wide variety of types.
Made from durable stainless steel or brass, our butt hinges are designed for strength and smooth operation. They provide reliable performance for doors and cabinets, ensuring longevity and ease of use. The materials offer resistance to wear, making them ideal for both residential and commercial applications.
Our cabinet handles are available in zinc alloy, stainless steel, or brass for a mix of durability and aesthetic appeal. These materials ensure resistance to wear and corrosion, offering both style and functionality. The handles are designed to withstand daily use while maintaining a sleek, modern appearance.
Constructed from steel, stainless steel, or aluminum, our drawer slide rails are designed to provide smooth and stable movement. These materials ensure high load capacity and resistance to corrosion. Whether for residential or industrial use, our rails ensure longevity and reliable performance even under heavy loads.
Butt Hinges
Drawer Slide Rails
Made from stainless steel or zinc alloy, our friction hinges provide smooth and controlled movement. Ideal for applications requiring adjustable angles, they ensure long-lasting performance. These hinges are designed for precision, providing reliable motion control for windows, doors, and other adjustable fixtures.
Our marble brackets are crafted from stainless steel, zinc alloy, or aluminum, offering superior strength and corrosion resistance. These materials provide stability and support for heavy marble slabs. The brackets are designed to securely hold marble in place while complementing the elegance of stone surfaces.
We offer rust-resistant screws made from stainless steel, brass, or coated PVC for enhanced durability. These materials provide excellent corrosion resistance, ensuring long-lasting performance in various environments. Perfect for both indoor and outdoor use, they maintain their strength and appearance despite exposure to harsh conditions.
Friction Hinges
Marble Brackets
Rust-Resistant Screws
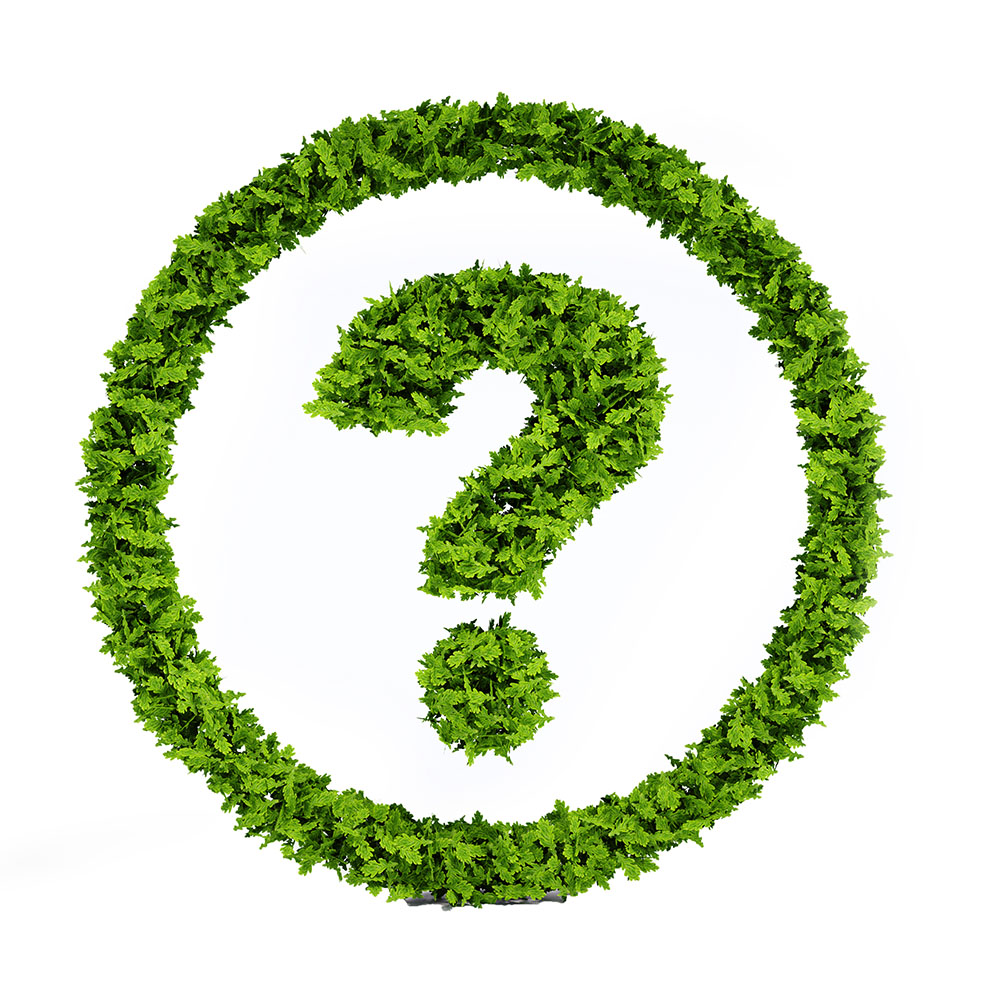
Yes, we specialize in both plastic injection molding and CNC machining of metal components, offering a full range of manufacturing solutions for your hardware products.
Yes, we offer rust-resistant options for many hardware components, particularly those made from stainless steel, brass, and coated materials, ensuring long-lasting durability in various environments.
The production timeline depends on the complexity and quantity of the order. Typically, it ranges from a few weeks to a couple of months, but we provide estimated delivery times upon request.
We serve various industries, including automotive, furniture, home appliances, electronics, and industrial equipment, providing precision hardware components for each.
Yes, we offer fully customizable solutions, allowing you to provide your specifications for product design, mold design, and manufacturing to meet your exact requirements.
We use a range of high-quality materials, including durable plastics such as PA, PBT, and POM, as well as metals like stainless steel, zinc alloy, and aluminum, ensuring the best fit for your hardware products.
Yes, our team offers design support, working closely with you to optimize product designs for manufacturability and functionality.
We implement strict quality control processes, including precision measurements, material testing, and visual inspections, to ensure that each hardware component meets high standards.
Yes, both injection molding and CNC machining techniques allow us to manufacture hardware components with intricate and complex geometries, providing customized solutions for your needs.
We offer various finishes, including matte, polished, anodized, and coated options to enhance the durability and appearance of your hardware components.
Yes, we specialize in both small and large production runs, offering flexibility to meet different project requirements with consistent quality.
Yes, we provide samples for approval before mass production to ensure that the final product meets your expectations in terms of design and functionality.