Every week we receive emails and phone calls from customers asking about Low-volume injection molding. Most of the questions are about mold material selection, production cycle, cost, etc. As a leading injection molding company, KingStar has organized the relevant questions into this post for buyers, design companies and other manufacturers in the industry to refer to.
Low-volume injection molding is transforming how businesses approach small batch production. Unlike traditional high-volume injection molding, which requires large quantities to be cost-effective, low-volume molding allows companies to produce small quantities of parts efficiently, with reduced tooling costs and shorter lead times. This makes it an attractive option for industries where flexibility and speed are essential.
The significance of low-volume injection molding lies in its ability to support the rapid production of functional parts, prototypes, or custom products with minimal upfront investment. With businesses constantly seeking faster time-to-market and the ability to adapt to changing needs, low-volume injection molding provides an ideal solution.
In recent years, this approach has gained traction in several sectors, including automotive, consumer electronics, and medical devices, where small batch production runs are common. By providing a cost-effective method for producing high-quality parts in smaller quantities, low-volume injection molding is enabling businesses to streamline their operations, reduce risks, and meet market demands more effectively.
As technology continues to advance, the accessibility and efficiency of low-volume injection molding make it an increasingly popular choice for companies looking to balance cost, speed, and quality in their production processes.
To better understand how low-volume injection molding compares to other production methods, here’s a quick look at the key differences in mold production, equipment requirements, lead times, and ideal applications across different production volumes.
Production Method | Low-Volume Injection Molding | Mid-Volume Injection Molding | High-Volume Injection Molding |
---|---|---|---|
Mold Production & Molding | In-house mold production and molding | Outsourced mold production and molding | Outsourced mold production and molding |
Required Equipment | 3D printer, desktop injection molding machine | CNC machine, injection molding machine | CNC machine, injection molding machine |
Mold Type | 3D printed polymer | Machined aluminum | Machined steel |
Mold Cost | Less than $100 | $2,000 – $5,000 | $10,000 – $100,000 |
Lead Time | 1-3 days | 3-4 weeks | 4-8 weeks |
Optimal Production Volume | Less than 500 | 500 – 10,000 | 5,000+ |
Typical Applications | Rapid prototyping, Custom injection molding, Short-run injection molding | Short-run injection molding | Mass production |
For more detailed illustration, please read on.
- 1. What is Low-Volume Injection Molding?
- 2. Advantages of Low-Volume Injection Molding
- 3. Ideal Applications for Low-Volume Injection Molding
- 4. How Low-Volume Injection Molding Works
- 5. Key Factors to Consider in Low-Volume Injection Molding
- 6. Optimizing the Low-Volume Injection Molding Process
- 7. Choosing the Right Injection Molding Partner for Low-Volume Production
- 8. Common Challenges and How to Overcome Them
- 9. Conclusion
1. What is Low-Volume Injection Molding?
Low-volume injection molding is a manufacturing process designed to produce small quantities of plastic parts quickly and cost-effectively. Unlike traditional injection molding, which is optimized for mass production, low-volume injection molding focuses on producing a limited number of parts — typically ranging from a few dozen to several thousand units. This approach allows businesses to avoid the high initial tooling costs associated with large-scale production, making it ideal for smaller batch runs.
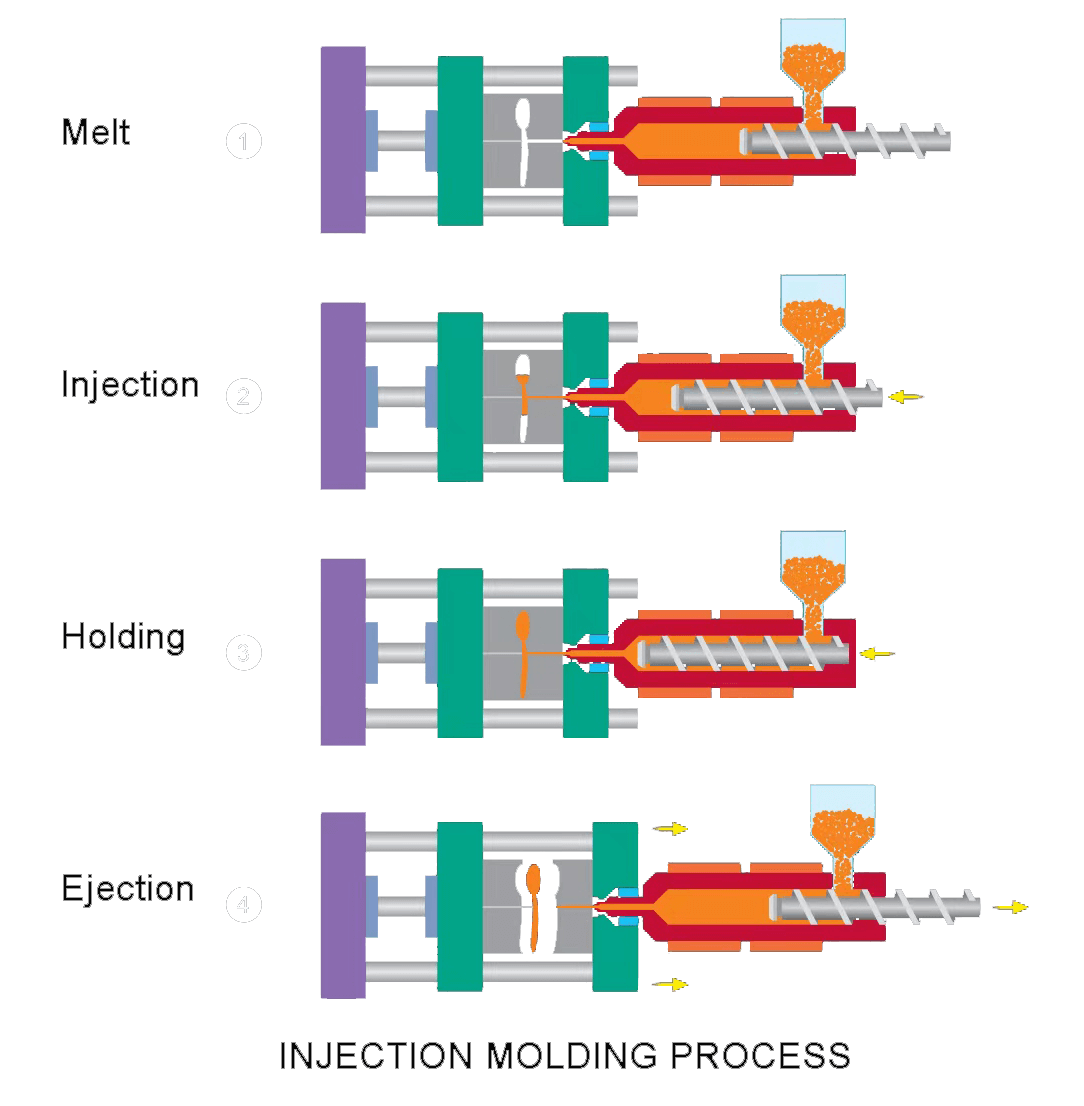
The process involves injecting molten plastic into a mold under high pressure, where it cools and solidifies to form the final part. However, the key difference lies in the scale and setup requirements. For low-volume production, the tooling costs are lower due to simpler molds or the use of alternative materials, such as aluminum, which are less expensive than the steel molds used in traditional high-volume injection molding.
Typical Production Quantities:
Low-volume injection molding is typically used for production quantities ranging from 50 to 10,000 units. It’s particularly advantageous when large-scale production isn’t feasible or necessary. Examples of typical production quantities include:
- Prototype parts
- Short production runs for testing or market trials
- Spare parts for existing products
- Custom or niche products for specific markets
2. Advantages of Low-Volume Injection Molding
Low-volume injection molding provides several key advantages for businesses looking to produce smaller quantities of high-quality parts efficiently. Here are the main benefits:
a. Cost-Effectiveness: Lower Tooling and Setup Costs
- Reduced Tooling Costs: Unlike traditional injection molding, which often requires expensive molds made from durable materials like steel, low-volume molding uses simpler molds, often made from aluminum. This lowers tooling costs significantly.
- Affordable Setup: The simplified setup process for low-volume production further reduces overall costs, making it an ideal solution for smaller production runs.
b. Faster Time to Market: Quicker Turnaround Times
- Reduced Lead Times: Low-volume injection molding speeds up production compared to traditional methods, allowing businesses to get their products to market more quickly.
- Faster Prototyping: With quicker turnaround times, companies can test prototypes, adjust designs, and produce small quantities without waiting for lengthy manufacturing cycles.
c. Design Flexibility: Ability to Quickly Iterate Designs and Make Adjustments
- Rapid Iteration: Since molds are less expensive and faster to produce, businesses can easily make design adjustments during the production process.
- Improved Product Development: Low-volume injection molding supports quick iterations, enabling companies to fine-tune their products based on feedback or testing without the cost of retooling.
d. Reduced Risk: Lower Financial Investment in Smaller Production Runs
- Smaller Investment: Low-volume injection molding requires a smaller financial commitment, making it an attractive option for startups and smaller companies.
- Reduced Financial Risk: By producing smaller batches, businesses can test the market and refine their products without committing to large-scale production, reducing the risk of overproduction or unsold inventory.
To better understand the production advantages of small batch injection molding, we have organized the contents for you into the following table:
Aspect | Traditional Injection Molding | Low-Volume Injection Molding |
Production Quantity | High | Low |
Tooling Cost | High | Low |
Lead Time | Long | Short |
Setup Time | Long | Short |
Design Flexibility | Moderate | High |
Waste Generation | More | Less |
Complexity of Parts | Suitable for complex parts | Suitable for complex parts |
Sustainability and Environmental Impact | Potential environmental impact | Generally more sustainable |
Maintenance and Repairs | Complex | Easy |
Customization Possibilities | Limited | High |
3. Ideal Applications for Low-Volume Injection Molding
Low-volume injection molding is an excellent solution for various production needs, especially in situations where high-volume manufacturing is not required or feasible. Here are the primary applications:
a. Prototypes: Used for Product Testing and Iteration
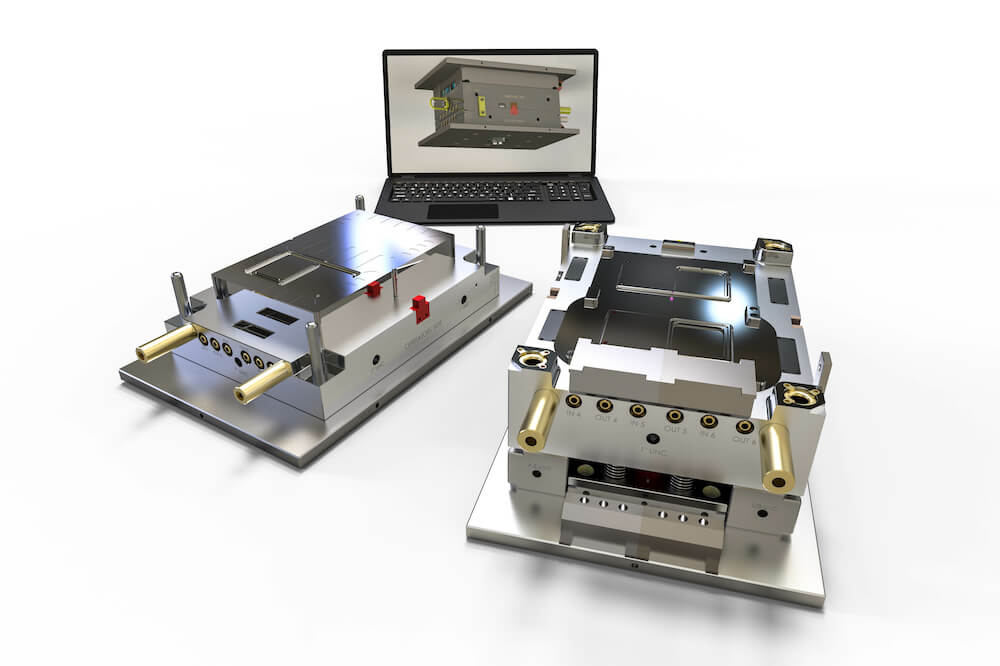
- Rapid Prototyping: Low-volume injection molding offers a fast and affordable way to produce functional prototypes. This is particularly beneficial during product development, where frequent design revisions are necessary to refine and perfect the final product.
- Design Testing: Prototypes produced via low-volume molding are ideal for testing form, fit, and function, enabling companies to identify any issues early in the development process without incurring high costs.
- Reduced Development Time: The speed of producing prototypes through low-volume molding helps shorten the overall product development cycle, allowing for quicker market testing.
b. Short-Run Production: For Small Quantities of Functional Parts

- Small Batch Runs: Low-volume injection molding is perfect for producing small quantities of functional components or parts, especially when large production runs aren’t required.
- Cost-Effective for Small Orders: For industries that need a limited number of parts, such as the automotive or medical device sector, low-volume molding allows businesses to meet demand without the expense of high-volume tooling or machinery.
- Maintaining Quality: Despite the smaller production scale, low-volume injection molding still maintains high part quality, making it suitable for precision components in small quantities.
c. Customized Products: For Niche Markets and Unique Requirements
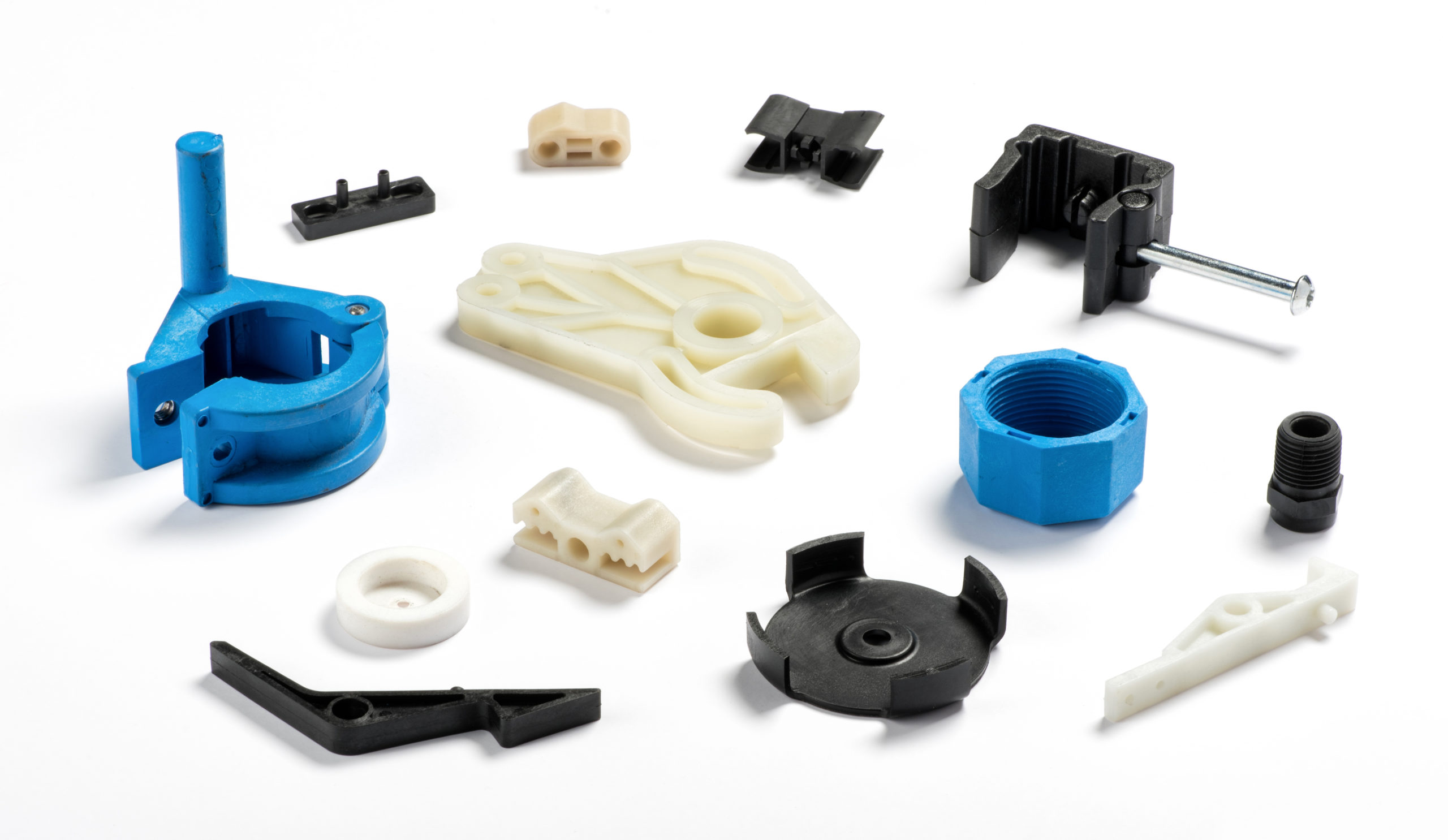
- Customization: Low-volume injection molding is ideal for producing customized products tailored to specific customer needs or niche markets. This can include custom colors, finishes, or dimensions that set products apart in competitive markets.
- Unique Product Designs: Businesses can use low-volume molding to create specialized parts or products that may not be viable through traditional manufacturing methods due to their unique requirements.
- Tailored to Small Markets: Whether it’s limited-edition products or components designed for specific applications, low-volume injection molding can be a valuable solution for companies needing to cater to specialized markets.
4. How Low-Volume Injection Molding Works
Low-volume injection molding follows a process similar to traditional injection molding but focuses on producing smaller quantities of parts. Here’s a step-by-step breakdown of the process:
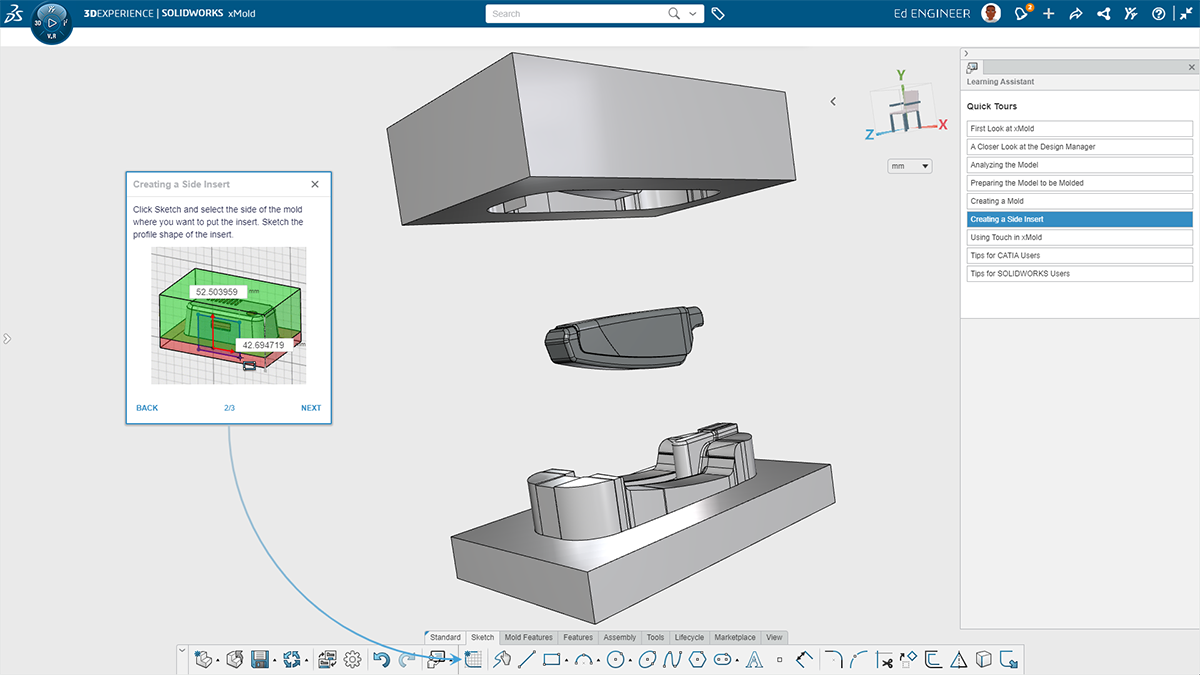
- Initial Design: The first step is to design the mold based on the part specifications. In low-volume injection molding, the mold can be made from various materials, such as aluminum or steel, depending on the production needs and desired mold life.
- Prototype Molds: For low-volume production, mold designs can be created quickly using 3D printing technology or rapid tooling techniques. This reduces lead times and allows for faster iteration of design changes.
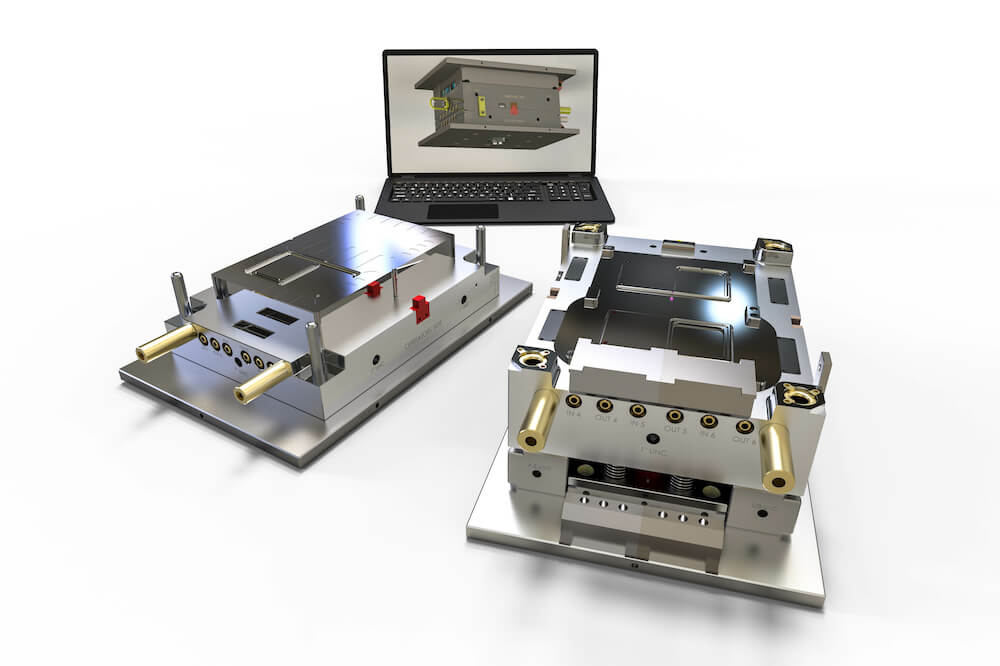
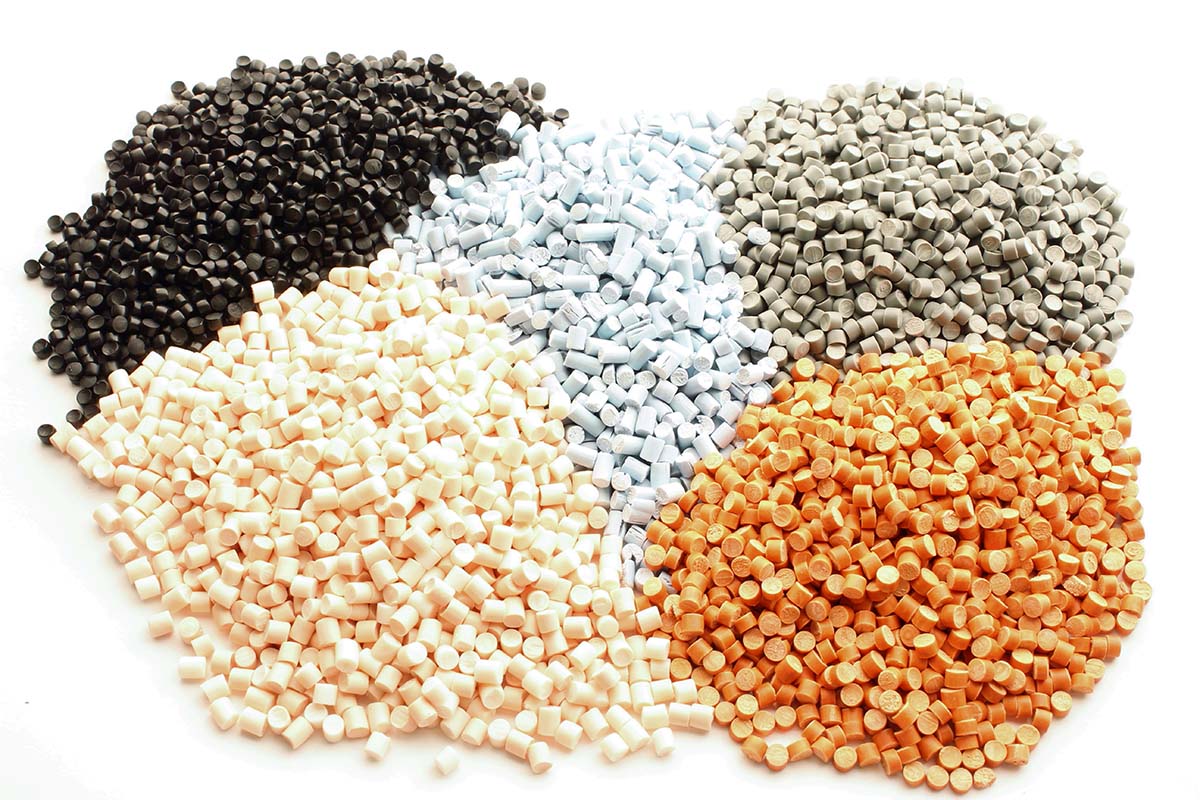
- Choosing the Right Material: The next step is selecting the material for injection. Material properties such as strength, flexibility, chemical resistance, and cost play a crucial role in the material selection process.
- Common Materials: Thermoplastics like ABS, polycarbonate, and polypropylene are commonly used for low-volume injection molding. However, custom materials may be chosen for specialized applications (e.g., high-temperature resistance in automotive parts).
- Material Compatibility: The material must be compatible with the mold and injection system to ensure smooth production and high-quality parts.
c. Injection Molding Setup
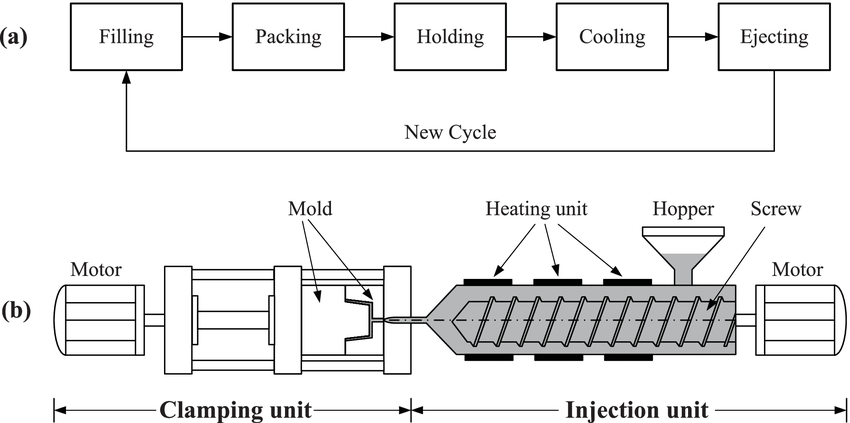
- Injection Unit: The material is heated and injected into the mold under high pressure using an injection molding machine. The temperature, pressure, and speed of injection are carefully controlled to ensure that the material fills the mold cavity properly and evenly.
- Mold Filling: The molten plastic is injected into the mold under pressure, filling the cavity and taking the shape of the desired part. This process is done with precision to ensure that the part’s details are accurately replicated.
d. Cooling and Solidification
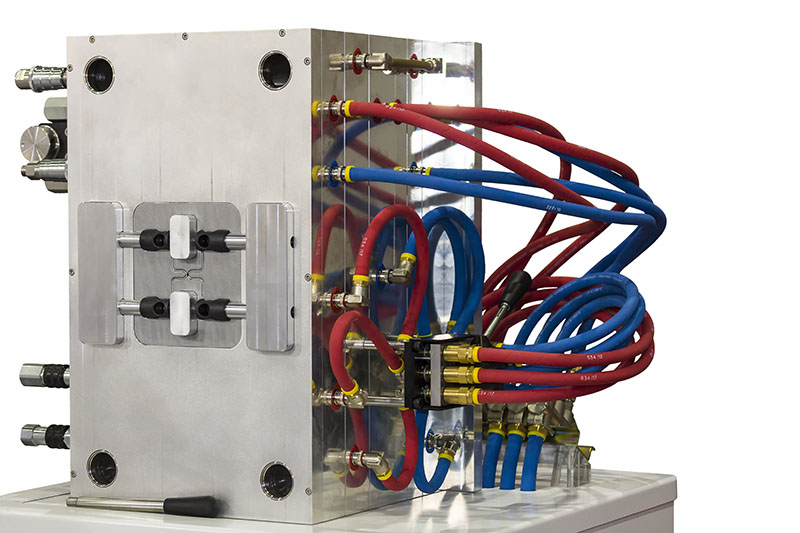
- Cooling Time: After the mold is filled, the part is allowed to cool and solidify inside the mold. The cooling time can vary depending on the material and the part’s complexity. Proper cooling is essential to prevent defects like warping or sink marks.
- Cooling Channels: The mold is designed with cooling channels to ensure even and efficient cooling of the part during solidification.
e. Part Ejection
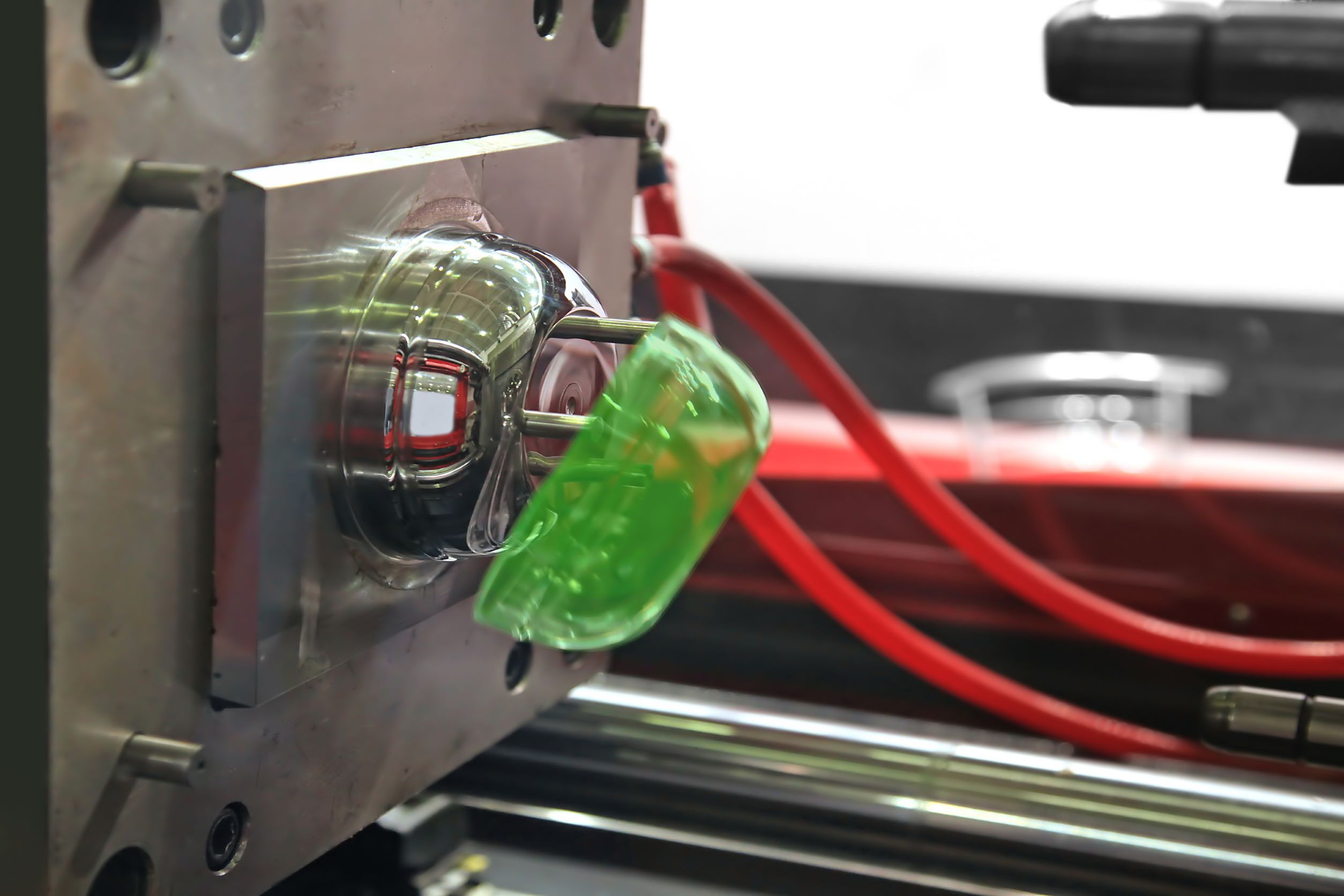
- Ejection Process: Once the part has cooled and solidified, it is ejected from the mold using ejector pins or other mechanical systems. The part may be inspected for any defects or quality issues before being sent to further processing, such as trimming or surface finishing.
f. Post-Processing (if needed)
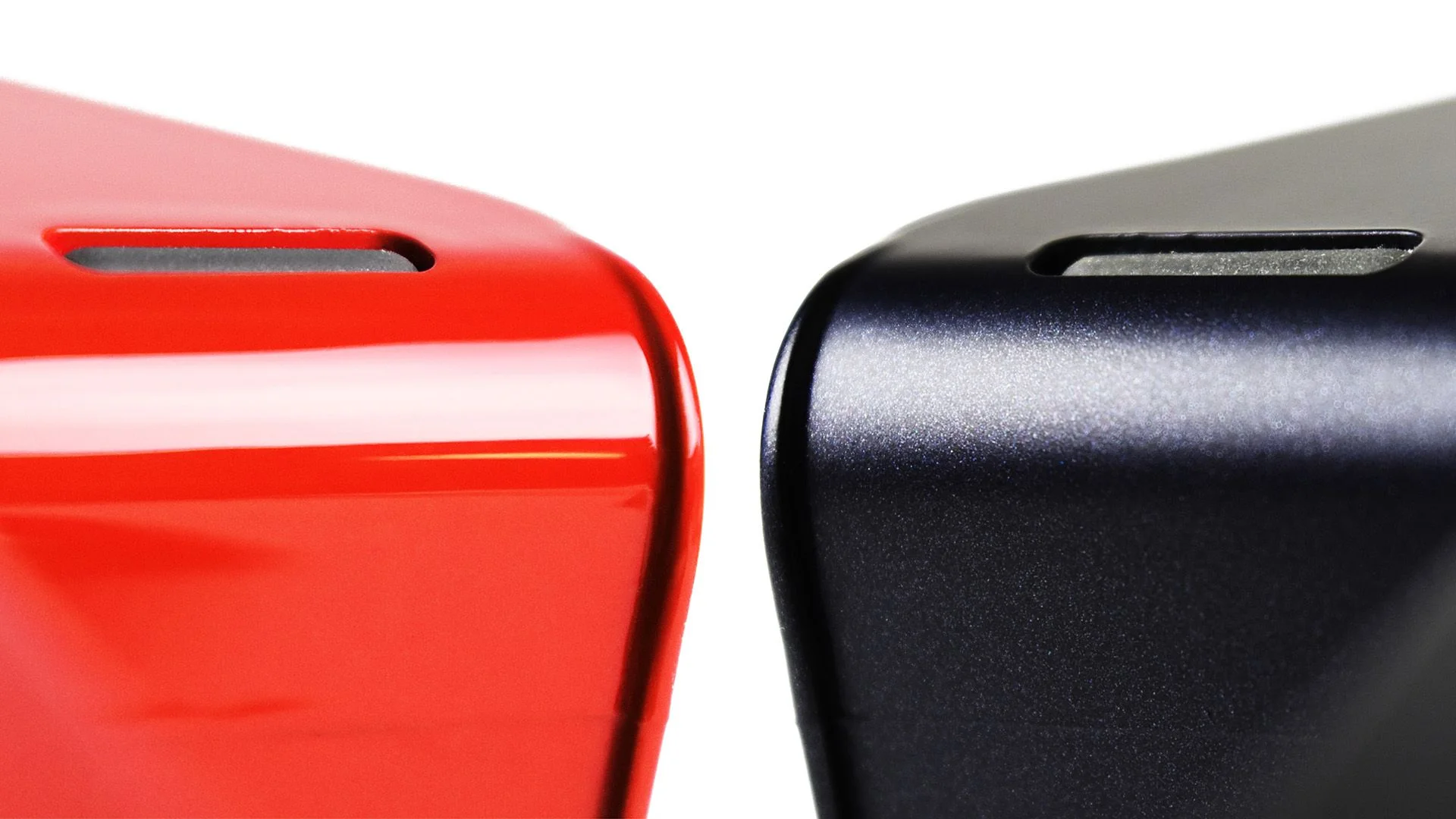
- Trimming: After the part is ejected from the mold, excess material or sprues are trimmed away to produce the final part.
- Surface Finishing: Parts may undergo additional finishing processes, such as painting, coating, or polishing, to meet the desired aesthetic or functional requirements.
Key Factors Influencing the Low-Volume Injection Molding Process
a. Material Selection
- The choice of material influences the strength, durability, and performance of the part. Materials must be selected based on the intended use of the part, including its environmental and mechanical requirements.
- Considerations: Material properties such as melt flow, heat resistance, and flexibility are critical for optimizing part quality.
b. Mold Design
- Complexity: Mold design is crucial in determining the cost and speed of production. Complex molds may require more time and investment to produce, but they can yield high-precision parts.
- Mold Lifespan: In low-volume production, molds may not be used for long runs, so mold material selection (e.g., aluminum vs. steel) plays a role in cost-effectiveness.
- Design for Manufacturability (DFM): Proper mold design ensures that the part can be molded with ease, minimizing defects such as warping, sink marks, or incomplete fills.
c. Part Geometry
- Complexity of Design: The geometry of the part affects how the mold is created and how easily the material can flow into the cavity. Intricate designs with thin walls or tight tolerances require more precise molds and careful handling during production.
- Wall Thickness: The thickness of the part walls directly impacts the cooling time, material flow, and strength of the final product. Consistent wall thickness helps to avoid defects and improve the part’s quality.
5. Key Factors to Consider in Low-Volume Injection Molding
When choosing low-volume injection molding for small batch production, several key factors must be taken into account. Each of these factors impacts the cost, quality, lead time, and flexibility of the process. Below, we break down these critical considerations:
a. Tooling and Mold Design
Impact on Cost
The tooling and mold design play a significant role in determining the overall cost of the injection molding process. While low-volume injection molding generally has lower tooling costs than high-volume production, the choice of material and complexity of the mold still affect pricing.
- Aluminum vs. Steel Molds: Aluminum molds are often used in low-volume runs due to their lower cost and faster turnaround times. However, they wear out faster compared to steel molds, which are more durable but more expensive. The trade-off between cost and mold life should be carefully considered based on the expected production quantities.
- Rapid Tooling: Rapid tooling techniques, such as 3D printing or soft tooling, can reduce the initial investment for low-volume production. These methods allow for quick mold creation, which is essential for fast prototyping or small batch runs.
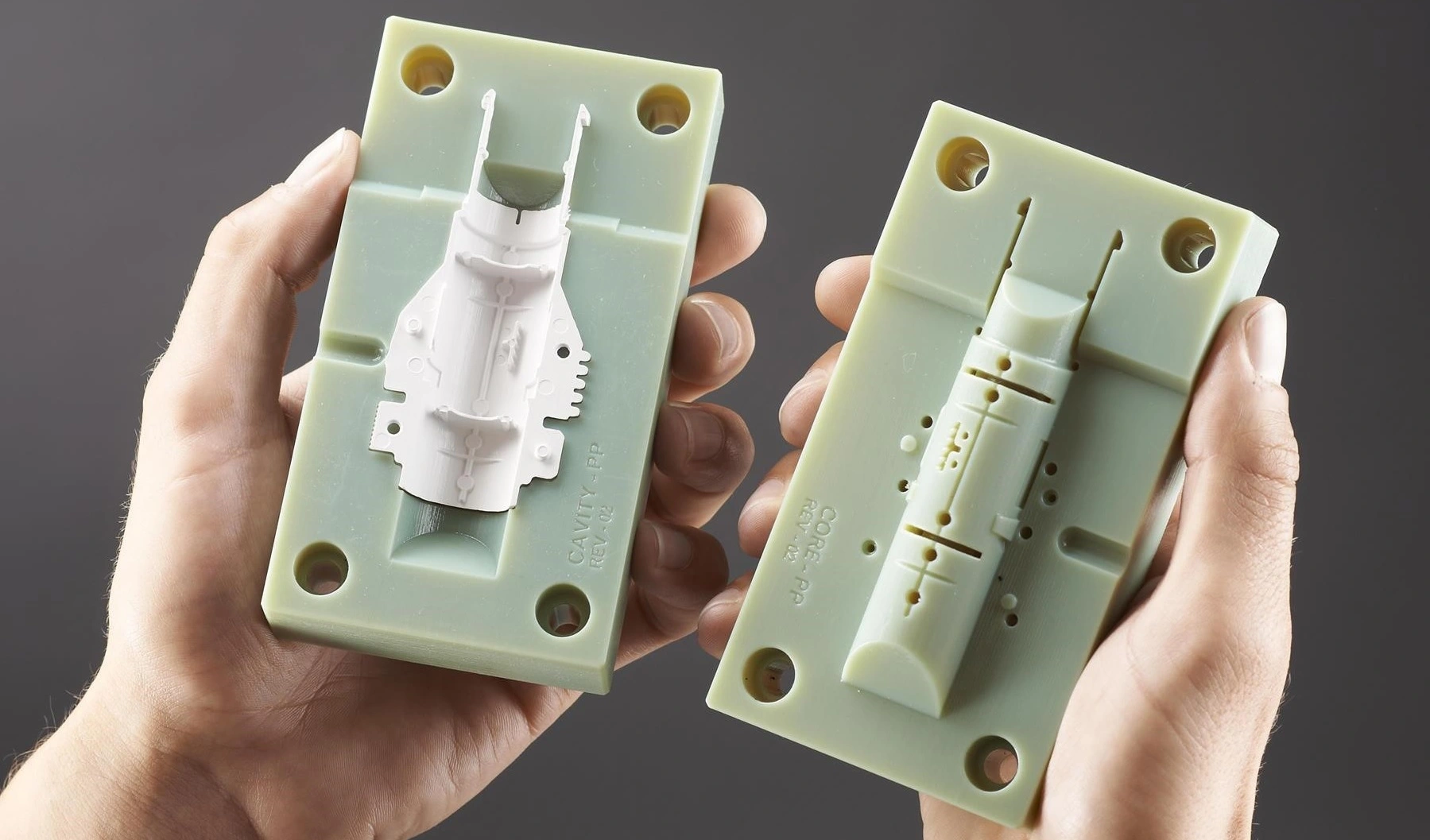
Impact on Quality
The precision and accuracy of the mold directly influence the quality of the final product. A well-designed mold ensures consistent part quality by minimizing defects such as warping, sink marks, or flash.
- Design for Manufacturability (DFM): This process involves designing parts that are easy to manufacture and minimizing complexity to reduce tooling costs and production time. Ensuring that your part design is optimized for the molding process is critical for achieving high-quality results.
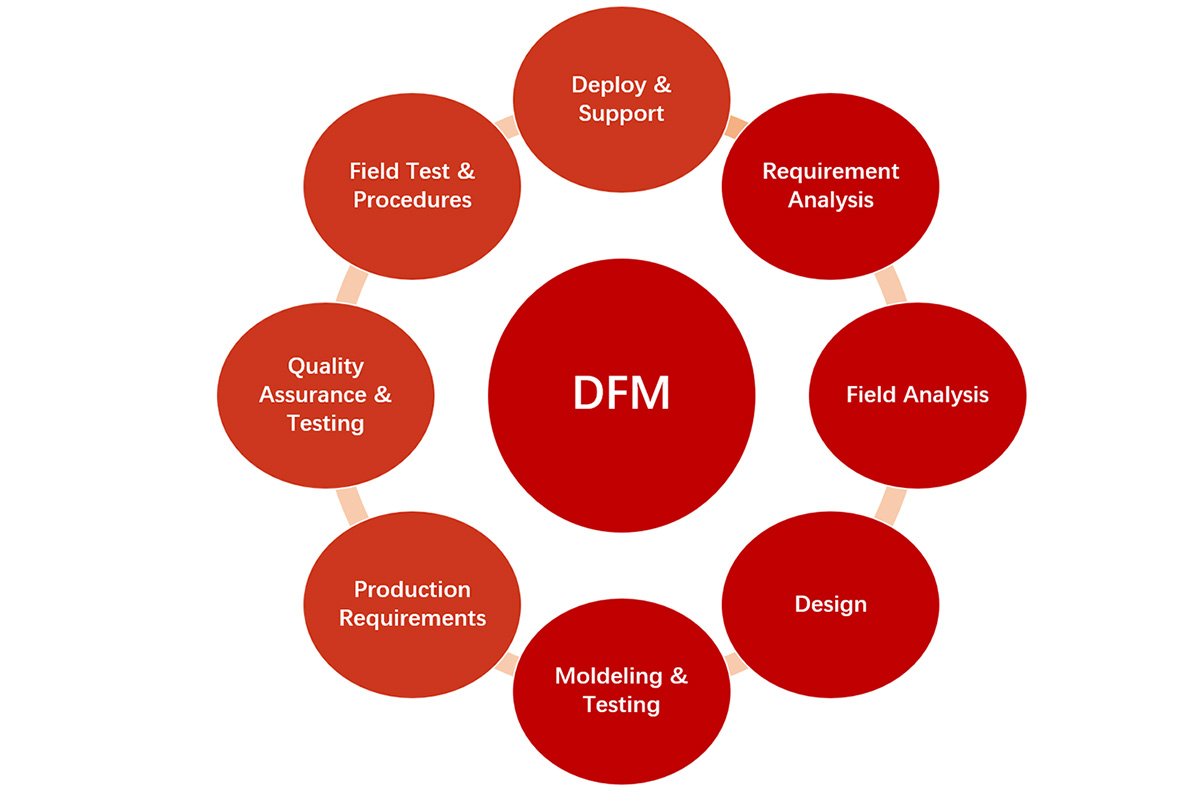
Impact on Production Speed
Mold design affects how quickly the part can be produced. Efficient mold cooling, proper venting, and simple geometries can lead to faster cycle times and higher production efficiency.
b. Material Selection
Choosing the Right Material: Selecting the appropriate material is essential to achieving the desired physical properties for the part, such as strength, flexibility, and heat resistance.
- Mechanical Properties: Consider the mechanical demands of the part, including tensile strength, impact resistance, and hardness. For example, automotive parts may require high-strength materials, while consumer products might prioritize flexibility or aesthetics.
- Material Compatibility: The chosen material must be compatible with both the mold and the injection system. Some materials require specific conditions for processing, such as temperature or pressure control, so understanding the material’s flow characteristics and thermal properties is key to achieving successful results.
- Cost Considerations: While high-performance materials often offer superior results, they can significantly increase production costs. Balancing material performance with cost-effectiveness is essential in low-volume injection molding.
c. Lead Time
Expected Timeframes: Lead time refers to the amount of time required to complete a production run, from mold design to part delivery. In low-volume injection molding, the lead time is typically shorter than traditional methods, but it can still vary depending on several factors:
- Tooling and Mold Design Complexity: More intricate molds or complex part geometries may require longer lead times to design, fabricate, and test.
- Material Availability: The availability of specific materials can affect lead times. If the material needs to be sourced or if custom materials are required, this can delay the start of production.
- Production Schedule: The urgency of your order and the manufacturer’s production schedule will also influence lead times. Many low-volume injection molding companies can accommodate expedited timelines, but additional charges may apply.
Factors that Influence Lead Time: External factors, such as supply chain issues, equipment downtime, or the complexity of post-processing steps (e.g., finishing, painting), can further impact the expected lead time.
d. Production Flexibility
Adjusting for Different Batch Sizes: Low-volume injection molding is inherently flexible, making it ideal for small batch runs. However, the process can also be adapted to accommodate different batch sizes or varying production schedules.
- Scaling Production: While low-volume molding is typically used for quantities ranging from a few hundred to a few thousand parts, the process can be adjusted for slightly higher volumes if required. This makes it a versatile solution for businesses that need the flexibility to scale production as demand increases.
- Customizing Product Designs: Low-volume injection molding allows businesses to iterate designs quickly. Changes to part features, materials, or dimensions can be made between production runs without significant cost increases, making it easier to respond to customer feedback or market shifts.
Customization for Unique Requirements: Low-volume injection molding is well-suited for producing customized products for niche markets or specific customer needs. The ability to adjust the production process means businesses can offer a variety of unique product variations without committing to expensive, high-volume production runs.
6. Optimizing the Low-Volume Injection Molding Process
Optimizing the low-volume injection molding process is essential to ensure that the production runs are efficient, cost-effective, and yield high-quality parts. Several strategies can be applied to achieve these goals, including the use of 3D printed molds, optimizing part designs, and fine-tuning injection parameters. Below, we explore each of these optimization techniques.
3D Printed Injection Molds: Advantages and Limitations
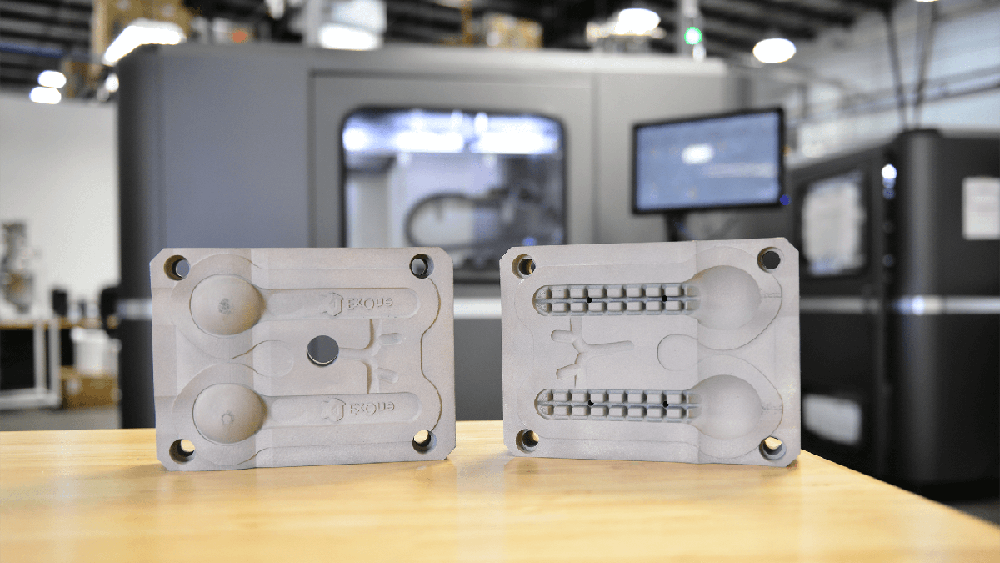
Advantages
- Cost-Effectiveness: 3D printed molds are often significantly cheaper than traditional metal molds, especially for low-volume production. This makes them an attractive option for small batch runs, reducing the upfront investment needed for tooling.
- Faster Turnaround: Since 3D printed molds can be designed and manufactured in a fraction of the time required for traditional molds, the production cycle is much quicker. This speed is crucial for businesses needing rapid prototyping or fast time-to-market.
- Complex Geometries: 3D printing allows for the creation of highly complex mold geometries that would be difficult or expensive to produce using traditional methods. This flexibility can help in creating intricate part features and designs without increasing costs.
- Design Iteration: 3D printed molds allow for quick design changes or adjustments. If issues arise during the testing phase, mold modifications can be easily implemented, reducing the time spent on redesigning or retooling.
Limitations
- Durability: One of the major limitations of 3D printed molds is their relatively short lifespan. Unlike traditional steel molds, which can withstand thousands of cycles, 3D printed molds may only be capable of handling a limited number of parts before they start to wear out. This can make them less suitable for larger production runs.
- Material Limitations: While 3D printed molds are suitable for many types of plastics, certain materials—especially those requiring high-temperature resistance—may not be compatible with 3D printed molds. This could limit their use in some industries, such as automotive or aerospace.
- Surface Finish: 3D printed molds may not achieve the same level of surface smoothness and finish as metal molds, which could affect the appearance or functionality of the molded parts.
Wall Thickness and Design Considerations
Optimizing Wall Thickness: Wall thickness plays a critical role in both the quality and efficiency of injection molding. Thicker walls can increase cooling time, which in turn extends cycle time and affects the overall production efficiency. On the other hand, overly thin walls can cause defects such as warping, sink marks, or incomplete filling.
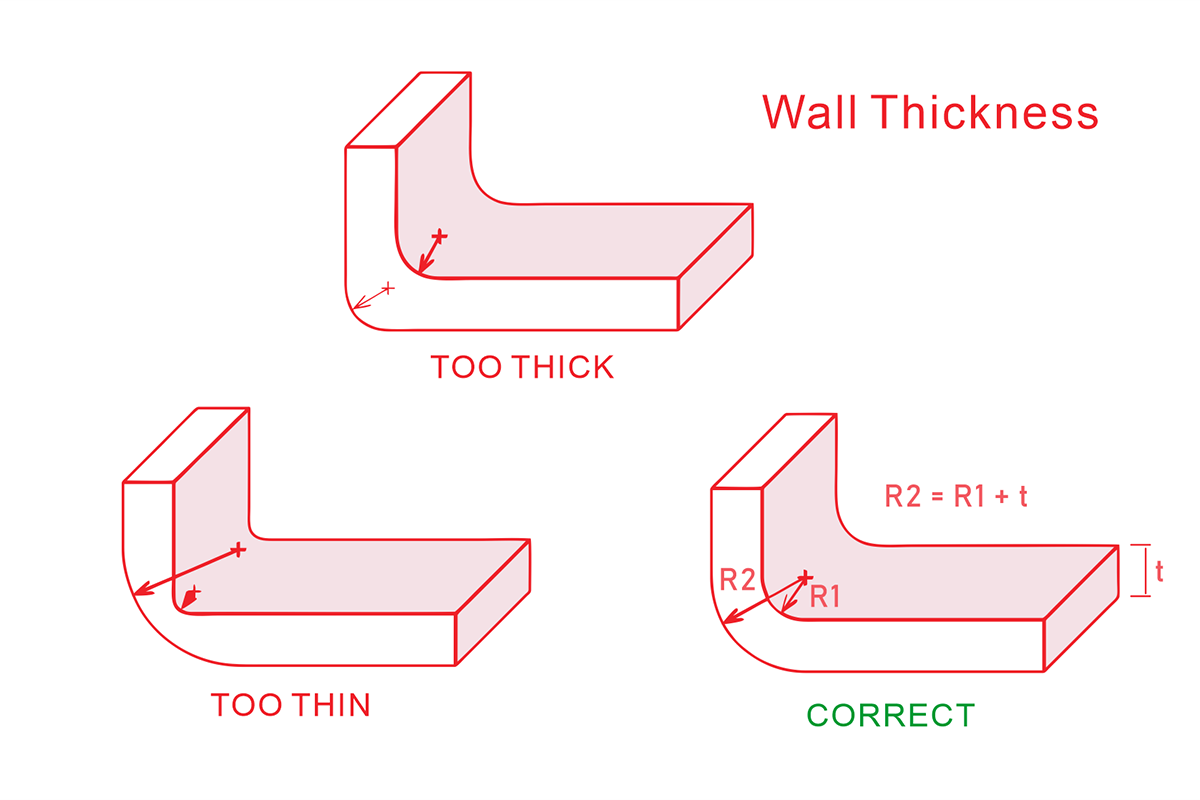
- Uniform Wall Thickness: To minimize defects and optimize material flow, it’s essential to maintain uniform wall thickness throughout the part. This consistency helps ensure that the material flows evenly, cools evenly, and solidifies without issues. Sudden changes in wall thickness should be avoided, as they can lead to stress concentrations, weak spots, and inconsistent parts.
- Design for Manufacturability (DFM): When designing parts for injection molding, it’s crucial to consider the ease of manufacturing. This includes choosing an appropriate wall thickness, adding draft angles to ease part removal, and ensuring that all features are achievable with the molding process. DFM principles can help optimize the design for both quality and cost-efficiency.
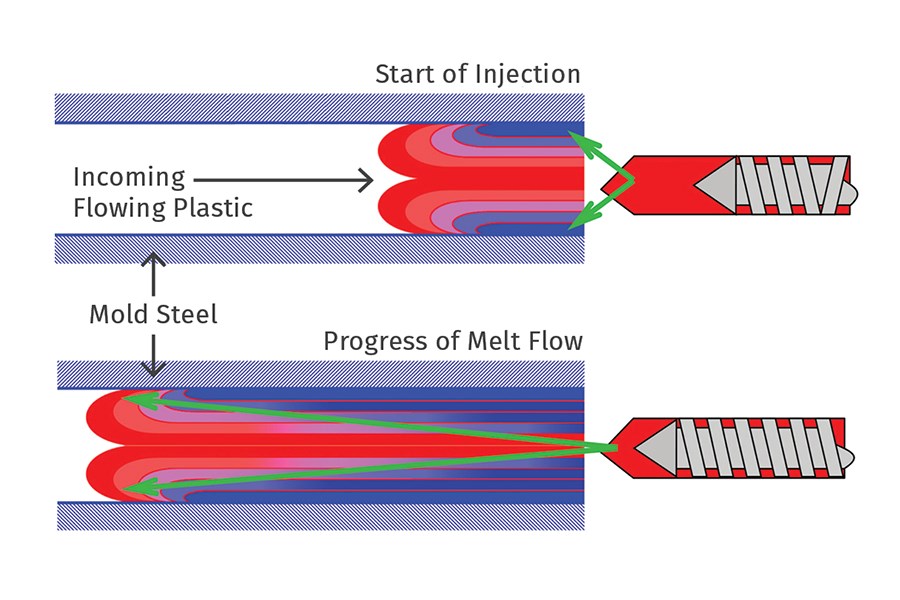
Material Flow and Cooling Efficiency: Properly designed parts can help optimize material flow and cooling, which can improve cycle times and reduce costs. Parts with well-thought-out geometries allow for more even material distribution, while efficient cooling systems can reduce the chances of defects and minimize overall production time.
Injection Parameters: How Adjusting Speed, Pressure, and Temperature Can Affect Outcomes
Injection Speed
The speed at which the material is injected into the mold can significantly impact part quality. High injection speeds may cause the material to flow too quickly, leading to defects such as short shots (incomplete filling) or excess pressure. Conversely, too slow an injection speed can lead to inconsistencies in part weight or surface finish.
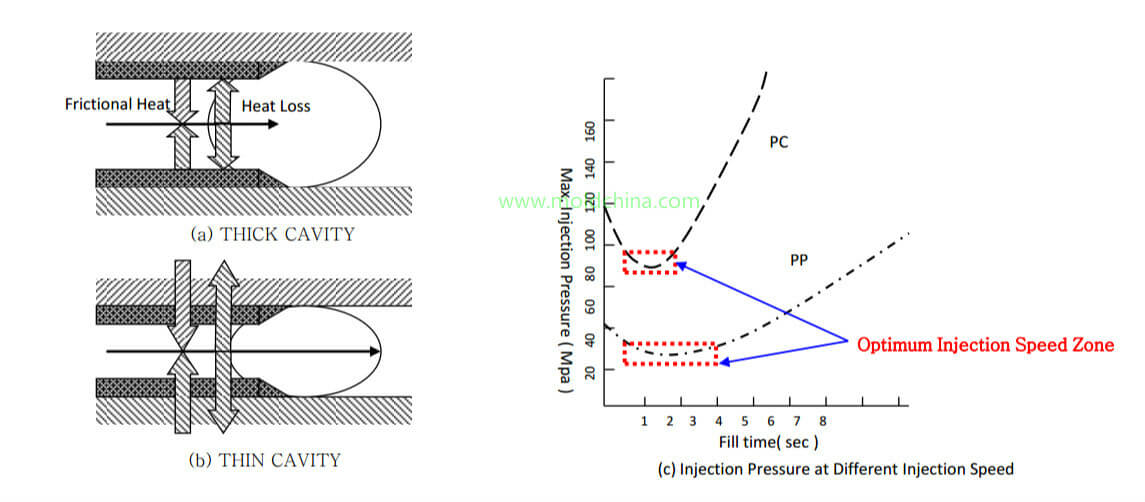
Optimal Speed: Adjusting the injection speed to match the material’s flow characteristics and the part geometry is essential. For complex parts with intricate features, slower injection speeds may be needed to ensure complete filling and to avoid trapped air or gas.
Injection Parameters: How Adjusting Speed, Pressure, and Temperature Can Affect Outcomes
Injection Speed
The speed at which the material is injected into the mold can significantly impact part quality. High injection speeds may cause the material to flow too quickly, leading to defects such as short shots (incomplete filling) or excess pressure. Conversely, too slow an injection speed can lead to inconsistencies in part weight or surface finish.
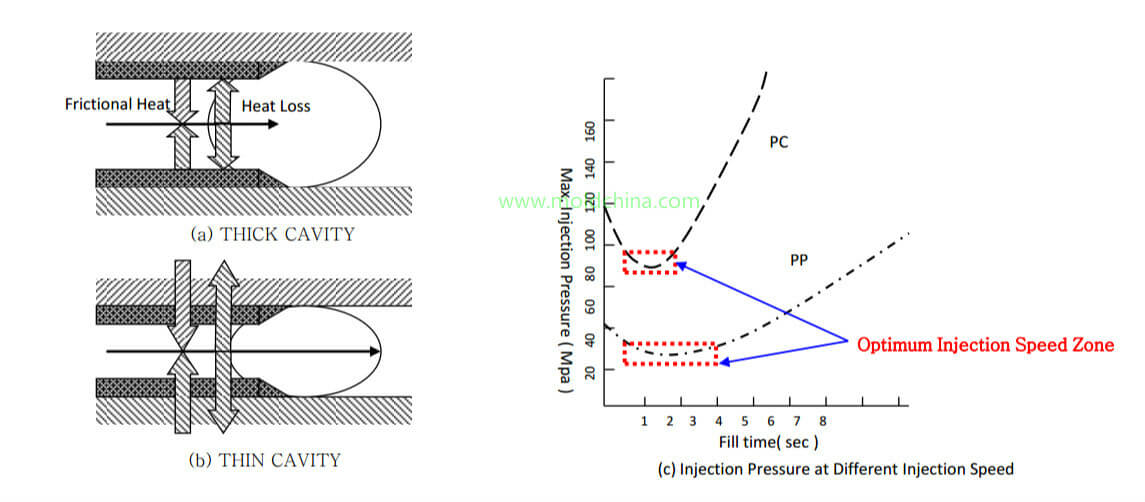
Optimal Speed: Adjusting the injection speed to match the material’s flow characteristics and the part geometry is essential. For complex parts with intricate features, slower injection speeds may be needed to ensure complete filling and to avoid trapped air or gas.
Injection Pressure
Injection pressure is another key parameter that affects part quality. Too much pressure can cause defects such as flash (excess material around part edges), while insufficient pressure can result in incomplete filling or weak parts.
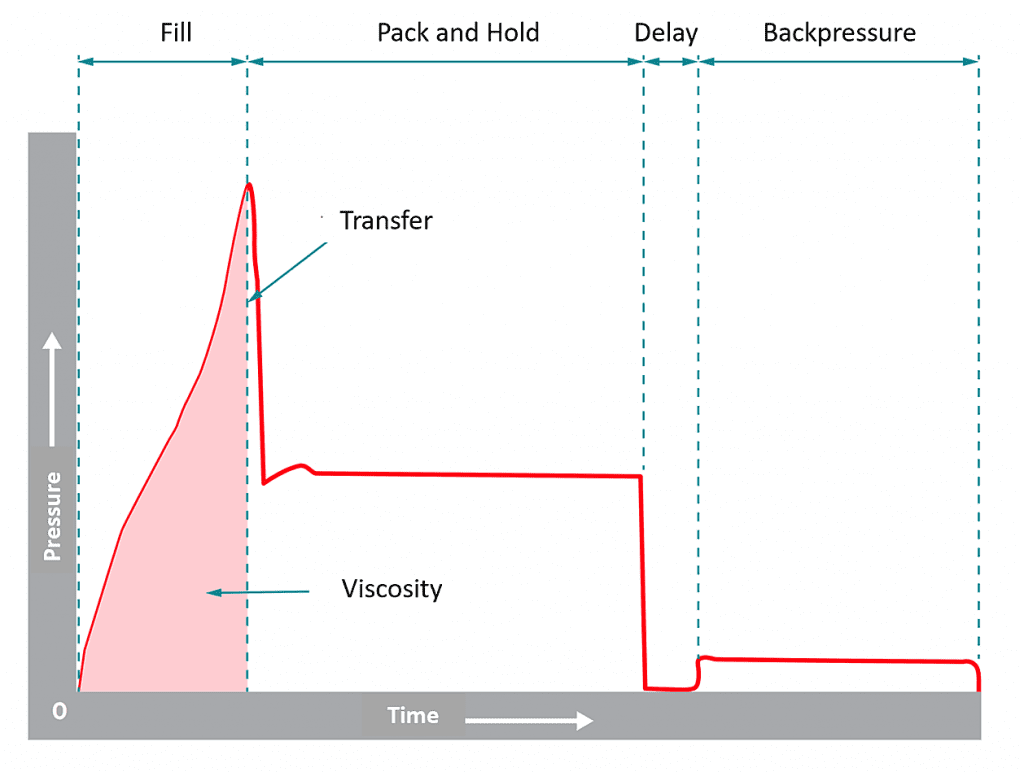
Balancing Pressure: The optimal injection pressure will depend on the material used, part complexity, and mold design. Adjusting the pressure allows manufacturers to optimize the filling process, ensuring a high-quality part without excess waste.
Injection Temperature
The temperature of the injected material is crucial for ensuring proper flow and material properties. If the material is too cool, it will flow slowly and may not fully fill the mold. If it’s too hot, it can lead to defects such as warping, burn marks, or an inconsistent surface finish.
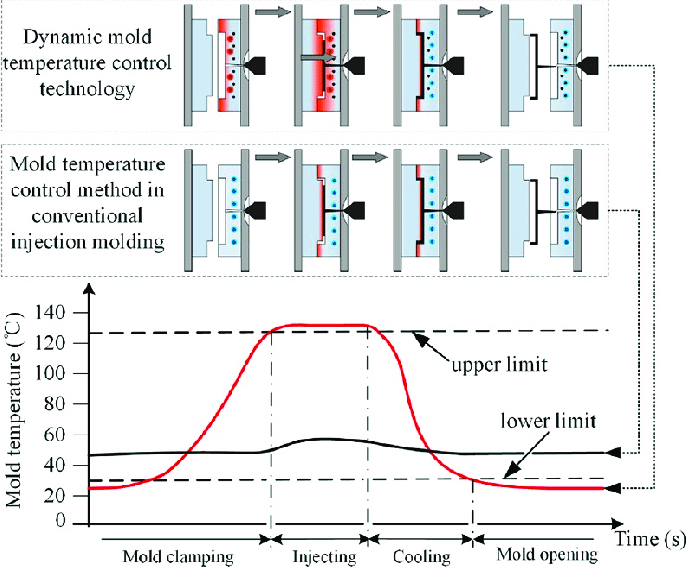
Controlling Temperature: Manufacturers should carefully control the injection temperature to match the material’s requirements and the complexity of the part. Temperature adjustments can also help improve the overall efficiency of the molding process, reducing cycle times and improving part quality.
By carefully optimizing these factors—using 3D printed molds, adjusting wall thicknesses, and fine-tuning injection parameters—businesses can enhance their low-volume injection molding processes. This not only improves the efficiency of production but also ensures that the resulting parts meet the highest quality standards while minimizing costs.
7. Choosing the Right Injection Molding Partner for Low-Volume Production
Choosing the right partner for low-volume injection molding is essential for a successful project. A good partner should have the right experience, provide high-quality products, and be flexible enough to meet your needs. As a leader in the industry, KingStar Mold excels in all these areas, ensuring that your low-volume production runs smoothly. Here are the key factors to consider when selecting an injection molding service provider:
a. Experience in Low-Volume Production
- Look for a partner with experience in small-batch production. KingStar Mold has extensive experience working with industries ranging from automotive to household products, handling the unique challenges of low-volume runs such as tight deadlines and cost control.
- Our team understands the intricacies of low-volume injection molding, ensuring that your production requirements are met efficiently, without compromising on quality.
b. Quality Control
- Ensuring consistent, defect-free parts is crucial in low-volume production. At KingStar Mold, we prioritize quality assurance at every stage of production. With our ISO 9001 certification, we maintain rigorous standards to deliver reliable, high-quality parts.
- We implement robust testing procedures to make sure that your parts meet the highest standards, ensuring they perform flawlessly in the end product.
c. Production Capacity and Flexibility
- Whether you’re producing hundreds or a few thousand parts, KingStar Mold is fully equipped to handle your low-volume needs. Our advanced equipment and experienced team enable us to adjust production volumes quickly, providing the flexibility you need for small runs.
- With KingStar Mold, you can rest assured that your production capacity will scale up or down according to your changing requirements, all while maintaining the highest level of service.
d. Cost-Effectiveness
- We understand that cost is a crucial consideration in low-volume production. KingStar Mold offers competitive pricing that aligns with your budget without compromising on quality. We work closely with you to find the most cost-effective solution, balancing quality and efficiency.
- Our detailed, transparent quotes ensure that you know exactly what you’re paying for, covering mold creation, materials, labor, and any other associated costs.
e. Communication and Support
- Good communication is key to a smooth production process. At KingStar Mold, we pride ourselves on our proactive customer service. Our team is responsive and keeps you updated on the status of your order at every stage.
- Whether it’s answering questions, providing updates, or addressing any issues, we’re committed to offering top-tier customer support, ensuring that your experience is seamless and stress-free.
f. Technology and Capabilities
- KingStar Mold uses state-of-the-art injection molding technology, enabling us to handle a wide variety of materials and complex designs with precision. Our advanced molding machines and capabilities like 3D printing for rapid prototyping ensure that we meet the most demanding production requirements.
- With our cutting-edge technology, we can offer high-quality solutions that improve efficiency, reduce waste, and shorten production times.
g. Post-Production Services
- At KingStar Mold, we don’t just stop at producing your parts—we offer comprehensive post-production services including part assembly, finishing, and packaging.
- We also handle shipping and logistics with the same attention to detail, ensuring that your parts are delivered on time and in perfect condition.
8. Common Challenges and How to Overcome Them
Low-volume injection molding offers many benefits, but it also comes with certain challenges. Understanding these challenges and how to overcome them can help ensure a smooth production process. Below are some common issues faced in low-volume injection molding and how to address them:
a. Material Variability
- Challenge: Materials used in low-volume production may exhibit variability in properties like strength, color, or consistency, especially if sourcing small quantities. This can lead to issues with the final part’s quality and performance.
- Solution: Work closely with your supplier to ensure material batches are consistent. Consider using well-established, high-quality materials that have been tested for your specific application. Request sample parts before starting full production to verify material consistency. Additionally, keep track of material performance data for future reference.
b. Mold Durability
- Challenge: Molds for low-volume injection molding are often produced with a focus on cost efficiency, which can lead to issues with mold durability. The mold might wear out more quickly than those used for high-volume production, resulting in defects or part inconsistencies.
- Solution: Use durable materials for mold construction, such as hardened steel or aluminum, and ensure proper maintenance throughout the production process. 3D printed molds can be an option for smaller production runs, but they may not last as long as traditional molds. Evaluate the number of parts needed and choose the most suitable mold material based on expected lifespan and cost.
c. Tight Tolerances
- Challenge: Low-volume production often requires parts with tight tolerances, which can be difficult to achieve consistently, especially when dealing with complex geometries.
- Solution: Collaborate closely with your injection molding partner to ensure precise design specifications are met. Use advanced molding machines with higher precision and ensure proper mold maintenance. If necessary, consider running tests with prototypes to identify any potential issues with tolerances before beginning full-scale production.
9. Conclusion
Low-volume injection molding offers a range of advantages, particularly for businesses needing small quantities of high-quality parts. With benefits such as cost-effectiveness, faster time-to-market, and design flexibility, it provides an efficient solution for prototyping, short-run production, and customized products. However, as with any manufacturing method, there are important considerations, including material selection, tooling costs, and maintaining tight tolerances.
To maximize the benefits of low-volume injection molding, it’s crucial to carefully evaluate your specific production needs. Collaborating with an experienced injection molding partner, such as KingStar Mold, can help ensure that you select the right materials, design the molds effectively, and optimize production processes to achieve high-quality, cost-efficient results.
By taking these factors into account and working with a trusted partner, you can streamline your low-volume production process and meet your business goals with confidence. Please feel free to send email to sales@kingstarmold.com or leave online message, we will reply via emailing within 24 hours.