Overview of Sheet Metal Forming & Bending
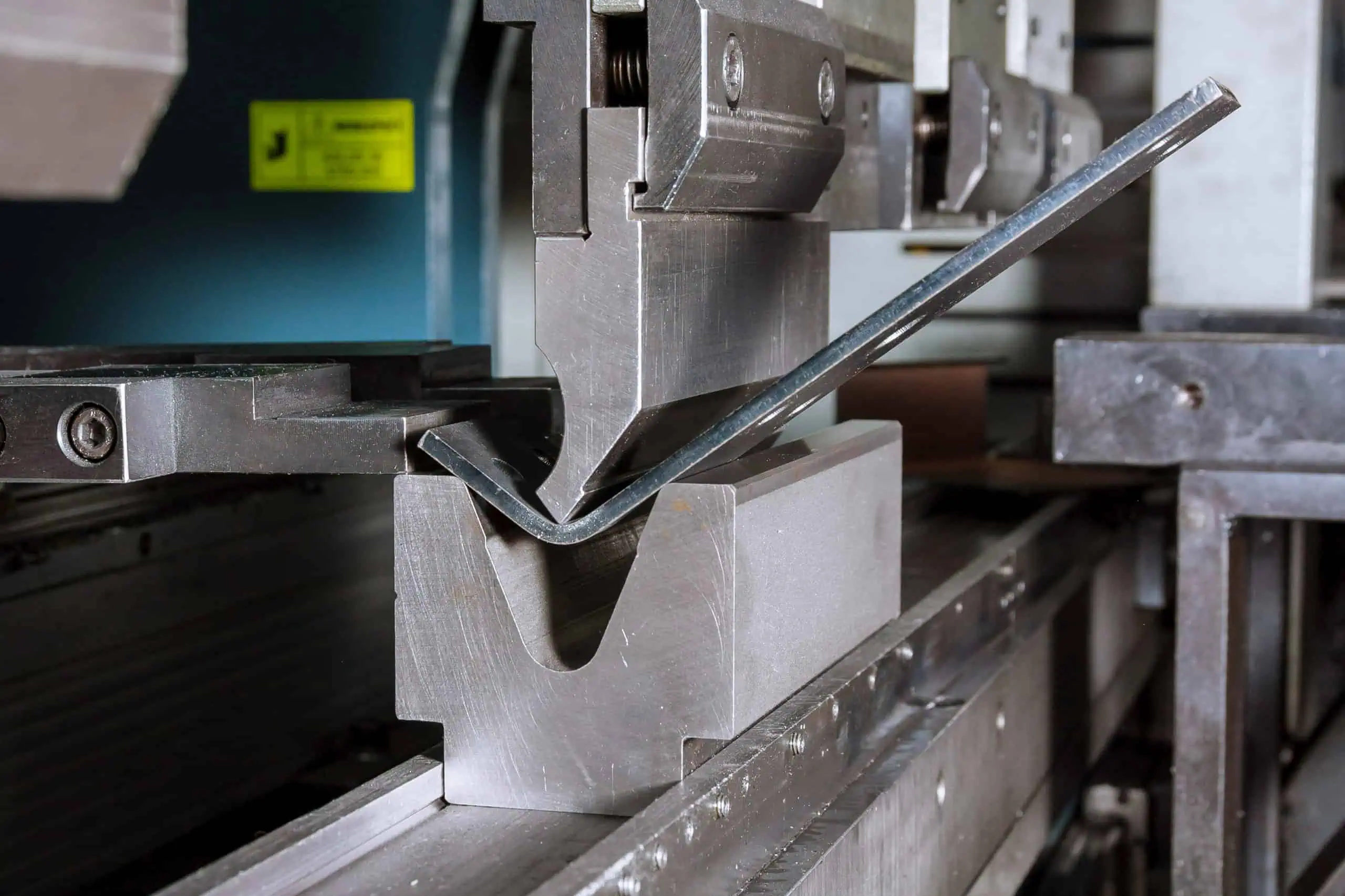
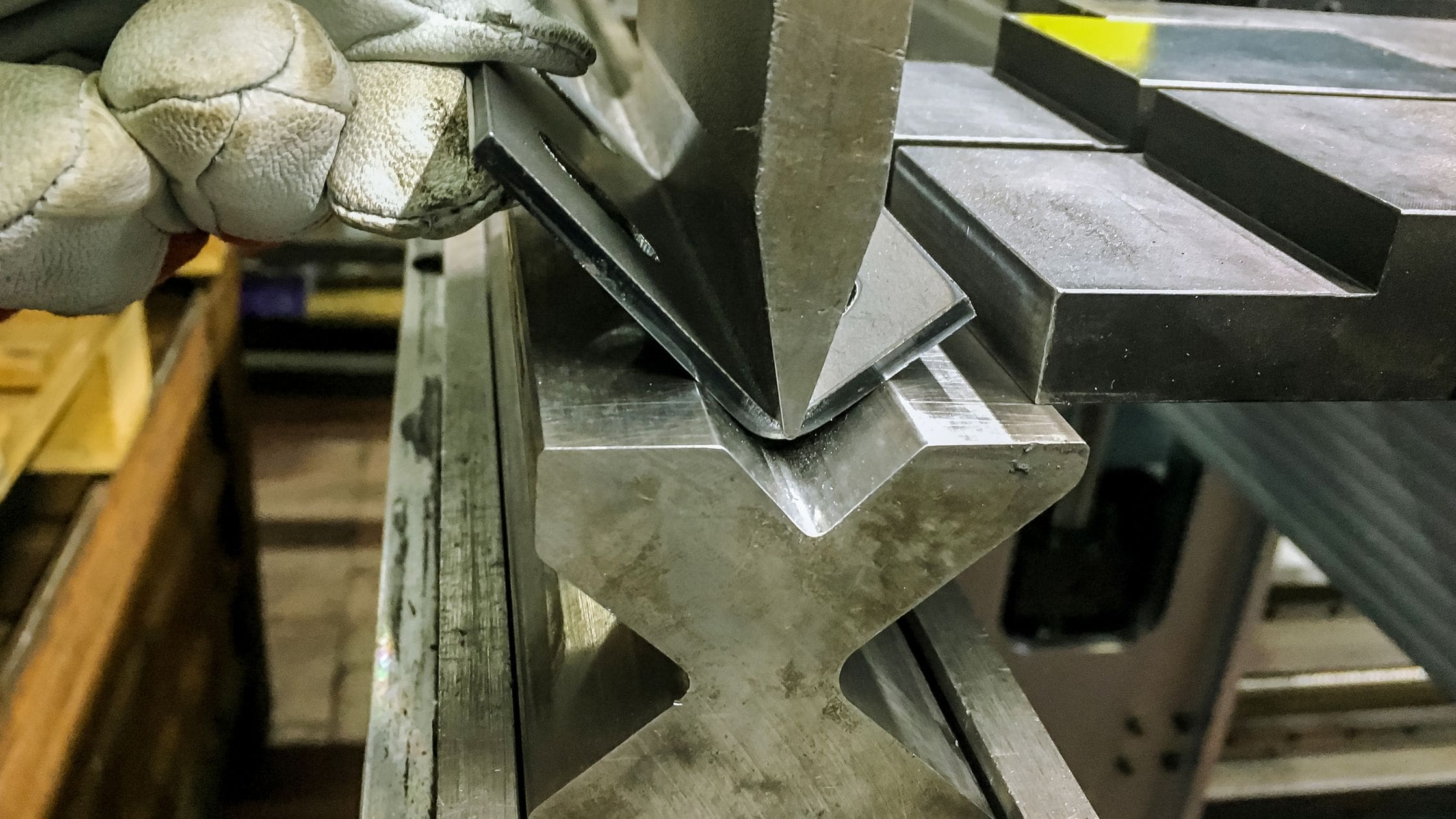
Free Design Review for Forming & Bending Projects
We offer a complimentary 30-minute virtual meeting with one of our sheet metal applications engineers to review your forming and bending project design. This session provides a valuable opportunity to discuss any questions or concerns you may have. Common topics covered during the review include:
Selection of appropriate forming and bending techniques
Material thickness and type considerations
Tolerances and precision requirements
Optimization for production efficiency and cost-effectiveness
Sheet Metal Forming & Bending Materials
Aluminum is a lightweight, corrosion-resistant material that is easy to form into complex shapes. It is ideal for applications in industries such as aerospace and automotive, where high strength-to-weight ratios are required.
- Aluminum 5052: Excellent corrosion resistance and good formability. Commonly used for marine and automotive components.
- Aluminum 5083: High strength and exceptional resistance to corrosion, making it ideal for harsh environments, such as marine and industrial uses.
- Aluminum 6061: Versatile and widely used, particularly in structural applications. Although it can be formed easily, it may require careful handling in more complex designs due to its strength.
Steel is commonly used in forming due to its strength and durability. It is easy to form, especially in thinner gauges, and offers versatility in various industries, from construction to heavy machinery.
- Mild Steel (A36): A widely used, cost-effective option that is easy to form, weld, and cut. Ideal for structural applications, automotive parts, and general manufacturing.
- Stainless Steel (304): Known for its corrosion resistance and strength. Stainless steel is suitable for forming parts that require high durability, such as kitchen equipment and medical devices.
- High-Strength Low-Alloy Steel (HSLA): Provides enhanced strength and resistance to fatigue, while still being formable. Commonly used in automotive and heavy machinery applications.
Copper offers excellent conductivity and corrosion resistance, making it ideal for electrical and plumbing applications. It is highly ductile, which makes it a good choice for forming into detailed shapes.
- Copper C1100: Offers high electrical conductivity and is easy to form. Commonly used for electrical components and wiring.
- Copper C2600 (Brass): Provides a balance of strength, ductility, and corrosion resistance, commonly used for fittings and hardware.
Brass is a copper alloy that combines copper and zinc. It is highly ductile, corrosion-resistant, and offers good machinability. Brass is often used for components requiring both strength and a decorative finish, such as fittings, hardware, and electrical components.
- Brass C36000: Known for excellent machinability, commonly used in plumbing fittings, electrical connectors, and decorative parts.
- Brass C2600: A balance of strength, corrosion resistance, and ductility, ideal for hardware, jewelry, and electrical components.
Stainless steel offers excellent strength, corrosion resistance, and durability. It’s widely used in industries where hygiene and long-term durability are essential, such as in medical devices, food processing, and marine applications. Bending stainless steel requires precise control to avoid cracking due to its hardness.
- Stainless Steel 304: Known for corrosion resistance and formability, widely used for medical devices, kitchenware, and industrial applications.
- Stainless Steel 316: Offers superior corrosion resistance, making it ideal for marine and chemical processing industries, though it requires careful handling during bending due to its strength.
Production Capabilities
for Forming
Minimum Qualifying Part Size | 0.05 in x 0.05 in (12.7mm x 12.7mm) |
Maximum Pressing Force | 80 tons |
Maximum U-Channel Ratio | 2:1 (width:height) |
Maximum Bend Length | 47 in. |
Bend Angles | 1 degree ‘kick’ to 135 degrees |
Bending Output | Linear bends—external and internal flanges |
Offsets | Standard |
Forming Best Practices | Relieve bends in CAD designs |
use manufacturer-recommended radius tooling | |
Ensure appropriate placement of nearby features (e.g., holes, hardware inserts, other bends) | |
Hems | Closed hems up to 47 in., open hems up to 36 in. |
Internal Radius Tooling Options | 0.01 in. to 1 in. (standard tooling increments) |
>1 in. radius bends will be bump formed |
for Bending
Maximum Part Size | 1.5 m x 1.5m |
General Tolerances | ISO 2768 |
Metal Bending Forces | Up to 1000 tons |
Lead Time | 5 days or more |
Bending Thickness | Up to 60 mm |
Bending Line Length | Up to 7200 mm |
Bend to edge/hole, single surface | +/- 0.254 mm (+/- 0.010 in.) |
Bend Angle | +/- 1° |
Bend Cutting Area | Up to 4000 mm |
Bend Radius | equal to material thickness |
Advantages of Forming & Bending Your Metal Part
Material Efficiency
These processes minimize material waste by accurately shaping the metal without excessive trimming or scrap, leading to more sustainable production.
Design Flexibility
The forming and bending processes allow for a wide variety of shapes and intricate designs, enabling customization to meet specific project needs.
Cost-Effective Production
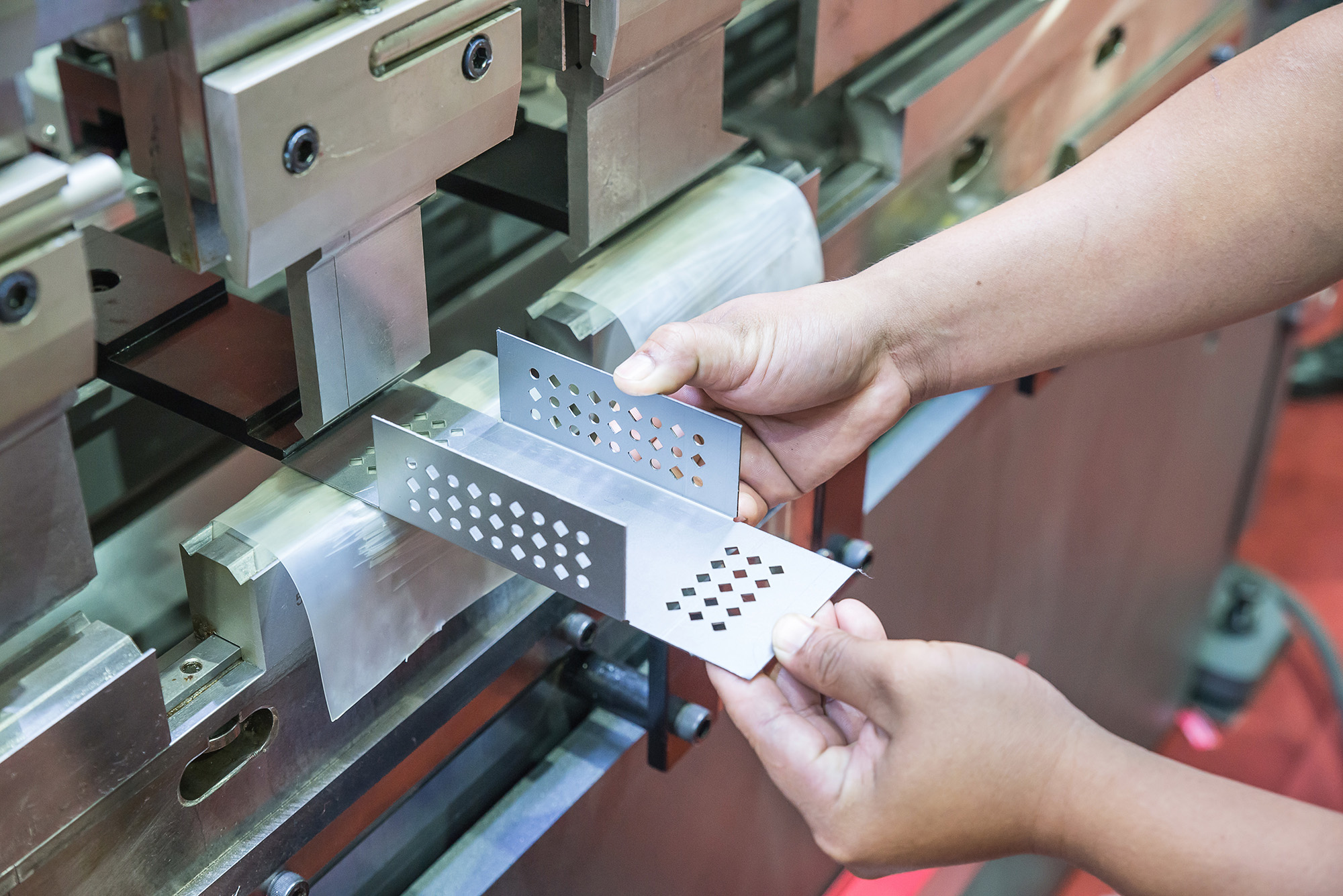
KingStar Mold Sheet Metal Forming & Bending Workshop
Our sheet metal forming and bending workshop is equipped with state-of-the-art machinery and a skilled team dedicated to precision and quality. From custom shapes to complex components, we handle a variety of materials and thicknesses to meet diverse industry requirements. Our advanced processes ensure consistent accuracy and durability, ideal for automotive, household, and industrial applications. With a commitment to efficiency and innovation, we deliver tailored solutions to match your exact specifications.
600+
Sets of Machines
100+
Countries Shipped
20,000+
Customers Served
Material Thicknesses for Forming
Material | Grade | Available Thicknesses |
---|---|---|
Brass | C260 | 0.025 in. – 0.125 in. (0.635 mm – 3.175 mm) |
Copper | C1010 | 0.025 in. – 0.125 in. (0.635 mm – 3.175 mm) |
C1100 | 0.025 in. – 0.125 in. (0.635 mm – 3.175 mm) | |
Steel | CRS/HRPO | 0.025 in. – 0.250 in. (0.635 mm – 6.35 mm) |
Galvanneal (pre-plated) | 0.025 in. – 0.134 in. (0.635 mm – 3.40 mm) | |
Galvanized (pre-plated) | 0.025 in. – 0.134 in. (0.635 mm – 3.40 mm) | |
Stainless Steel | 304-2B | 0.025 in. – 0.250 in. (0.635 mm – 6.35 mm) |
304-#4 | 0.025 in. – 0.119 in. (0.635 mm – 3.023 mm) | |
316-2B | 0.025 in. – 0.134 in. (0.635 mm – 3.40 mm) | |
Aluminum | 6061-T6 (requires review) | 0.025 in. – 0.134 in. (0.635 mm – 3.40 mm)* |
5052-H32 | 0.025 in. – 0.250 in. (0.635 mm – 6.35 mm) |
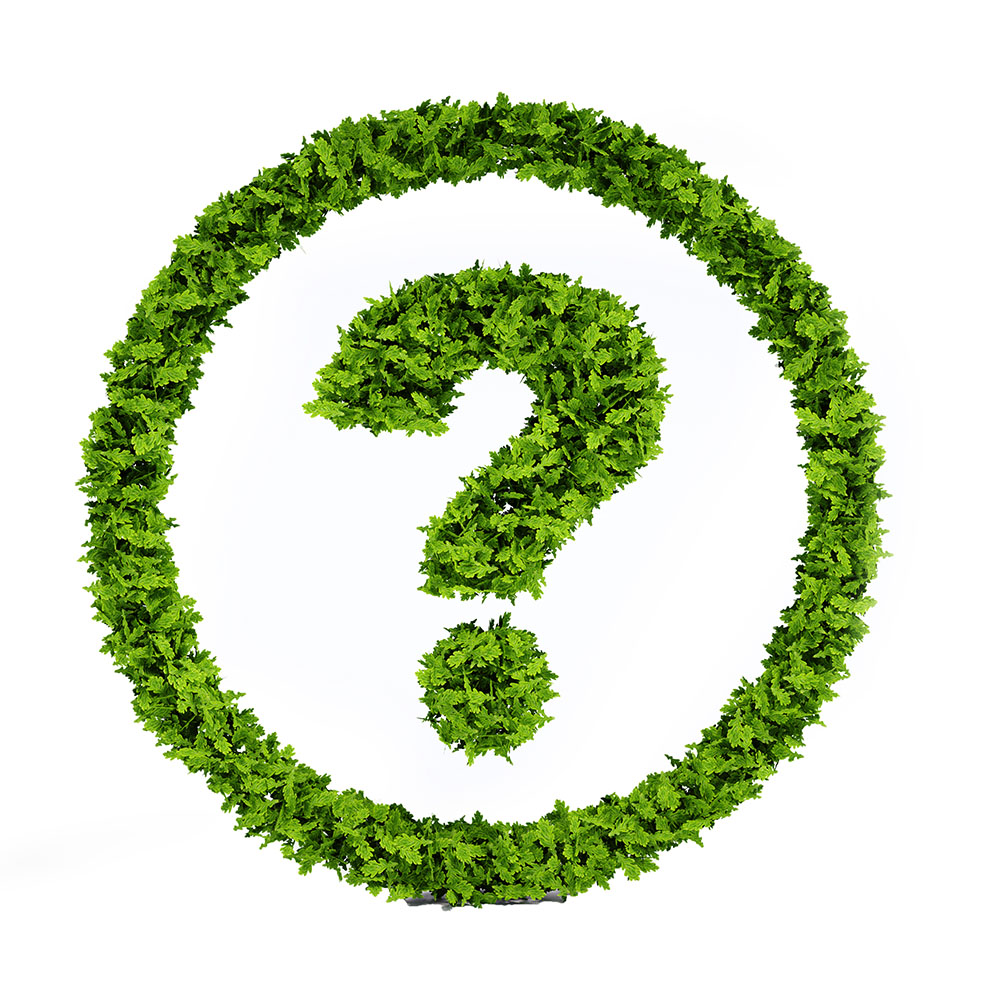
We can bend metal sheets with a maximum thickness of 60 mm and a bending line length of up to 7200 mm.
Our general tolerances comply with ISO 2768 standards. For bend-to-edge or hole-to-edge measurements, the tolerance is ±0.254 mm, and for bend angles, it is ±1°.
We work with aluminum, stainless steel, steel, brass, and copper in various grades and thicknesses to meet your specific project needs.
Sheet metal forming and bending are manufacturing processes used to reshape metal sheets into desired shapes and angles without altering their material properties.
Yes, we specialize in custom designs and can accommodate complex geometries. Our team reviews all designs to ensure manufacturability and provides recommendations to enhance efficiency.
We implement stringent quality control measures, including regular inspections and adherence to ISO standards, to deliver consistent and high-quality results for every project.
At KingStar Mold, we emphasize precision and quality. We use advanced equipment to ensure consistent results, and our team offers design assistance to help you optimize your project for efficiency and cost-effectiveness.
Lead times typically start at five days or more, depending on project complexity and volume.