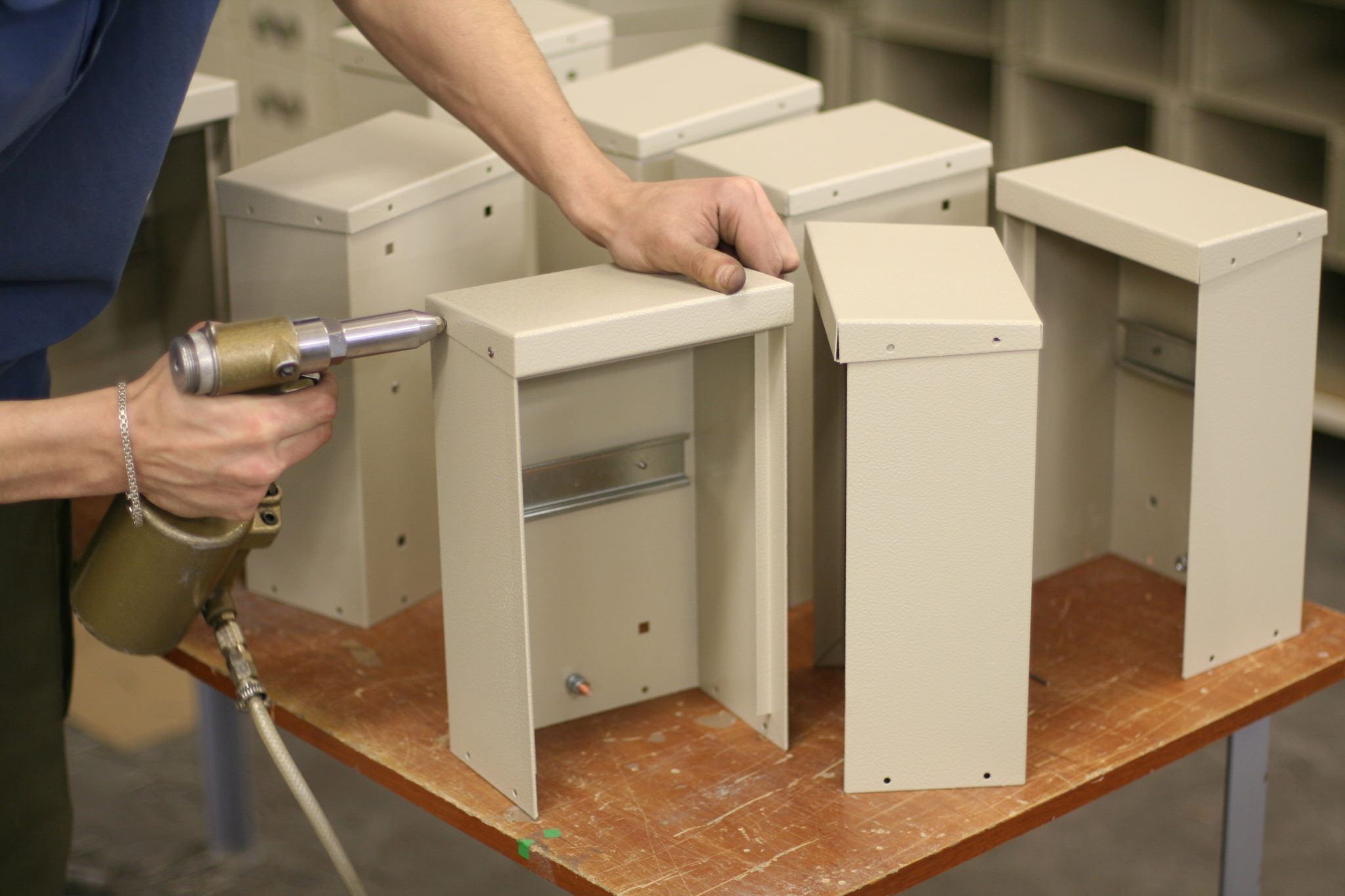
Overview of Sheet Metal Fabricated Assemblies
Free Design Review for Sheet Metal Fabrication Assemblies
Take advantage of our 30-minute virtual meeting with a sheet metal applications engineer to refine your project. This session is ideal for addressing your questions and ensuring your design aligns with production needs.
Material suitability for application
Optimizing design for cost-effectiveness
Improving strength and durability
Best fabrication techniques for accuracy and minimal waste
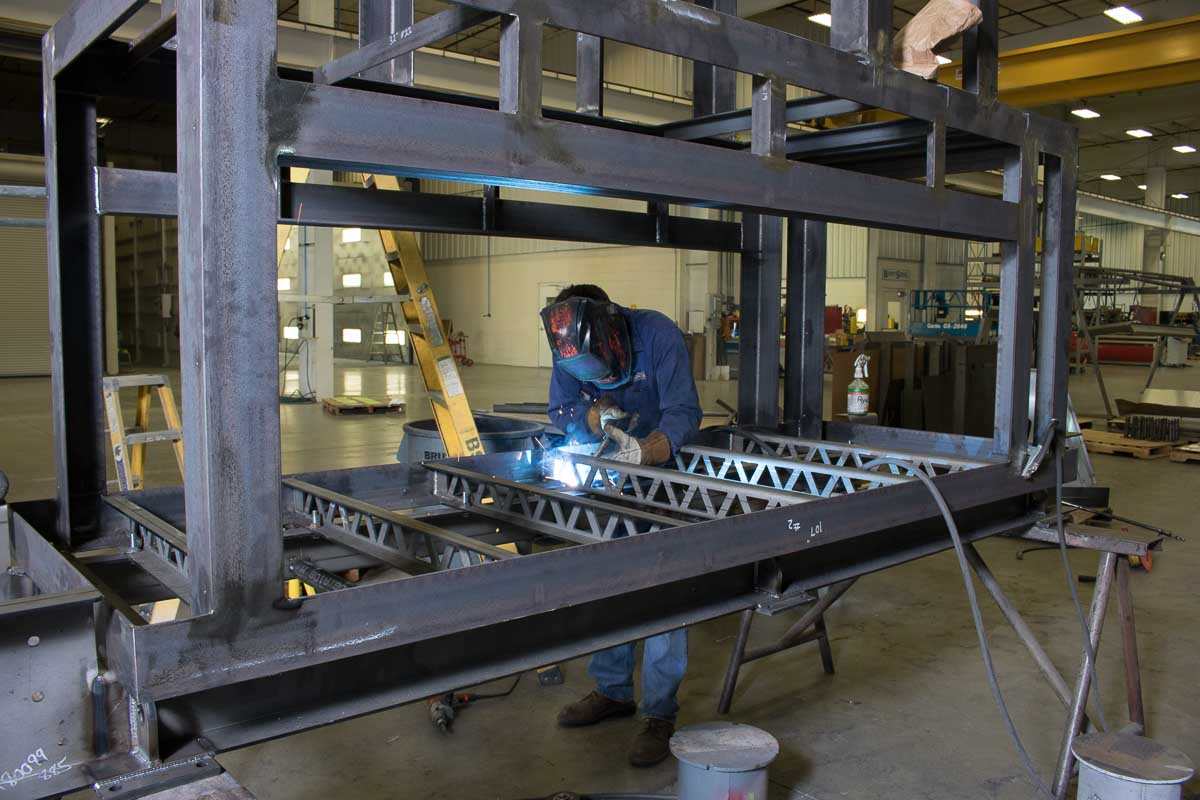
Applications of Fabricated Assemblies
Our online sheet metal assembly service allows you to create functional, end-use products delivered in just days. With each project, you receive design for manufacturability (DFM) feedback and expert-level support, ensuring your design is optimized for production. A wide range of finishing options is available to meet your aesthetic needs.
Fabricated assemblies are commonly used for:
Accepted File Format and Configuration
File Format | Details |
---|---|
Preferred Format for Assemblies | Upper-level assembly STEP files |
SOLIDWORKS Users | Solid assembly file (.sldasm) with separate component files (.sldpart) |
Weldment Projects | Provide a 2D drawing along with your CAD submission |
Non-assembly Projects | Solid (or top-level) assembly file is not required if no assembly is needed |
Sheet Metal Fabricated Aseemblies Materials
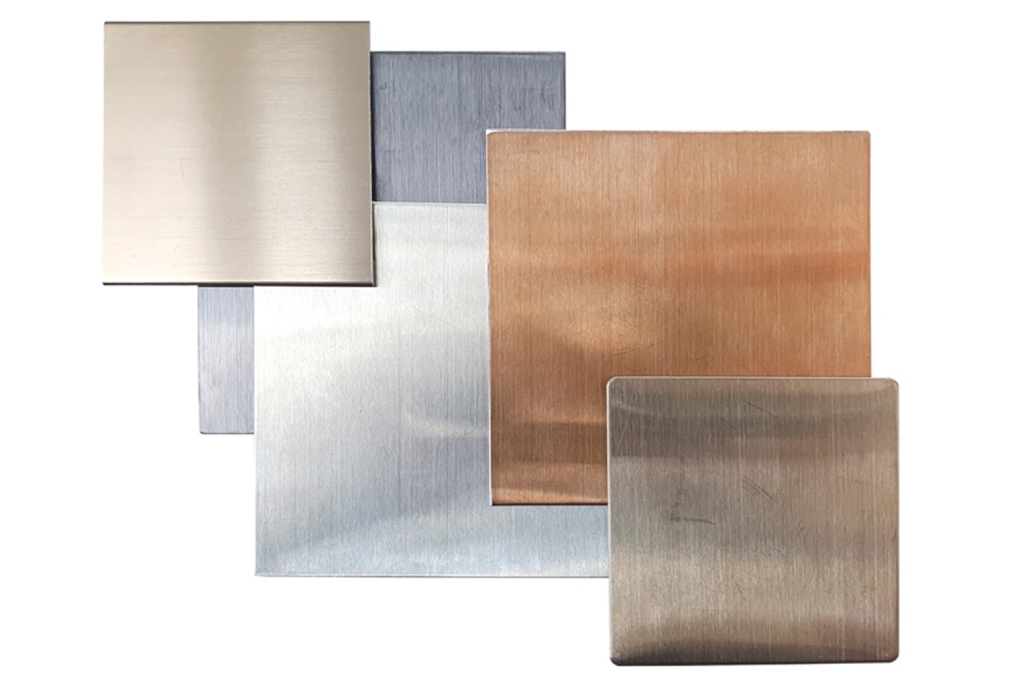
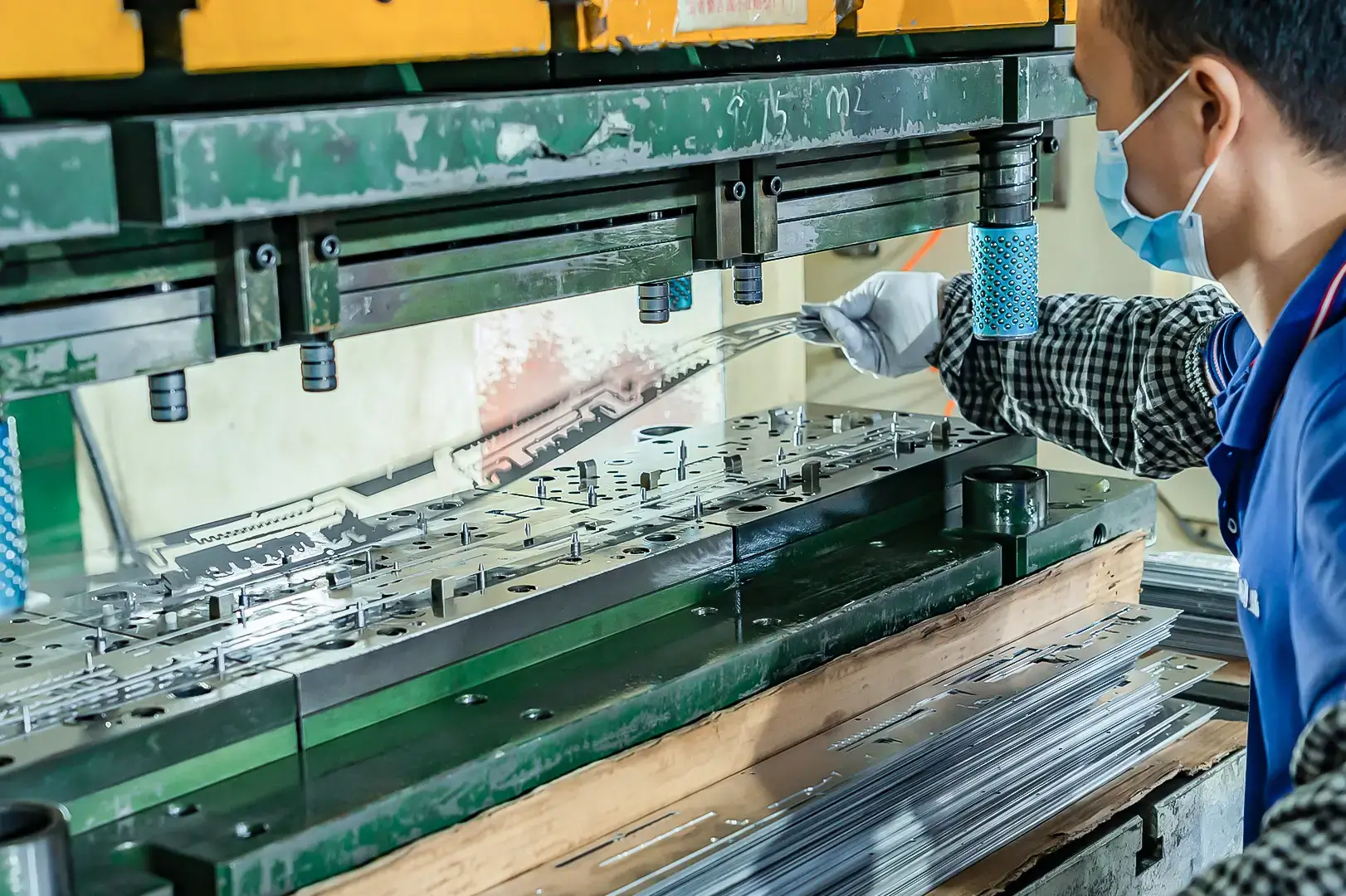
Assembly Construction Guidelines
Formed features
Machined Features
Inspection reporting options
Available Methods for Assembly
Welding Guidelines
Design Guidelines
If flexibility in joining is needed, consider riveting, a technique where components are joined using rivets.
Lead Time: Welding adds 1 business day to your project.
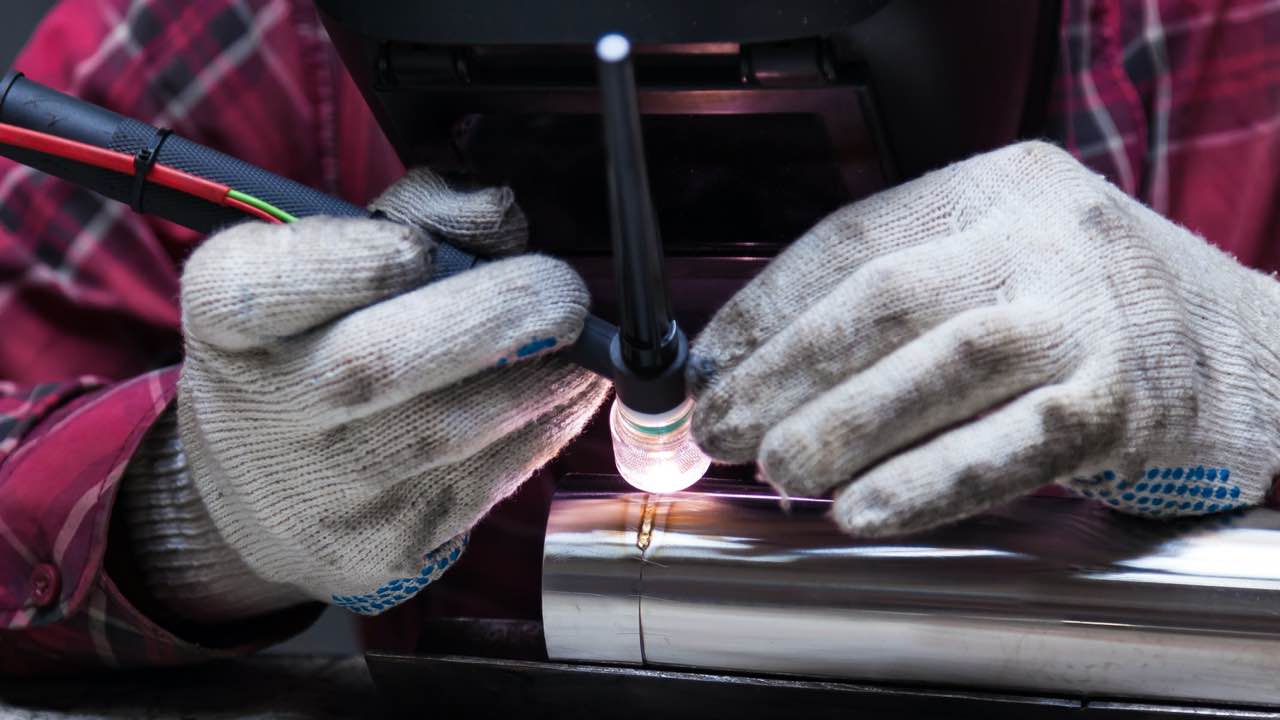
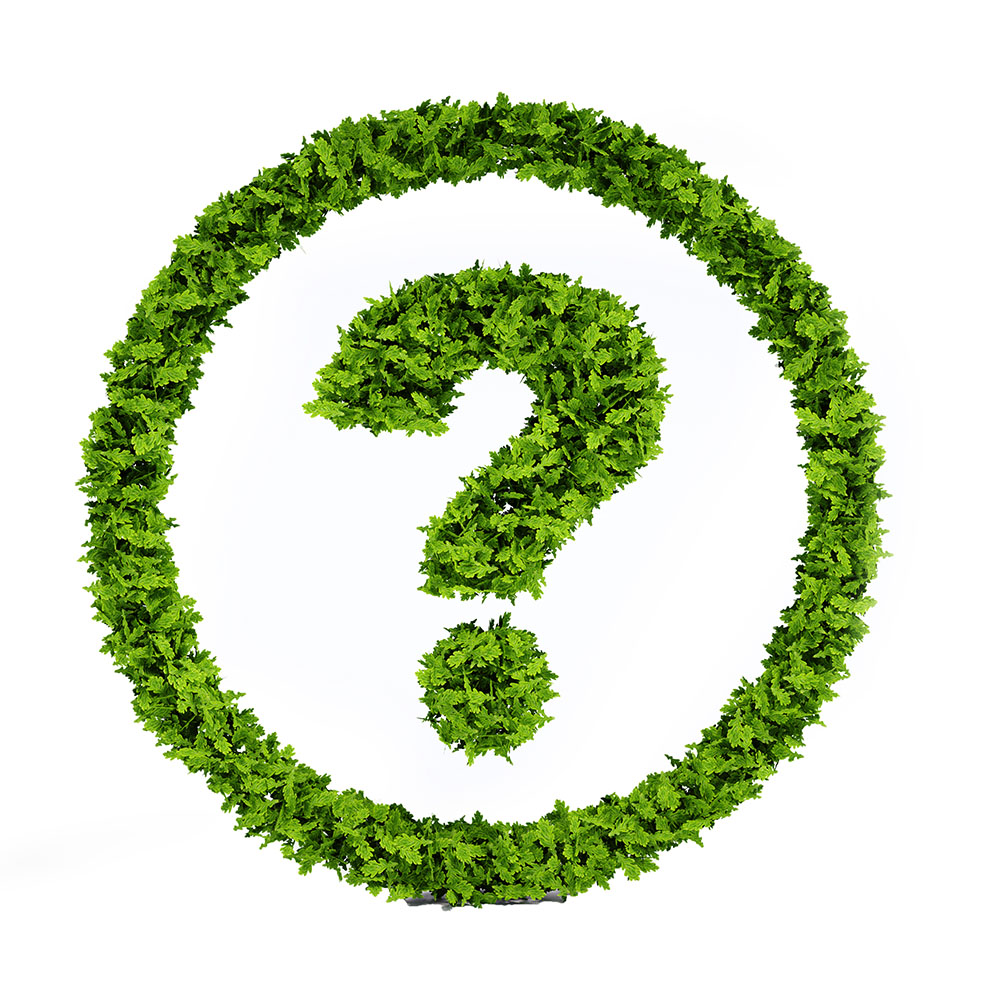
At KingStar Mold, we follow stringent quality control processes, ensuring that each fabricated assembly meets your specifications. Our team conducts regular inspections, including material checks, weld quality assessments, and dimensional verifications, to guarantee the final product’s accuracy and durability.
The lead time can vary based on the complexity and quantity of the assembly. Typically, it ranges from a few days to a few weeks, depending on the specific requirements and post-processing needs.
When selecting materials, consider the application’s environmental conditions, strength, and corrosion resistance. For example, stainless steel is ideal for corrosion-resistant applications, while aluminum is lighter and suitable for structures requiring reduced weight.
The most common materials for sheet metal assemblies include aluminum, low carbon steel, stainless steel (304/304L and 316/316L), and galvanized steel. These materials offer excellent formability, weldability, and corrosion resistance, suitable for various industries.
Yes, we specialize in custom designs and can accommodate complex geometries. Our team reviews all designs to ensure manufacturability and provides recommendations to enhance efficiency.
We implement stringent quality control measures, including regular inspections and adherence to ISO standards, to deliver consistent and high-quality results for every project.
At KingStar Mold, we emphasize precision and quality. We use advanced equipment to ensure consistent results, and our team offers design assistance to help you optimize your project for efficiency and cost-effectiveness.
Lead times typically start at five days or more, depending on project complexity and volume.