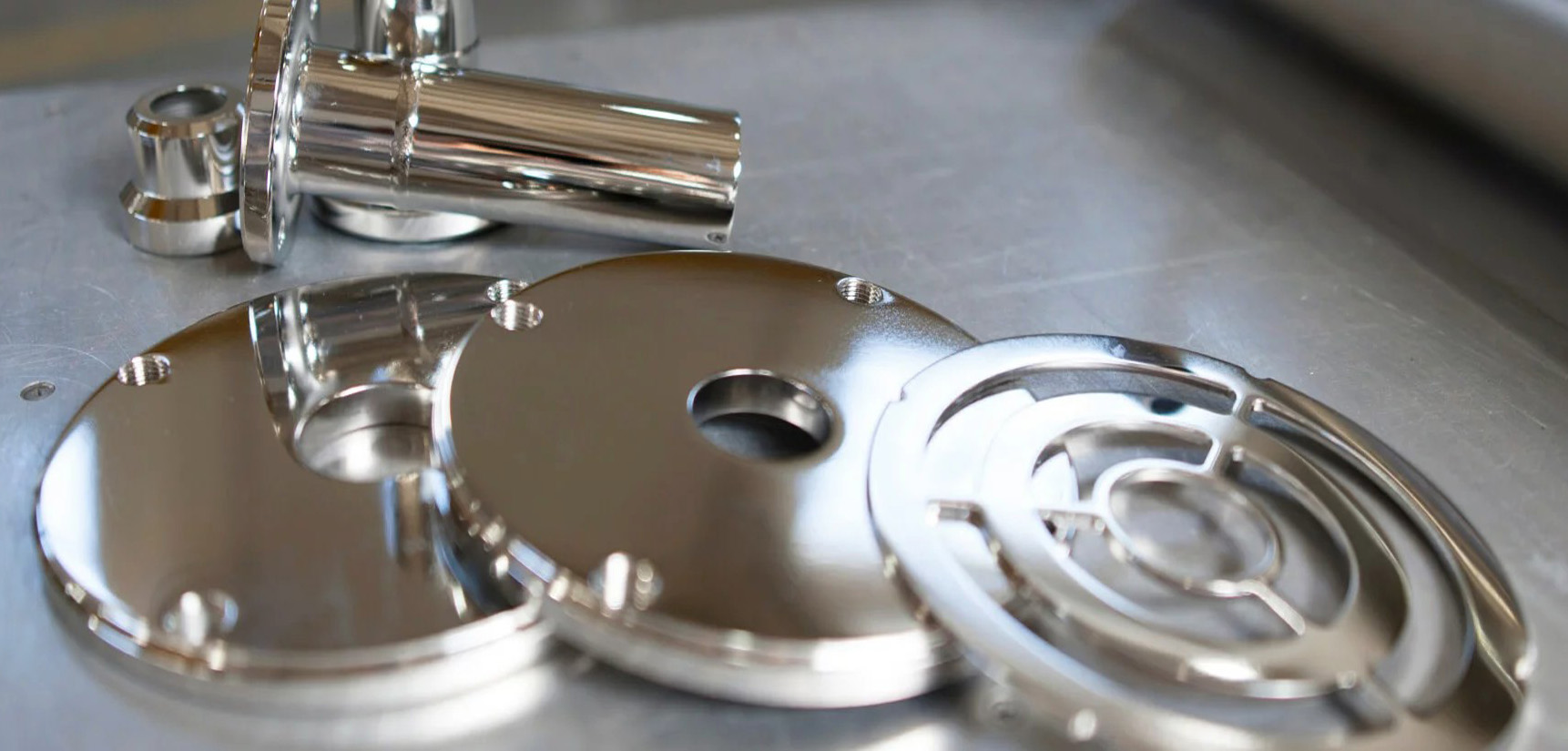
What Is Electropolishing?
How Electropolishing Works
Electropolishing, also known as electrochemical polishing, is a precision finishing process that improves metal surfaces by removing a thin, controlled layer of material. Here’s how it works:
Microscopic flaws in sensitive components—such as surgical tools, aerospace fittings, or reactor tubing—can lead to failure or contamination. Electropolishing eliminates these imperfections, enhancing function, durability, and appearance across a wide range of metals including 300- and 400-series stainless steels, aluminum, nickel, and titanium. Get a quote for our electropolishing service for metal parts — your trusted custom parts on-demand manufacturing company.
Why Electropolish Your Product?
Streamline Manufacturing and Reduce Costs
Electropolishing helps optimize part design early in development, improving manufacturability before regulatory approvals like FDA certification. By combining multiple finishing steps into one, it eliminates the need for additional polishing, passivation, or chemical cleaning—saving both time and cost throughout the part’s lifecycle.
Enhance Surface Preparation for Further Processing
Electropolished parts offer superior surface conditions for downstream processes. It improves weldability, ensures better adhesion for plating or over-molding, and prevents sticking in mold cavities. It’s also ideal for preparing parts for dye penetrant inspection and reduces the risk of hydrogen embrittlement.
Remove Machining and Heat Treatment Defects
The process removes surface contaminants like free iron, grinding residue, light rust, and embedded particles. It also eliminates defects such as microburrs, heat tint, oxide scale, EDM recast layers, and rough edges. For titanium parts, electropolishing can effectively remove alpha case, while also helping prevent galling in threaded parts.
Maximize Durability and Performance
Electropolishing significantly increases part longevity by improving fatigue strength, especially in components that bend or flex. It enhances corrosion resistance—up to 30 times better than passivation—and improves surface cleanliness to reduce contamination risks. For conductive parts like copper, it also enhances conductivity and reduces the risk of electrical arcing.
Electropolishing cannot remove deep or highly visible processing marks.
It is a fine finishing process designed to smooth and refine surfaces at the microscopic level, but it won’t eliminate heavy scratches, deep tool marks, or severe machining defects.
Electropolishing is not suitable for magnetic materials.
Ferro-magnetic metals like carbon steel do not respond well to the electropolishing process and may not achieve the desired finish or corrosion resistance.
Material Options for Electropolishing
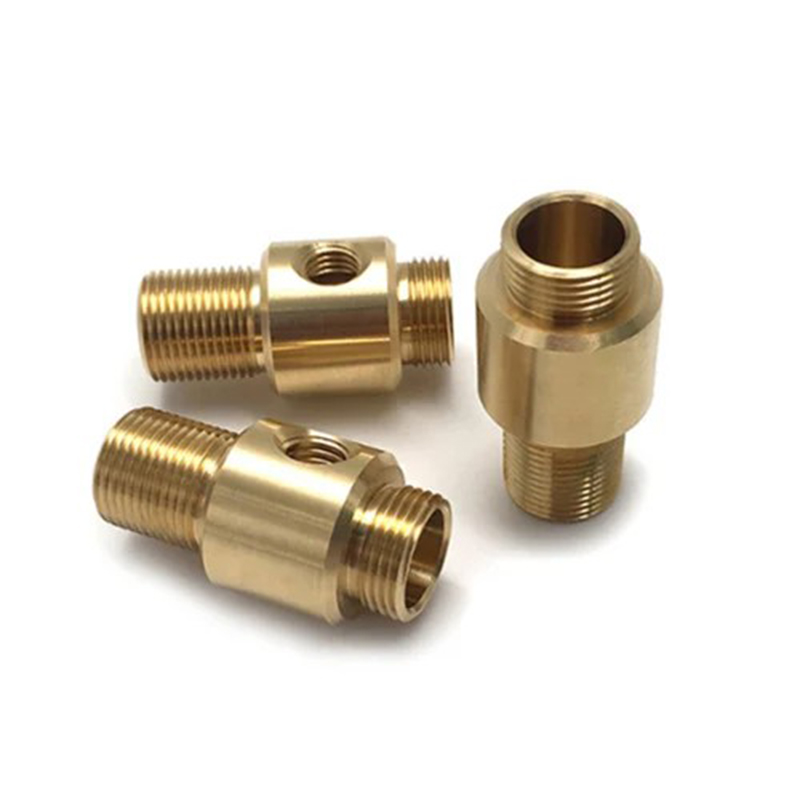
Brass
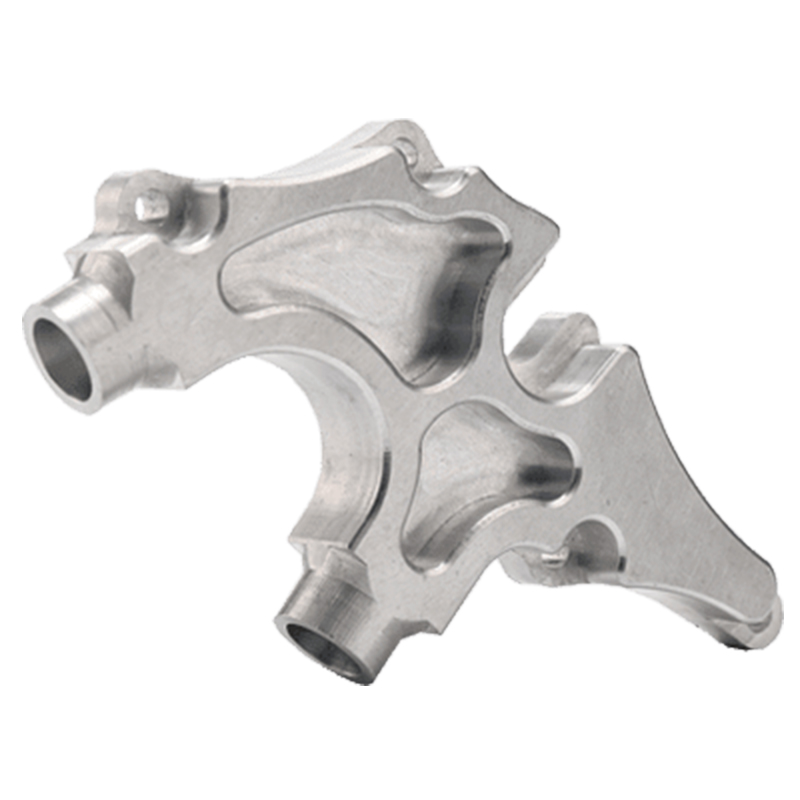
Aluminum
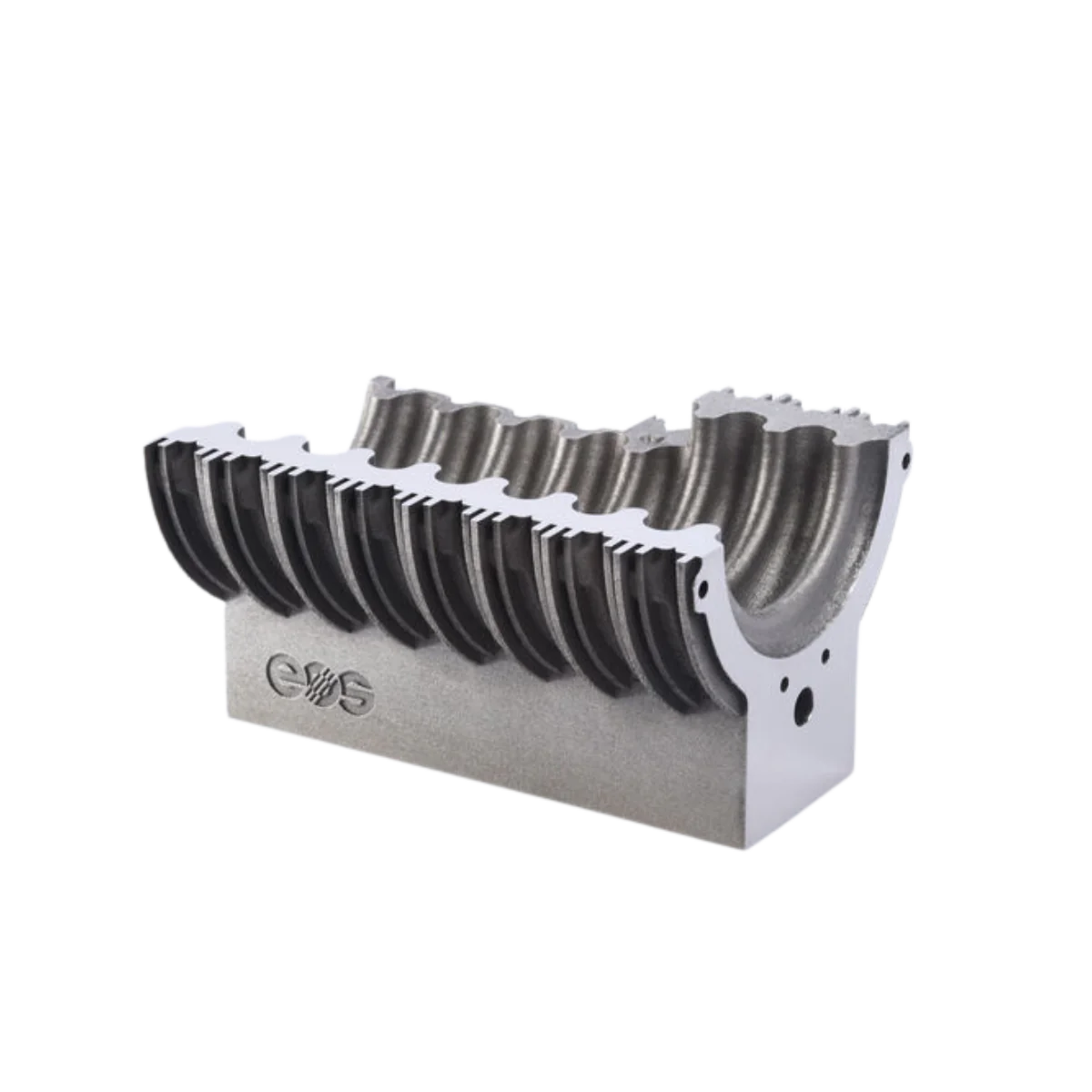
Tool Steel
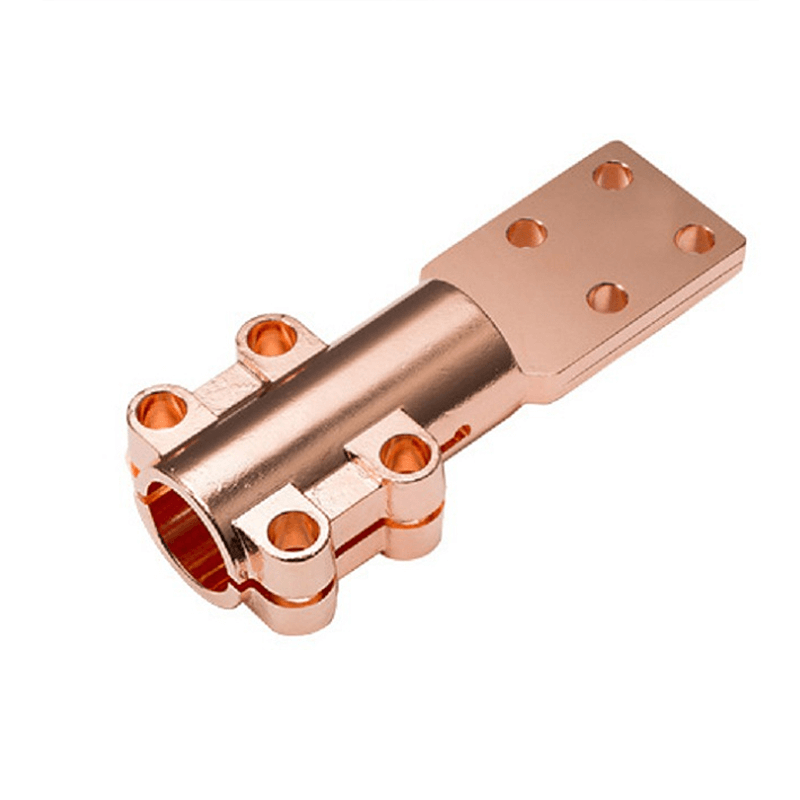
Copper
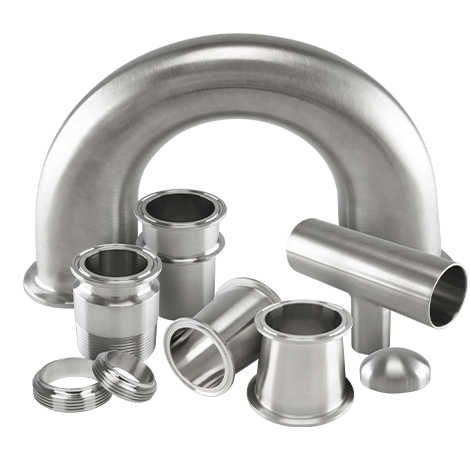
Stainless Steel
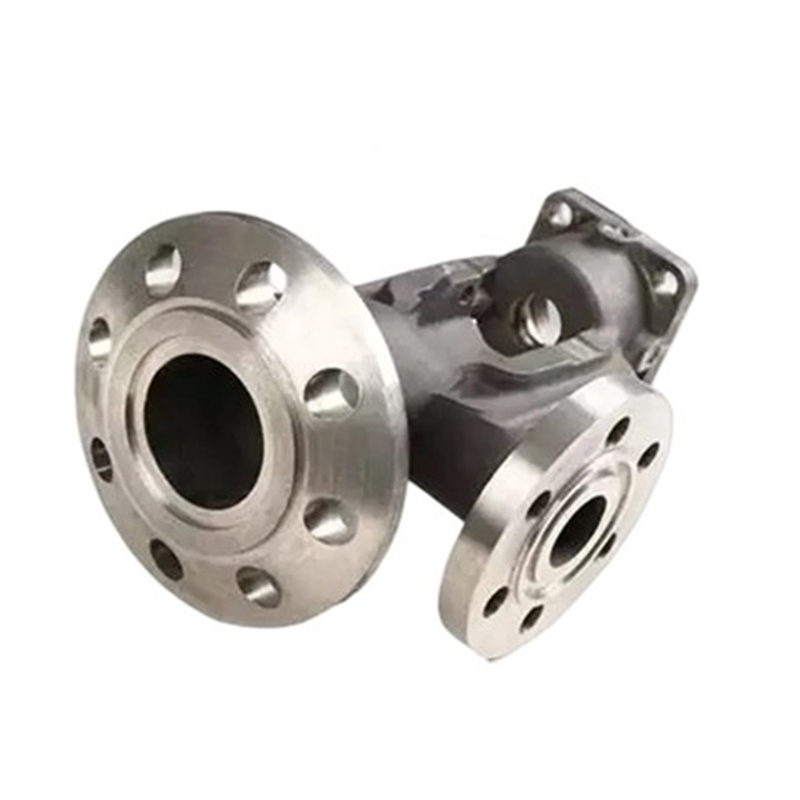
Titanium
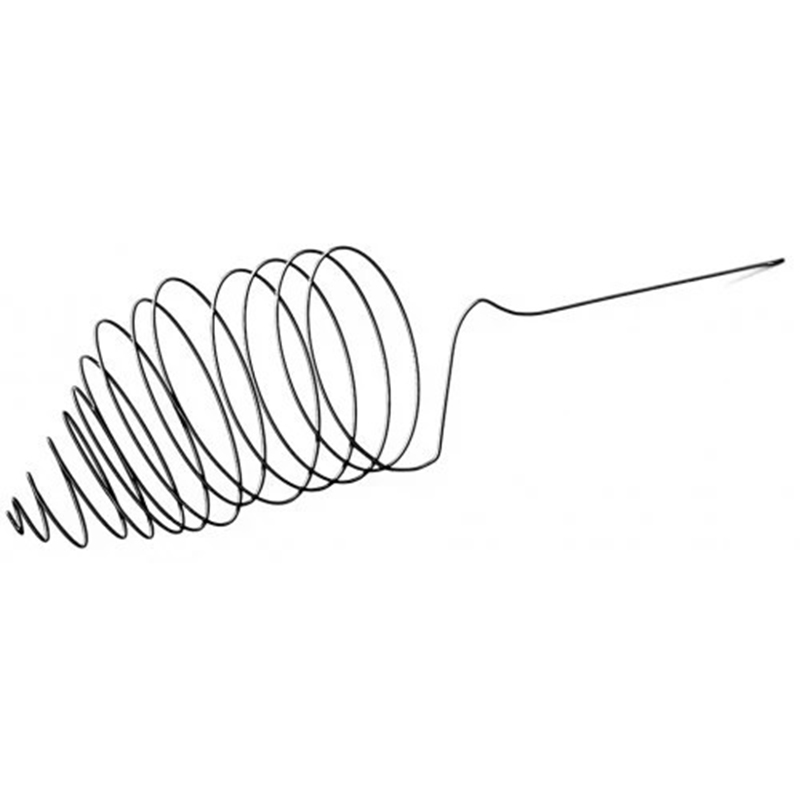
Nitinol
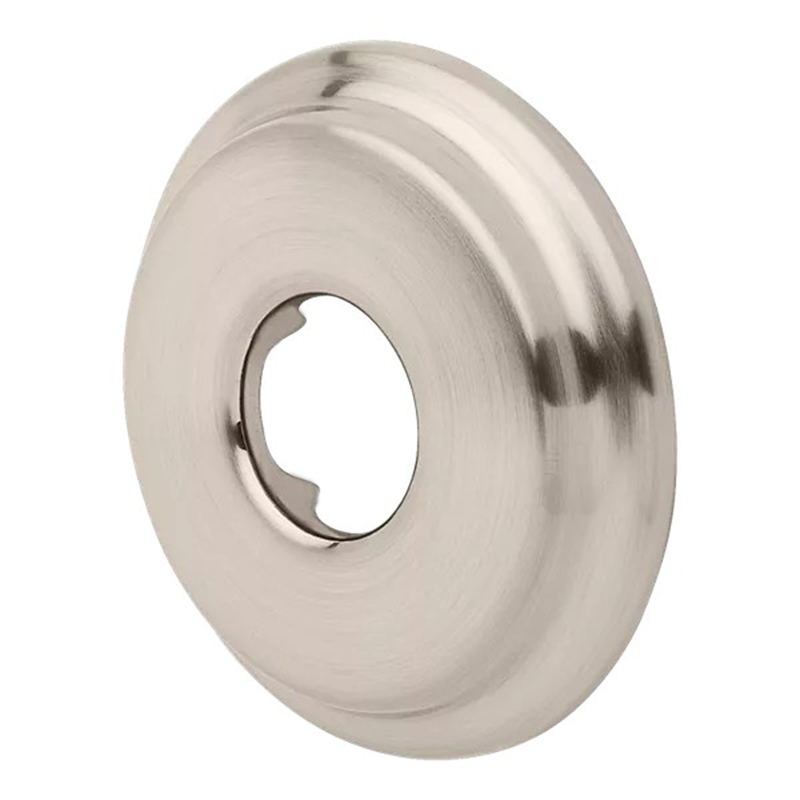
Nickel
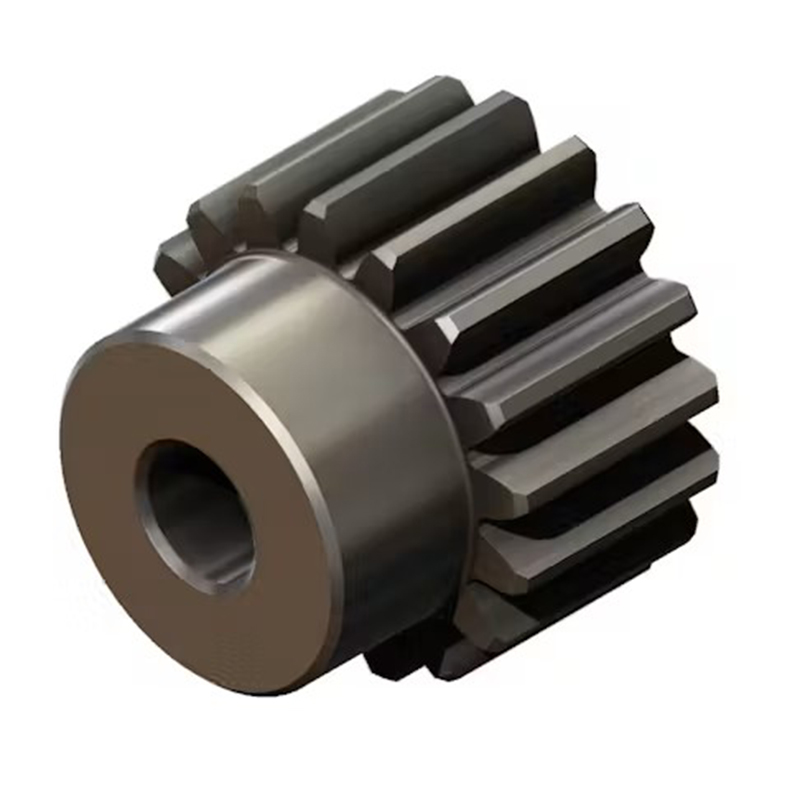
Carbon Steel
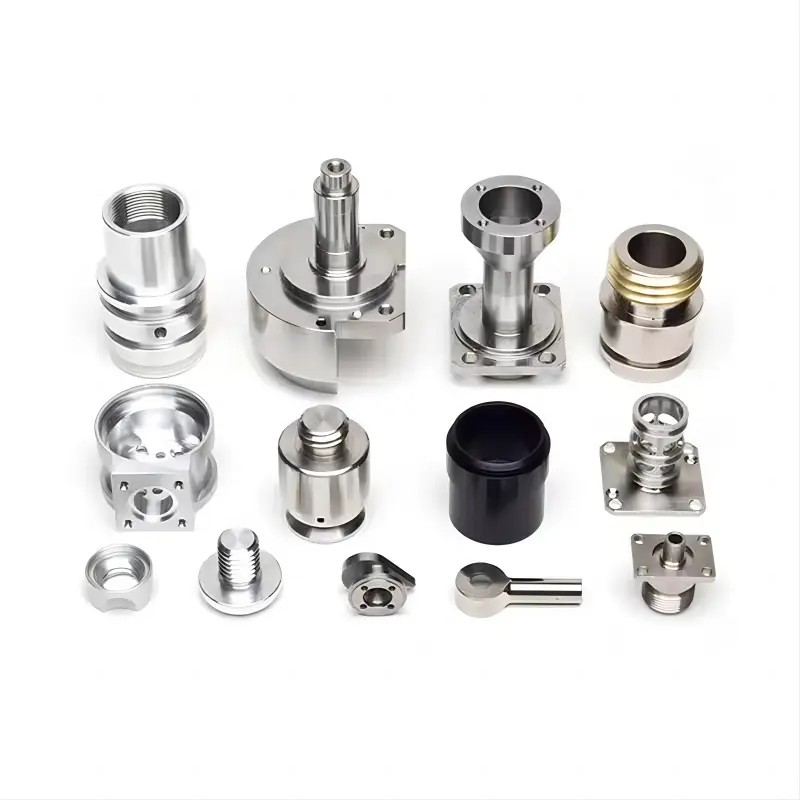
Other Metals
Electropolishing Parameters and Effect
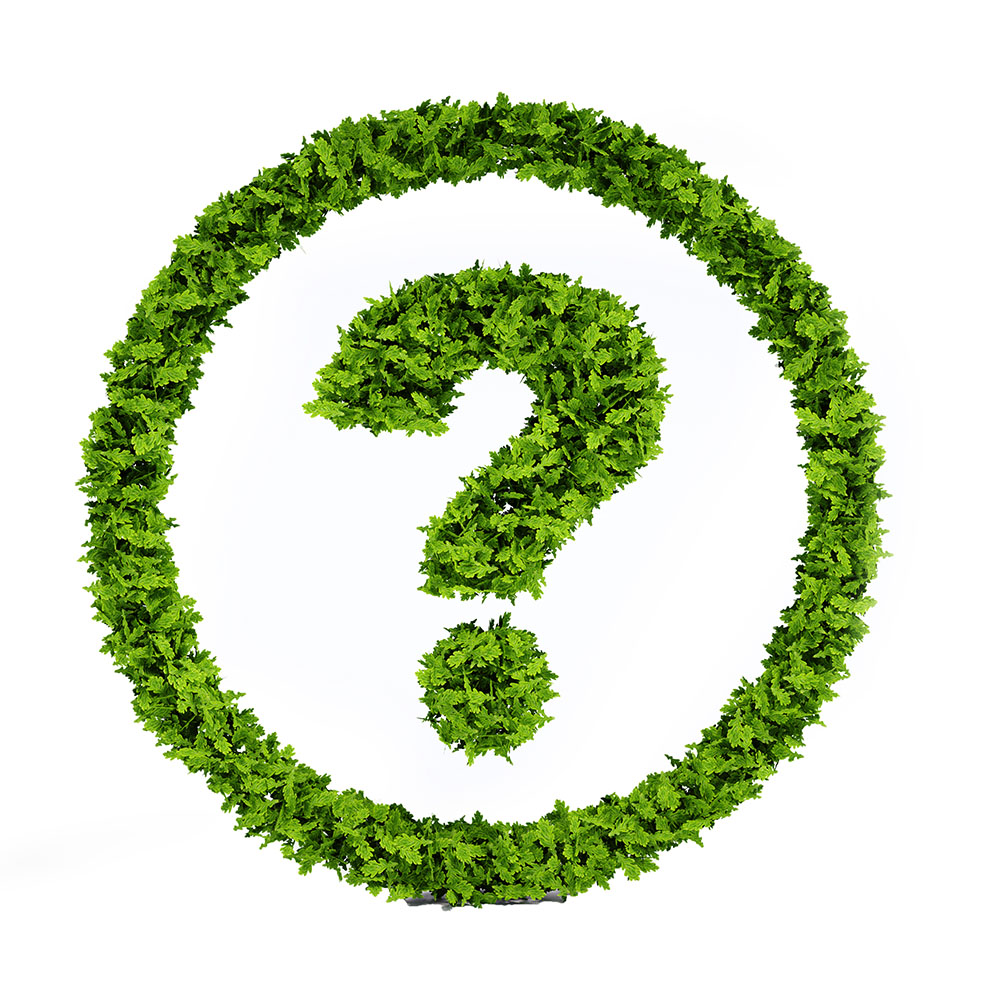
Frequently Asked Questions
Electropolishing works best on conductive, corrosion-resistant metals like stainless steel (especially 300 and 400 series), titanium, aluminum, nickel alloys, and copper. However, it is not suitable for magnetic carbon steels or metals that lack sufficient conductivity or passivity. The metal’s composition and structure must be compatible with the electrolyte solution and current used in the process to ensure safe, effective results.
Electropolishing typically removes between 0.0001 to 0.002 inches (2.5 to 50 microns) of material from the surface. The exact amount depends on factors like the metal type, part geometry, surface condition, and processing time. The process is precise and controlled, making it ideal for parts requiring tight dimensional tolerances and smooth finishes.
Electropolishing is designed to smooth surfaces at a microscopic level, so it can remove light surface imperfections and burrs. However, it will not eliminate deep scratches, heavy tool marks, or major surface defects. For parts with those features, pre-polishing or surface preparation may be needed.
While mechanical polishing uses abrasives to physically grind the surface, electropolishing removes metal through an electrochemical reaction, producing a smoother, cleaner, and more uniform finish—especially in hard-to-reach or intricate areas where mechanical tools can’t access.