Cooperative Partners
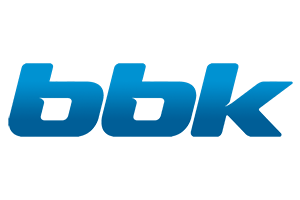
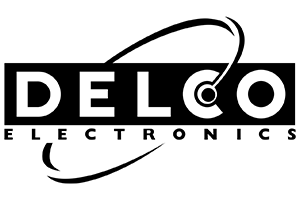
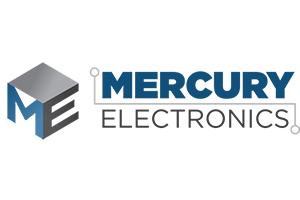
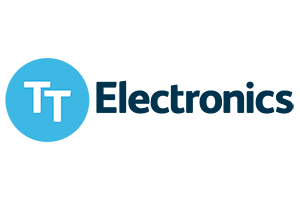
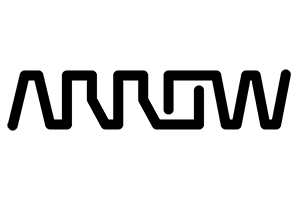
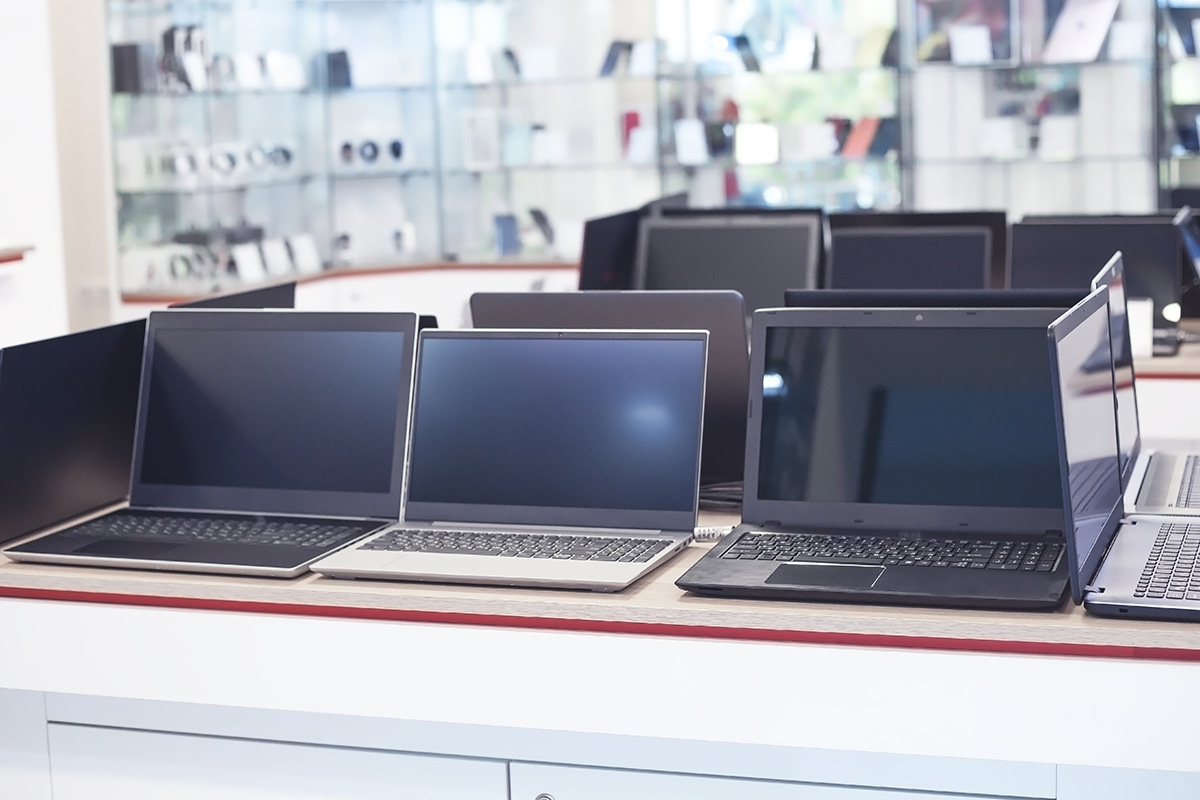
Customizable Solutions of Electronic Components Manufacturing
Proven Track Record in High-Precision Mold Making
Extensive Experience in Electronic Components Manufacturing
Trusted Expertise in Precision Electronics Production
At KingStar Mold, our team of experts is dedicated to providing high-quality services, including product design, mold design, injection molding, and other advanced manufacturing techniques. We offer a complete, one-stop solution for all your consumer electronics mold needs.
We specialize in a variety of custom plastic molds for consumer electronics, including:
What We Can Make for You
Electronic Components Manufacturing Capabilities
Most consumer electronic products you encounter daily are made from metal and plastic, which are materials Firstmold specializes in. With over ten years of experience in continuous processing, we have developed a deep understanding of the industry and can offer tailored processing solutions to meet your needs.
Note:
Due to NDAs signed with many clients, we are only able to display a select few products from the consumer electronics industry after obtaining explicit consent through communication with our clients.

Audio & Video Equipment
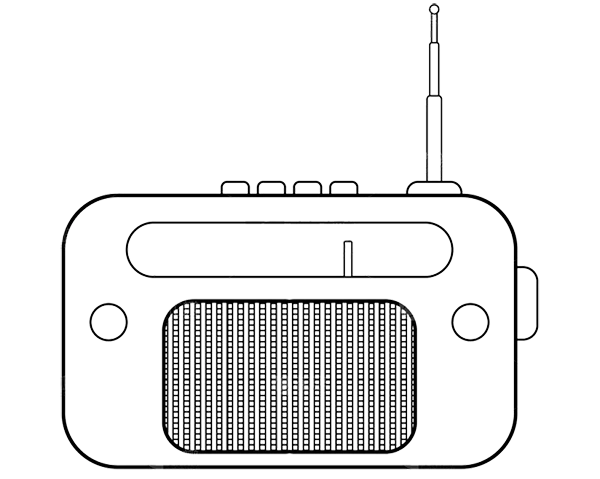
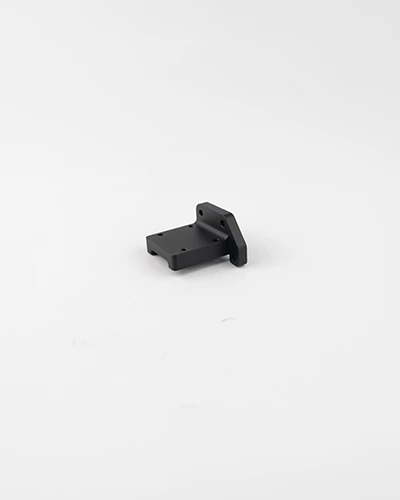
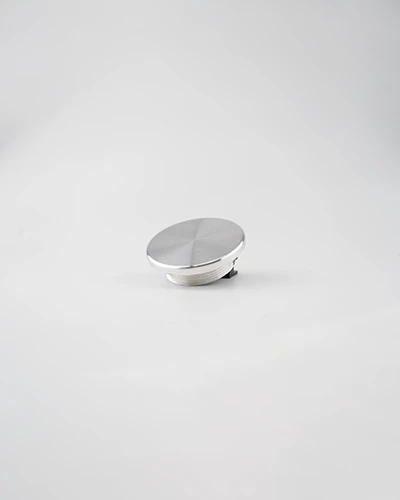
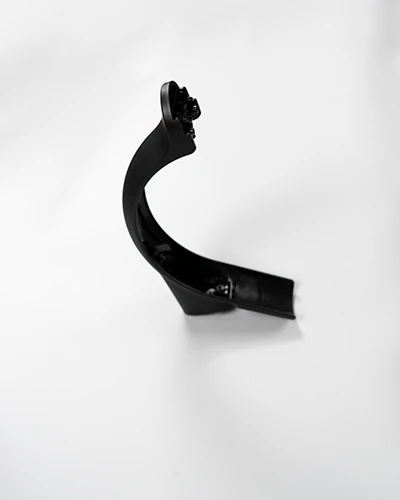

Gaming & Entertainment
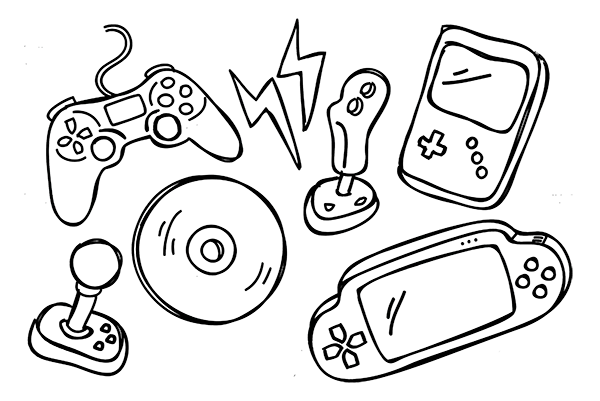
Why Choose KingStar As Your Partner
Materials For the Electronic Components
Material selection plays a crucial role in creating durable, high-performing, and visually appealing devices in today’s fast-evolving consumer electronics market. At KingStar Mold, we view each material as a unique asset. We work with advanced plastics and metals that are meticulously engineered to meet the rigorous demands of the environments in which the end products will be used.
We take material integrity very seriously, providing detailed certificates to assure the exceptional quality of our materials. Additionally, if clients prefer to source materials from their own suppliers, we remain fully adaptable and can accommodate those preferences, ensuring the materials perfectly match project specifications.
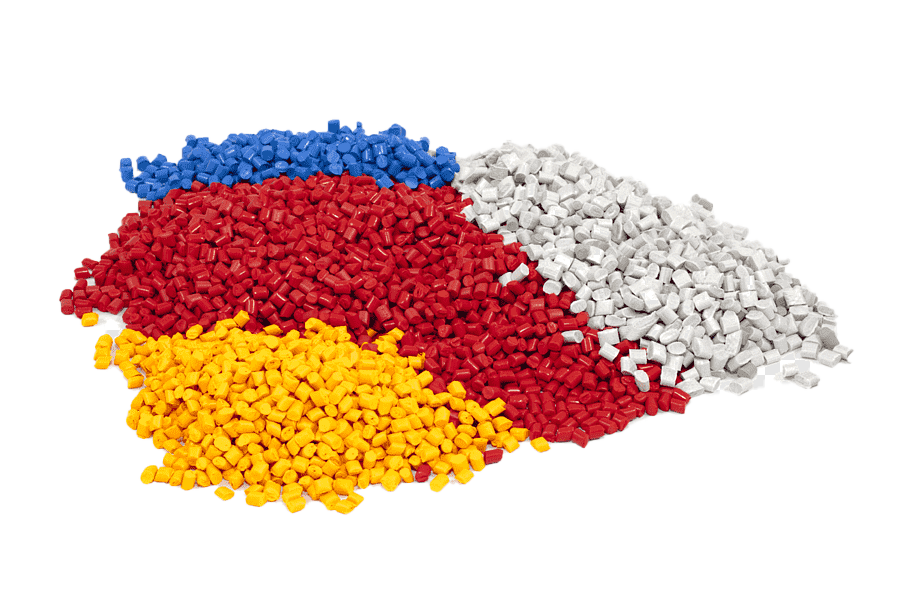
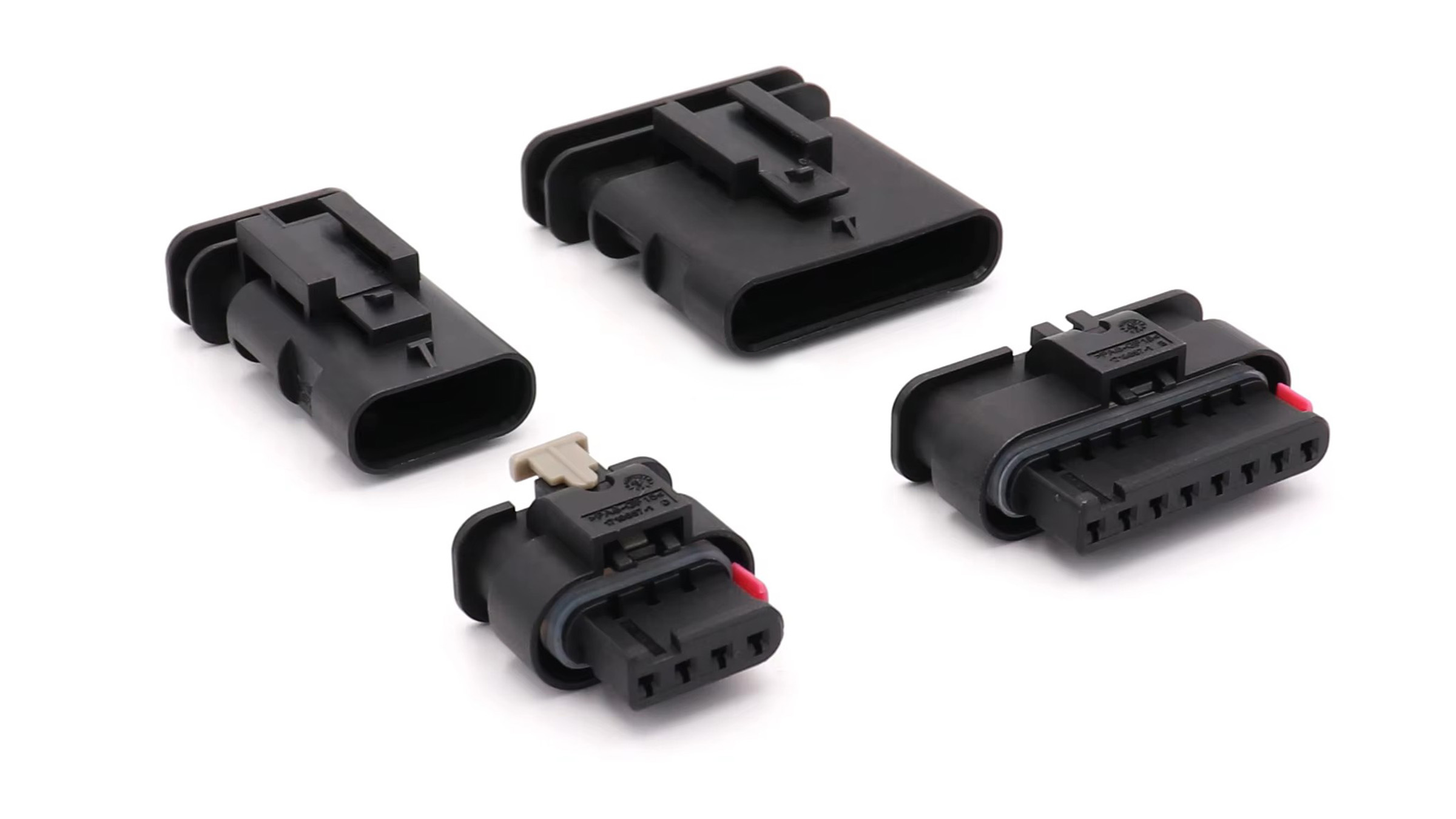
PBT
Used for components such as connector housings, power supply enclosures, sensor brackets, switch bases, and compact motor casings in small appliances and consumer electronics.
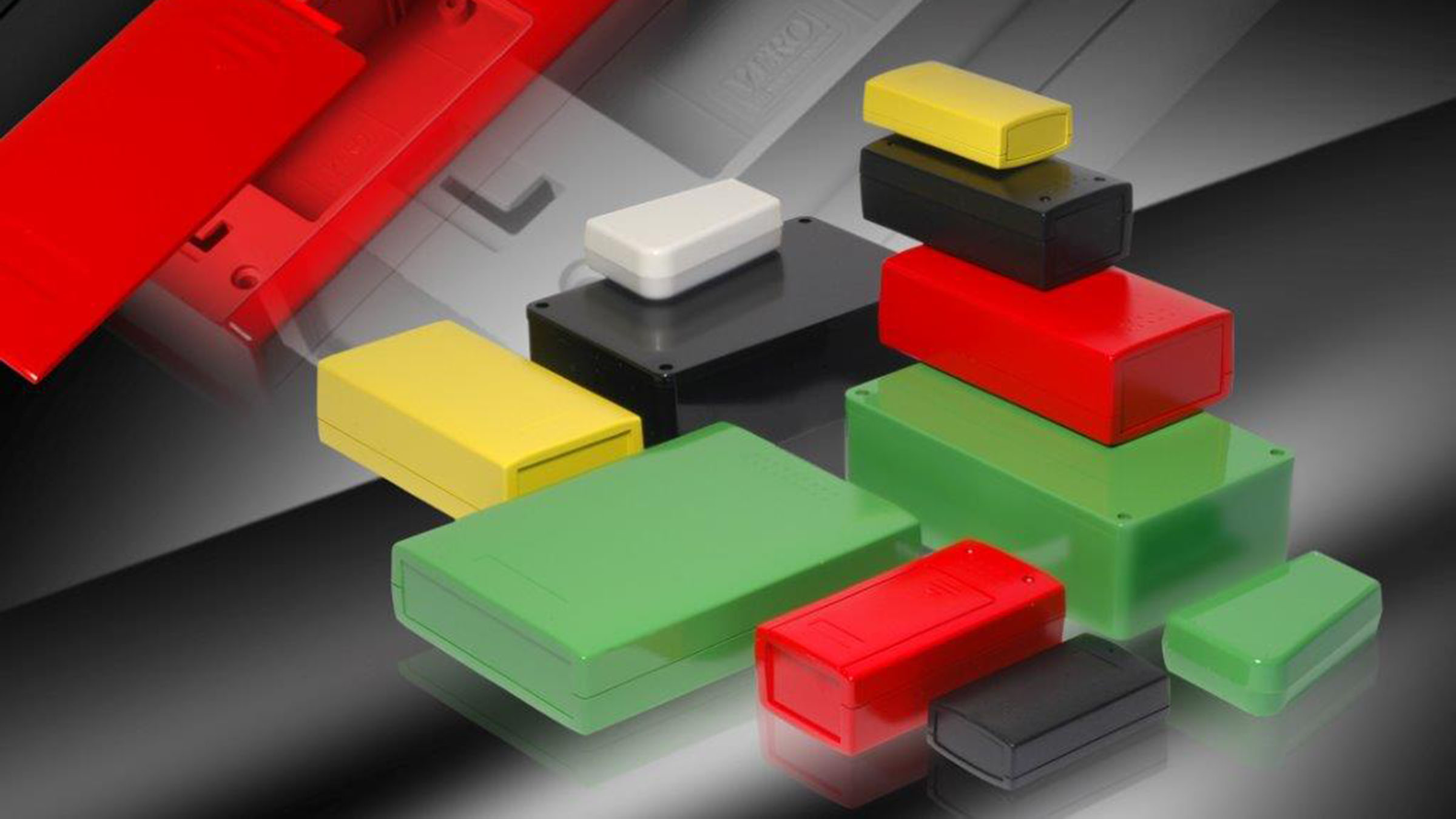
ABS
Commonly used for parts like remote control shells, keyboard frames, monitor housings, charging dock casings, and lightweight structural components in various consumer electronics.
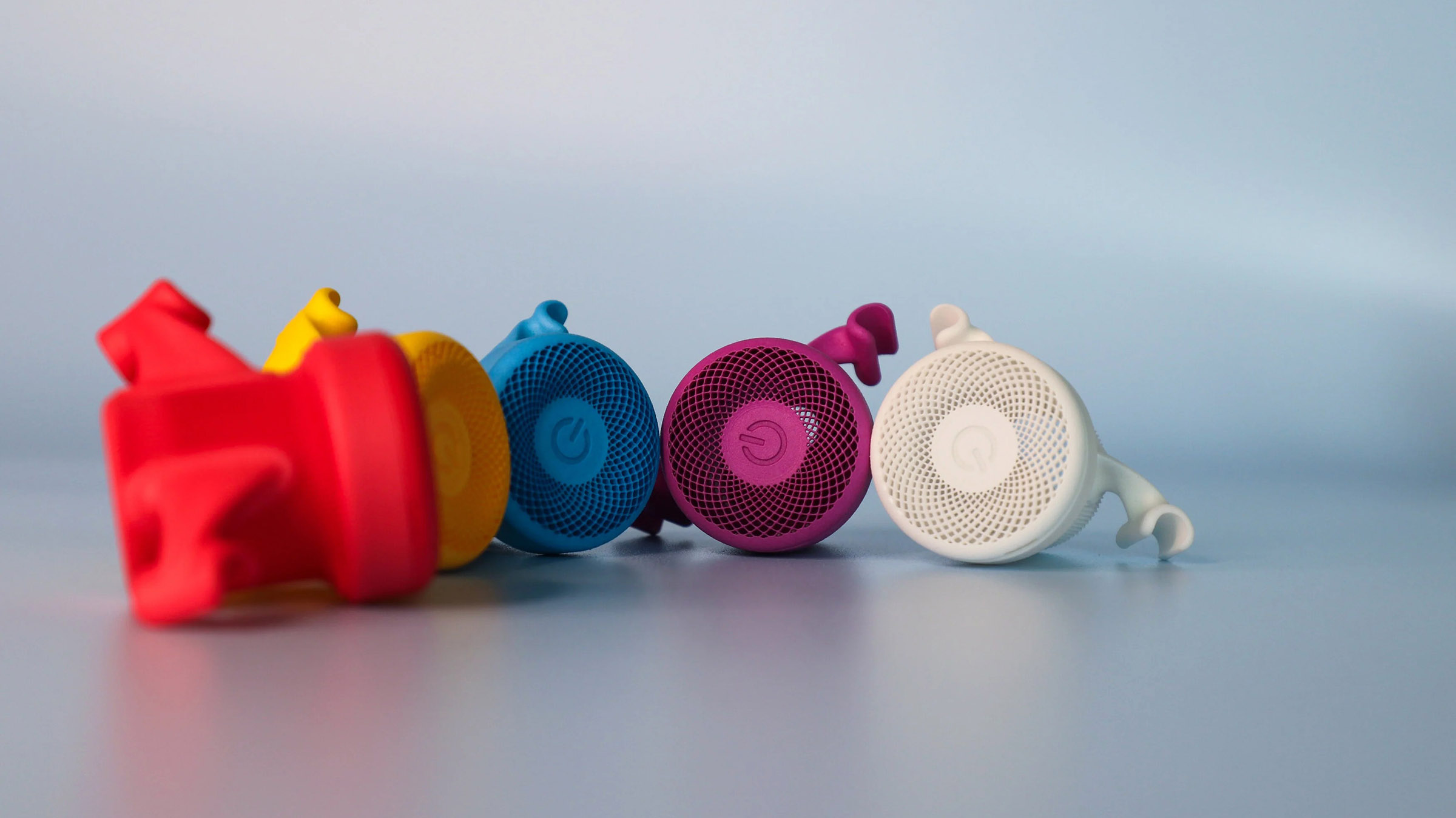
PA
Ideal for components requiring strength and wear resistance, such as gear assemblies in printers, motor housings in electric shavers, cable ties in power units, and internal brackets in handheld electronics.
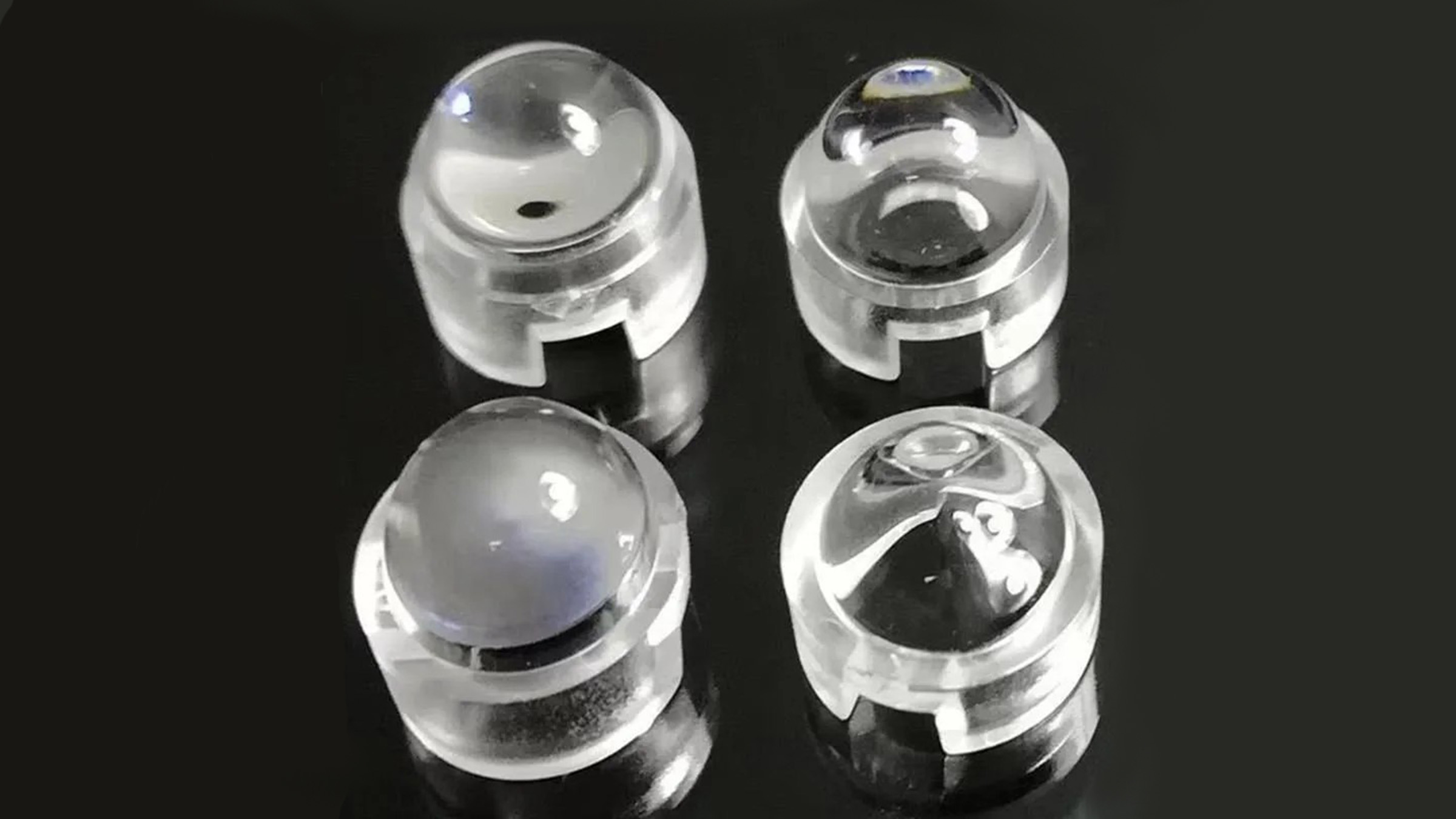
PMMA
Commonly used for transparent or glossy parts, such as LED light covers, display screens, smartphone windows, and indicator panels in home appliances.
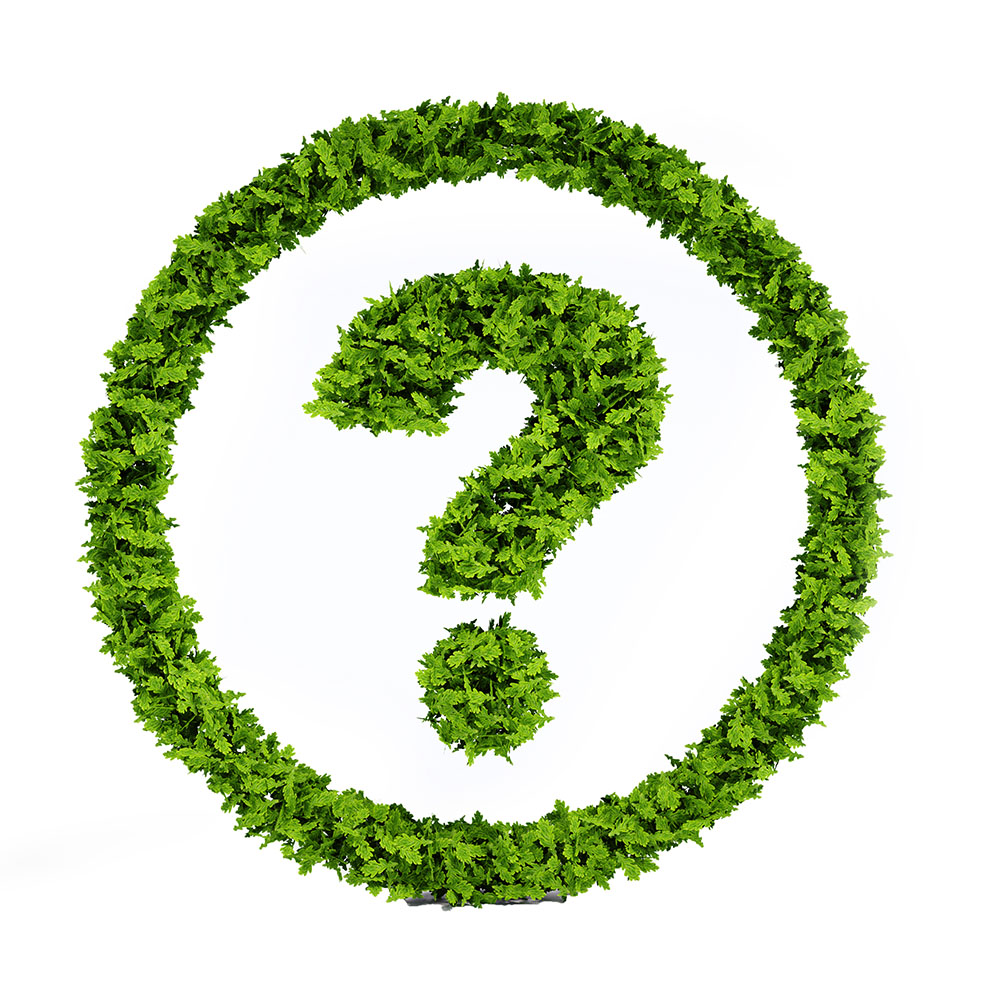
Frequently Asked Questions
Yes, KingStar Mold offers comprehensive design support to help you turn your ideas into functional, manufacturable parts. Our design team works closely with you to refine concepts, ensure manufacturability, and optimize performance. We also provide prototyping services to validate designs before moving to mass production, ensuring that your parts meet all requirements.
Lead times for custom electronics parts vary depending on the complexity of the design, material availability, and production volume. For prototypes, the lead time can range from a few days to a couple of weeks. For mass production, it typically takes several weeks to a few months. We work closely with clients to establish realistic timelines based on their specific needs.
Yes, KingStar Mold offers end-to-end solutions, from rapid prototyping to low- and high-volume production. We ensure seamless scaling from prototypes to mass production while maintaining consistent quality. Our team utilizes flexible manufacturing methods to accommodate both small and large production runs efficiently.
At KingStar Mold, quality is a top priority. We follow strict quality control procedures that include detailed inspections, material testing, and certifications. Our team conducts rigorous checks throughout the manufacturing process to ensure each part meets the required specifications. We also provide advanced inspection reports, material certifications, and certificates of conformity to ensure transparency and quality assurance.
KingStar Mold can manufacture a wide range of custom electronics parts, including enclosures, connectors, housings, heat sinks, and other precision components designed for electronic devices. We specialize in creating parts that require high precision, durability, and functionality, utilizing various materials and advanced production techniques like injection molding, CNC machining, and 3D printing.