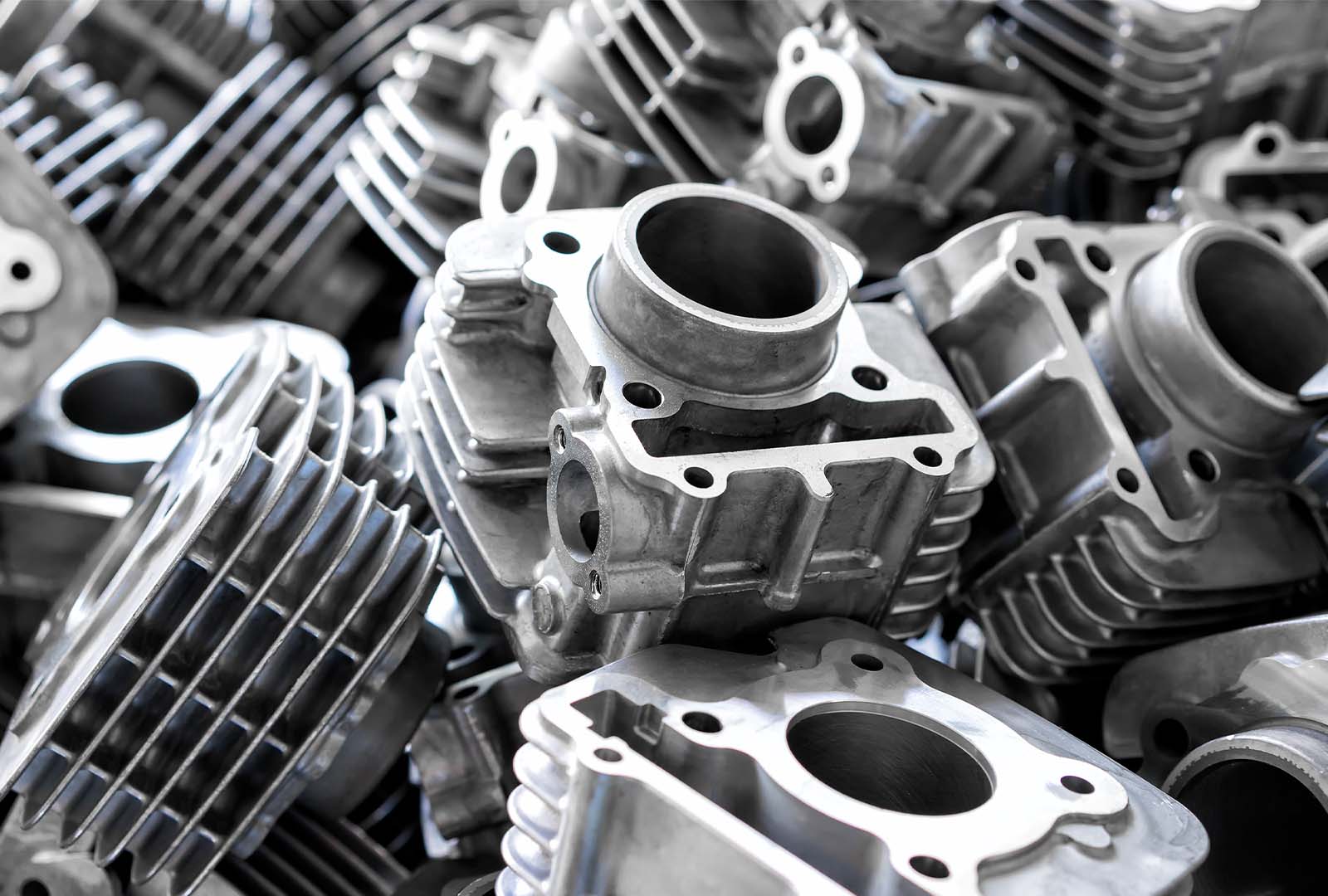
What Is Die Casting?
Die casting is a manufacturing process used to produce high-precision metal parts in large quantities. Molten metal is injected under high pressure into a metal mold, or die, which is typically made of steel. The metal cools and solidifies to form the desired shape, making this process ideal for producing parts with complex designs and fine details. It is widely used in industries like automotive, aerospace, and electronics due to its accuracy, smooth surface finishes, and consistency.
There are two main types of die casting: hot chamber and cold chamber. Hot chamber die casting is used for metals with low melting points, such as zinc and magnesium, while cold chamber die casting is suited for higher melting point metals like aluminum and brass. Both methods offer high precision and strength, though cold chamber die casting requires a separate melting process due to the higher temperatures involved.
Key Benefits of Choosing KingStar
High Precision and Expertise
Fast Turnaround and Competitive Pricing
Comprehensive One-Stop Service
KingStar Mold’s Die Casting Services
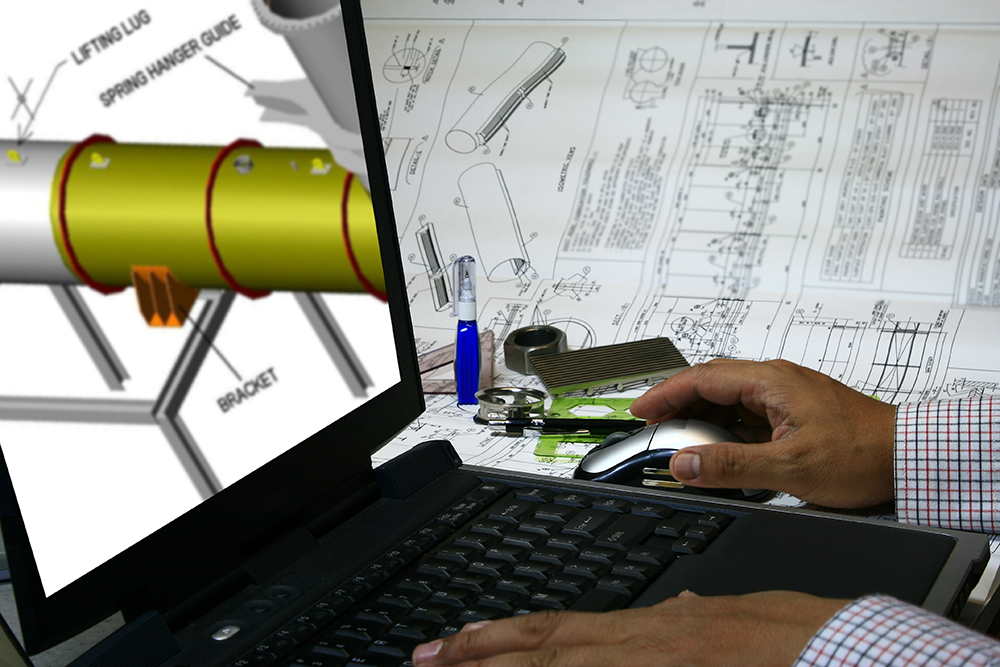
CAD Engineering
KingStar Mold offers advanced CAD engineering services to create precise 3D models and prototypes for your metal parts. Our team utilizes cutting-edge CAD software to design and optimize components for enhanced performance and manufacturability.
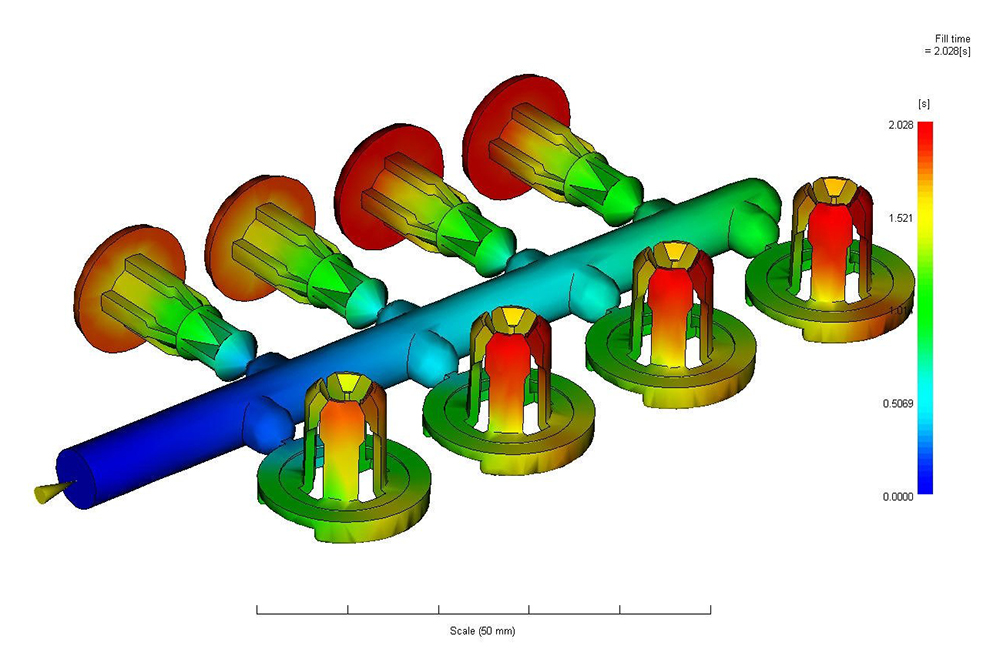
Flow Simulation Analysis
Our flow simulation analysis service mimics the die-casting process to detect potential defects and enhance design efficiency. By employing state-of-the-art simulation tools, we ensure the ideal distribution of molten metal, preventing issues such as cold shuts and air entrapment.
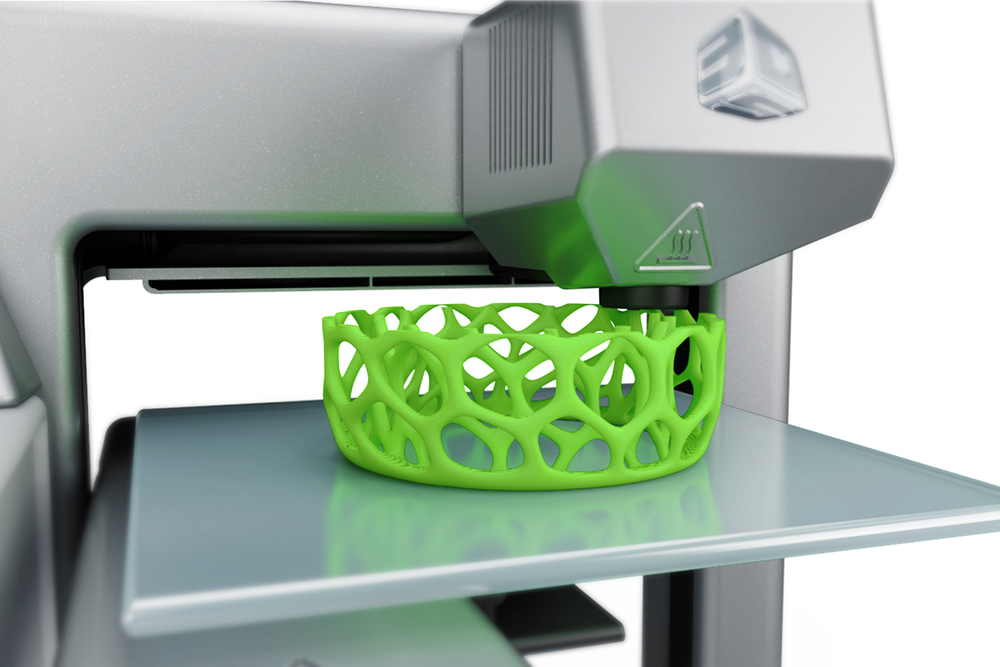
Rapid Prototyping
We utilize rapid prototyping techniques, including 3D printing, to create prototypes and test die-cast metal parts before full-scale production. This allows for faster iterations of complex designs, shortening development times and improving accuracy.
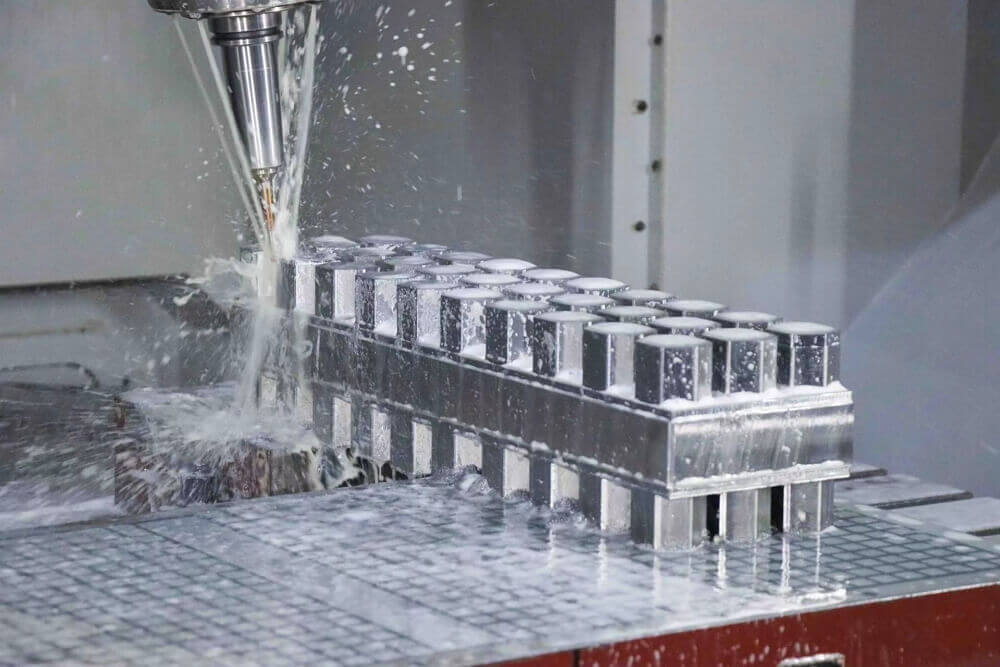
CNC Machining
KingStar Mold offers CNC machining services that produce highly accurate, intricate die-cast metal parts with tight tolerances. Our advanced CNC machining ensures consistent quality and efficient production of metal components for your products.
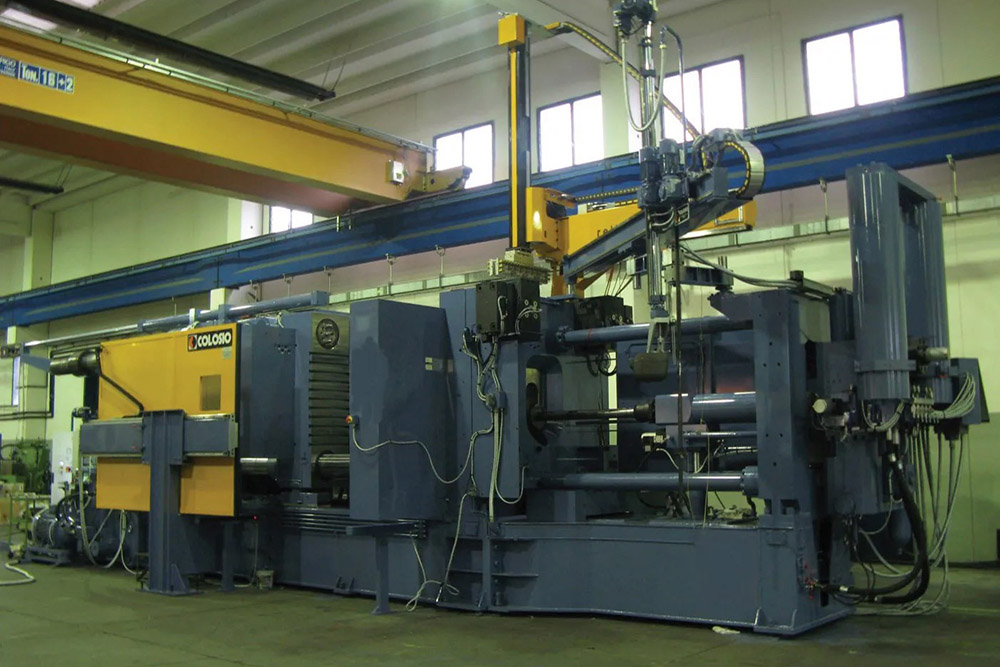
Die Casting Production
Our die-casting services facilitate the mass production of high-quality metal parts with complex geometries and fine details. We specialize in providing fast, cost-effective solutions for manufacturing durable, high-volume metal components.
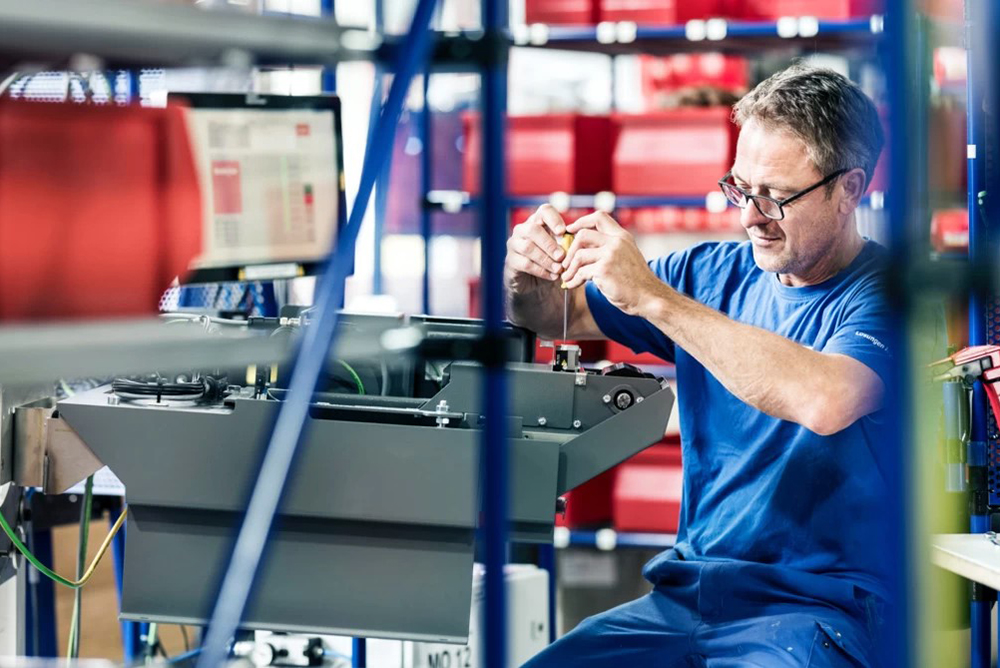
Surface Finishing & Assembly
We offer a comprehensive range of surface finishing services, including polishing, coating, and more, to improve the performance and appearance of die-cast metal parts. Our assembly services guarantee that each component is assembled with precision, ready for seamless integration into the final product design.
All-in-one die casting solutions for precision, tight-tolerance parts
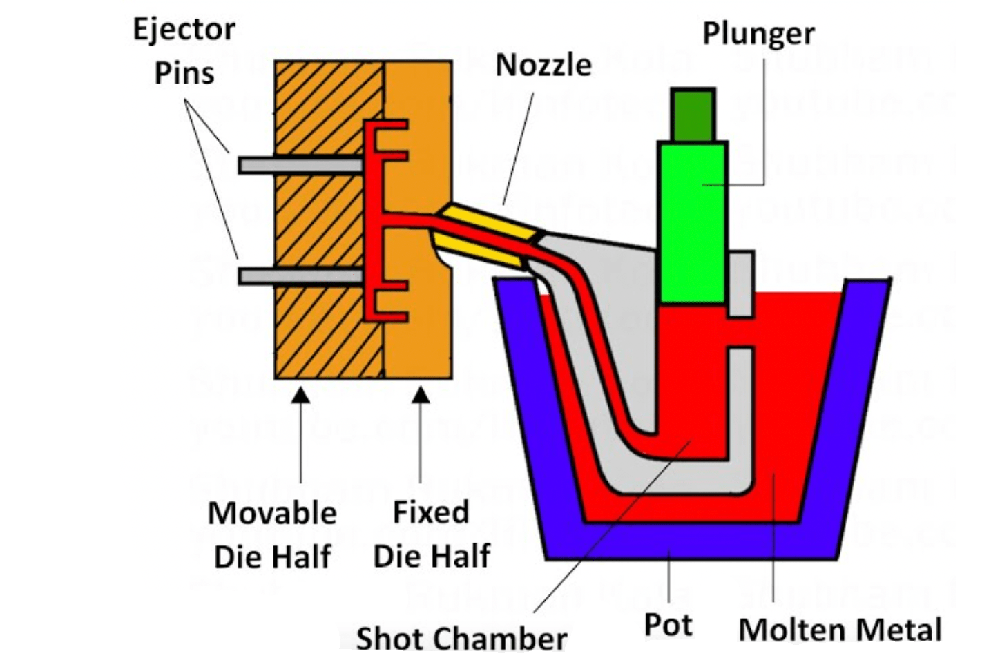
Hot Chamber Die Casting
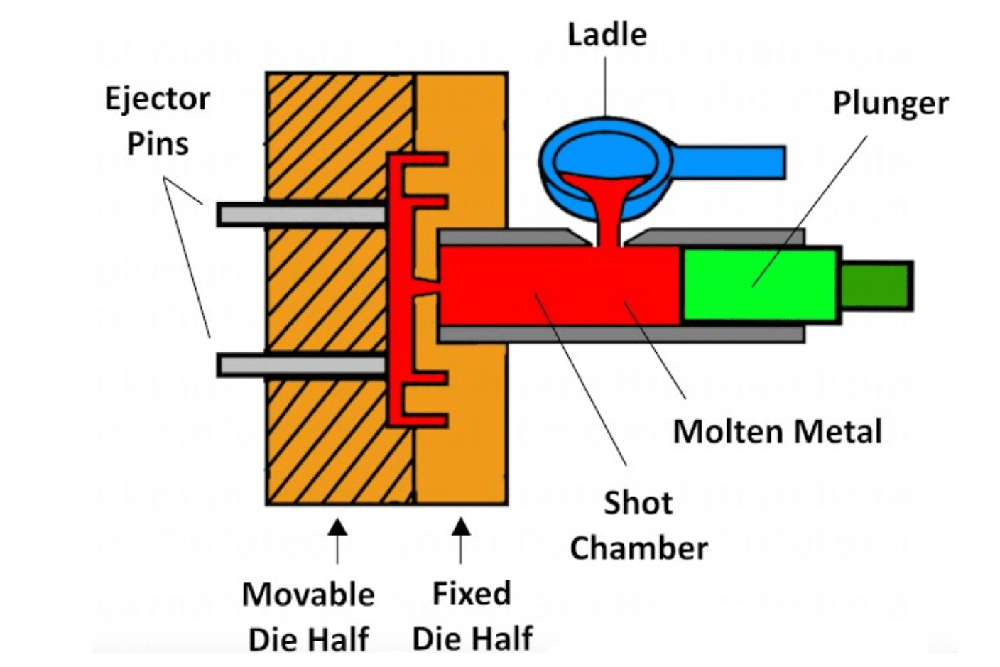
Cold Chamber Die Casting
Die Casting Materials
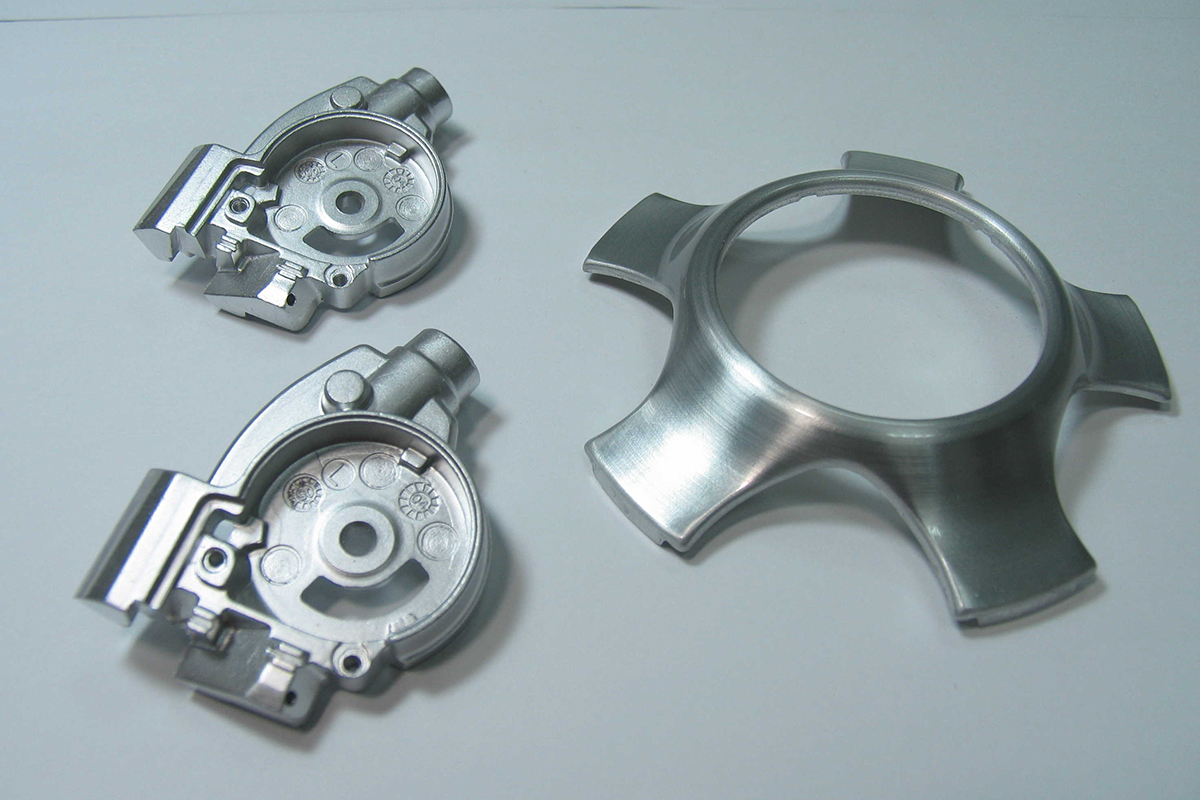
Magnesium Die Casting
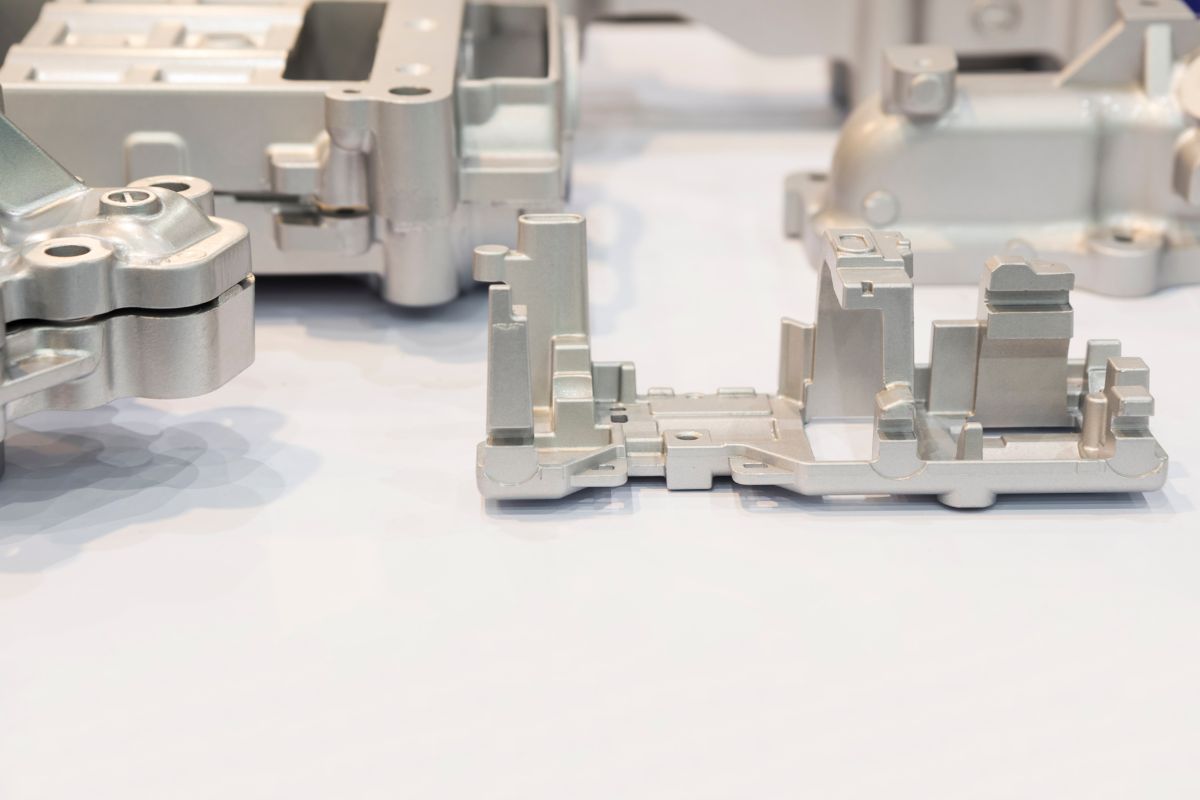
Zinc Die Casting
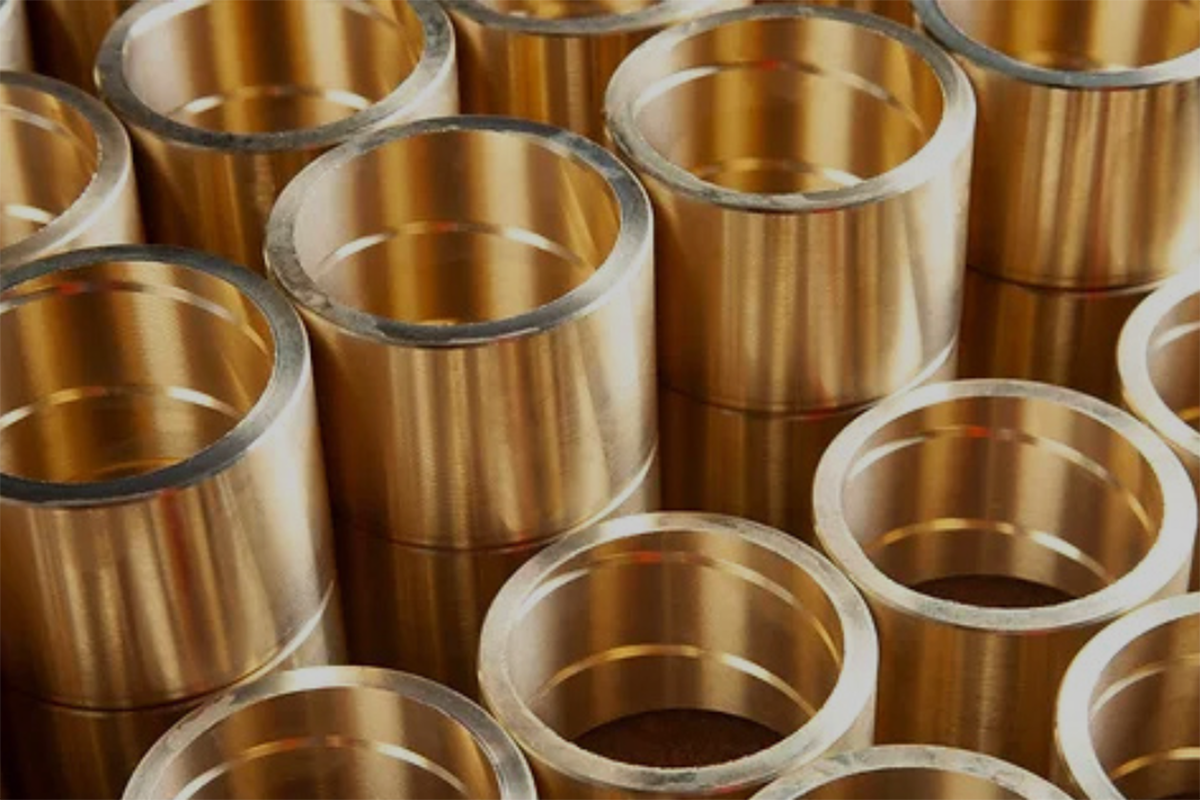
Copper Die Casting
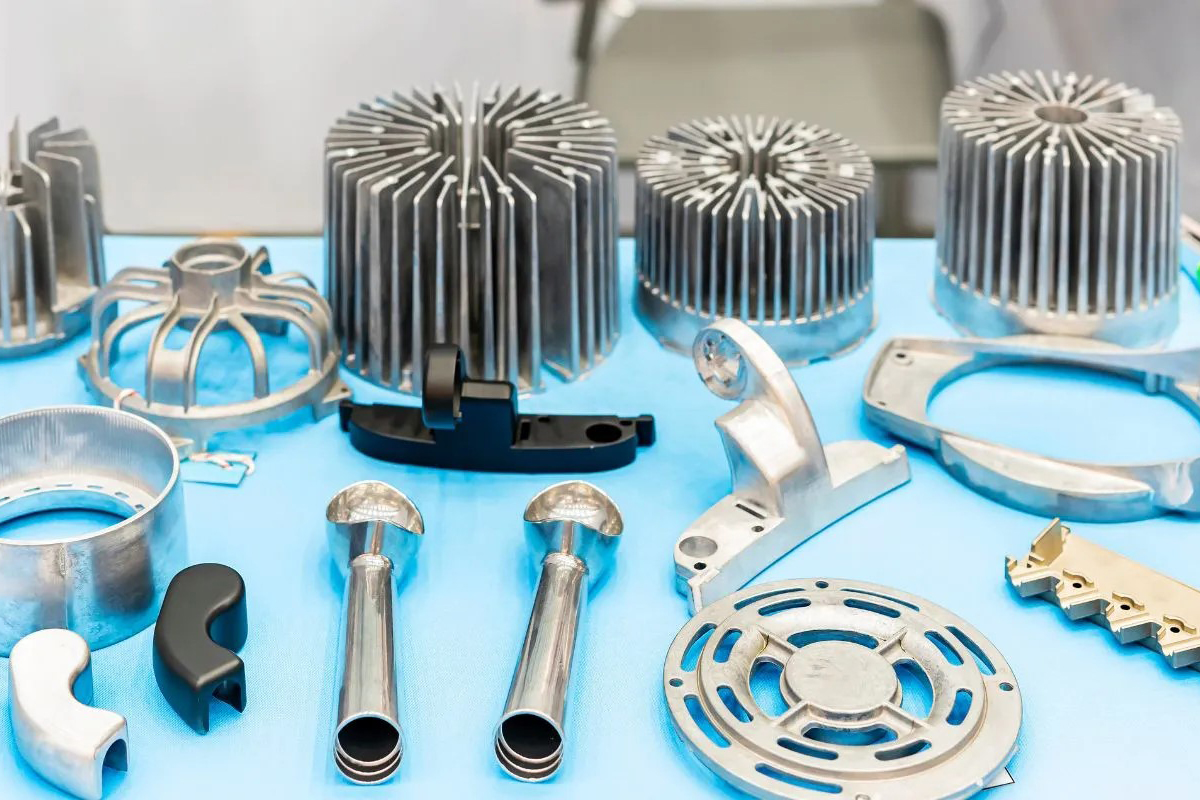
Aluminum Die Casting
Previous Projects
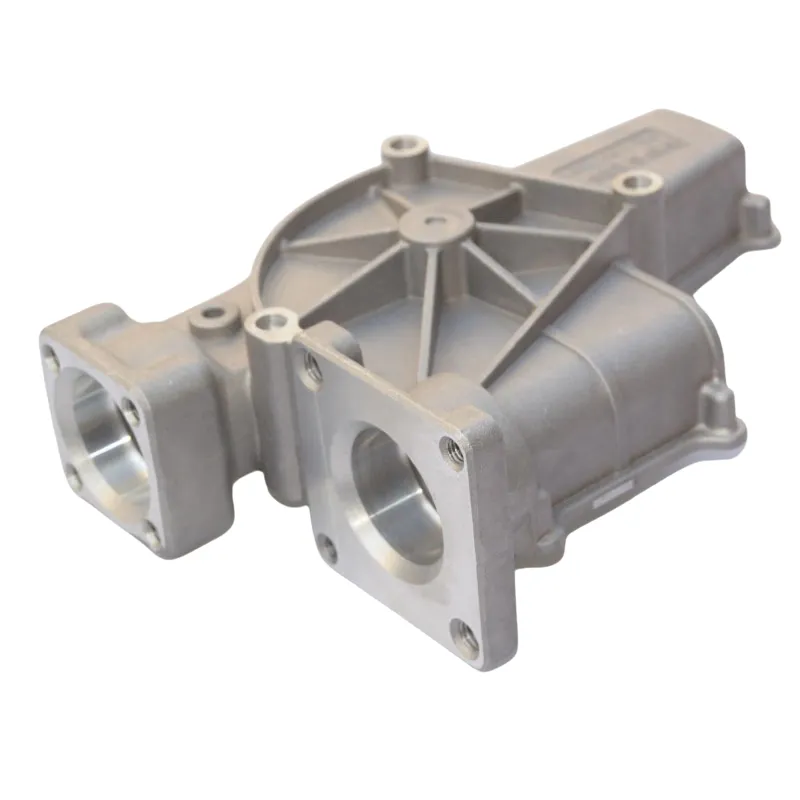
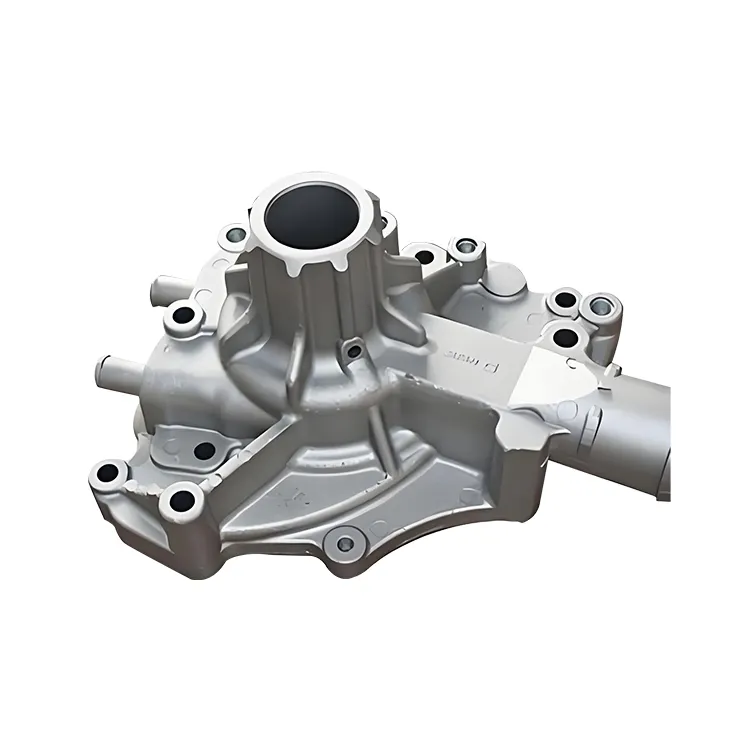
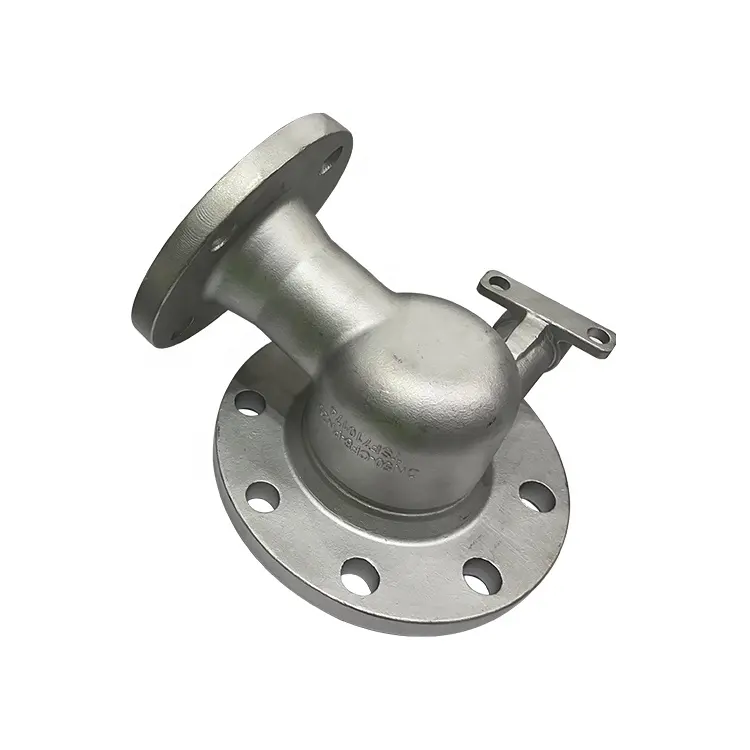
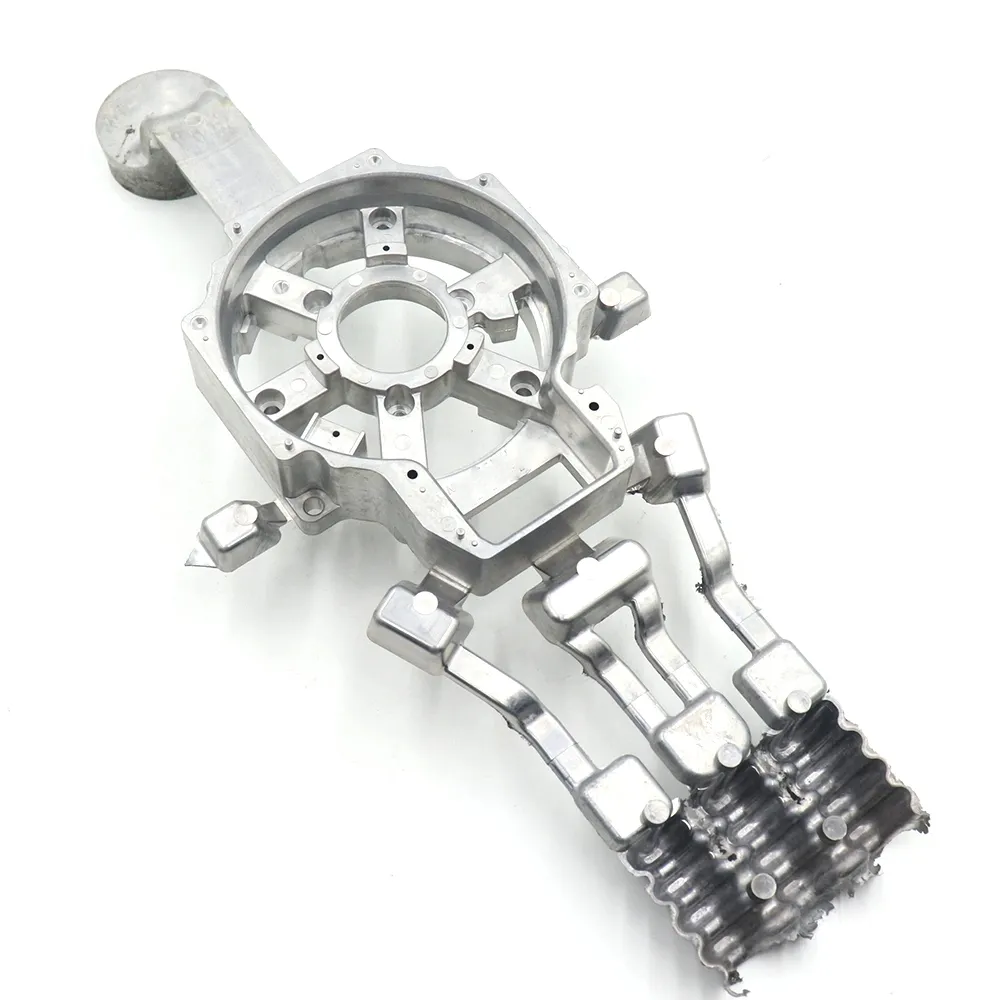
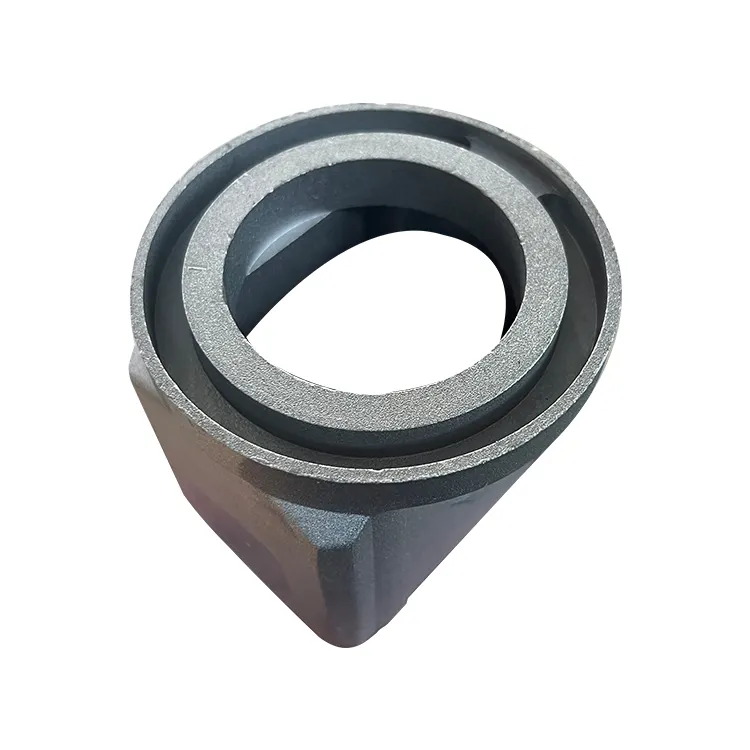
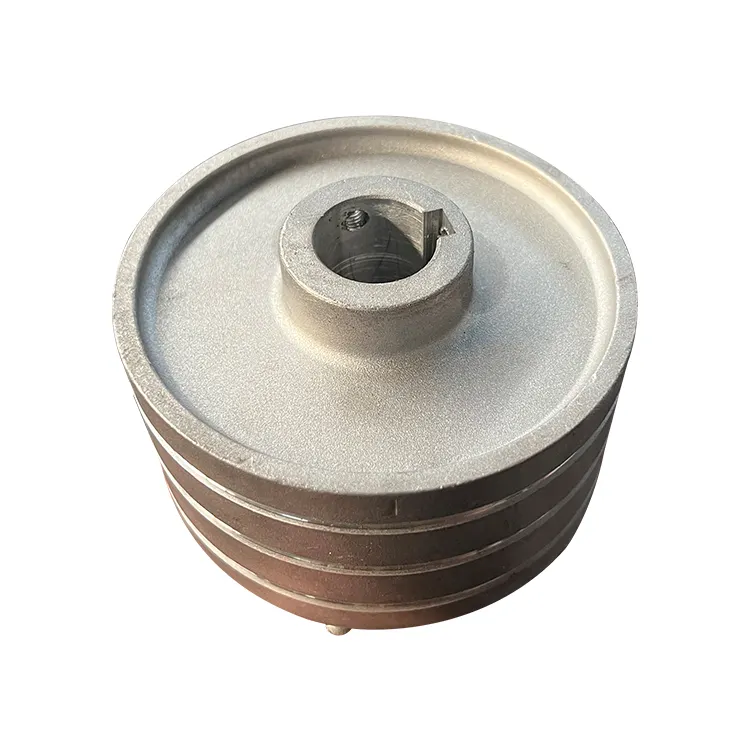
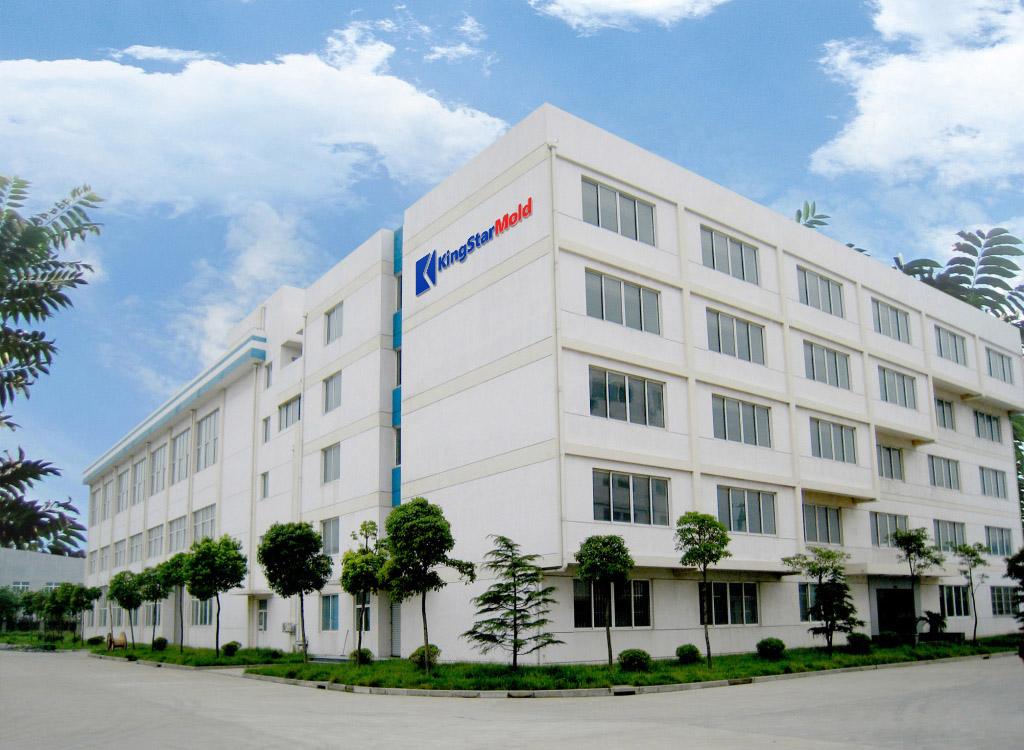
Our Factory In China
KingStar Mold is a leading manufacturer based in China, specializing in custom injection molds and the production of plastic and silicone components. With over ten years of experience, we offer comprehensive solutions from mold design to production, ensuring the highest standards of quality and precision.
Our factory is equipped with advanced machinery and staffed by skilled professionals, dedicated to delivering tailored, high-performance parts for a variety of industries. Whether it’s plastic, silicone, or a combination of materials, KingStar Mold provides reliable, cost-effective solutions for every project.
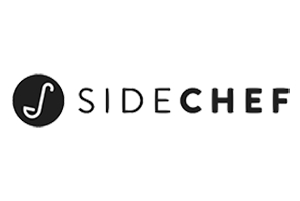
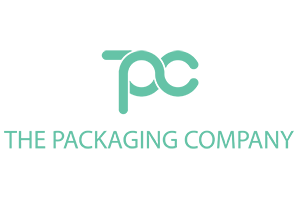
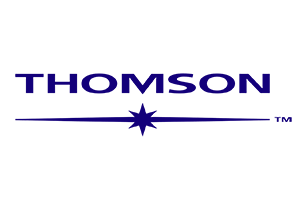
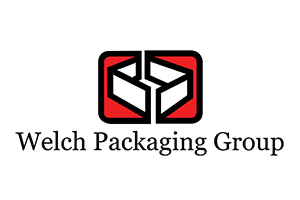
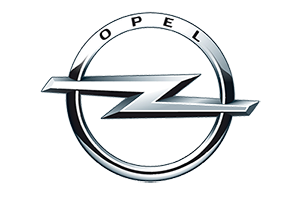
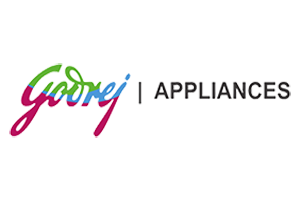
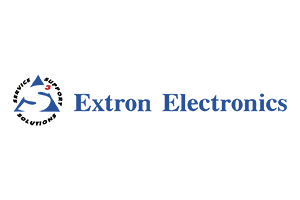
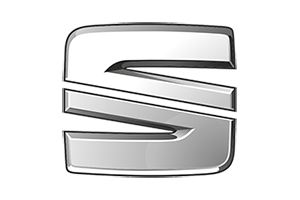
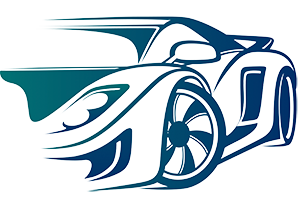
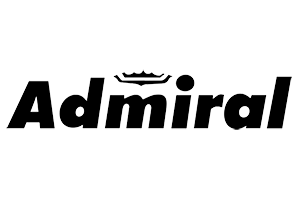
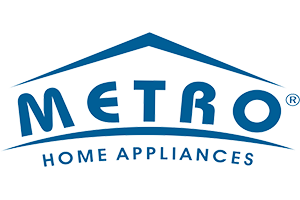
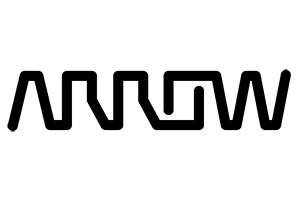
Surface Finishing Options For Die Casting Parts
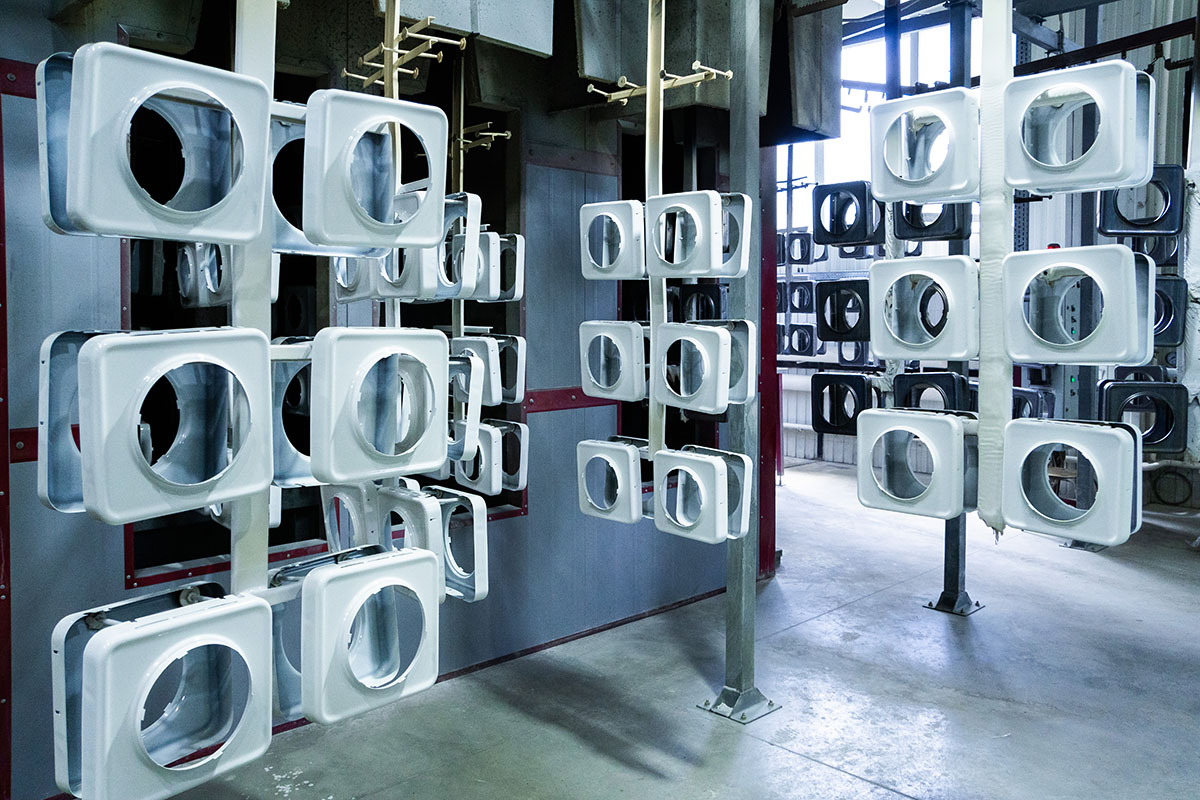
KingStar Mold provides a complete suite of surface treatment services for die-cast parts, aimed at improving their appearance, functionality, and longevity. Our offerings include polishing, anodizing, powder coating, and so on, all designed to enhance surface finish, corrosion resistance, and wear resistance. Through these treatments, we ensure your die-cast parts meet the highest quality standards, delivering the optimal finish for both visual appeal and performance needs.
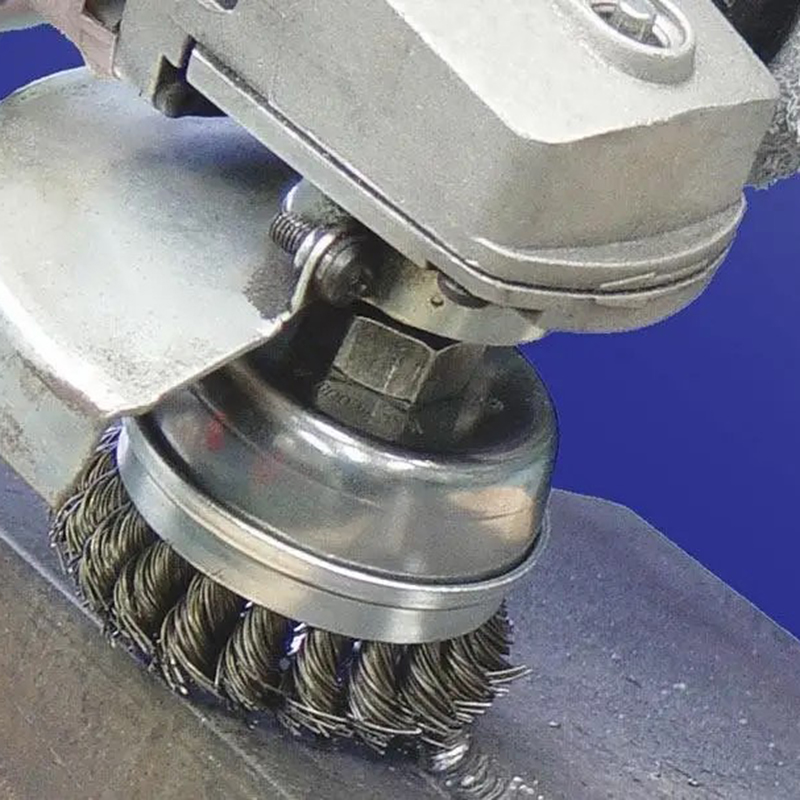
Powder Coating
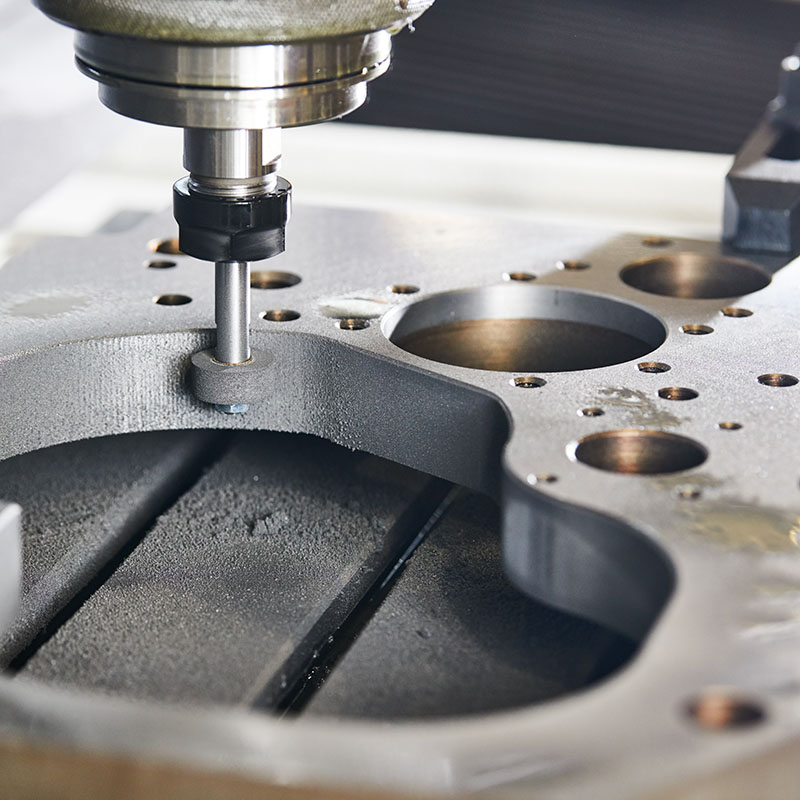
Grinding & Polishing
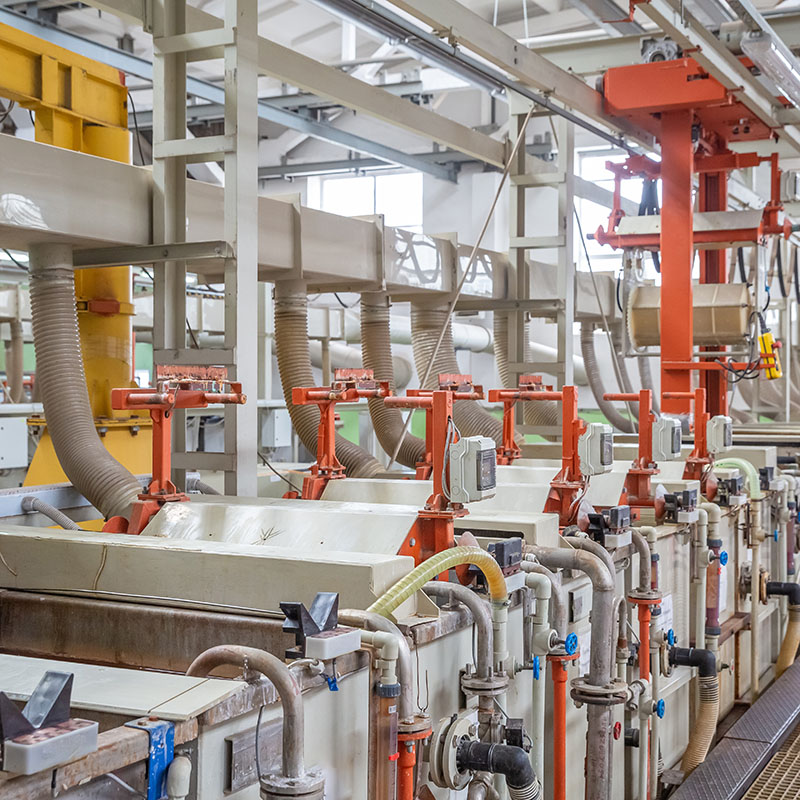
Anodizing
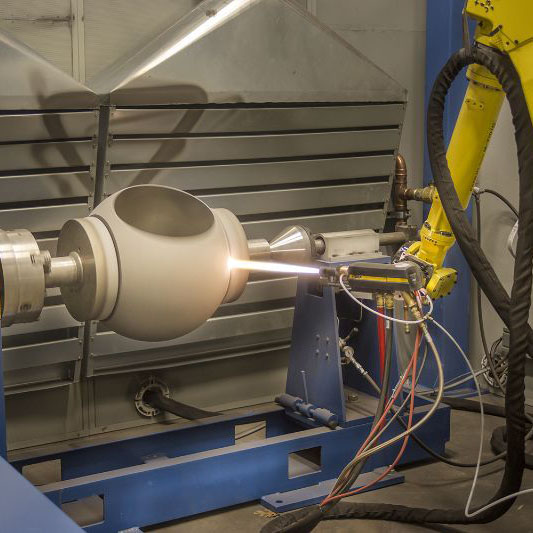
Spraying
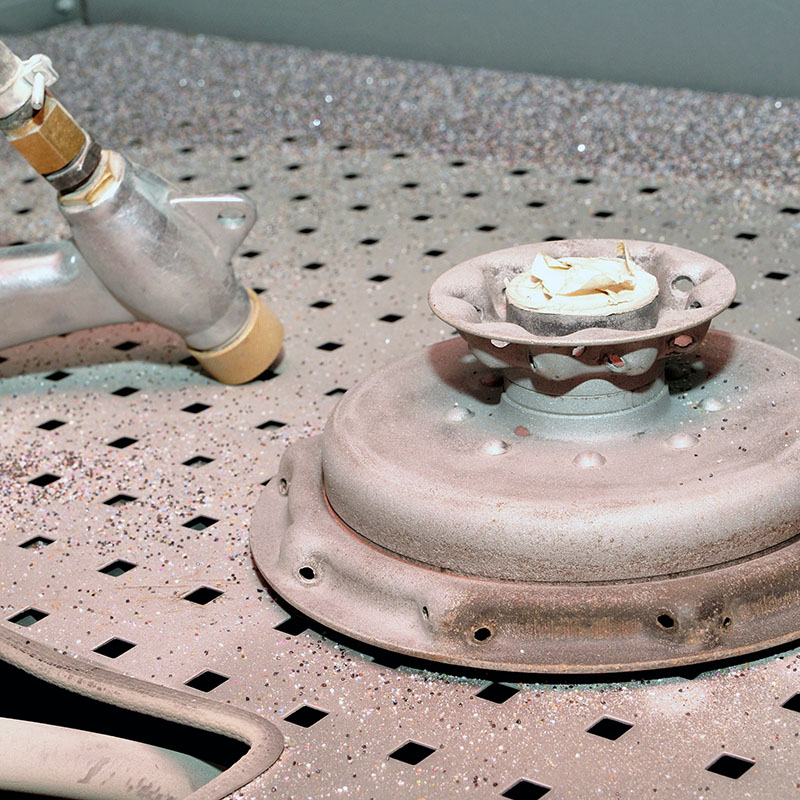
Sand Blasting
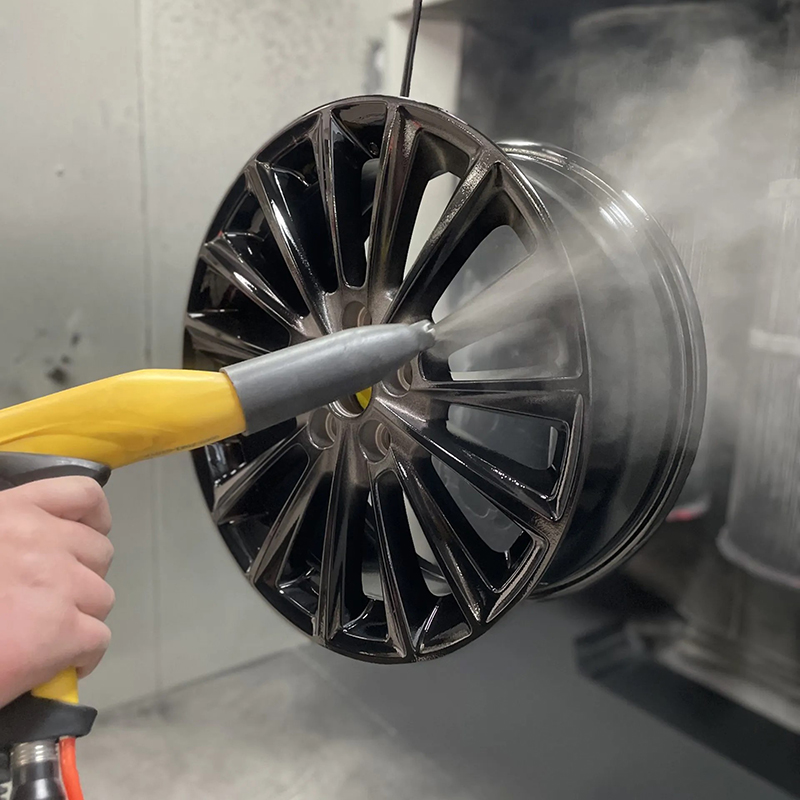
Brushed Finishing
10+
Types Available
400M+
Capacity Monthly
20+
Partnerships
10Y+
Experience
99%+
Satisfactory Rate
KingStar Mold’s Production Capacity
Minimum Part Weight | 0.017 kg |
Maximum Part Weight | 12 kg |
Minimum Part Size | ∅17 mm × 4 mm |
Maximum Part Size | 300 mm × 650 mm |
Minimum Wall Thickness | 0.8 mm |
Maximum Wall Thickness | 12.7 mm |
Quality Control | ISO 9001 Certified |
Minimum Order Quantity | 1000 pcs |
Orders Workflow
Initial Consultation & Design Review
We begin by discussing your project’s goals and reviewing the design to ensure it’s optimized for the specific manufacturing process. At this stage, we suggest improvements or adjustments to enhance efficiency, functionality, and manufacturability.
Material Selection
Our experts assist in selecting the right materials for your product based on performance requirements and compatibility with the manufacturing process. The correct material choice ensures durability, cost-effectiveness, and the desired product functionality.
Design & Engineering
Using advanced CAD and simulation tools, we develop a custom design for your project. This step ensures precise details and identifies potential challenges early in the process, optimizing the design for efficient manufacturing.
Prototyping & Sample Testing
A prototype or sample is created to verify design accuracy, functionality, and performance. Rigorous testing is conducted to ensure the product meets your specifications before moving into full-scale production.
Production Setup & Initial Production
We set up the required machines, molds, or tools for the manufacturing process. The initial production run is performed to confirm the setup, assess quality, and fine-tune settings for optimal results.
Final Production & Quality Control
After final approval, we proceed with full-scale production, ensuring continuous quality checks. Comprehensive inspections at each stage ensure that every part meets the highest standards before delivery.
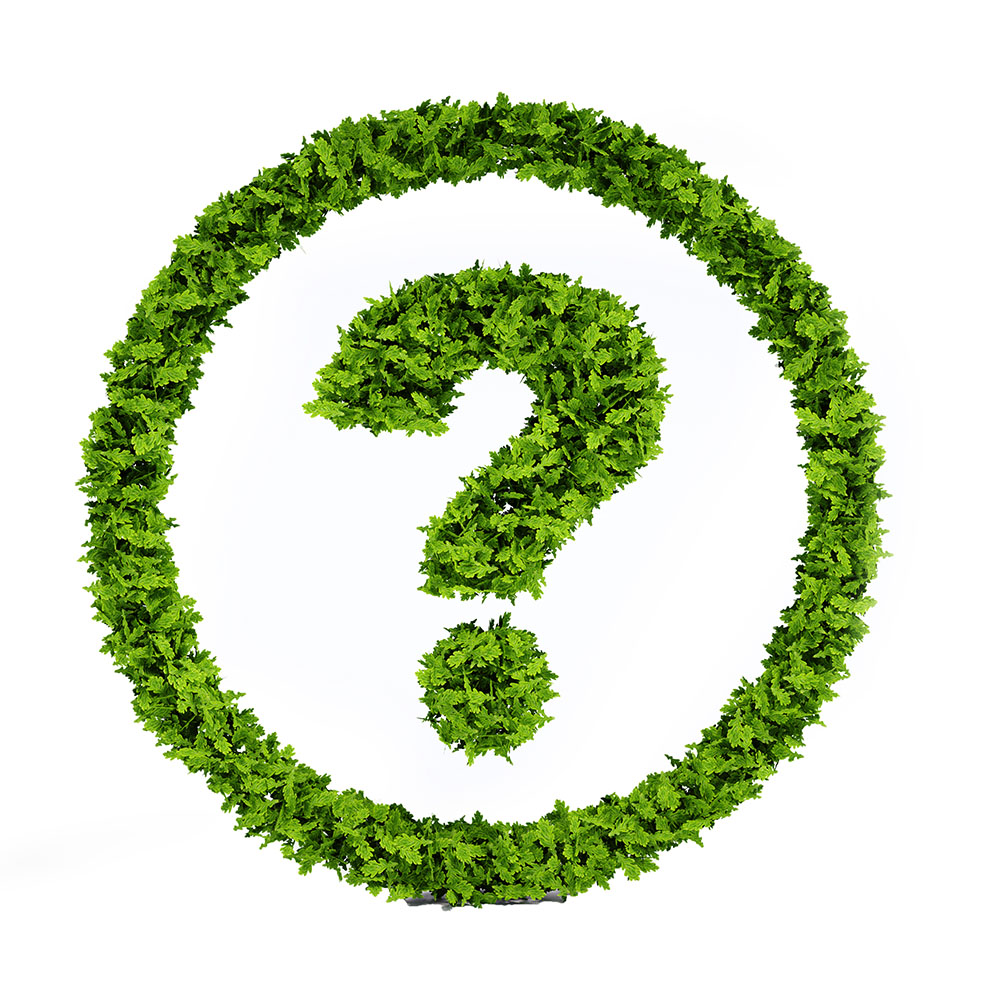
KingStar Mold provides die casting solutions to various industries, including automotive, aerospace, electronics and so on.
KingStar Mold follows ISO 9001 standards and a strict quality control process to guarantee that every part meets the required specifications.
Materials like aluminum, zinc, magnesium, and copper alloys are typically used in die casting.
Die casting is a manufacturing process where molten metal is injected into a mold at high pressure to create precise and complex parts.
Die casting can be limited by high initial tooling costs, material choices (mostly non-ferrous metals), and size constraints for larger components.
KingStar Mold works closely with clients to create custom die casting designs, ensuring the parts meet specific functionality and design criteria.
KingStar Mold provides both hot chamber and cold chamber die casting, tailored to the specific material and size requirements of the part.
Die casting offers high precision, the ability to produce complex shapes, faster production cycles, and durable, strong components.