Design Support
We Provide Differential Design Support Service Based On Your Business Type
Whether you’re launching your first physical product, collaborating with an internal team, or scaling up as a seasoned developer, we partner with you to plan strategically, design efficiently, engineer precisely, document thoroughly, and smoothly transition your product into manufacturing.
For Companies or Startups Without a Product Development Team
We help startups and companies without internal R&D teams bring ideas to life—quickly, affordably, and with manufacturing in mind.
At KingStar Mold, we go beyond design—we’re a full-stack partner with deep manufacturing expertise. Whether you have a rough sketch or just a concept, we turn it into a ready-to-quote, ready-to-produce solution.
We balance function, cost, and manufacturability, all while ensuring every detail is optimized for large-scale injection molding and part production.
For Companies With a Product Development Team
Even with strong internal R&D, many companies need outside expertise for unfamiliar or technically demanding parts of a project. We support your team with fast, cost-effective solutions—from early design to final optimization.
As a leading on-demand manufacturer, we bring deep experience in industrial design, mechanical engineering, and design strategy. Whether you’re integrating new tech, updating existing products, or tackling complex design issues, our team helps you avoid costly errors and speed up development.
For Entrepreneurs With A Product Concept
Turning an idea into a real product is challenging—especially without an in-house team. That’s where we come in.
At KingStar, we go beyond design. Our team supports you from concept to production with end-to-end services: engineering design, prototyping, app integration, manufacturing readiness, and even business operations like supply planning and go-to-market support.
Whether you’re refining an early concept or recovering from a failed design, we help you move forward with confidence—ensuring your product is not only buildable, but scalable.
Our 6-Step Development Process
Comprehensive Product Design & Manufacturing Support
As a manufacturer with 15+ years in precision molding and machining, we don’t just design—we build products that work on the production line. Our design support ties every step to manufacturability, so you avoid costly reworks and delays. Here’s how we deliver:
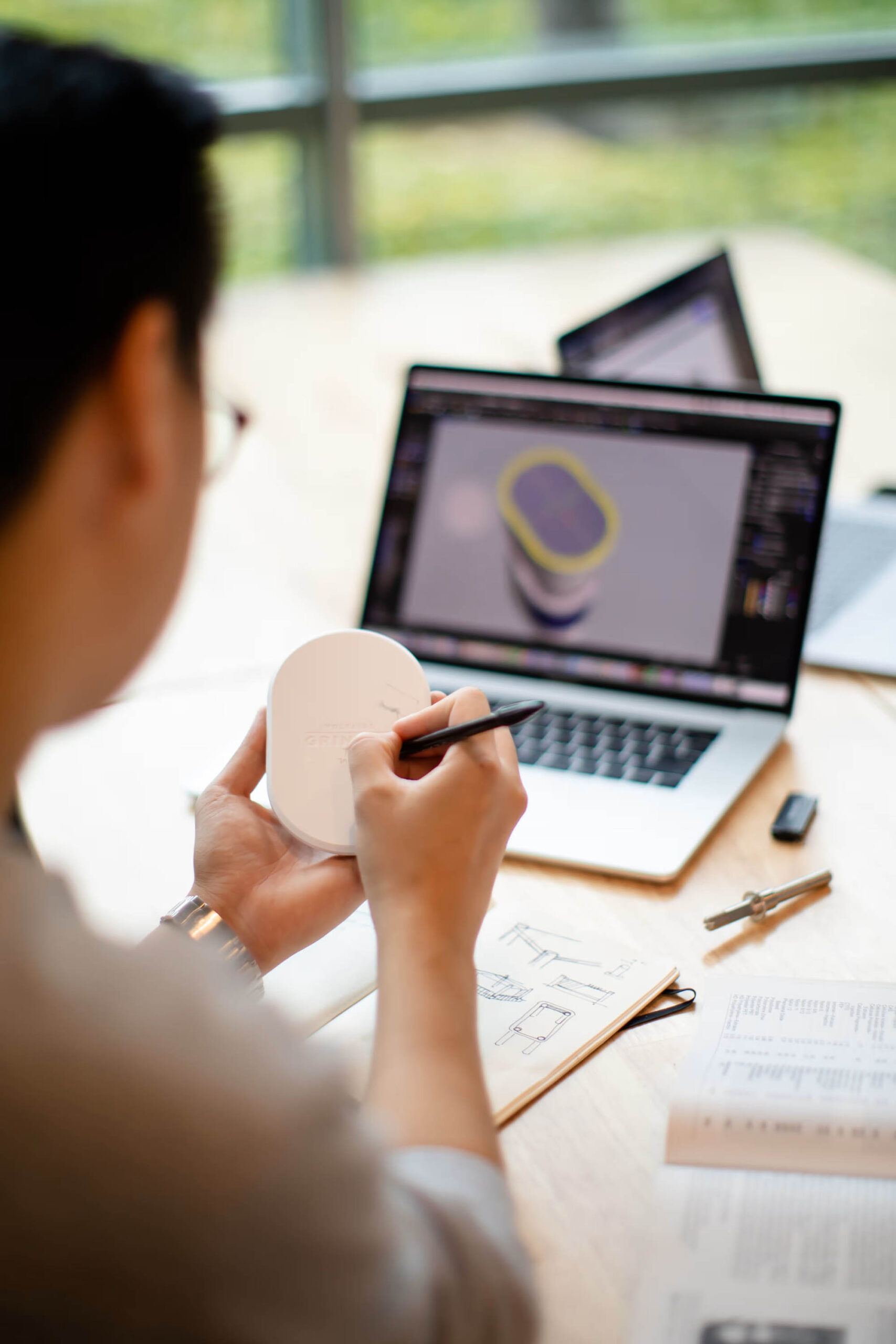
Why Collaborate With Us
Design Optimization
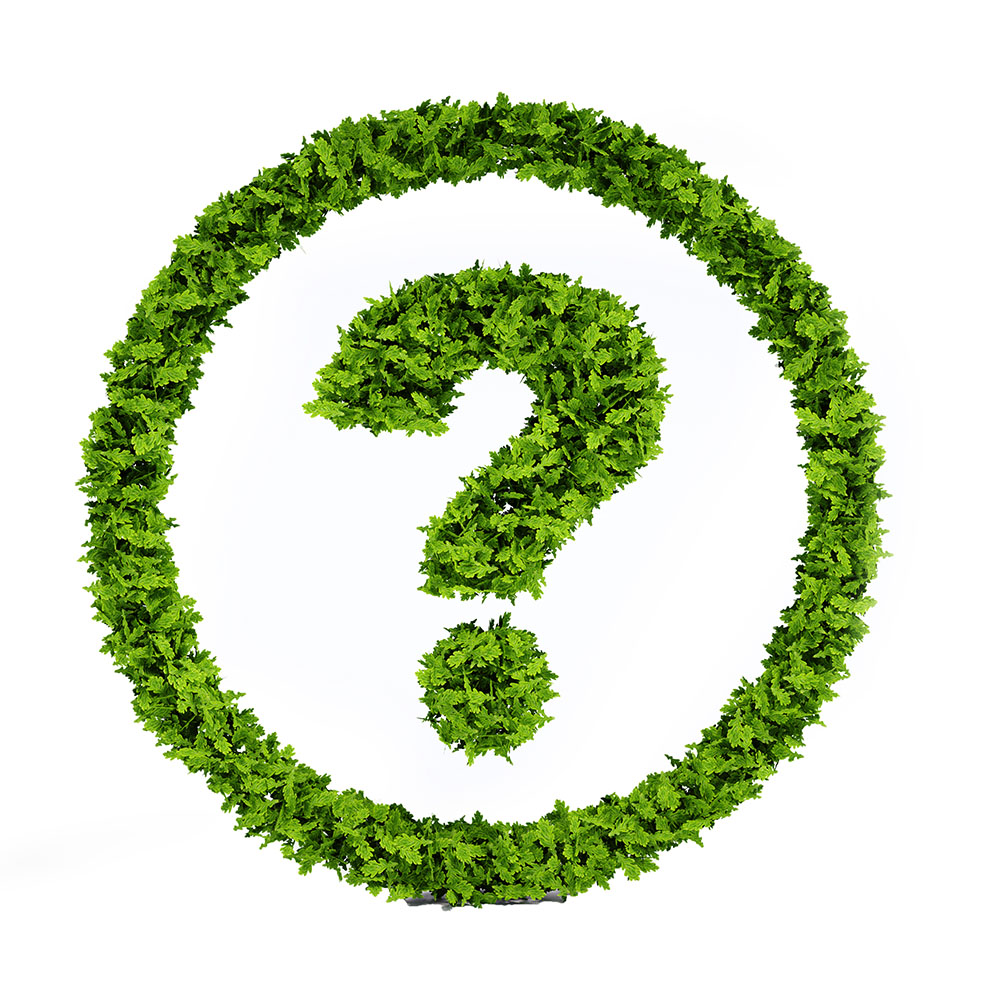
Frequently Asked Questions
The development timeline varies based on the product’s complexity, number of components, and any technical challenges involved. However, for most projects, it typically takes 3 to 6 months to go from initial concept to a fully tested and functional prototype.
At KingStar Mold, we break this journey into several structured stages — including product definition, design strategy, detailed engineering, and iterative prototyping. Each phase includes milestone reviews and feedback cycles to ensure alignment with your performance goals and manufacturability needs. We also use rapid prototyping tools such as CNC machining, 3D printing, vacuum casting, and rapid tooling to accelerate physical testing and design refinement.
With close collaboration and clear objectives, we help you move quickly and confidently through the product development pipeline while minimizing risks and surprises.