Fused Deposition Modeling (FDM) is one of the most widely adopted technologies in the field of additive manufacturing. Known for its cost-efficiency, simplicity, and material versatility, FDM is particularly well-suited for rapid prototyping, functional modeling, and low-volume production. It operates by extruding melted thermoplastic filament layer by layer, creating parts directly from 3D CAD data.
Compared to resin-based or powder-bed processes like SLA, SLS, or DMLS, FDM involves unique design considerations due to its method of material deposition. While it may not offer the same level of surface finish or fine detail as other technologies, it excels in speed, affordability, and the ability to use common thermoplastics like ABS, PLA, and Nylon. As a result, designers must understand both the capabilities and limitations of the process to fully leverage its strengths.
This guide outlines essential design principles tailored specifically for FDM 3D printing. From overhangs and wall thickness to mating parts and text features, it provides actionable recommendations to help you create models that print reliably and perform as intended.
1. How the FDM Process Works
While the FDM workflow includes several operational steps, not all of them are equally important from a design perspective. Below are the key stages where design decisions have the greatest impact on print success.
1.1 Model Preparation (Design Begins Here)
This is the most design-intensive step and the foundation of a successful FDM print.
- Design for watertight geometry
A printable 3D model must be manifold, meaning no holes or non-joined surfaces. Any geometry errors here will cause slicing issues or incomplete prints. - Minimize unsupported features
Overhangs greater than 45° or bridges longer than ~1.2mm may require support, which affects both surface finish and post-processing effort. Avoid unnecessary overhangs in your design when possible. - Choose part orientation strategically
Orientation affects strength (due to anisotropy), surface finish, and support requirements. For example, features requiring higher strength should be aligned in the XY-plane rather than across layers. - Account for tolerances and fit
Add intentional clearances for assemblies—at least 0.5mm gap between mating parts—to prevent fused or stuck components.
1.2 Slicing (Design-Driven Choices)
Although slicing is often handled by engineers or technicians, designers benefit from understanding its implications.
- Layer height affects detail and tolerance
Finer layers yield better detail but longer print times. For embossed or engraved features, ensure their size exceeds the layer height by a clear margin to remain visible after printing. - Infill patterns influence strength and material use
A designer specifying functional prototypes may need 50% infill for durability, while conceptual models can use as little as 10%. - Support generation ties back to geometry
The need for supports depends on how the part is designed. Reducing steep angles or adding self-supporting geometry can minimize unnecessary material and cleanup.
1.3 Machine Setup and Material Loading
This step is mainly operational and doesn’t require design input. It includes leveling the bed, heating components, and loading filament. While important for print quality, it doesn’t influence design decisions directly.
1.4 Printing and Layer Deposition
The printer follows G-code instructions to deposit filament layer by layer. From a design standpoint, it’s important to remember:
- The first layer’s adhesion is critical—designing large, flat surfaces at the base helps improve grip and prevent warping.
- Shrinkage and cooling can cause distortion in thin or tall parts; adding ribs or adjusting wall thickness can help counteract this.
1.5 Cooling, Removal, and Post-Processing
Once the part is finished, it cools and is removed from the build plate. Post-processing tasks like support removal and surface finishing follow.
From a design perspective:
- Use design features like chamfers or breakaway tabs to make support removal easier.
- If aesthetic appearance matters, consider post-processing compatibility (e.g., ABS is suitable for acetone vapor smoothing, while PLA is not).
2. Key Limitations and Challenges in FDM
FDM is a versatile and cost-effective technology, but it has inherent constraints that must be considered during the design phase. Overlooking these limitations can lead to failed prints or compromised functionality.
2.1 Rounded Corners from Nozzle Geometry
FDM printers extrude filament through a circular nozzle, which limits the precision of sharp features.
- No sharp internal corners
Inner corners will always have a radius equal to or slightly larger than the nozzle diameter (typically 0.4 mm). This can affect assemblies that rely on tight corner geometry, such as snap-fits or interlocking joints. - Design workaround
Where square internal corners are critical, consider adding relief cuts (dog-bone or T-shaped) to maintain functional fit without relying on unrealistic precision.
2.2 Anisotropic Mechanical Properties
Because FDM prints are built layer by layer, strength varies depending on orientation.
- Weaker in the Z-direction
Layers adhere through thermal bonding, which is inherently weaker than the continuous extrusion in the XY-plane. Parts are more prone to delamination or fracture when stress is applied perpendicular to layers. - Design strategies
Align critical load-bearing features in the XY-plane. If strength in the Z-direction is unavoidable, consider thicker walls or mechanical reinforcements like ribs or inserts.
2.3 Warping and Thermal Distortion
During cooling, printed parts shrink unevenly, especially across large, flat areas or thin walls. This can cause warping, lifting from the build plate, or internal stress.
- Geometry-related triggers
Sharp corners, tall unsupported sections, and thin features are more prone to distortion. PLA tends to warp less, while materials like ABS and Nylon are more sensitive to uneven cooling. - Preventative design choices
Add fillets to corners, use chamfered bases, and avoid abrupt transitions in cross-section. Design with thermal behavior in mind by minimizing large, flat, unsupported surfaces.
3. Technical Capabilities of FDM Printing
Understanding the technical capabilities of FDM is essential for making informed design choices. By knowing the system’s limits, designers can optimize parts to achieve the best results.
3.1 Build Size and Resolution Specifications
FDM printers come with different build volumes and resolution capabilities, both of which influence part design.
- Maximum Build Size
Standard FDM printers typically offer build volumes around 800 x 800 x 550 mm, but this can vary. Large prints require strategic part orientation to minimize overhangs and supports. - Resolution and Layer Height
FDM printing resolution is around ±0.3mm, meaning that fine details might not always be accurately rendered unless parts are designed with larger tolerances. The resolution is also influenced by the chosen layer height, with finer layers producing more detailed prints at the cost of longer print times.
3.2 Dimensional Accuracy Limits
While FDM is excellent for prototyping, its dimensional accuracy has inherent limits.
- Accuracy Range
FDM parts typically have dimensional accuracy of ±0.3%, with a minimum limit of ±0.3 mm. This can be significant for high-precision applications, so designers must account for potential variations, especially in assemblies or interfaces that require tight tolerances. - Design Considerations
Allowing for slight tolerance variation and focusing on critical dimensions can help mitigate any potential fit or assembly issues. Parts requiring high precision may need to be designed using other manufacturing methods or post-processed to improve accuracy.
3.3 Surface Finish and Typical Texture
Surface finish in FDM prints is typically rough due to visible layer lines.
- Visible Layer Lines
Prints will inherently exhibit a layer-by-layer texture, especially if a higher layer height is chosen for faster printing. For parts requiring a smooth surface, consider post-processing methods like sanding, vapor smoothing (for ABS), or adding texturing patterns that can complement the print finish. - Design for Aesthetics
Consider adding features like rounded edges or fine details that hide rough surfaces or make the layer lines less noticeable. Additionally, the use of higher-resolution prints or additional finishing steps can help achieve the desired surface quality.
3.4 Support Material Usage
Certain FDM parts require support material for overhangs or complex geometries.
- Support Types
FDM uses soluble or breakaway support structures, which are essential for geometries with overhangs above 45° or features that don’t have enough self-support. Soluble supports (like PVA) are more suitable for parts with intricate designs, while breakaway supports are easier to remove but may leave some traces of marks. - Design Strategies for Supports
Minimize the need for supports by designing parts with self-supporting angles (below 45°) or using angled features that reduce dependency on support. The careful placement of features and support structures can reduce post-processing time and material costs.
4. Design Guidelines for FDM Printing
Effective FDM designs require an understanding of various print limitations and best practices. Below are the essential guidelines for achieving optimal results with FDM 3D printing.
a. Overhangs
Overhangs are a common challenge in FDM 3D printing, as excessive angles can compromise print quality. Overhang angles greater than 45° or lengths exceeding 1.2 mm typically require support structures.
- Maximum Overhang Angles and Lengths
FDM printing allows overhangs of up to 45° without the need for support. The length of overhangs should not exceed 1.2 mm for stable print quality. - When to Use Support Structures
If overhangs surpass the recommended angle or length, support structures become necessary to maintain print quality and reduce the risk of sagging or poor resolution.
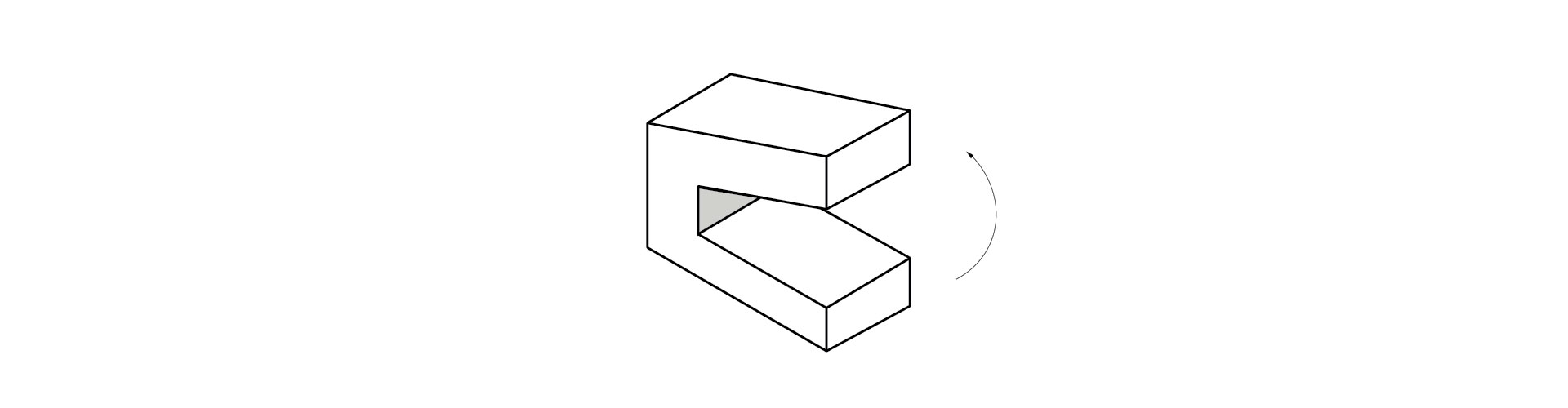
b. Unsupported vs. Supported Walls
Walls that lack support are prone to warping during the cooling process. Understanding the thickness requirements for both supported and unsupported walls is crucial to avoid structural issues.
- Minimum Wall Thickness
Unsupported walls must be at least 1.2 mm thick to prevent warping. Supported walls, which are connected to at least two sides, can be thinner—around 1.0 mm—since they are more stable. - Warping Risk
Thin unsupported walls are highly vulnerable to warping, especially in materials like ABS. To minimize this risk, consider increasing the thickness or adding internal structures for support.
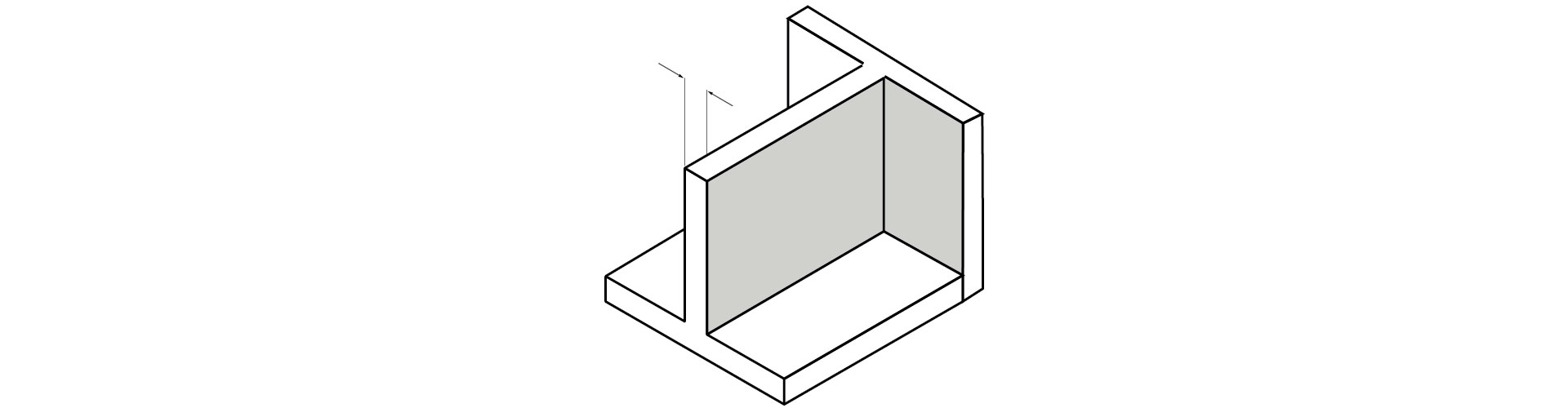
Supported Walls
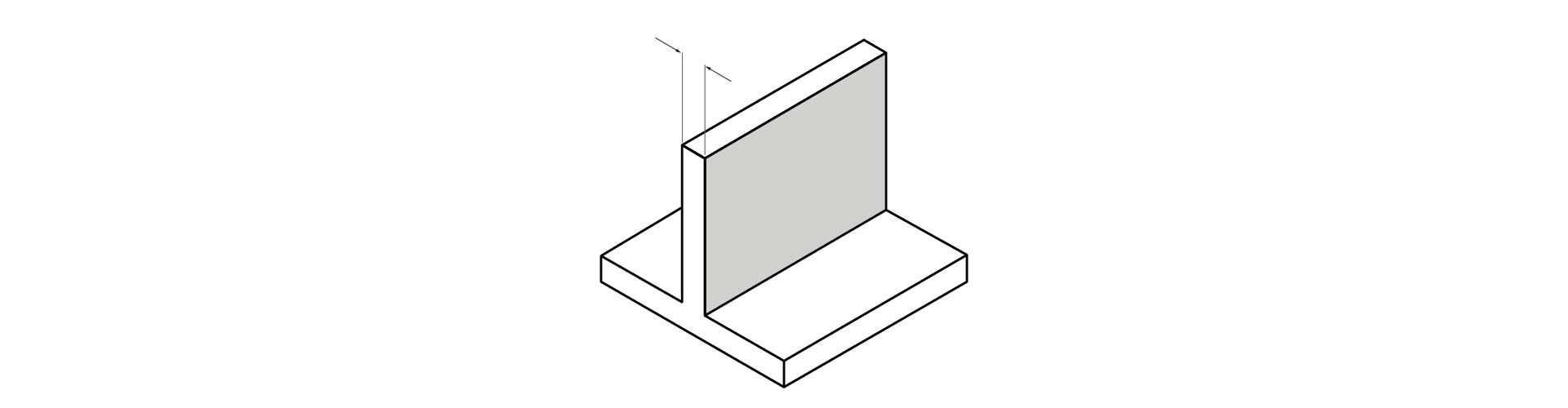
Unsupported Walls
c. Pins and Columns
Pins and columns are narrow, tall features that require careful design to ensure stability during printing.
- Minimum Diameter for Reliability
The minimum diameter for reliable pins is 1 mm. Pins smaller than this are prone to breakage or deformation during printing, making them unsuitable for most applications. - Reinforcement Recommendations
For taller pins or columns, consider adding bracing or increasing the diameter to ensure structural integrity throughout the print process.
d. Mating Parts
When designing parts that fit together, adequate clearance is necessary to ensure proper assembly and prevent fusion during printing.
- Minimum Clearance
A clearance of 0.5 mm between mating parts is recommended to avoid friction-fit issues, ensuring that parts can be assembled without difficulty post-printing. - Best Practices for Functional Assemblies
Ensure your mating parts are designed with enough clearance to account for minor dimensional variations in the printing process. Consider chamfering edges to make assembly smoother.
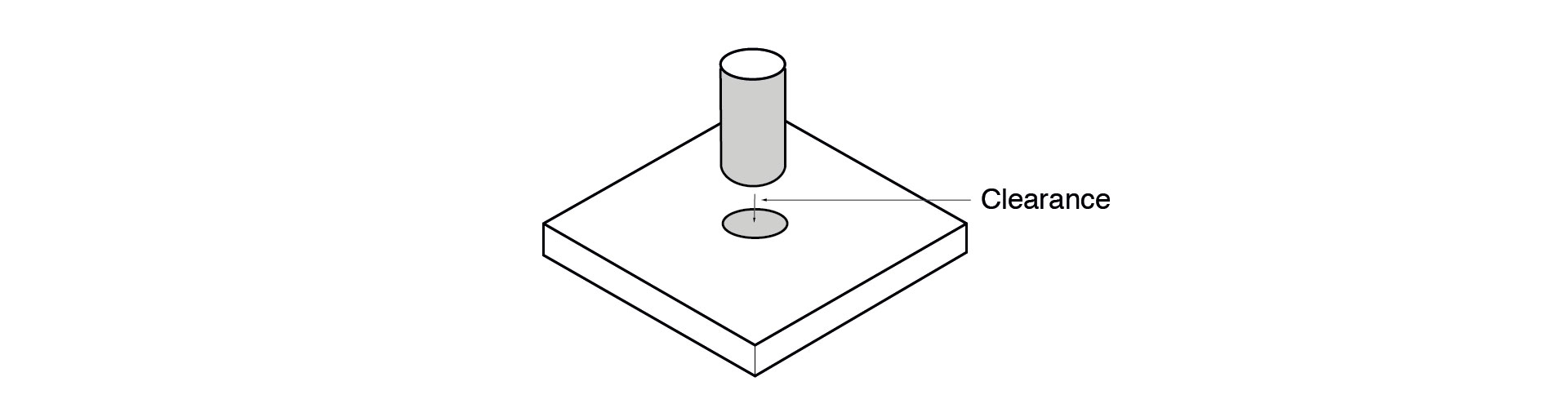
e. Embossed Features
Embossed details, such as logos or raised text, add depth to the surface of a part but require specific design considerations for proper printability.
- Minimum Height for Visibility
Embossed features should have a minimum height of 0.3 mm to ensure they are visible and distinguishable in the finished print. - Common Applications
Embossed features are typically used for logos, brand names, or decorative elements. Ensure that the features are placed on flat surfaces to avoid distortion.
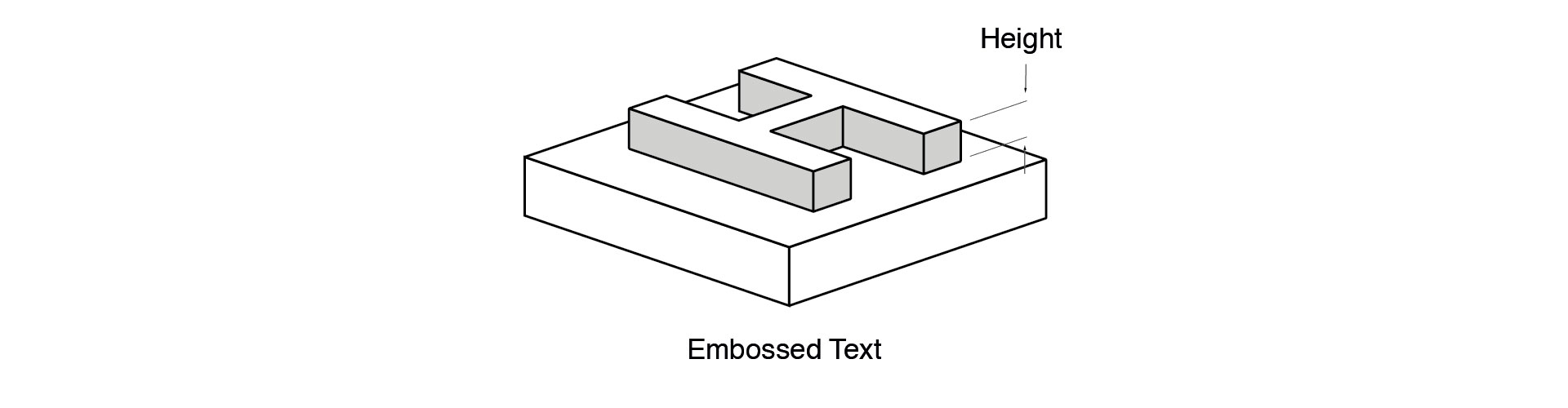
f. Engraved Features
Engraved details require careful design to ensure they are both visible and correctly extruded during the printing process.
- Minimum Depth and Width for Legibility
Engraved features should have a depth of at least 0.5 mm and a width of 0.5 mm to ensure legibility and proper material extrusion. - Design Considerations
For small text or intricate designs, use larger fonts and avoid overly detailed engravings to ensure the features remain clear after printing.
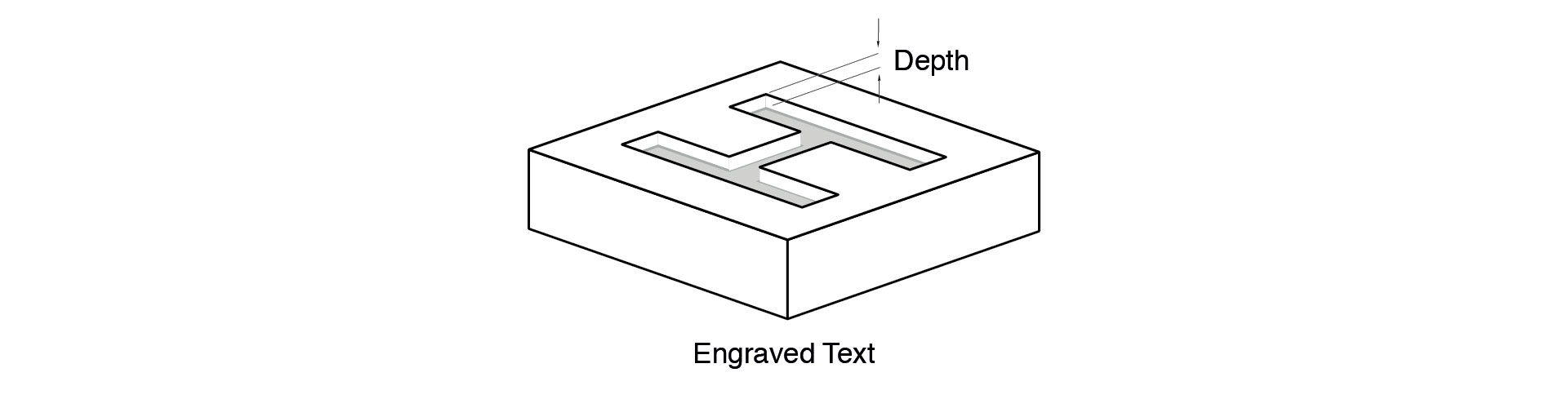
Summary of Best FDM Design Practices
Design Element | Recommended Specifications |
Overhangs | Maximum length: 1.2 mm, angle: up to 45° |
Unsupported Walls | Minimum thickness: 1.2 mm |
Supported Walls | Minimum thickness: 1.0 mm |
Pins | Minimum diameter: 1.0 mm |
Mating Parts | Minimum clearance: 0.5 mm |
Embossed Details | Minimum height: 0.3 mm |
Engraved Details | Minimum depth: 0.5 mm, minimum width: 0.5 mm |
5. Preparing Files for Printing
Before a part reaches the printer, the digital model must be optimized and exported correctly to ensure that what’s designed is what gets printed. This step often makes the difference between a successful print and a failed one.
5.1 Exporting to STL Format
STL (stereolithography) is the standard file format used for FDM printing, but improper export settings can cause significant issues.
- Ensure Model is Watertight
A printable STL file must be watertight—this means it has no holes or gaps in the mesh. Open edges or non-manifold geometry will result in slicing errors or failed prints. - Set Appropriate Resolution
When exporting to STL, choose a resolution that balances detail and file size. Too low, and curves become faceted; too high, and file size becomes unnecessarily large. A chord height (tolerance) of 0.01 mm to 0.05 mm is usually sufficient for most FDM applications. - Check Unit Consistency
Confirm that your CAD model’s unit system (e.g., millimeters) matches the slicing software’s interpretation. Many STL files lack embedded unit data, which can lead to incorrect scaling if not double-checked.
5.2 Pre-Submission Considerations
Before handing off your file for manufacturing—whether in-house or to a supplier—it’s important to do a final design sanity check.
- Wall Thickness Verification
Make sure all walls and features meet the minimum thickness guidelines for FDM (e.g., 1.2 mm for unsupported walls). Undersized features may not print at all or may be structurally weak. - Orientation and Supports
If your design requires a specific orientation to preserve functional surfaces or minimize support scars, document it. Otherwise, the technician may orient it based purely on printability, potentially compromising aesthetics or tolerances. - Consolidate Assemblies When Needed
If your design consists of multiple parts, separate them in the file or clearly label them. Overlapping geometry in a single file can cause the slicing software to misinterpret the part boundaries.
6. Practical Tips for Better Results
While proper modeling is essential, the final success of an FDM print also depends on a few key practical choices during preparation and printing. These tips can help balance strength, quality, and efficiency.
6.1 Selecting the Right Filament for Your Application
Not all filaments behave the same way—and picking the wrong one can compromise the entire design.
- Strength vs. Flexibility
If mechanical strength is your priority, filaments like ABS, PETG, or Nylon are preferred. For flexibility, TPU offers excellent elasticity while still maintaining decent durability. Avoid PLA in load-bearing or outdoor applications, as it becomes brittle over time. - Environmental Factors
Choose filaments based on exposure: ASA for UV resistance, Nylon for chemical resistance, and PC for heat resistance. Don’t default to PLA unless the part is purely decorative or low-stress.
6.2 Layer Height and Its Tradeoffs
Layer height directly affects surface finish, speed, and detail resolution.
- Fine Layers (e.g., 0.1 mm)
Offer better visual quality and detail, suitable for aesthetic or precision parts, but significantly increase print time. - Thicker Layers (e.g., 0.2–0.3 mm)
Improve strength between layers and reduce printing time but result in rougher surface texture. Ideal for rapid prototypes or functional parts where appearance is secondary.
6.3 Strategic Orientation of the Model
Print orientation affects more than just support material—it can determine whether a part functions as intended.
- Minimize Supports
Orienting flat surfaces parallel to the build plate and avoiding overhangs above 45° reduces the need for support structures, saving material and post-processing time. - Improve Mechanical Strength
Layer adhesion is weakest between layers, so align the part’s load-bearing axis vertically to enhance durability. For example, pins or hooks should be printed upright to prevent delamination. - Prioritize Critical Surface Quality
Surfaces in contact with support often need sanding. Orient visually or dimensionally critical surfaces upward to preserve finish and accuracy.
7. When to Ask for Help
Not every design challenge can—or should—be solved in isolation. Knowing when to reach out to experts can save time, reduce print failures, and improve overall product quality.
7.1 Identifying Design Features That Need Expert Review
Some geometries may appear printable in CAD but pose serious challenges in FDM execution.
- Thin walls and micro features
If your design includes ultra-fine embossing, engraving, or walls below 1 mm, consult with a professional to ensure they’re printable without warping or being skipped entirely. - Interlocking or assembled parts
Mating components, hinges, or snap fits require tight control over tolerances and clearances. If unsure about fit or print orientation, an expert review can prevent fusion or poor assembly. - Organic shapes and complex overhangs
Freeform or biomorphic surfaces may require advanced support strategies or multi-axis printing approaches. These are best reviewed by experienced technicians.
7.2 Why Partnering with a Manufacturer Like KingStar Mold Matters
Working with a knowledgeable manufacturing partner can streamline your design-to-production workflow, especially when tolerances or mechanical performance are critical.
- Design feedback grounded in production reality
KingStar Mold offers practical design-for-manufacturing (DFM) guidance that goes beyond theory. Their engineers can suggest geometry tweaks to minimize risk without compromising function. - Access to high-end printing and post-processing
When parts need precision, smooth finishes, or specific strength profiles, KingStar Mold’s equipment and material expertise ensure your prints match your expectations. - Fast, collaborative iteration
Whether you need quick prototyping or are ready for small-batch production, KingStar Mold helps shorten development cycles with responsive support and full-scale capabilities.
Final Thoughts
FDM printing rewards those who design with both creativity and practicality in mind. While it’s tempting to push boundaries, success often comes down to how well you understand and apply design-for-manufacturing principles.
- Design smarter to reduce post-processing
Thoughtful planning during the modeling stage—like minimizing overhangs or orienting parts for fewer supports—not only improves quality but also cuts down on finishing time and material waste. - Treat guidelines as adaptable, not absolute
Every printer, material, and project has its own variables. The specifications shared in this guide serve as solid starting points, but adjustments may be needed depending on your exact setup or performance needs.
Ultimately, great FDM design is about balancing what’s possible with what’s practical. And when in doubt, collaborating with an experienced manufacturing partner like KingStar Mold can take the guesswork out of the equation—helping you go from CAD to successful print with confidence. If you would like to learn more about our FDM 3D printing services, please visit our service page: Fused Deposition Modelling (FDM) 3D Printing Service