Free Design Review for Sheet Metal Fabrication Assemblies
Take advantage of our 30-minute virtual meeting with a sheet metal applications engineer to refine your project. This session is ideal for addressing your questions and ensuring your design aligns with production needs.
Material suitability for application
Optimizing design for cost-effectiveness
Improving strength and durability
Best fabrication techniques for accuracy and minimal waste
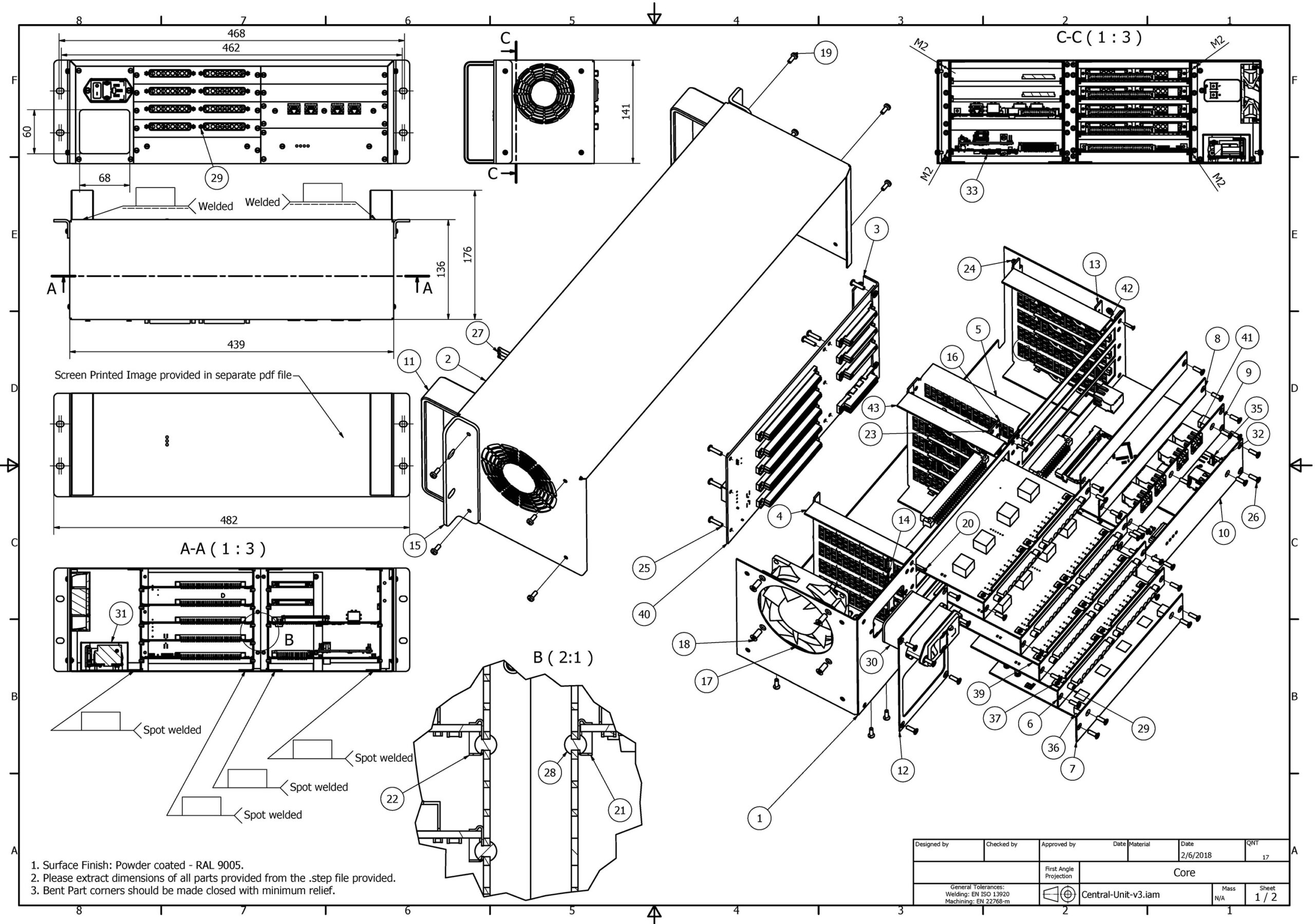
Professional Part Design for Sheet Metal Fabrication
Our professional part design services for sheet metal fabrication focus on optimizing your components for cost-effective and efficient production. By considering factors like material selection, thickness, bend radii, and manufacturability early in the design process, we ensure your parts meet all functional requirements while minimizing production costs and lead times. With our expert guidance, we help you navigate complex design challenges and achieve high-quality results.
Critical Design Advisories
Follow these 4 design advisories can help you optimize production efficiency and aesthetic function of your sheet metal parts.
Minimum Flange Lengths
Minimum flange lengths are essential to securely hold a workpiece between the top and bottom die in the press brake during the forming process. The required flange length varies based on material type, material thickness, and bend radius. Please refer to the table below for specific length guidelines according to KingStar Mold’s tooling requirements.
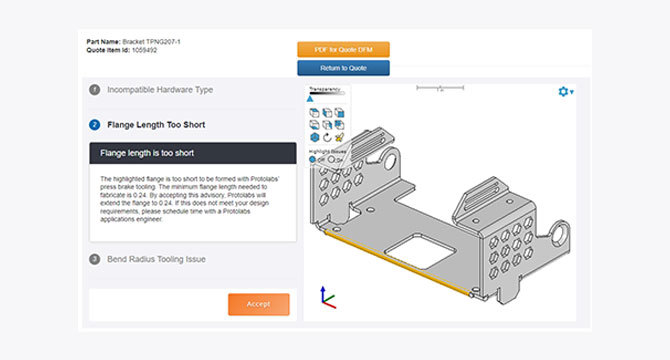
Flange Lengths | |||
---|---|---|---|
Material Thickness | Copper / Aluminum | Galv. / Galvnl. / CRS | Stainless Steel |
.024 -.050 in. | bend radius + 3.0x material thickness | bend radius + 3.5x material thickness | bend radius + 3.5x material thickness |
.060 -.090 in. | bend radius + 2.5x material thickness | bend radius + 2.75x material thickness | bend radius + 2.75x material thickness |
.100 -.134 in. | bend radius + 2.5x material thickness | bend radius + 2.5x material thickness | bend radius + 2.5x material thickness |
.160+ | bend radius + 3.0x material thickness | bend radius +3.5x material thickness | bend radius + 4.0x material thickness |
Additional design considerations:
Placing Features Near Bends
Placing features strategically in sheet metal design enhances complexity and functionality, but care must be taken when positioning them near bends. As the material stretches during the forming process, features located too close to bends may experience distortion. The appropriate distance from bends depends on factors like material type, thickness, and bend radius. Refer to the table below for recommended distance guidelines to minimize distortion.
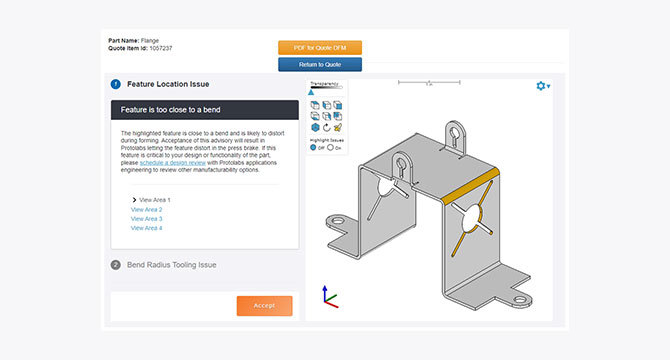
Feature Proximity | |||
---|---|---|---|
Material Thickness | Copper / Aluminum | Galv. / Galvnl. / CRS | Stainless Steel |
.024 -.050 in. | bend radius + 3.0x material thickness | bend radius + 3.5x material thickness | bend radius + 3.5x material thickness |
.060 -.090 in. | bend radius + 2.5x material thickness | bend radius + 2.75x material thickness | bend radius + 2.75x material thickness |
.100 -.134 in. | bend radius + 2.5x material thickness | bend radius + 2.5x material thickness | bend radius + 2.5x material thickness |
.160+ | bend radius + 3.0x material thickness | bend radius +3.5x material thickness | bend radius + 4.0x material thickness |
Additional design considerations:
Bend Radius Outside Tooling Range
KingStar Mold offers internal bend radius tooling options ranging from 0.01 in. to 1 in.
Note: As KingStar Mold primarily uses air bending technology, the actual radius on a physical part may slightly differ from the tool used during the forming process.
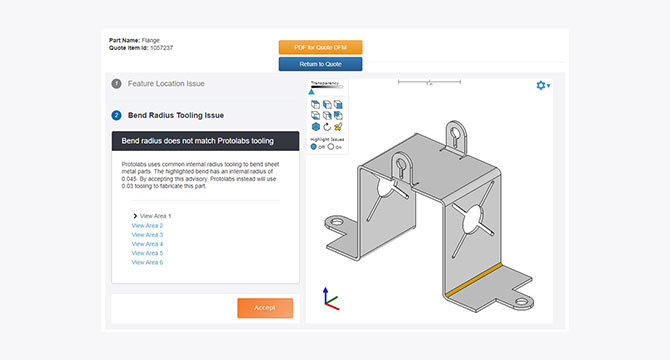
internal bend radius tooling options | |||
---|---|---|---|
0.01 in. | 0.03 in.* | 0.06 in.* | 0.09 in.* |
0.12 in.* | 0.25 in. | 0.375 in. | 0.5 in. |
0.188 in. | 0.5 in. | 0.625 in. | 0.75 in. |
Additional design considerations:
Hardware Insert and Sheet Stock Compatibility
KingStar Mold offers a broad selection of PEM® fasteners for your sheet metal parts. To ensure proper installation and functionality, follow these two key guidelines for hardware insert and sheet stock material compatibility:
- The sheet metal material should be softer than the hardware material to ensure compatibility.
- Sufficient grip is necessary for the insert to securely seat into the sheet metal during installation.
Refer to the table below for a reference guide on compatible insert and material types.

Part Material | Common Hardware Types | Standard hardware materials | |||
Studs/Pins | Clinch Nuts | Standoffs | Other | ||
Stainless Steel 304, Stainless Steel 316 | FH4, FHP, TP4 | SP, SMPP | SO4, TSO4, BSO4 | A4, F4 | 400 Series Stainless Steel |
Pre-plated Steel (galvanneal, galvanized), Cold Rolled Steel (CRS) | FH, TFH, FHL | S, SS | SO, TSO, BSO | LK, PL, AS, CFN | Steel |
Aluminum 5052, Aluminum 6061 | FHA | CLA | SOA, TSOA, BSOA | LKA, RAA | Aluminum |
FHS, FHLS, TPS | CLS, CLSS, SMPS | SOS, TSOS, BSOS | F, FE, TDS, LKS, AC, FEX | Stainless Steel |
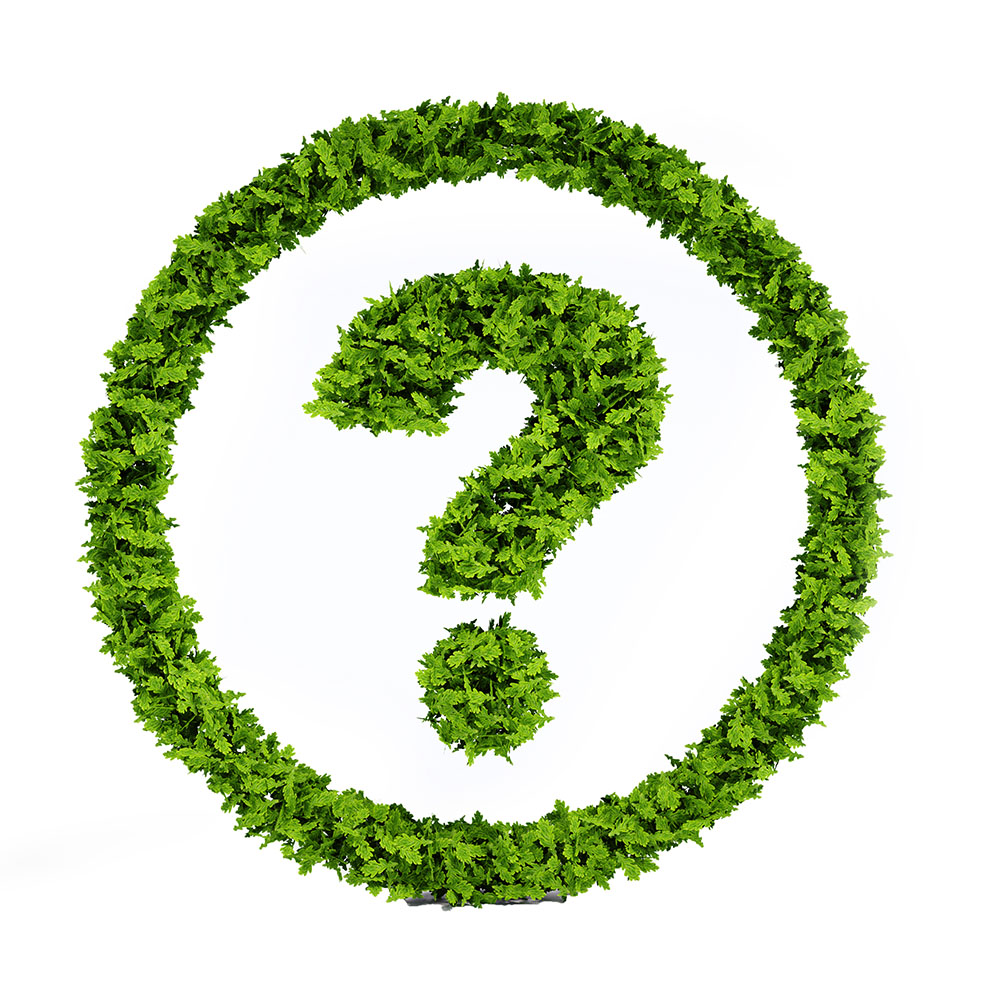