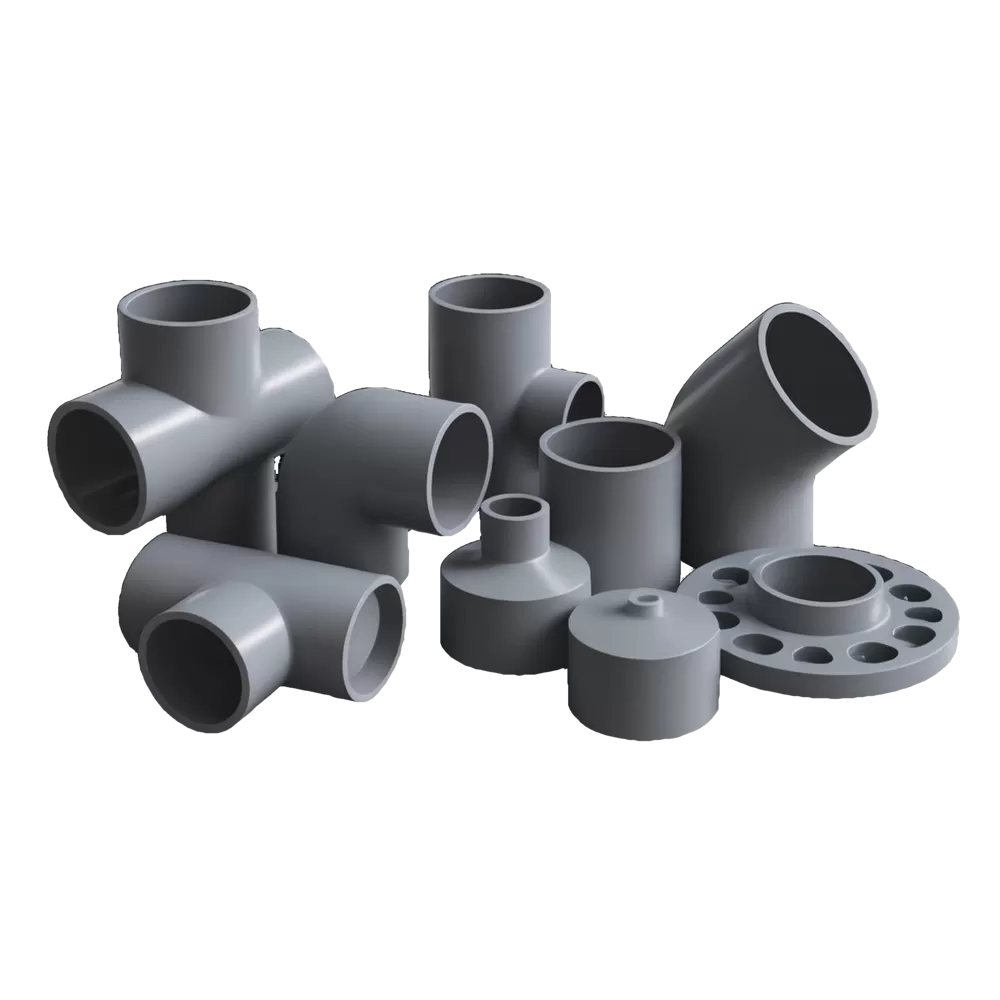
-
Resources for The Complete Guide to PVC Injection Molding
What is PVC?

PVC, or Polyvinyl Chloride, was first created in the 1800s but became widely used in the 1920s after it was made more flexible.
This synthetic plastic polymer is made from vinyl chloride, which is derived from petroleum. PVC is the third most commonly used plastic globally, following polyethylene and polypropylene, with around 40 million tons produced annually.
There are two types of PVC: rigid and flexible. Rigid PVC is used for products like pipes, doors, and windows, while flexible PVC is commonly used for plumbing, electrical cables, flooring, and inflatable items.
PVC is a white, brittle solid available in both powder and granule forms. Known for its resistance to chemicals, weather, and corrosion, it is a durable and versatile material.
Plasticizers can be added to make PVC more flexible. It also has excellent electrical insulation properties, self-extinguishes if ignited, and is inexpensive to produce.
PVC is widely used across various industries, including construction, healthcare, automotive, and packaging. It is commonly found in products such as pipes, window frames, electrical cables, medical devices, clothing, and much more.
What characteristics does Polyvinyl Chloride (PVC) possess?
Electrical Properties
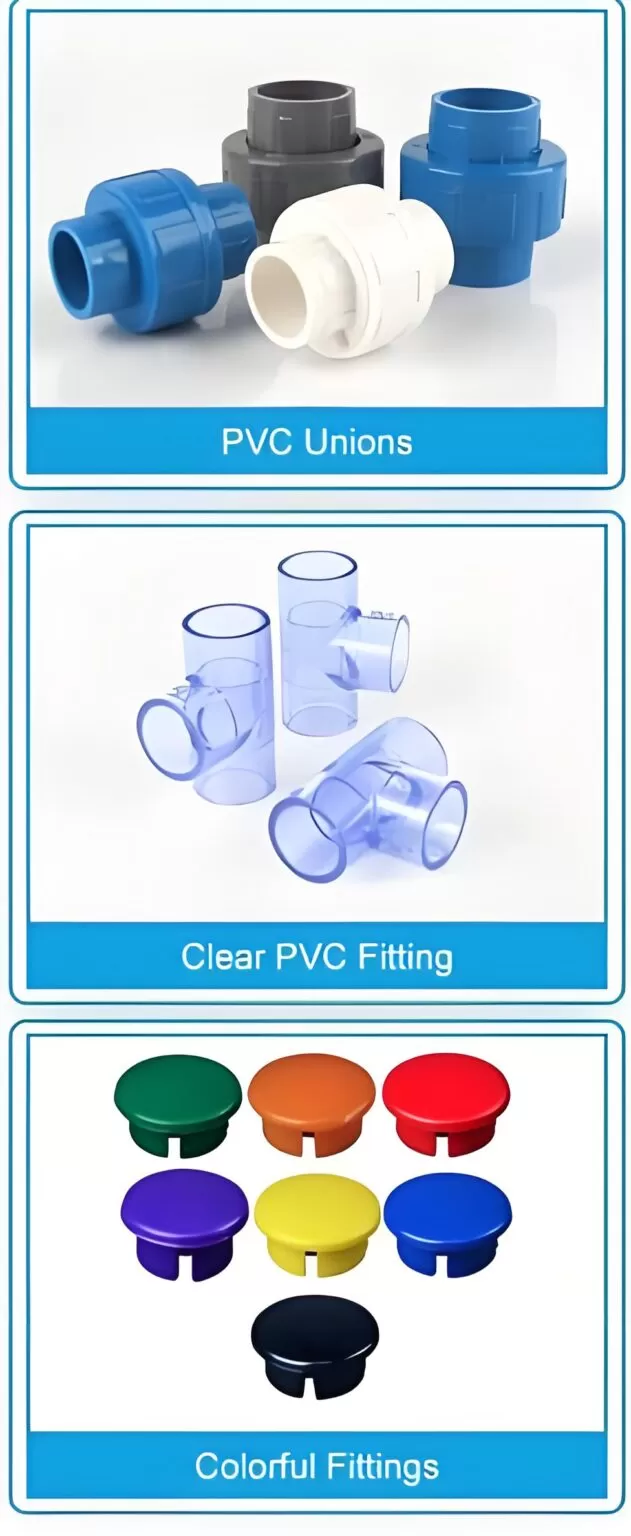
Flame Retardancy
PVC is self-extinguishing, meaning it stops burning once the fire source is removed. This is due to its high chlorine content, which helps prevent the spread of fire.
Mechanical Properties
- Abrasion Resistance: PVC is tough, lightweight, and highly resistant to abrasion, making it suitable for a variety of applications.
- Strength: Rigid PVC has a yield strength ranging from 4,500 to 8,700 psi (31-60 MPa), while flexible PVC ranges from 1,450 to 3,600 psi (10.0-24.8 MPa).
Chemical Resistance
- Resistance to Inorganic Chemicals: PVC is resistant to most inorganic chemicals, including weak acids, bases, and aliphatic hydrocarbons.
- Resistance to Organic Chemicals: Some types of PVC can be damaged by ketones, esters, aromatic hydrocarbons, and nitro compounds.
Cost/Performance Ratio
- Cost-Effective: PVC is an affordable material that offers long-lasting durability with minimal maintenance.
Additives
- Plasticizers: These additives make PVC easier to work with and enhance its toughness and strength.
- Heat Stabilizers: Heat stabilizers protect PVC from degradation during manufacturing and prevent breakdown when exposed to sunlight.
What are the properties of PVC?
PVC is a thermoplastic polymer, and its properties are generally categorized into two types: rigid PVC and soft PVC.
Property | Unit of measurement | Rigid PVC | Soft PVC |
Density | g/cm3 | 1.3–1.45 | 1.1–1.35 |
Thermal conductivity | W/(m·K) | 0.14–0.28 | 0.14–0.17 |
Yield strength | psi | 4,500–8,700 | 1,450–3,600 |
MPa | 31–60 | 10.0–24.8 | |
Flexural strength | psi | 10,500 | — |
MPa | 72 | — | |
Compression strength | psi | 9,500 | — |
MPa | 66 | — |
What are the advantages of Injection Molding PVC?
Injection molding PVC (Polyvinyl Chloride) possesses several advantages, including:
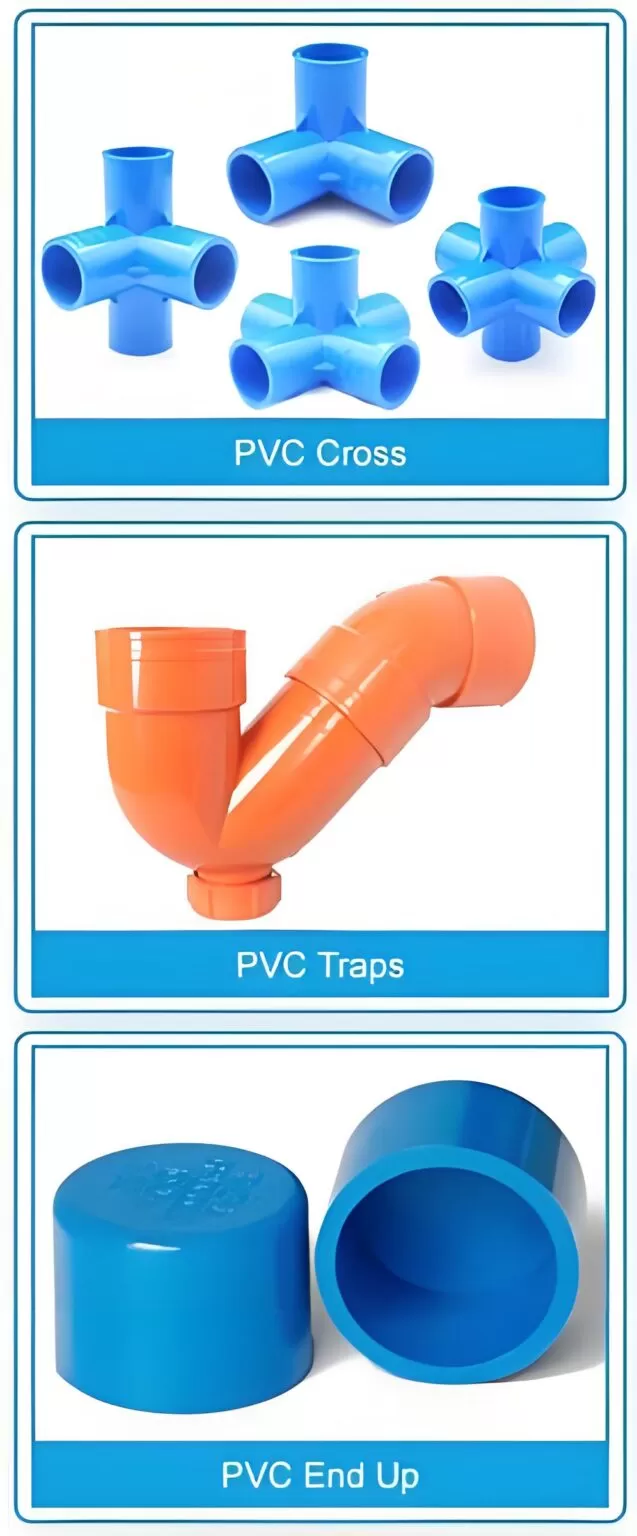
- Cost-Effective: PVC injection molding is a cost-efficient method for producing large quantities of products, such as pipes, fittings, and other plastic components.
- High-Quality Products: PVC injection molding produces high-quality products with precise dimensions, smooth surfaces, and consistent wall thickness.
- Consistent Quality: The injection molding process ensures uniform quality by injecting molten PVC into the mold under high pressure.
- Fast Production: PVC injection molding enables high-volume production with quick turnaround times, making it a fast and efficient process.
- Low Labor Costs: Automation of the injection molding process reduces labor costs, benefiting manufacturers.
- Wide Range of Applications: PVC injection molding is versatile, used to create products like pipes, fittings, tubing, and other plastic components.
- Resistance to Corrosion: PVC’s resistance to corrosion makes it ideal for applications exposed to chemicals, acids, or other corrosive substances.
- Fire-Resistant: PVC is fire-resistant and produces minimal smoke, making it a good choice for applications requiring fire safety.
- Easy Installation: PVC products are easy to install using solvent cement or heat fusion, making them popular for plumbing and piping.
- Recyclable: PVC is recyclable, making it an environmentally-friendly option for both manufacturers and consumers.
- Wide Temperature Range: PVC can withstand a broad range of temperatures, making it suitable for applications with extreme temperature conditions.
- Chemical Resistance: PVC is resistant to many chemicals, including acids, bases, and solvents, making it ideal for applications exposed to chemicals.
What are the shortcomings of Injection Molding PVC?
While injection molding PVC offers numerous advantages, it also comes with certain shortcomings, including:
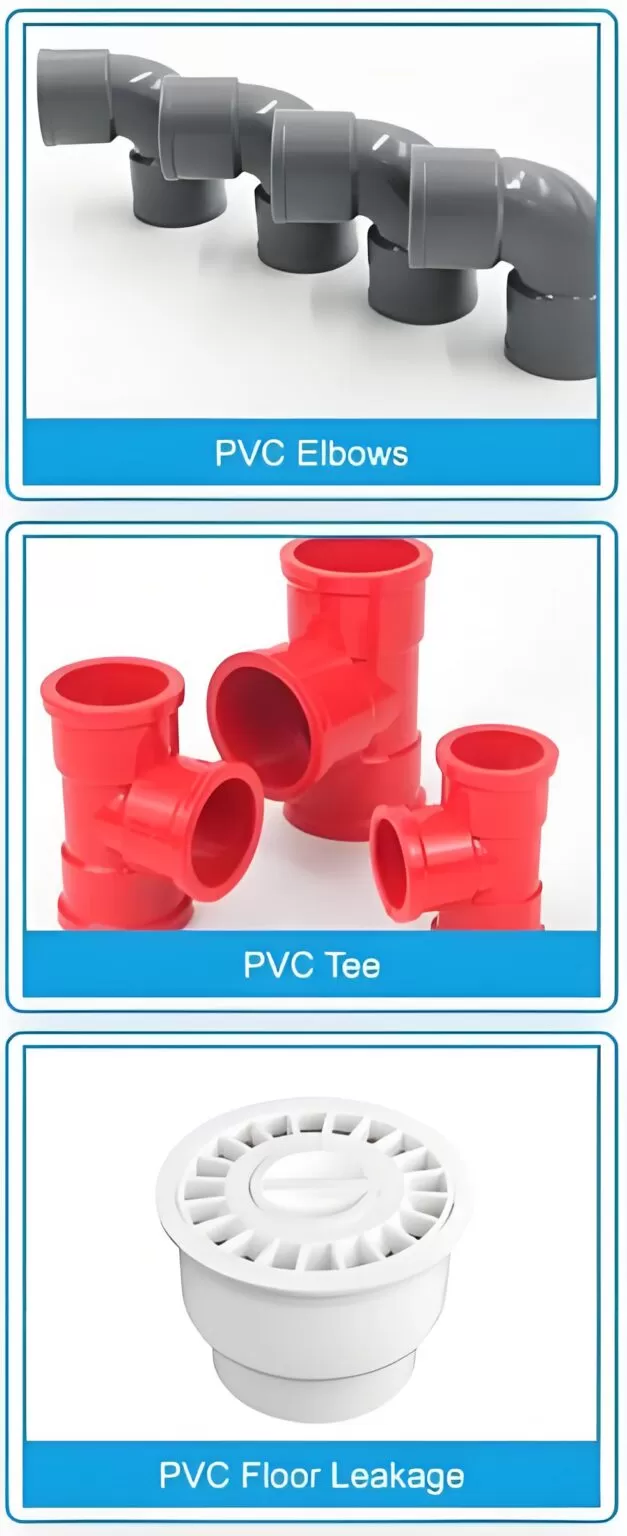
- Higher Up-Front Costs: PVC material is highly corrosive, and the molds are prone to rust during injection molding. Stainless steel materials like 4Cr13 or S136 are required for the molds, making the initial cost higher than for other plastic materials.
- Environmental and Health Concerns: Burning PVC releases harmful dioxins and chlorine, which are detrimental to both the environment and human health. Additionally, PVC products do not break down easily, contributing to plastic waste.
- Toxicity: PVC emits toxic fumes when burned or melted, which are hazardous to health.
- Limited Heat Resistance: PVC has lower heat resistance compared to other plastics. It can degrade during injection molding at high temperatures, releasing harmful gases.
- Limited Flexibility: PVC is a rigid material, making it difficult to form complex shapes or create products that require flexibility.
- UV Degradation: PVC can degrade when exposed to UV light over time, leading to discoloration and reduced functionality.
- Softening: PVC softens at high temperatures, which can cause it to lose its shape and performance.
- Difficult to Bond: PVC is challenging to bond with other materials, making it harder to create multi-part products.
- Limited Recyclability: Although PVC is recyclable, it is difficult to process due to its complex composition.
- Limited Color Options: PVC is difficult to color, which limits the options for achieving specific hues during injection molding.
- Moisture Absorption: PVC can absorb moisture, which may cause it to deform and negatively affect its performance over time.
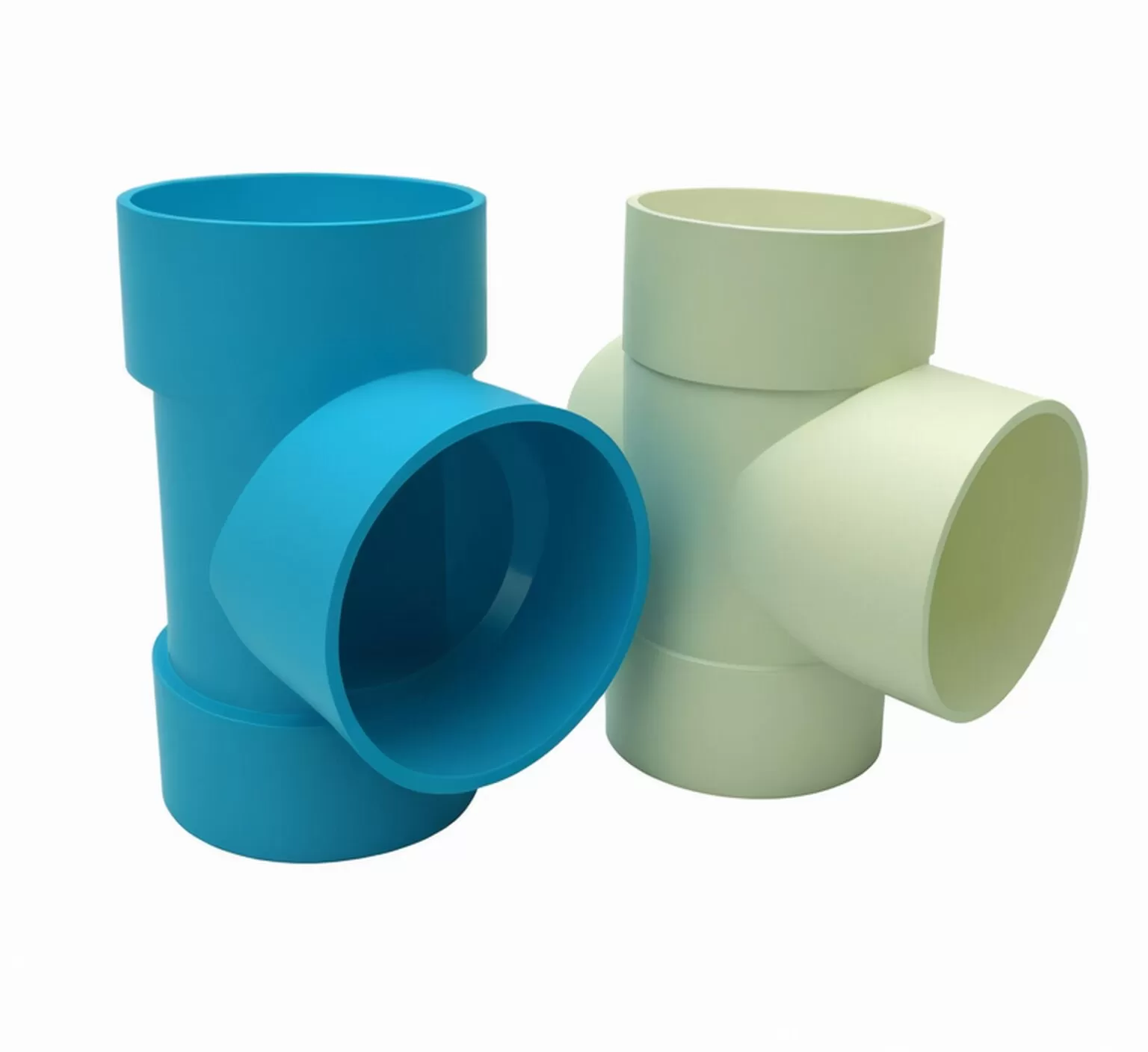
Can PVC be Injection Molded?
Indeed, PVC can be injection molded, and PVC injection molding is a popular manufacturing process used to create a wide range of plastic products and parts.
PVC is a versatile material, suitable for molding both flexible items, such as soft toys, and rigid structures like pipes. It is cost-effective, easily recyclable, dense, and offers high strength.
For successful PVC injection molding, it’s important to carefully consider factors such as moisture content, temperature control, injection pressure and speed, and mold design.
How to Perform PVC Injection Molding: A Step-by-Step Guide
PVC injection molding is a detailed process that turns raw PVC material into durable plastic parts. Whether you’re a beginner, professional, or student, understanding the step-by-step procedure is essential for achieving the best results. This guide will walk you through everything, from temperature settings to injection speeds, to help you master PVC injection molding.
Injection Molding PVC Specifications
Here are some common specifications for injection molding PVC (Polyvinyl Chloride):
Material Properties:
PVC Resin | UPVC (unplasticized) or CPVC(plasticized) depending on the application |
Density | 1.35-1.45 g/cm³ |
Melt Flow Index (MFI) | 3-15 g/10 min (depending on the grade) |
Vicat Softening Point | 70-120°C |
Tensile Strength | 40-60 MPa |
Elongation at Break | 100-300% |
Flexural Strength | 60-100 MPa |
Tooling and Mold Design:
Mold Material | Stainless steel mold materials(4Cr13, 2344, S136) Choose different mold materials according to product quantity |
Mold Temperature | 50-100°C |
Cooling System | Water or air cooling |
Gate Type | Sub-gate, edge gate, or corner gate |
Ejection System | Mechanical or hydraulic ejection |
Injection Molding Process:
Melt Temperature: | 180-220°C |
---|---|
Injection Pressure | 50-150 bar |
Injection Speed | 10-50 mm/s |
Cooling Time | 10-30 seconds |
Ejection Force | 5-20 kN |
Design Guidelines for PVC Injection Molding
Here are some design guidelines for PVC injection molding to ensure your parts meet the required specifications and standards while being produced efficiently and cost-effectively.
- Wall Thickness: The ideal wall thickness for PVC is between 1.2-3.5mm. Too thick walls can lead to sink marks, warping, and longer cycle times, while too thin walls may result in weak parts or incomplete filling.
- Ribs: Ribs should be 0.5-0.7 times the nominal wall thickness. To prevent sink marks, the height of the ribs should be no more than three times the rib thickness.
- Draft Angles: Ensure a minimum draft angle of 1-2 degrees on all vertical surfaces to aid in easy part ejection. If the surfaces are textured, consider a draft angle of 3-5 degrees.
- Corners and Edges: Avoid sharp corners. Use rounded corners with a radius at least 0.5 times the wall thickness to reduce stress concentrations and improve material flow.
- Bosses and Threads: For threads, use threaded inserts instead of molding threads directly into the part. Integral bosses should have a draft angle and rounded corners to ensure ease of production and proper material flow.
What are the Applications of PVC Injection Molding?
PVC injection molding is a versatile process that can make all kinds of stuff, like:
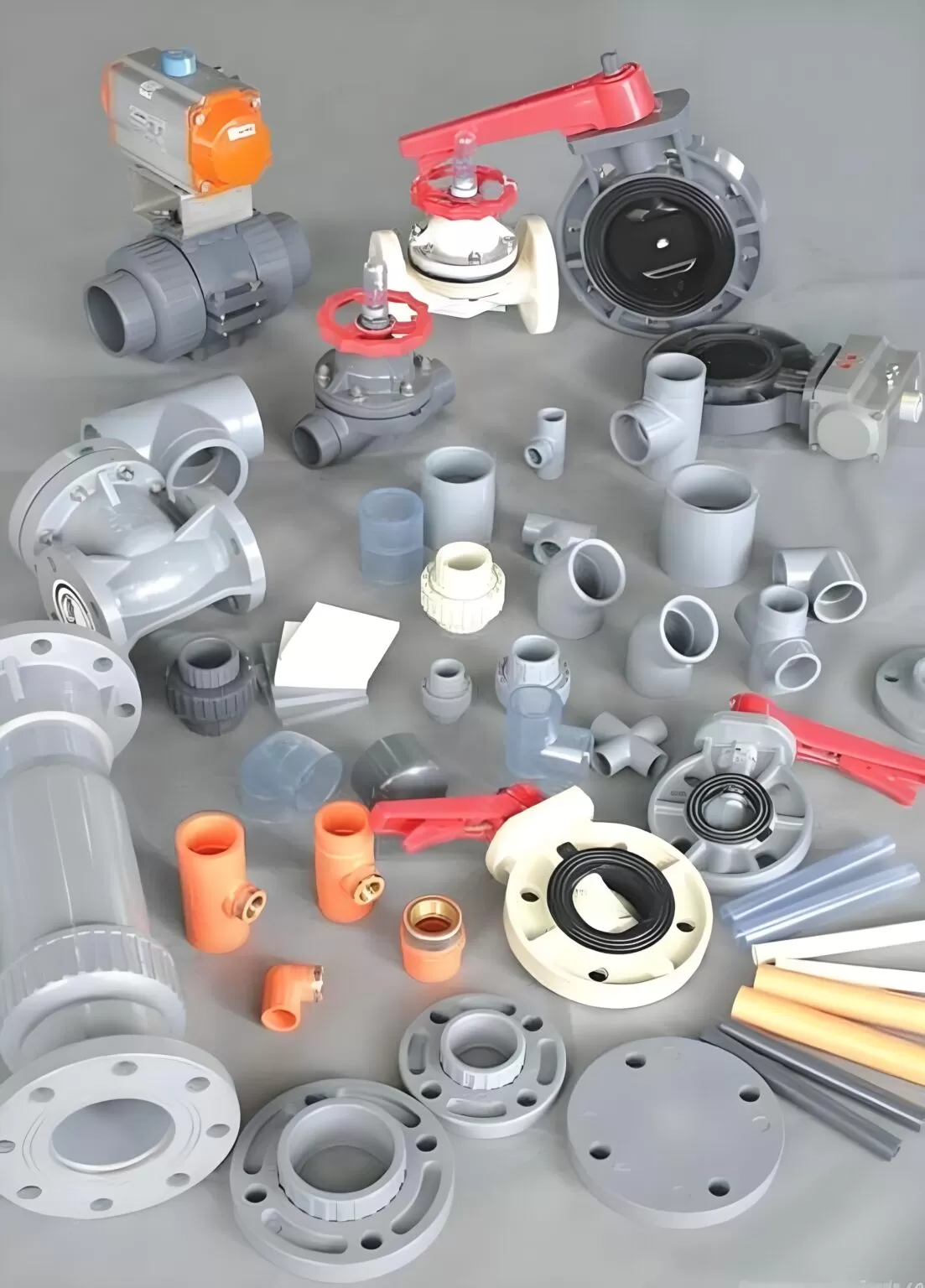
Optimization Solutions Provided For Free
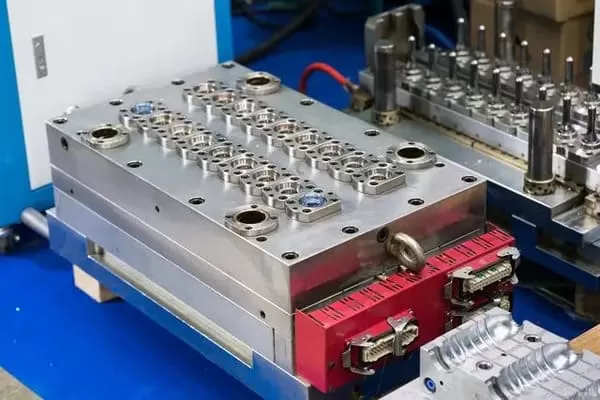