Materials that KingStar Uses in CNC Machining
CNC machining is a highly versatile process capable of working with a broad range of materials, making it ideal for producing complex, precise parts across various industries. Materials can be classified into metals, plastics, composites, and others, each offering unique properties for different applications. Metals such as aluminum, stainless steel, titanium, and brass are commonly used for their strength and durability, while plastics like POM, acrylic, and nylon provide flexibility and lightweight solutions. Composites combine multiple materials to achieve enhanced performance characteristics, and other materials like ceramics can also be machined for specialized uses. CNC machining ensures that these materials are shaped, cut, and milled to exact specifications, meeting tight tolerances for any project.
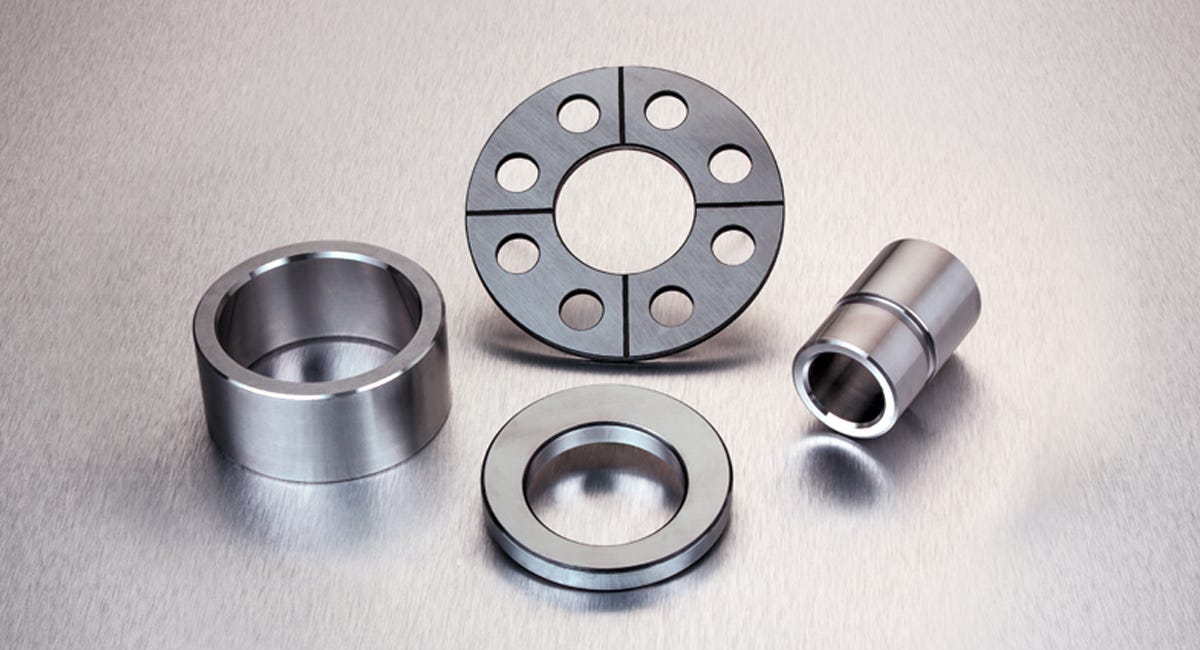
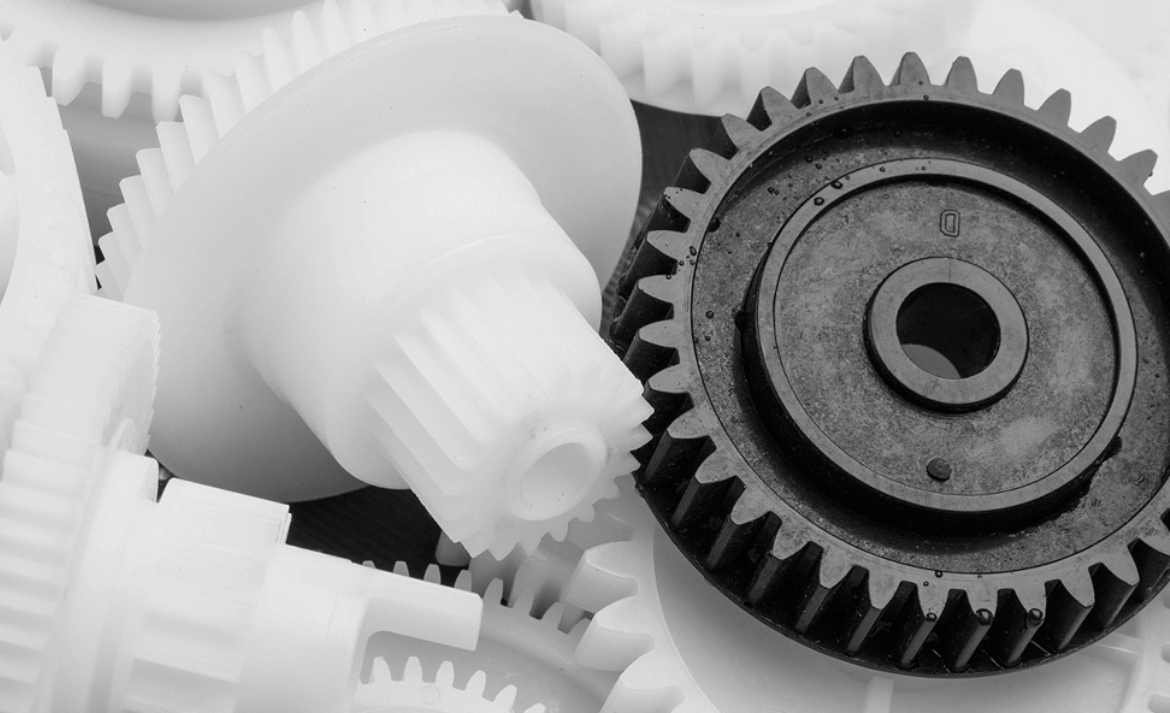
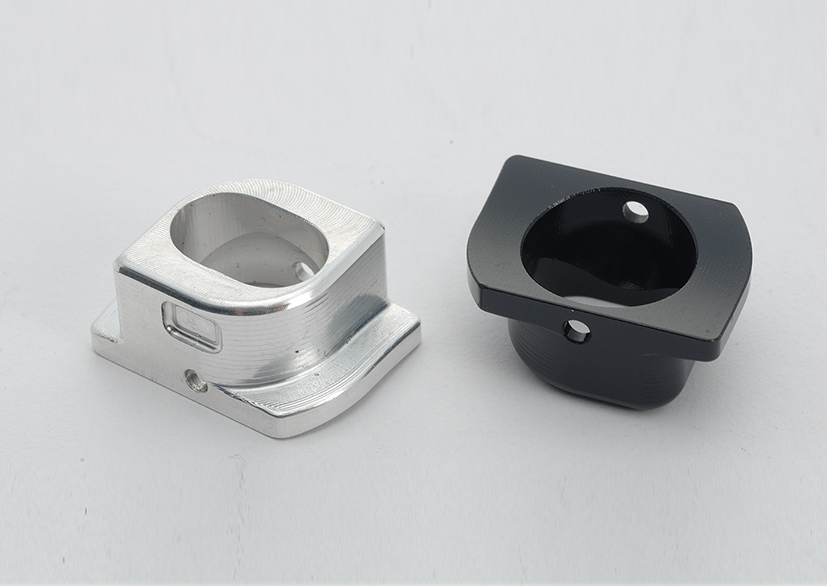
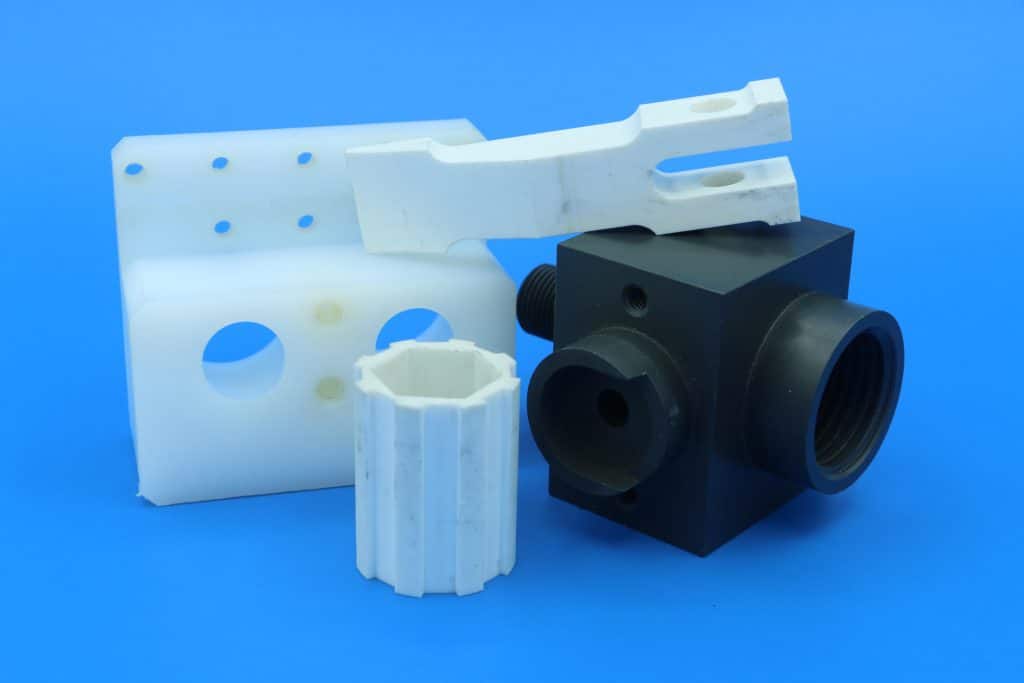
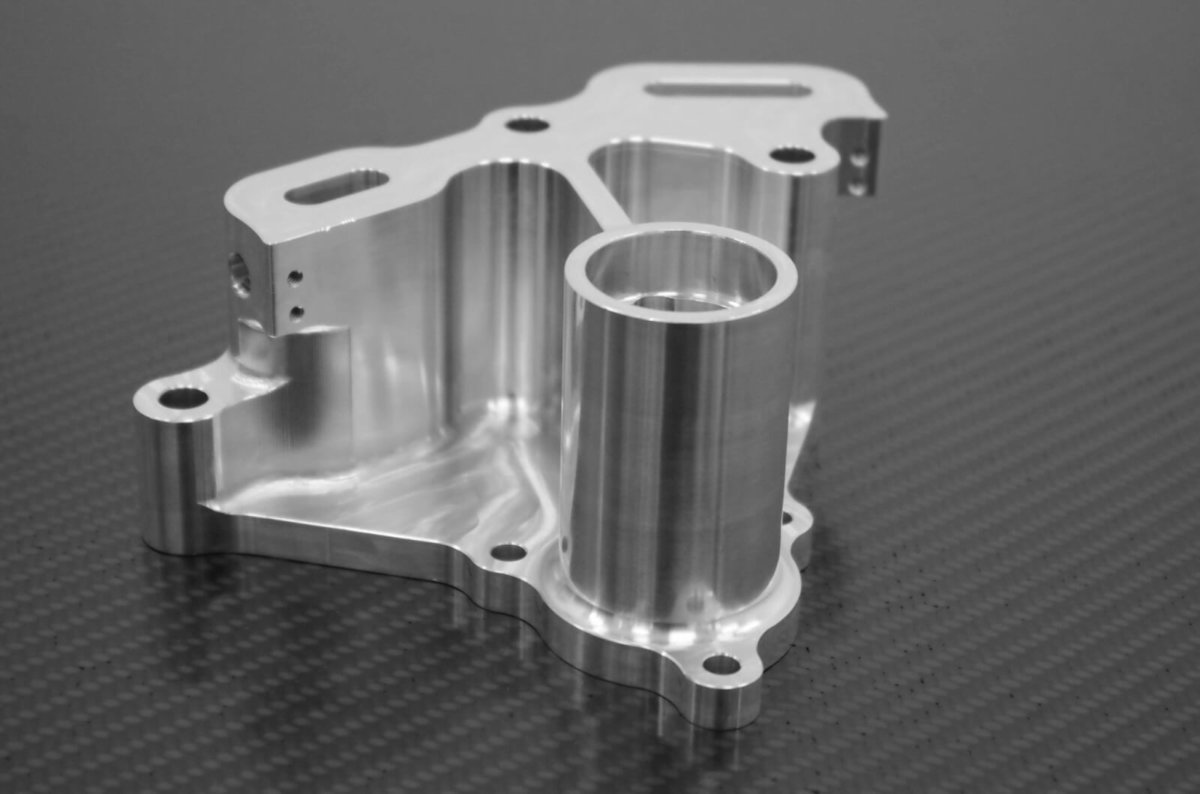
Comparison Between CNC Machining Metal Materials
Material | Density (g/cm³) | Yield Strength (MPa) | Hardness (HB) | Machinability | Tensile Strength (MPa) | Applications |
---|---|---|---|---|---|---|
Aluminum 6061 | 2.70 | 275 | 95 | High | 310 | Aerospace, automotive, structural components |
Stainless Steel 304 | 7.93 | 215 | 150 | Medium | 520 | Food processing, medical devices, marine equipment |
Titanium Ti-6Al-4V | 4.43 | 880 | 330 | Low | 900 | Aerospace, medical implants, high-performance parts |
Brass (C36000) | 8.49 | 150 | 65 | High | 345 | Plumbing, electrical connectors, decorative parts |
Carbon Steel (1045) | 7.85 | 350 | 120 | Medium | 570 | Machinery parts, shafts, automotive components |
POM (Acetal) | 1.41 | 55 | 70 | High | 65 | Precision gears, bearings, automotive parts |
Nylon 6 | 1.15 | 50 | 80 | Medium | 75 | Mechanical parts, automotive, electrical insulation |
Aluminum 2024 | 2.78 | 325 | 120 | High | 470 | Aircraft structures, military, aerospace components |
Copper (C11000) | 8.92 | 70 | 40 | Medium | 210 | Electrical wiring, heat exchangers, electronics |
Acrylic (PMMA) | 1.19 | 90 | 20 | High | 70 | Optical lenses, signage, automotive lighting |
Magnesium AZ31 | 1.78 | 150 | 60 | Medium | 230 | Aerospace, automotive, military, electronics |
Tool Steel (A2) | 7.85 | 450 | 450 | Low | 780 | Cutting tools, dies, molds |
Plastic Materials for CNC Machining
Material | Description | Lead Time | Minimum Wall Thickness | Price |
---|---|---|---|---|
ABS | ABS offers excellent impact resistance and is easy to machine, making it a popular choice for rugged housings, automotive components, and everyday consumer goods. | ≈ 6 days | 0.8mm | $$ |
PEEK | PEEK delivers high strength and superior heat resistance, ideal for aerospace, medical implants, and demanding industrial applications. | ≈ 8 days | 0.8mm | $$$$$ |
PA (Nylon) | Nylon is abrasion-resistant and strong, commonly used in gears, mechanical linkages, and automotive structural parts. | ≈ 6 days | 0.8mm | $$ |
PMMA (Acrylic) | PMMA is lightweight and transparent, making it a great option for lenses, displays, and optical components. | ≈ 6 days | 0.8mm | $ |
PBT | PBT combines mechanical strength and dimensional stability, ideal for connectors, automotive parts, and electronic housings. | ≈ 6 days | 0.8mm | $$ |
PTFE (Teflon) | PTFE resists heat and chemicals, making it perfect for seals, gaskets, and non-stick components. | ≈ 6 days | 0.8mm | $$ |
PEI | PEI maintains structural integrity at elevated temperatures and is suitable for aerospace and high-performance electronics. | ≈ 6 days | 0.8mm | $$ |
PVC | PVC is known for chemical resistance and rigidity, used in piping, electrical insulation, and construction parts. | ≈ 6 days | 0.8mm | $$ |
POM | POM offers high stiffness and wear resistance, often used for precision parts like gears and bearings. | ≈ 6 days | 0.8mm | $$ |
LDPE | LDPE is soft and flexible with impact resistance, widely applied in containers, tubing, and packaging. | ≈ 6 days | 0.8mm | $$ |
PAI | PAI withstands extreme mechanical and thermal stress, ideal for aerospace and high-end automotive applications. | ≈ 8 days | 0.8mm | $$$$$ |
PET | PET is a tough, durable plastic used in packaging, mechanical covers, and textile-related components. | ≈ 6 days | 0.8mm | $ |
PC | PC offers toughness and optical clarity, commonly used for protective covers, lenses, and structural parts. | ≈ 6 days | 0.8mm | $$ |
FR-4 | FR-4 is flame-retardant and structurally stable, ideal for printed circuit boards and insulation panels. | ≈ 6 days | 0.8mm | $ |
PP | PP provides good fatigue resistance and chemical stability, ideal for automotive and lab equipment. | ≈ 6 days | 0.8mm | $ |
HIPS | HIPS is impact-resistant and machinable, great for casings, models, and prototyping. | ≈ 6 days | 0.8mm | $$ |
HDPE | HDPE has excellent impact resistance and chemical tolerance, used in industrial containers and piping. | ≈ 6 days | 0.8mm | $$ |
PPS | PPS offers thermal and chemical resistance, often chosen for automotive, electronics, and pump components. | ≈ 6 days | 0.8mm | $$$ |
PS | PS is lightweight and dimensionally stable, ideal for disposable packaging and rigid structural prototypes. | ≈ 6 days | 0.8mm | $$ |
Bakelite | Bakelite is heat-resistant and electrically insulating, used in switches, sockets, and vintage casings. | ≈ 6 days | 0.8mm | $$ |
UPE | UPE features excellent abrasion resistance and low friction, ideal for guide rails and wear components. | ≈ 6 days | 0.8mm | $$ |
PE | PE is flexible and lightweight with strong chemical resistance, commonly used in tanks, linings, and ducts. | ≈ 6 days | 0.8mm | $$ |
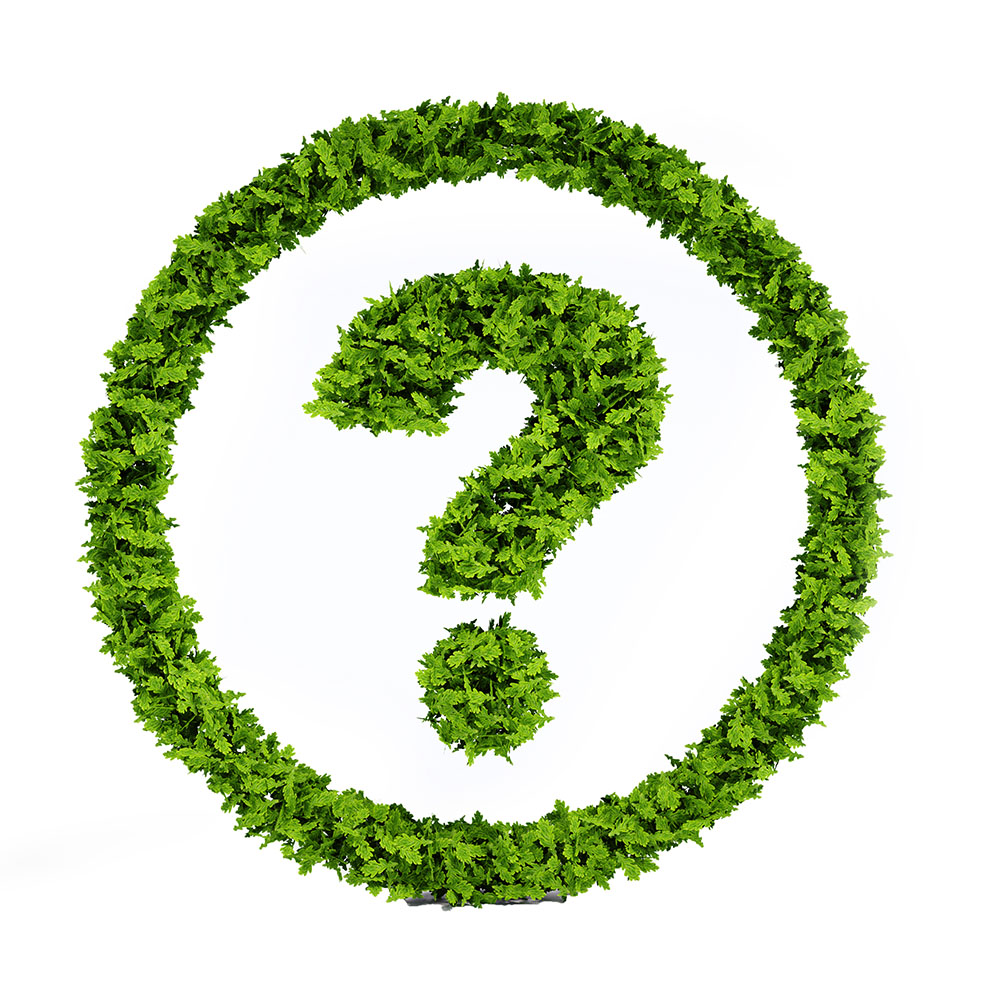
Frequently Asked Questions
At KingStar Mold, we provide a range of post-machining services to enhance the functionality and appearance of CNC parts, including:
-
Surface finishing: Anodizing, electroplating, polishing, and coatings for corrosion resistance and improved aesthetics.
-
Assembly: We offer assembly services to integrate CNC parts into larger systems or products.
-
Inspection: We conduct final dimensional inspections using Coordinate Measuring Machines (CMM) to ensure all parts meet quality and tolerance specifications.
-
Packaging: Customized packaging options to ensure parts are shipped safely and securely to customers.
Yes, CNC machining is ideal for producing parts with high precision and tight tolerances. We can achieve tolerances as tight as ±0.001 inches (±0.025 mm), depending on the material and machining process. This makes CNC machining suitable for critical applications in aerospace, medical, automotive, and other industries requiring exacting specifications.
The most commonly used metals in CNC machining include aluminum, steel (such as 304, 316, and stainless steel), brass, copper, and titanium. Each metal offers unique properties:
-
Aluminum: Lightweight, corrosion-resistant, and easy to machine, ideal for automotive, aerospace, and consumer goods.
-
Stainless Steel: Known for its strength, corrosion resistance, and durability, commonly used for medical devices, aerospace, and structural components.
-
Brass: Offers excellent machinability and is widely used in fittings, valves, and electrical components.
-
Titanium: High strength-to-weight ratio and resistance to extreme temperatures, making it ideal for aerospace and medical applications.
Yes, KingStar Mold regularly machines high-performance engineering plastics including PEEK, PAI, PTFE, and PPS. These materials require precise tooling and process control, which we handle in-house using our advanced CNC setups.