Air bubbles are a common defect in injection molding, occurring when gas pockets or voids become trapped within the molded part. These bubbles can significantly impact the product’s appearance, mechanical properties, and overall quality. While they may seem like a minor surface flaw, they can compromise the part’s strength and durability, making it prone to cracks or failure under stress.
Effectively addressing air bubbles is essential for maintaining high-quality molded parts. If left unresolved, bubbles can lead to surface irregularities, internal weaknesses, and even part rejection, resulting in wasted materials, increased production costs, and reduced customer satisfaction.
As a leading custom plastic part injection molding company, KingStar Mold‘s engineering team specializes in identifying and eliminating injection molding defects, including air bubbles. With our advanced molding techniques, precision mold design, and thorough quality control processes, we help manufacturers produce flawless, high-performance plastic components.
- 1. What Are Air Bubbles in Injection Molded Parts?
- 2. Types of Bubbles Based on Causes
- 3. Machine-Related Causes and Solutions
- 4. Mold-Related Causes and Solutions
- 5. Material-Related Causes and Solutions
- 6. Process-Related Causes and Solutions
- 7. Preventive Measures for Bubble-Free Molding
- 8. KingStar Mold’s Expertise in Defect Prevention
- Conclusion
1. What Are Air Bubbles in Injection Molded Parts?
Air bubbles in injection molded parts refer to gas pockets or voids trapped inside the molded material during the manufacturing process. These bubbles often occur when air or gas fails to escape the mold cavity, becoming encapsulated within the plastic. This leads to aesthetic flaws and can weaken the part’s structural integrity.
2.1 Difference from Vacuum Voids
It is important to distinguish air bubbles from vacuum voids, as they have different causes and solutions:
- Bubbles:
- Caused by trapped air or gas during the filling stage.
- Typically visible immediately after demolding.
- More common near weld lines or flow ends.
- Vacuum Voids:
- Form due to shrinkage during cooling, creating internal gaps.
- Often appear after the part has cooled.
- Frequently occur in thicker sections with uneven cooling.
2.2 Visual Characteristics
Recognizing the visual traits of air bubbles and voids helps with accurate defect diagnosis:
- Bubbles:
- Appear as small, scattered, or clustered gas pockets.
- Often located near weld lines or the flow front.
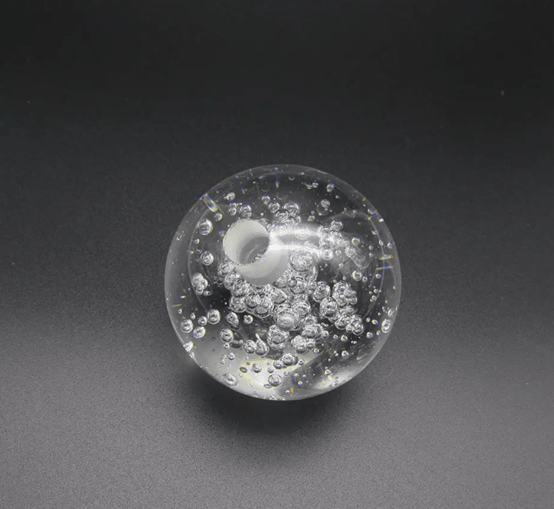
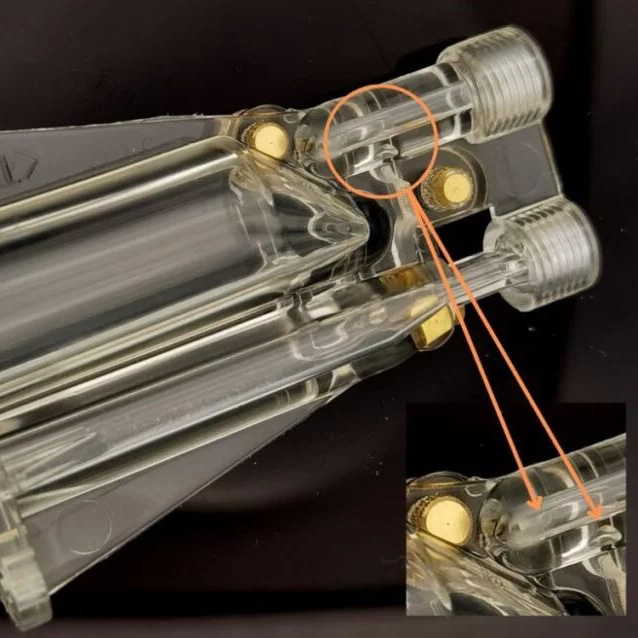
- Voids:
- Typically larger and singular, rather than scattered.
- Most commonly found in thicker or uneven wall sections.
2. Types of Bubbles Based on Causes
Understanding the different types of air bubbles in injection molded parts is key to effectively preventing and addressing them. The causes of these bubbles can vary significantly, each with distinct characteristics and solutions.
Type | Cause | Appearance |
Moisture-Related Bubbles | Insufficient drying of raw materials, leading to plastic hydrolysis. | Small, dispersed bubbles near the surface or moisture-rich areas. |
Vacuum Bubbles | Uneven cooling or incomplete mold filling, causing trapped vacuum. | Larger bubbles in thicker sections with noticeable shrinkage. |
Thermal Degradation Bubbles | Excessive heating decomposes resin, releasing gaseous byproducts. | Irregular, discolored bubbles; may show black streaks or burns. |
Trapped Air Bubbles | Air trapped during plasticizing or filling due to rapid injection or poor venting. | Small, scattered bubbles near weld lines or flow ends. |
3. Machine-Related Causes and Solutions
Machine-related issues can significantly contribute to the formation of air bubbles in injection molded parts. Addressing these issues is crucial for improving part quality and preventing defects.
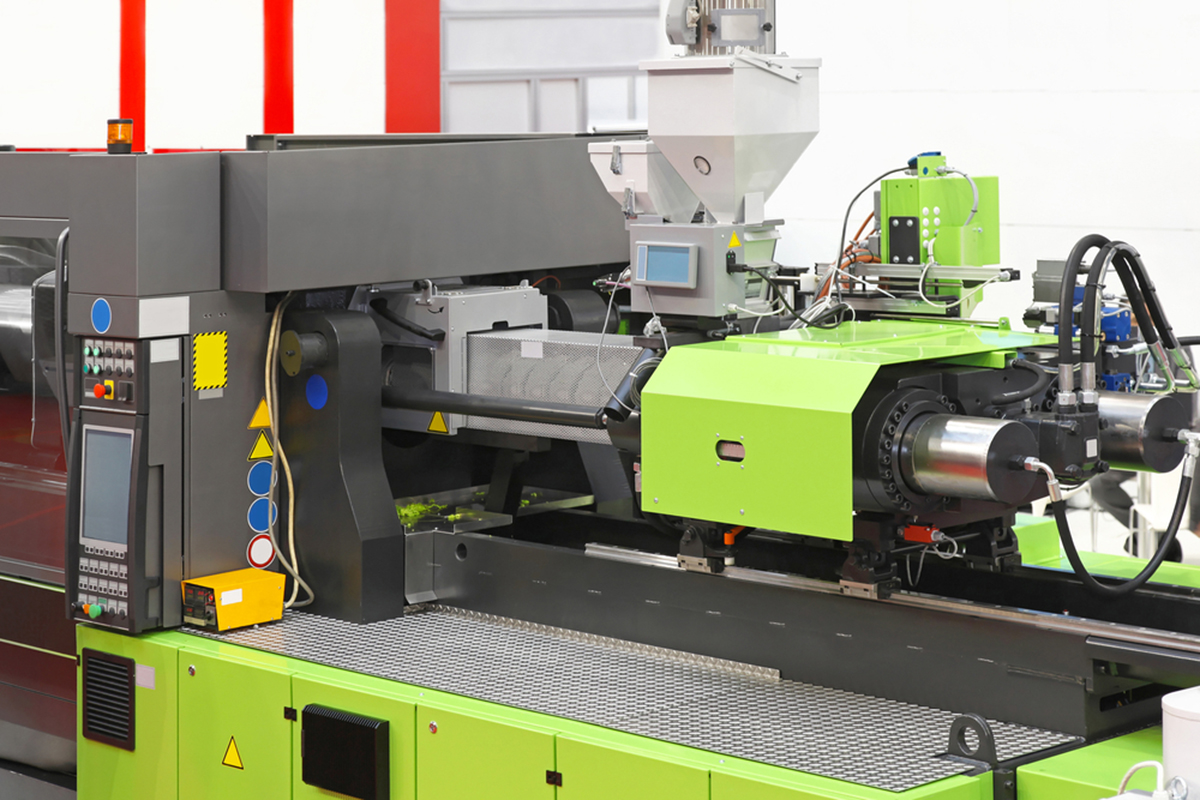
3.1 Low Injection Pressure or Insufficient Holding Time
- Problem: When injection pressure is too low or holding time is insufficient, gases trapped in the material cannot escape, leading to the formation of bubbles.
- Solutions:
- Increase injection pressure to ensure proper material flow and compaction.
- Extend hold time to allow trapped gas to escape before the material solidifies.
- Maintain a material cushion (typically between 1/8″ and 1/4″) at the end of the injection stroke to ensure better packing and gas venting.
3.2 Improper Temperature Profile
- Problem: Inconsistent or incorrect heating during the injection molding process can cause gas to form in the resin, leading to bubbles.
- Solutions:
- Always follow resin supplier’s temperature guidelines to maintain proper heating.
- Adjust barrel temperature in 10°F increments to prevent overheating or underheating of the material.
3.3 Excessive Injection Speed
- Problem: High injection speeds can generate excessive shear heat, which may cause decomposition of the material and trap air inside the part.
- Solutions:
- Slow down the injection speed to reduce shear heat and allow for better flow and venting.
- Gradually increase the injection speed until bubbles disappear, ensuring that the material fills the cavity properly without excessive heat generation.
3.4 Insufficient Back Pressure
- Problem: Low back pressure during the molding process prevents proper packing of the material, allowing air pockets to form in the mold.
- Solutions:
- Gradually increase back pressure (between 50–300 psi) to help compact the material and reduce air entrapment.
- Always follow resin supplier recommendations for optimal back pressure settings to avoid air bubble formation.
4. Mold-Related Causes and Solutions
Mold-related factors play a crucial role in the formation of air bubbles. Ensuring proper mold design, venting, and temperature control is vital for preventing defects in molded parts.
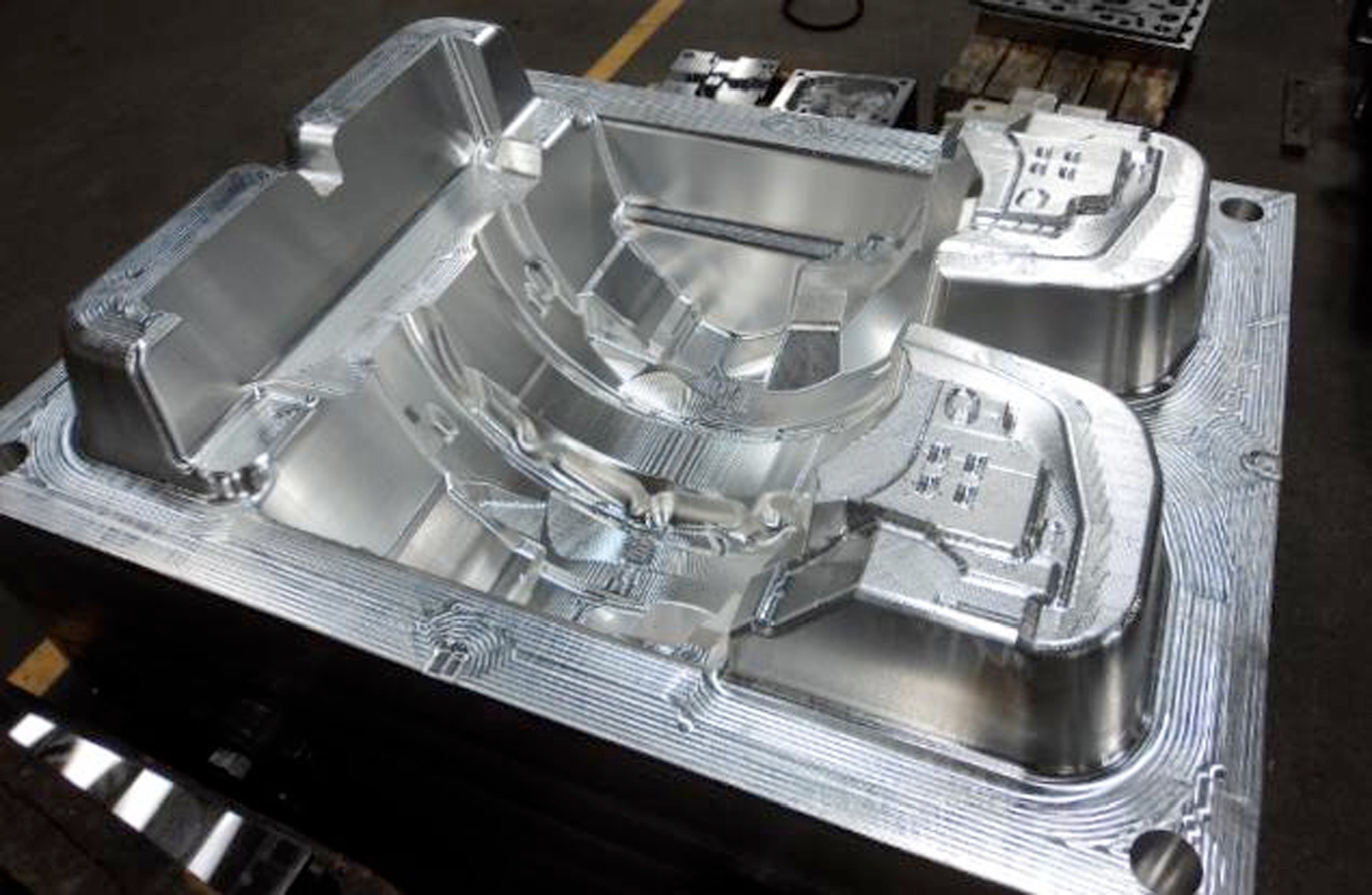
4.1 Poor Mold Venting
- Problem: Inadequate or blocked vents can trap air in the mold cavity, leading to bubble formation during the injection process.
- Solutions:
- Add or enlarge venting slots (typically between 0.0005″ and 0.002″) around the cavity edges to allow trapped air to escape.
- Vent runner channels to prevent air from entering the part and accumulating inside the mold.
4.2 Improper Gate and Runner Design
- Problem: Narrow or poorly positioned gates restrict air escape, causing air pockets to form in the molded part.
- Solutions:
- Increase gate size to at least 50% of the wall thickness to promote better material flow and reduce air entrapment.
- Position gates at thicker sections of the part to ensure proper filling and air venting.
- Enlarge runner diameter to avoid pressure drops and ensure uniform flow of material, preventing the formation of bubbles.
4.3 Low Mold Temperature
- Problem: Insufficient mold heating can cause uneven cooling, which leads to shrinkage and the formation of voids or bubbles in the molded part.
- Solutions:
- Increase mold temperature in 10°F increments to ensure uniform cooling and reduce the likelihood of voids.
- Allow 10 cycles for the mold temperature to stabilize, ensuring consistent molding conditions and reducing the risk of air bubbles.
5. Material-Related Causes and Solutions
The material used in injection molding significantly affects the occurrence of air bubbles. Proper handling, drying, and temperature control are essential to prevent material-related defects.
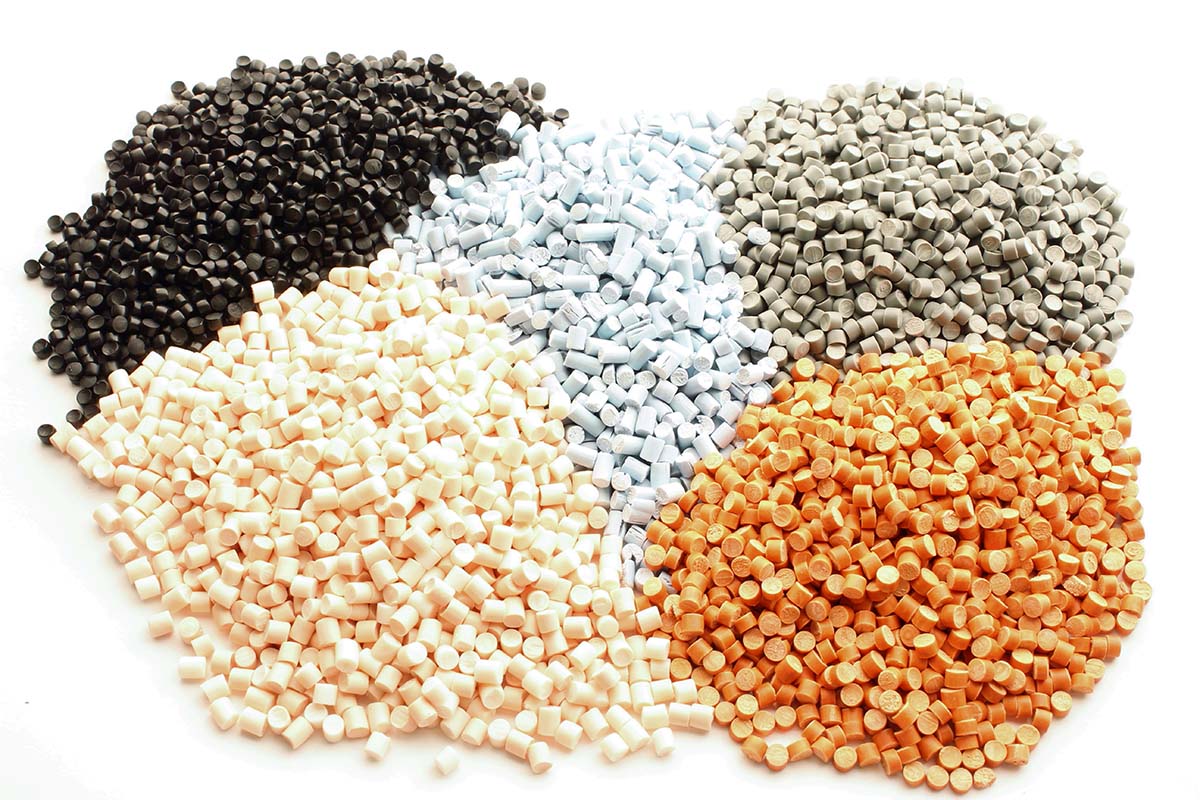
5.1 Excessive Moisture Content
- Problem: Improperly dried or hygroscopic resins can trap moisture during the molding process, leading to bubbles.
- Solutions:
- Thoroughly dry raw materials according to the supplier specifications to reduce moisture content.
- Target moisture content between 0.1% and 0.2% by weight to minimize air bubble formation.
- Use dehumidifying dryers with a dew point of -20°F to -40°F to effectively remove moisture from hygroscopic materials.
5.2 Thermal Degradation of Resin
- Problem: Overheating the resin during the molding process can cause thermal degradation, releasing gases that lead to bubbles in the molded part.
- Solutions:
- Reduce barrel and nozzle temperature to prevent excessive heating and material breakdown.
- Minimize residence time in the barrel to avoid prolonged exposure to high temperatures, which could result in gas generation.
5.3 Use of Recycled or Contaminated Materials
- Problem: Recycled materials with loose structures tend to trap air during molding, while contamination from foreign materials can also cause bubbles.
- Solutions:
- Limit recycled material ratio to no more than 20% to maintain material integrity and minimize bubble formation.
- Ensure recycled resin is properly dried to eliminate trapped moisture and air pockets before use.
6. Process-Related Causes and Solutions
Process conditions play a crucial role in determining the occurrence of air bubbles in injection molded parts. Proper control over cooling time, cycle consistency, and processing parameters can prevent bubble-related defects.
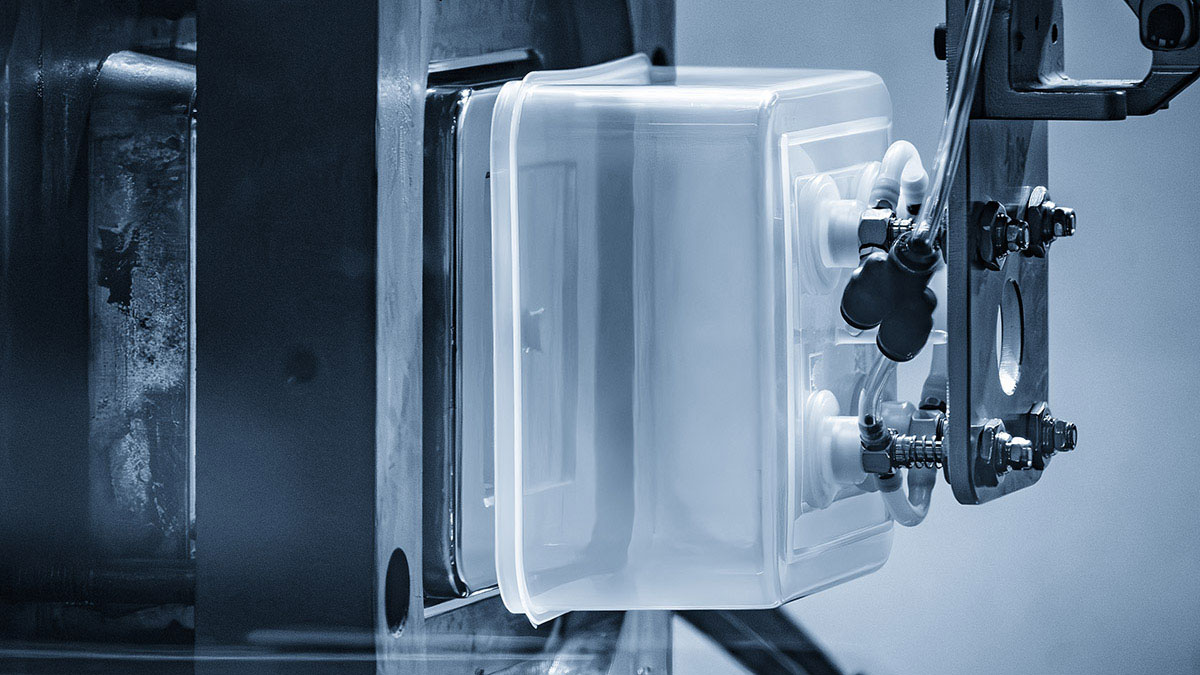
6.1 Uneven Cooling or Short Cooling Time
- Problem: Rapid cooling causes internal shrinkage, leading to the formation of vacuum voids and bubbles, especially in thick-walled parts.
- Solutions:
- Increase cooling time to ensure uniform cooling throughout the molded part, especially for thick-walled sections.
- Use external cold water or cooling molds to assist in more controlled and even cooling, reducing the risk of shrinkage and voids.
6.2 Inconsistent Cycle Times
- Problem: Fluctuations in cycle time can result in inconsistent mold filling, leading to variable bubble formation and part quality.
- Solutions:
- Standardize the process cycle to ensure uniform filling, cooling, and ejection times, which reduces the likelihood of defects.
- Automate the cycle or utilize robots to maintain consistent timing, especially in high-volume production, to eliminate variations that may contribute to air bubble formation.
7. Preventive Measures for Bubble-Free Molding
Proactive measures can significantly reduce the occurrence of bubbles during the injection molding process. By optimizing venting, controlling processing parameters, refining mold design, and ensuring proper material management, manufacturers can achieve consistent, high-quality parts with minimal defects.
7.1 Optimize Venting
- Clean and Maintain Venting Channels: Regular maintenance of venting channels ensures that air can escape during molding, preventing bubbles from being trapped inside the part.
- Add Extra Vents for Large or Complex Parts: For parts with intricate geometries or larger volumes, adding additional vents helps facilitate the escape of air, especially in hard-to-reach areas.
7.2 Control Processing Parameters
- Follow Precise Temperature, Pressure, and Backpressure Standards: Maintaining the correct processing parameters as per material specifications ensures that the resin flows smoothly and evenly, preventing trapped air from forming bubbles.
- Gradually Adjust Injection Speed During Troubleshooting: When troubleshooting bubble formation, adjusting injection speed gradually can help identify the optimal speed for minimizing trapped air and ensuring a consistent fill.
7.3 Use Proper Mold Design
- Ensure Balanced Gate and Runner Systems: A well-designed gating system with properly sized runners and gates allows for uniform material flow, reducing the chances of air pockets being trapped during injection.
- Incorporate Overflow Wells to Relocate Bubbles: Designing overflow wells or vents at strategic points in the mold allows any trapped air to be directed away from the molded part, reducing bubble formation in the final product.
7.4 Material Management
- Use High-Quality, Properly Dried Resins: Ensuring that resins are free of moisture and contaminants prevents the generation of gas that could lead to bubbles during molding.
- Store Raw Materials in Dry, Temperature-Controlled Environments: Proper storage of raw materials is essential to maintaining resin quality, especially for hygroscopic materials that absorb moisture from the air, increasing the risk of bubbles.
8. KingStar Mold’s Expertise in Defect Prevention
At KingStar Mold, we prioritize the quality and precision of every molded part. With our advanced techniques and expertise, we ensure that air bubbles and other defects are minimized, providing our clients with consistently reliable and high-quality products.
8.1 Advanced Mold Design
Precise Venting and Gating Systems: KingStar Mold’s experienced team designs molds with optimal venting and gating systems to ensure efficient air escape. This reduces the likelihood of air entrapment, helping to maintain the integrity and appearance of molded parts.
8.2 Optimized Processing Parameters
Fine-Tuned Temperature, Speed, and Pressure Settings: Our experts meticulously adjust processing parameters—such as temperature, injection speed, and pressure—to create the ideal conditions for bubble-free molding. By continually monitoring and refining these settings, we maximize the consistency and quality of every part produced.
8.3 Comprehensive Quality Control
Thorough Inspection Processes: KingStar Mold implements a multi-step inspection process to identify and eliminate potential bubbles before the parts are shipped to clients. This commitment to rigorous quality control ensures that only defect-free parts reach the customer, preserving both functionality and aesthetic appeal.
Conclusion
Air bubbles are a common defect in injection molding, often caused by issues such as trapped air, moisture, improper mold design, and inconsistent processing parameters. Addressing these causes with targeted solutions—such as optimizing venting, adjusting processing settings, and improving material handling—can significantly reduce the occurrence of bubbles and improve part quality.
By emphasizing the importance of proper venting, maintaining consistent temperature control, and ensuring stable processing conditions, manufacturers can achieve bubble-free molding and enhance the overall performance of their parts. At KingStar Mold, we integrate these practices into every project, ensuring high-quality, defect-free parts for our clients.
Are you experiencing air bubble issues? Don’t worry! Please fill out the online form or send an email to sales@kingstarmold.com and our engineering team will give you professional suggestions.