Our Satisfied Clients
Featured Cases Display
Using our top-level tool shop, we offer custom services including injection molding and insert molding with many types of plastic materials .
Other Cases
Our other cases display a wide range of successful projects, showcasing our expertise in delivering tailored solutions across various industries.
Case Display
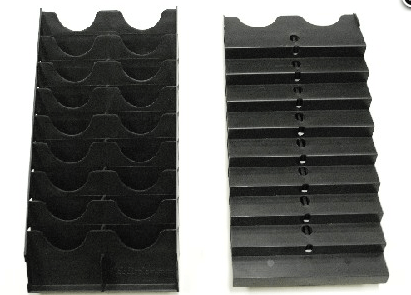
Collectible Display
Custom Coin Holder/Display for Certified Collectible Coins
Our Process
Steps | Description |
---|---|
1. Concept to Prototype | Collaborate with customers to transform their concepts into a tangible design. |
Develop and supply a rapid prototype for evaluation and feedback. | |
2. Production and Tooling | Create new tooling using CNC and EDM machining for accuracy and efficiency. |
Perform mold repairs, maintenance, and run production cycles using advanced injection molding machines. | |
3. Fabrication | Utilize 100% recycled high-impact polystyrene for sustainable and durable displays. |
Coin display dimensions: 10.5 X 5.25 X 1.5 inches, weight: 4.5 ounces, tolerance: +/- 0.0005 inches. | |
Materials: 420 stainless steel for tooling and high-impact polystyrene for the holder. | |
4. Customer-Centric Services | Offer drop shipping directly to customers or their distributors. |
Provide customer inventory maintenance. | |
Ensure quality with visual and functional testing. |
Our Process
Steps | Description |
---|---|
1. Flaw Identification and Analysis | Identified excessive heat buildup at the center of the original component reel. |
2. Redesign with CAD | Developed a new CAD design to optimize gate location and cooling requirements. |
3. Tooling and Fabrication | Manufactured new tooling using CNC and EDM machining. |
Utilized P20 steel and 420 stainless steel for durable and precise mold fabrication. | |
4. Injection Molding | Created reels with high-impact polystyrene (in multiple colors) and black polycarbonate. |
Ensured reduced production cycle times and improved quality. | |
Achieved versatility in manufacturing with interchangeable cavities for multiple part designs. | |
5. Quality Assurance and Maintenance | Conducted rigorous testing to ensure the quality of new tooling and products. |
Provided mold repairs and maintenance services. | |
6. Inventory Support | Maintained customer inventory for seamless production and delivery. |
Case Display
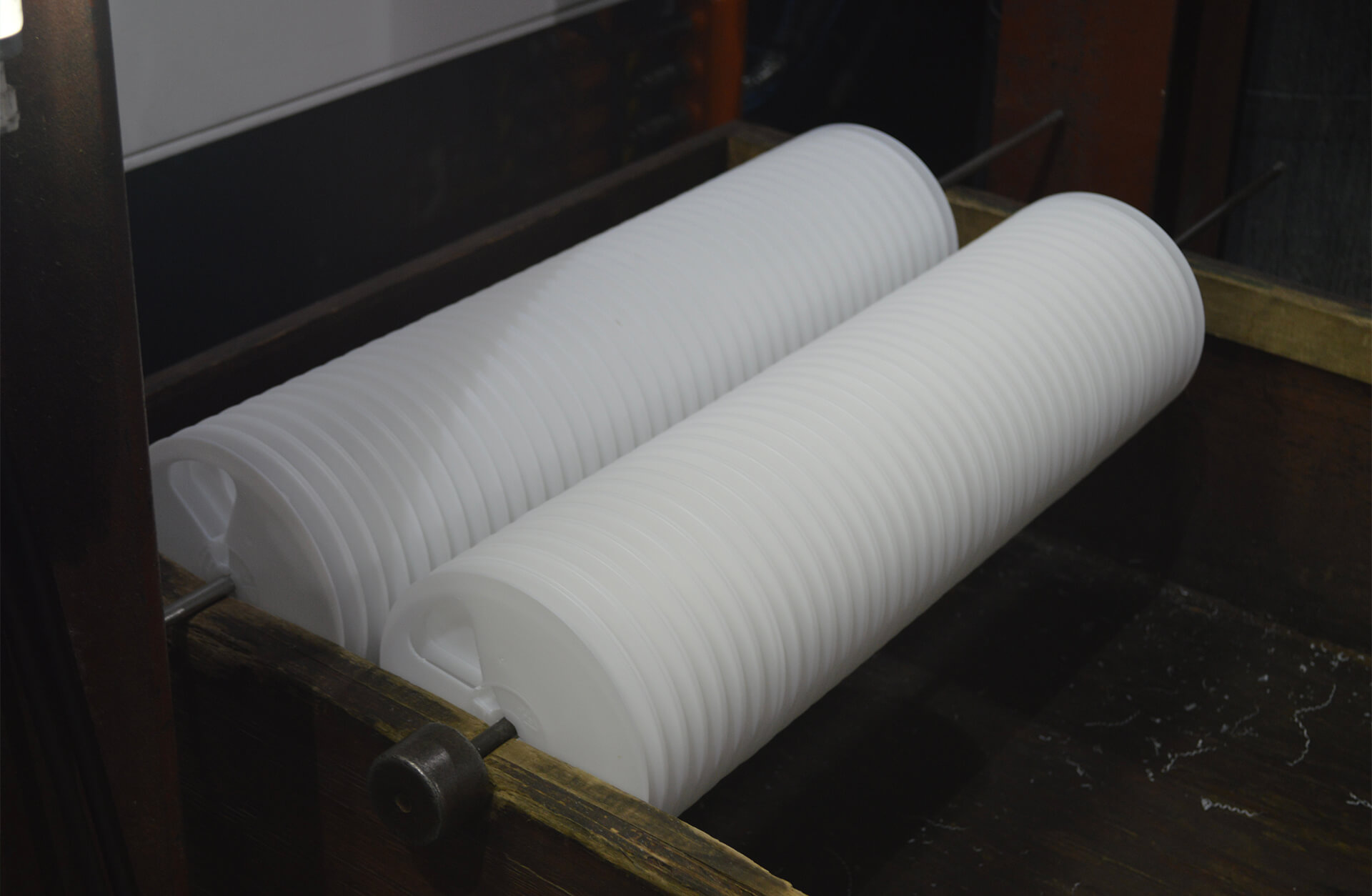
Polystyrene Components Reel
Redesign and Manufacturing of Surface Mount Component Reels
Case Display
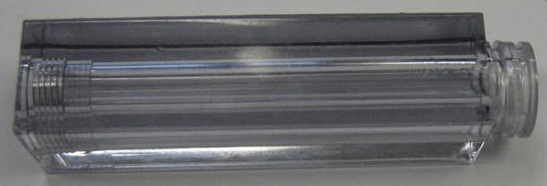
Flow Meter Tool
Custom Flow Meter Tube for Liquid Measurement Applications
Our Process
Steps | Description |
---|---|
1. Injection Molding with Core Pull | The mold features a core pull mechanism and a threaded insert that is manually unscrewed between cycles. |
2. Precision Manufacturing | Tubes are precisely molded to dimensions of 1″ x 1″ x 5 inches, weighing 3.2 ounces, with a tight tolerance of +/- .0005 inches. |
3. Material and Quality | Made from clear polycarbonate, ensuring durability and clarity. |
Reduced production cycle times while maintaining exceptional quality. | |
4. Inspection and Testing | Comprehensive testing, including gauge measurements, thread tests, and clarity inspections, ensures flawless performance. |
5. Customer-Centric Approach | Stocking components for timely shipment based on customer requests. |
Drilling to the specified depth and providing the correct mating surface for seamless assembly. |
Our Process
Steps | Description |
---|---|
1. Injection Molding | Yellow ABS material is used to create durable and precise gauge covers based on customer-supplied molds and specifications. |
2. Secondary Operations | Holes are drilled post-molding to accommodate screws and bolts for hardware insertion. |
3. Specifications | Dimensions: 7″ x 7″ x 3 inches |
Weight: 3.7 ounces | |
Tolerance: +/- .0005 inches | |
4. Quality and Efficiency | Optimized production cycles ensure shorter lead times and consistent high-quality outputs. |
5. Inventory Management | Components are planned, stocked, and shipped based on customer requests, ensuring timely delivery. |
Case Display
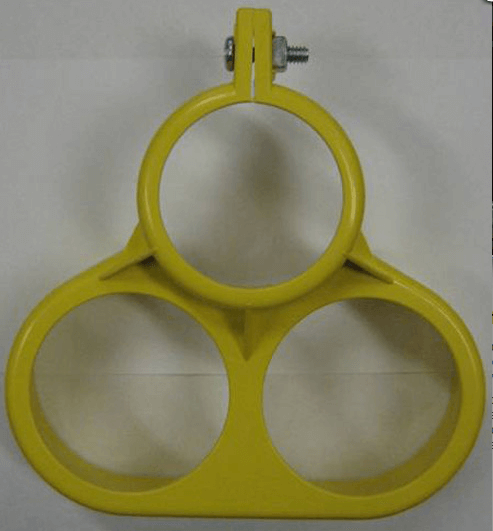
ABS Gauge Cover
Custom Molded Gauge Cover for Protective Applications
Case Display
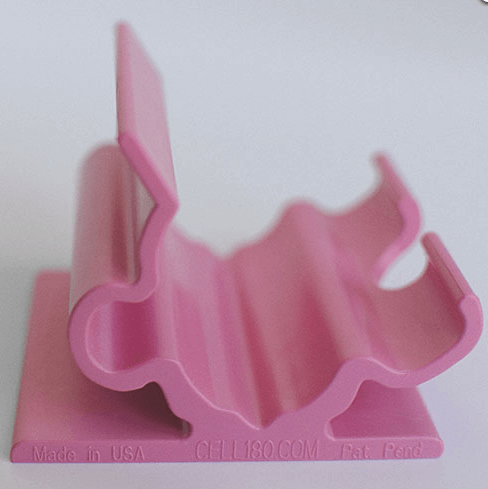
Mobile Device
Custom-Designed Phone Stands for Cell180.com
Our Process
Steps | Description |
---|---|
1. Design & Prototyping | Conceptualizing the design based on client specifications and preferences. |
Creating a prototype using CAD software or 3D printing to visualize the final product. | |
2. Inventory Management | Choosing the appropriate material (plastic, metal, etc.) based on durability, aesthetics, and cost. |
Ensuring material compatibility with the intended manufacturing process (injection molding, CNC machining, etc.). | |
3. Manufacturing | Producing the phone stands using the selected material through methods like injection molding or CNC machining. |
4. Quality Control | Inspecting the finished phone stands for defects such as cracks, inconsistencies, or dimensional inaccuracies. |
Our Process
Steps | Description |
---|---|
1. Design and Tooling | Developed initial CAD drawings based on customer specifications. |
Fabricated new tooling using CNC and EDM machining techniques. | |
2. Injection Molding and Production | Manufactured the switches with copolymer polypropylene using P20 steel molds. |
Produced high-precision parts with dimensions of 2″ x 2″, weight 0.13 ounces, and a standard tolerance of +/- .0005″. | |
3. Quality Assurance | Conducted dimensional, visual, and functional inspections to ensure consistent quality. |
4. Customer-Centric Services | Maintained inventory for customers to enable timely production and delivery. |
Shipped finished products as required to meet client needs. |
Case Display
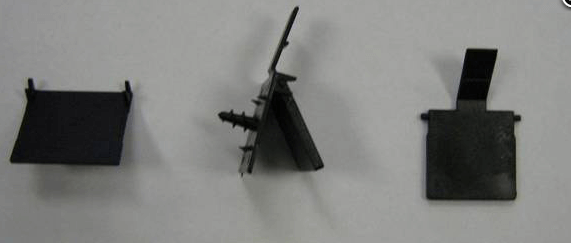
Molded Sensor Switch for Tool Vending
Custom Molded RFID Sensor Switch for Tool Vending Applications