Black Oxide Finish Service
Our black oxide finish services deliver durable rust protection and a sleek matte black look—perfect for metal parts needing both resilience and visual appeal. We apply precision black oxide treatments to boost longevity and elevate aesthetics, with results you can rely on.
3 Types of Black Oxide Finishing Process
MIL-C-13924 Black Oxide Coating Standards
As a manufacturer specializing in black oxide coating services, we adhere strictly to industry standards to ensure consistent quality. The MIL-C-13924 standard is a key reference for our processes, outlining specific requirements for different coating types and material compatibilities. Below is a clear breakdown of its core classifications—including versions, classes, and applicable materials—to help you understand the specifications we follow in our production.
Standard Version | Details |
---|---|
MIL-C-13924C | No dimensional changes occur during the coating process. |
Class 1 | Alkaline oxidizing treatment. Suitable for wrought iron, cast/malleable irons, plain carbon steels, and low-alloy steels. |
Class 3 | Fused salt oxidizing treatment. (Not offered at TPP.) |
Class 4 | Alkaline oxidizing treatment. Exclusively for 300-series corrosion-resistant steel alloys. |
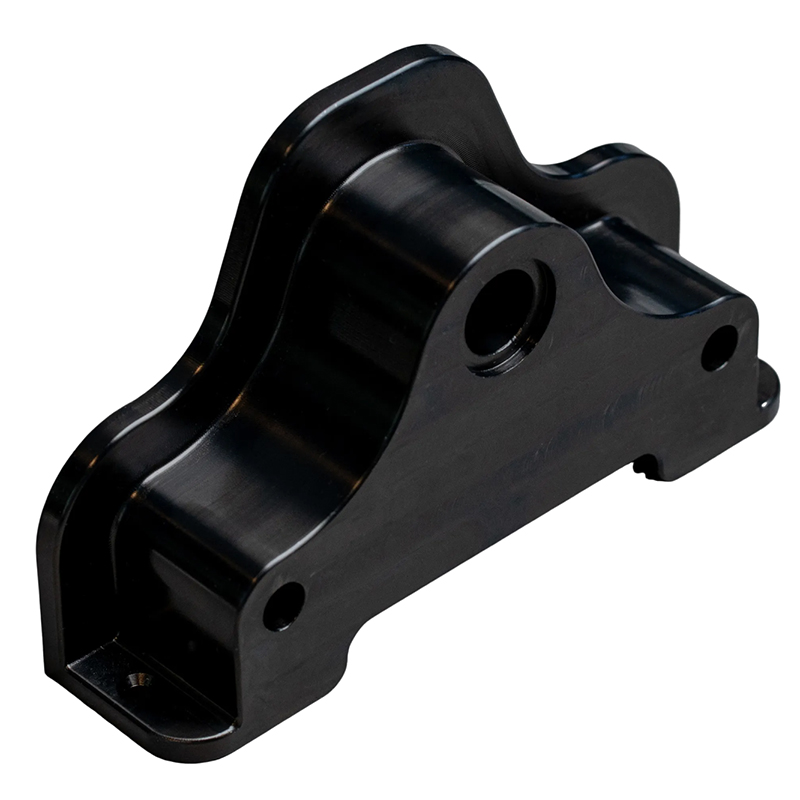
Applicable Materials
Material Category | Specific Types | Key Characteristics & Notes | Model Examples (Common Types) |
---|---|---|---|
Ferrous Metals | Carbon Steel | Core material; forms matte-black magnetite layer; requires oil/wax post-treatment | 1018, 1045, S235JR, Q235 |
Alloy Steel | Compatible; high-Mn alloys may show red/brown hues | 4140, 34CrMo4, 30CrMnSiA | |
Stainless Steel | Enhanced corrosion resistance; typically no post-treatment needed | 304, 316L, 0Cr18Ni9, X6CrNiMo17-12-2 | |
Cast Iron | Requires thorough cleaning of surface porosity | HT200, EN-GJL-250 | |
Powdered Metal | Resin impregnation mandatory to seal pores | FL-4605, FL304-260N, FX-08C20 | |
Non-Ferrous Metals | Copper & Alloys | Forms copper selenide layer; verify post-treatment needs | C11000, C26000, T2 |
Zinc & Alloys | Cold process only; high-temp causes deformation | ZnAl4, ZL043A | |
Brass | Compatible only with specific alloys (e.g., low-zinc types) | C36000, HPb63-3, CuZn39Pb3 | |
Aluminum & Alloys | Restricted: Cold process feasible; high-temp damages material | 6061-T6, 2A12, AW-6082 |
Applications of Black Oxide Coating
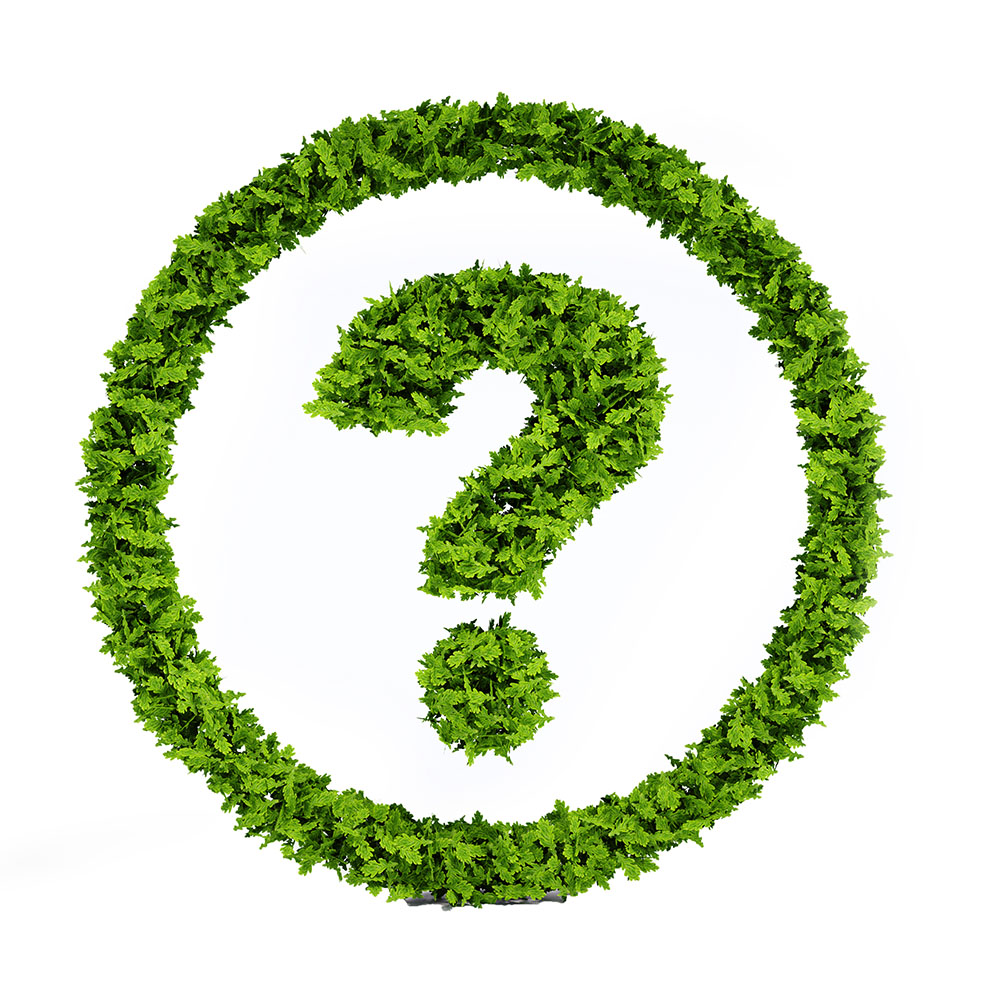
Frequently Asked Questions
Black oxide treatment, from cleaning to sealing, usually takes 1 to 3 hours. How long exactly depends on the process type—hot, mid-temperature, or cold—and the size of the parts. Plus, we can handle batches, so multiple components get processed efficiently at the same time.