Cooperative Partners
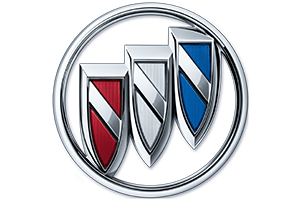
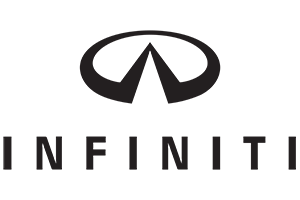
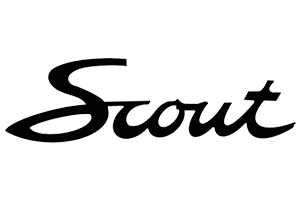
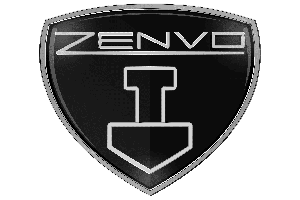
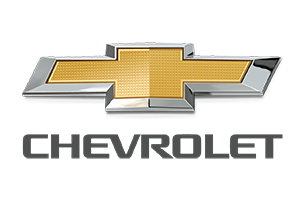
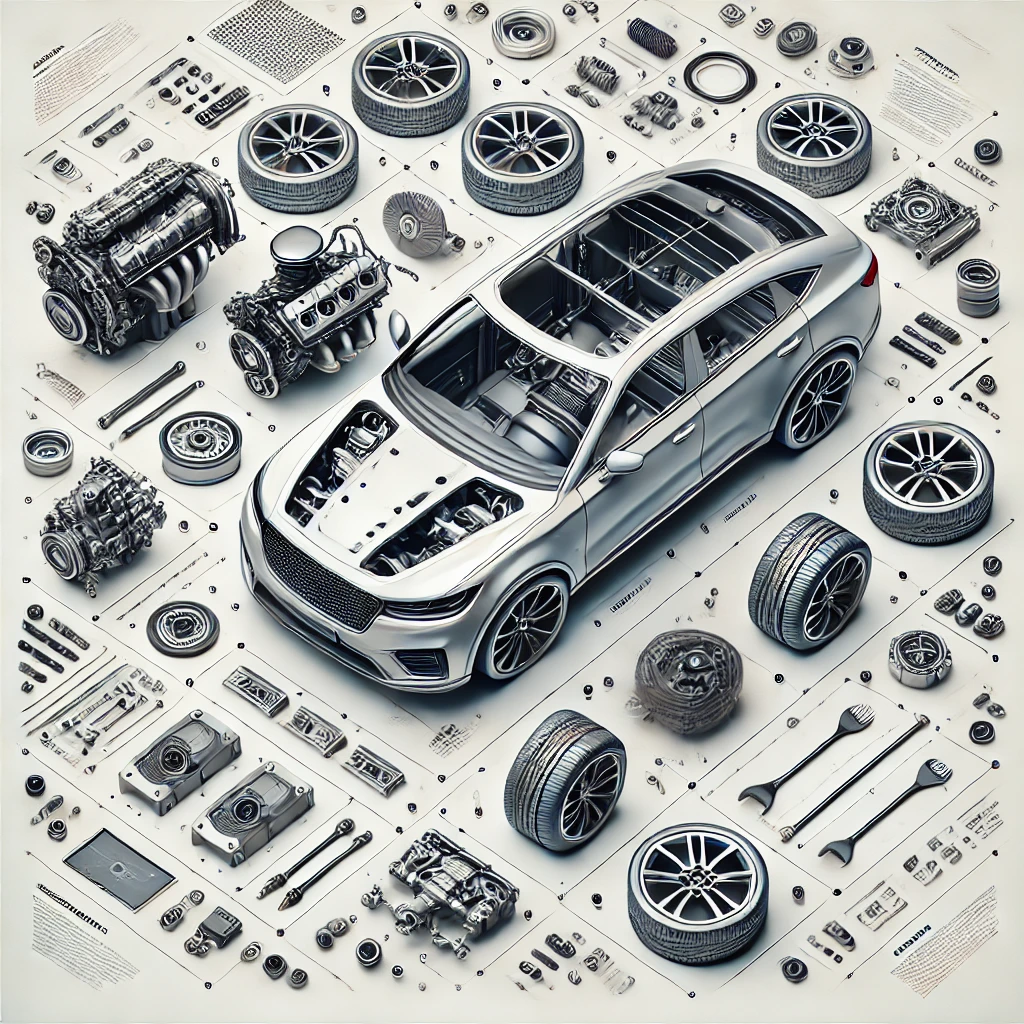
High-Precision Automotive Manufacturing Solutions for the Global Market
10+ Years of Automotive Manufacturing Experience
Certified Material Selection & Traceability
Fast Turnaround for Custom Orders
KingStar Mold delivers precision-engineered automotive components for a wide range of applications, from interior trims to under-the-hood parts. Our expertise in custom injection molding ensures that every component meets strict dimensional tolerances, durability requirements, and regulatory standards essential to the automotive industry.
Whether you’re developing a new vehicle model or improving an existing design, our team works closely with OEMs and tiered suppliers to provide high-performance plastic parts that integrate seamlessly into complex assemblies. With advanced tooling, quality control, and fast turnaround, we help accelerate your production timeline without compromising on quality.
What We Can Make for You
Automotive Parts Manufacturing Capabilities
KingStar Mold offers a comprehensive range of manufacturing services tailored to the automotive industry.
Our core processes include:
We’ve produced a diverse array of automotive components, including interior trims, exterior panels, and car lighting parts. Within the automotive sector, injection molding and mold-making contribute the largest portion of our annual revenue, while CNC machining and 3D printing also play an important role in supporting the industry’s specialized needs.
Please note: Due to confidentiality agreements with our clients, we are only permitted to showcase a limited selection of automotive product appearances. These examples are shared with full consent following direct communication with the respective clients.
Automotive Interior Parts
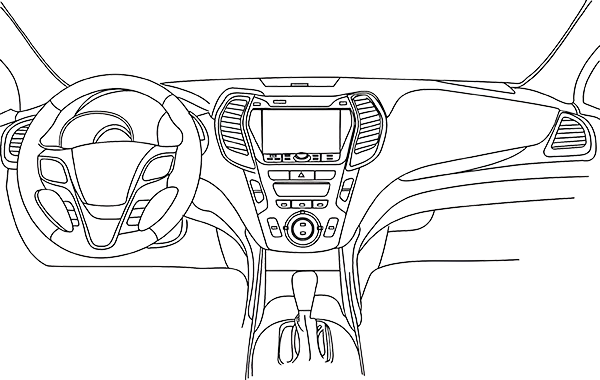
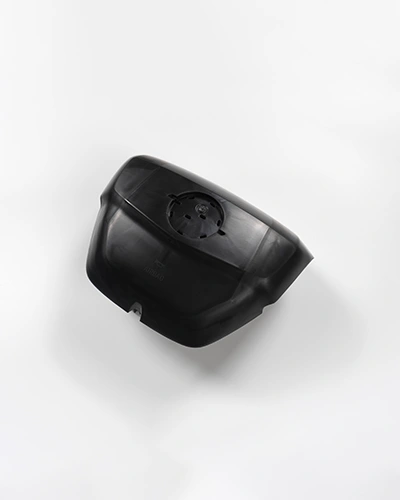
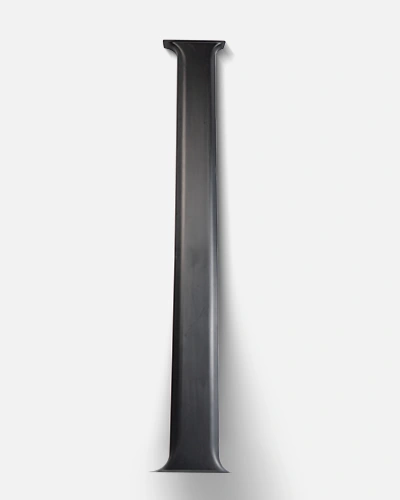
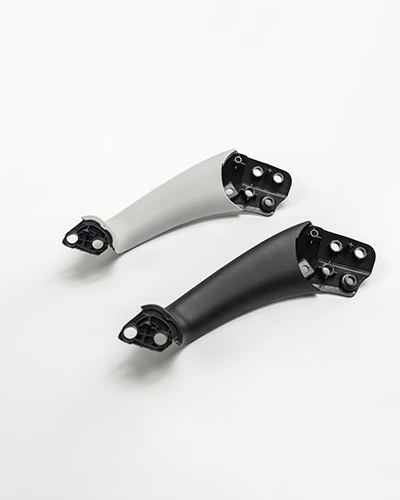
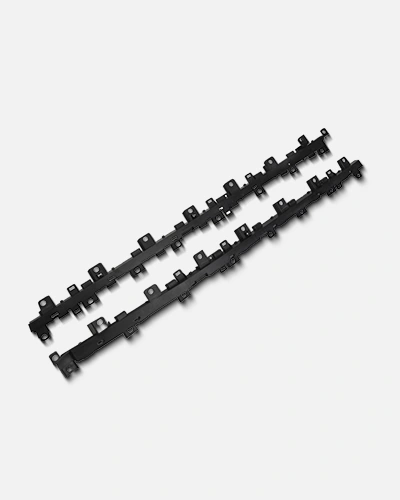
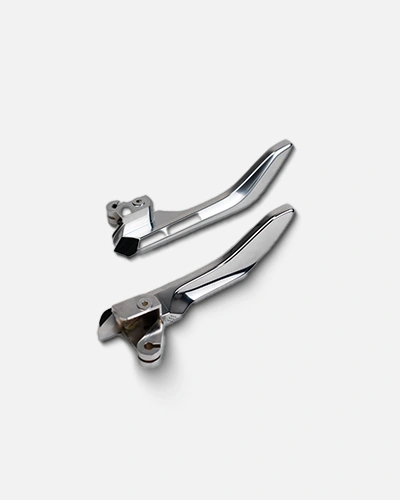
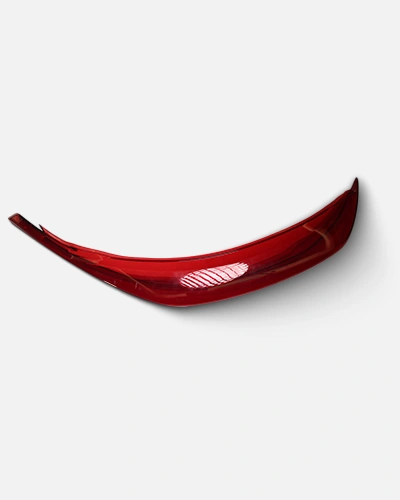
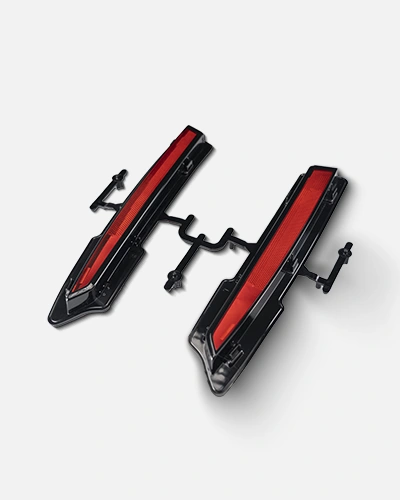
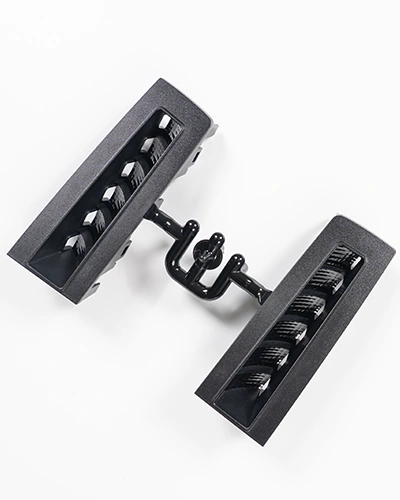
Automotive Exterior Parts
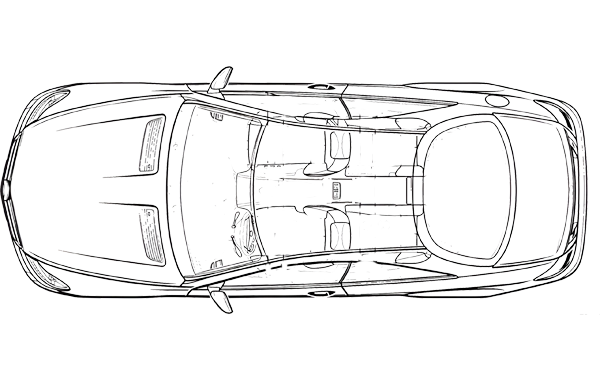
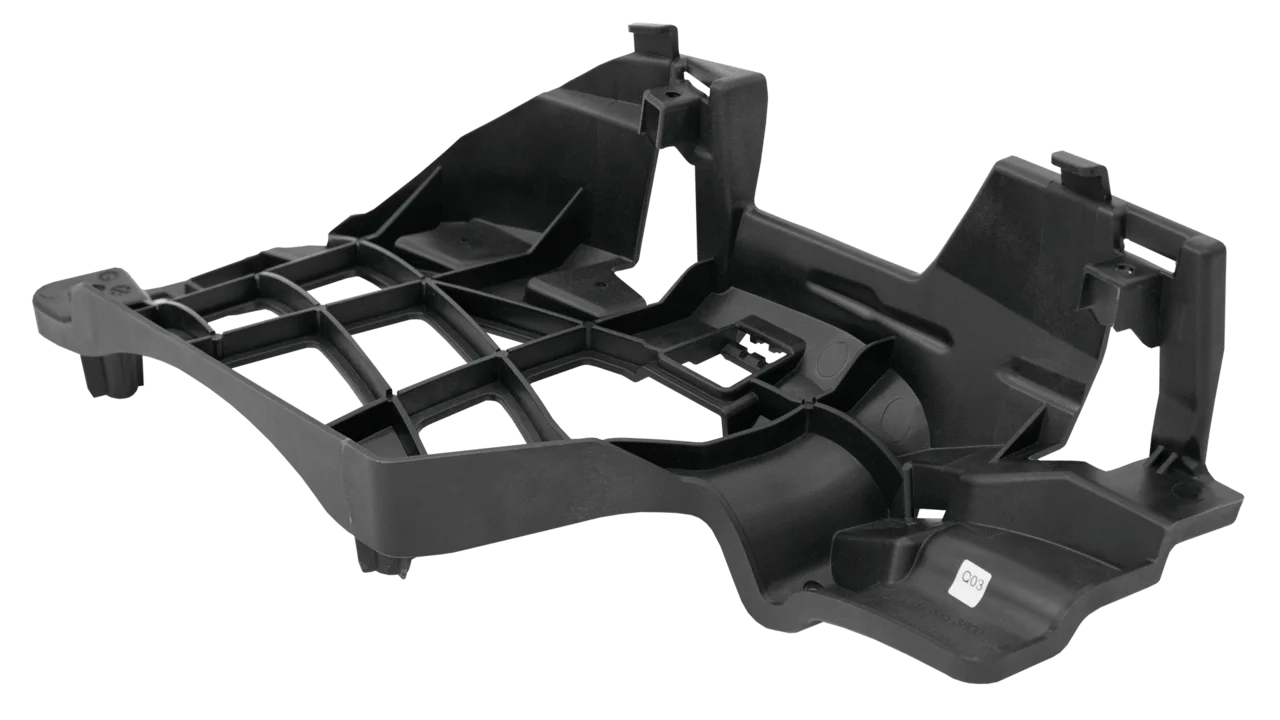
Recommended Automotive Manufacturing Solutions
After years of experience in automotive components manufacturing and successfully supporting hundreds of projects, we’ve developed a range of tailored solutions to meet diverse production needs. Each solution is built around a specific manufacturing process, offering distinct advantages depending on your part design, volume, and performance requirements. While some processes may seem similar at first glance, they differ significantly in workflow, purpose, and technical approach. Below are several recommended automotive manufacturing solutions we offer based on project goals and complexity:
Advantages of Partnering with Us
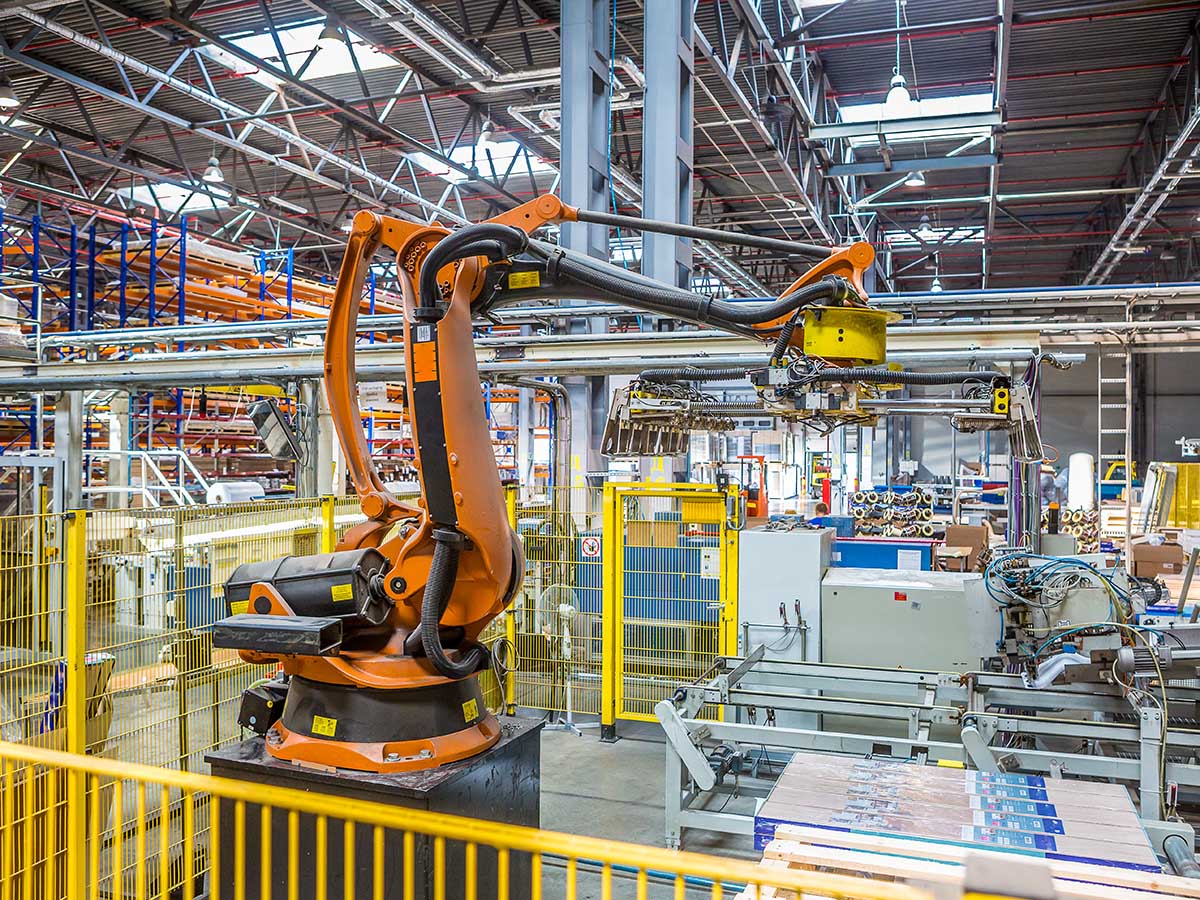
Shorter Leadtimes for a Competitive Edge
We help you cut production cycle times by up to 50% with in-house capabilities and expert planning—ideal for tight schedules and competitive markets.
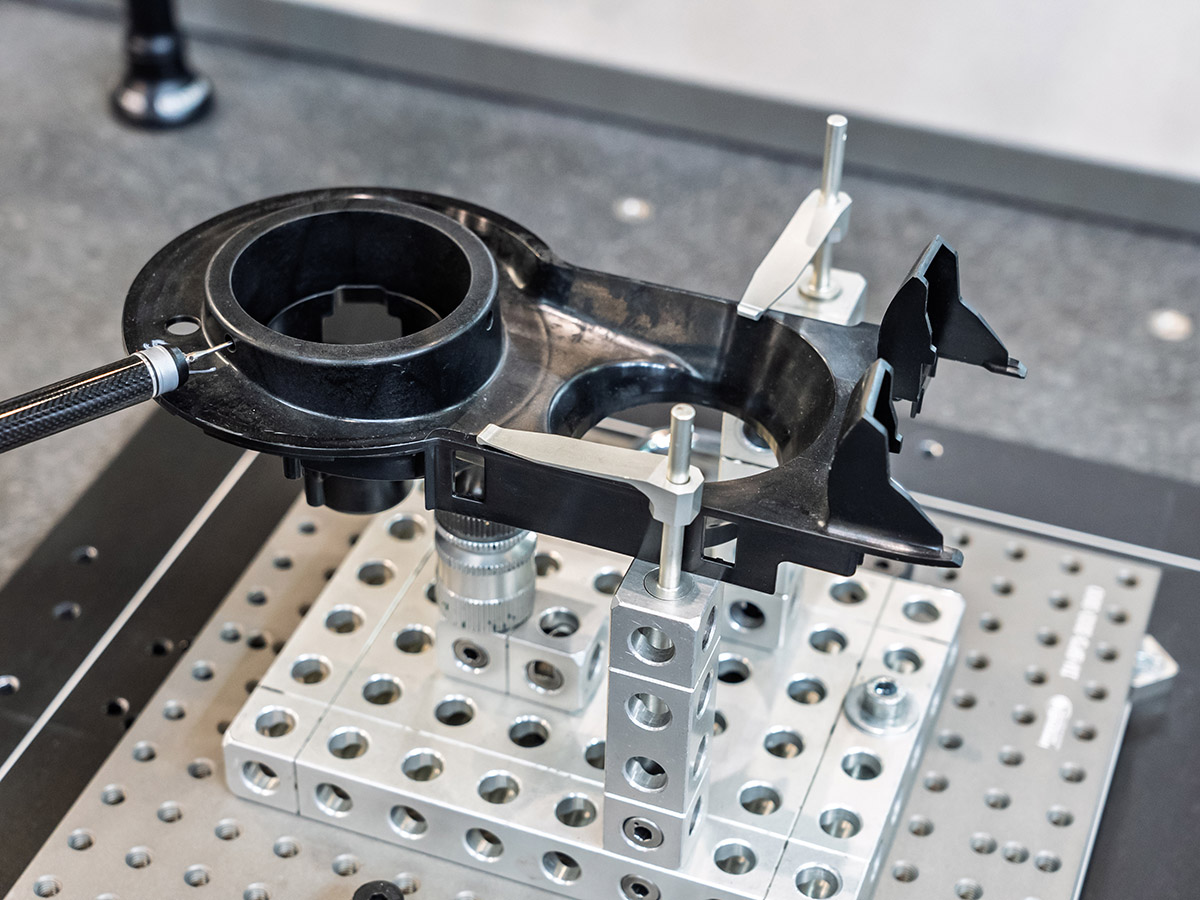
Reliable Quality Control
Certified to IATF 16949:2016 and ISO 9001:2015, we provide full documentation and rigorous inspections to ensure consistent, trusted quality.
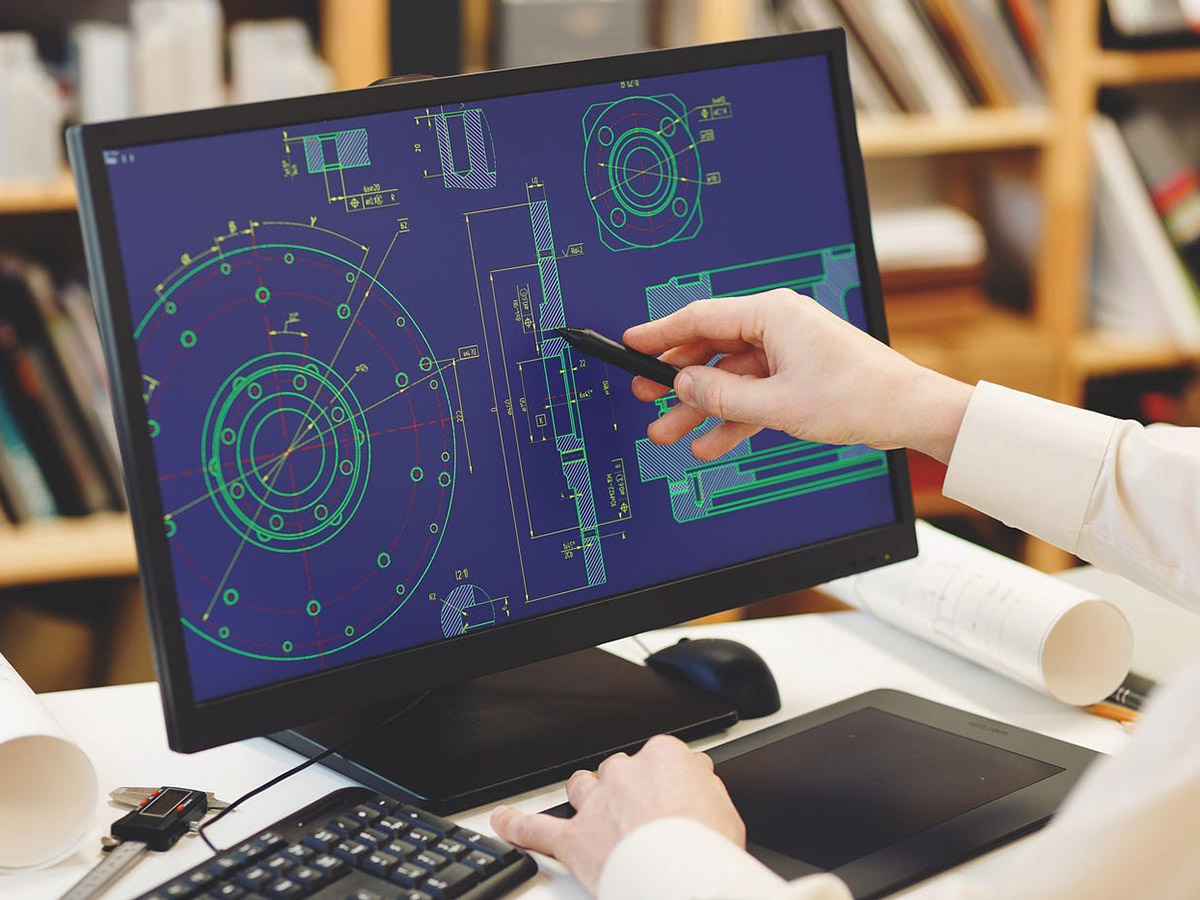
DFM Support
Our team provides hands-on DFM analysis to optimize designs for safety, performance, cost-efficiency, and manufacturability.
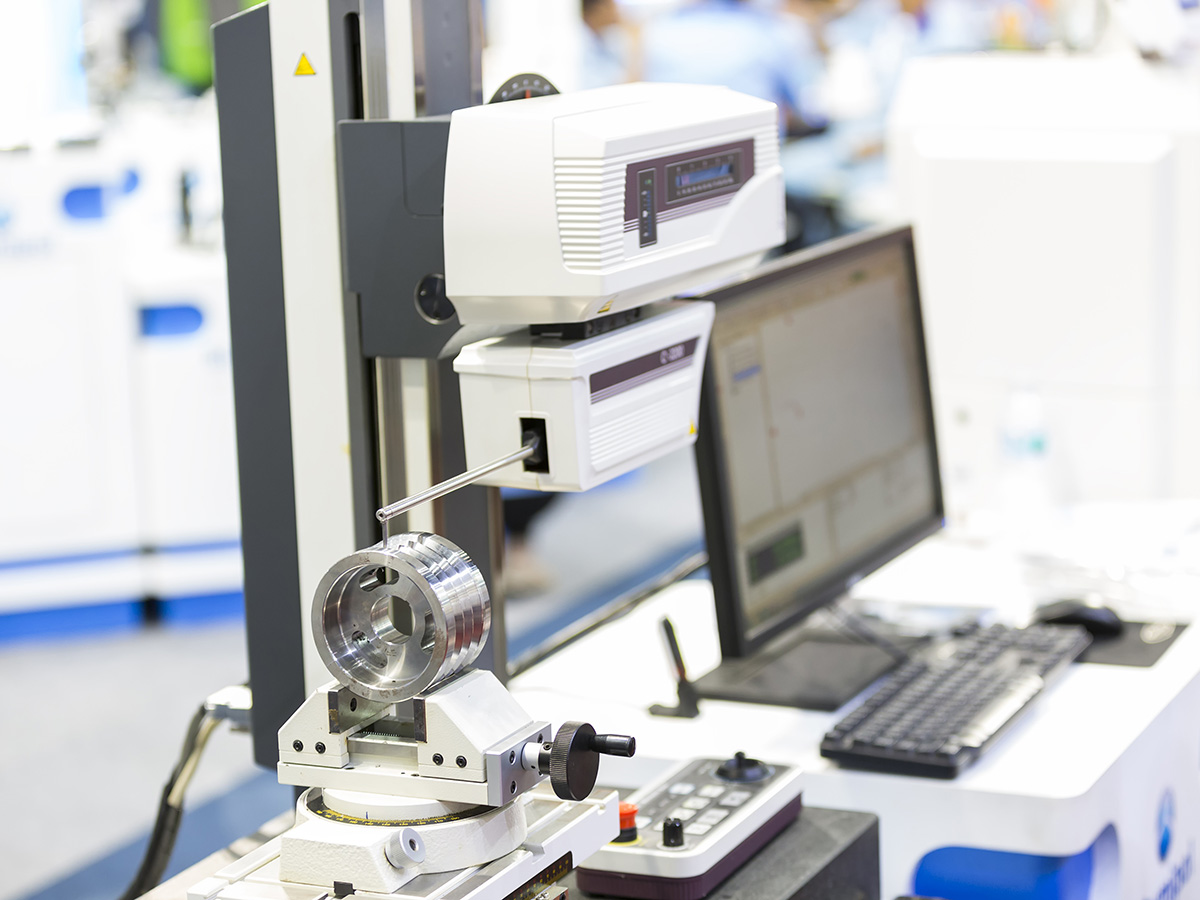
High Precision Tolerances
We deliver tolerances as tight as ±0.001″, ensuring exceptional accuracy and fit for high-performance automotive parts.
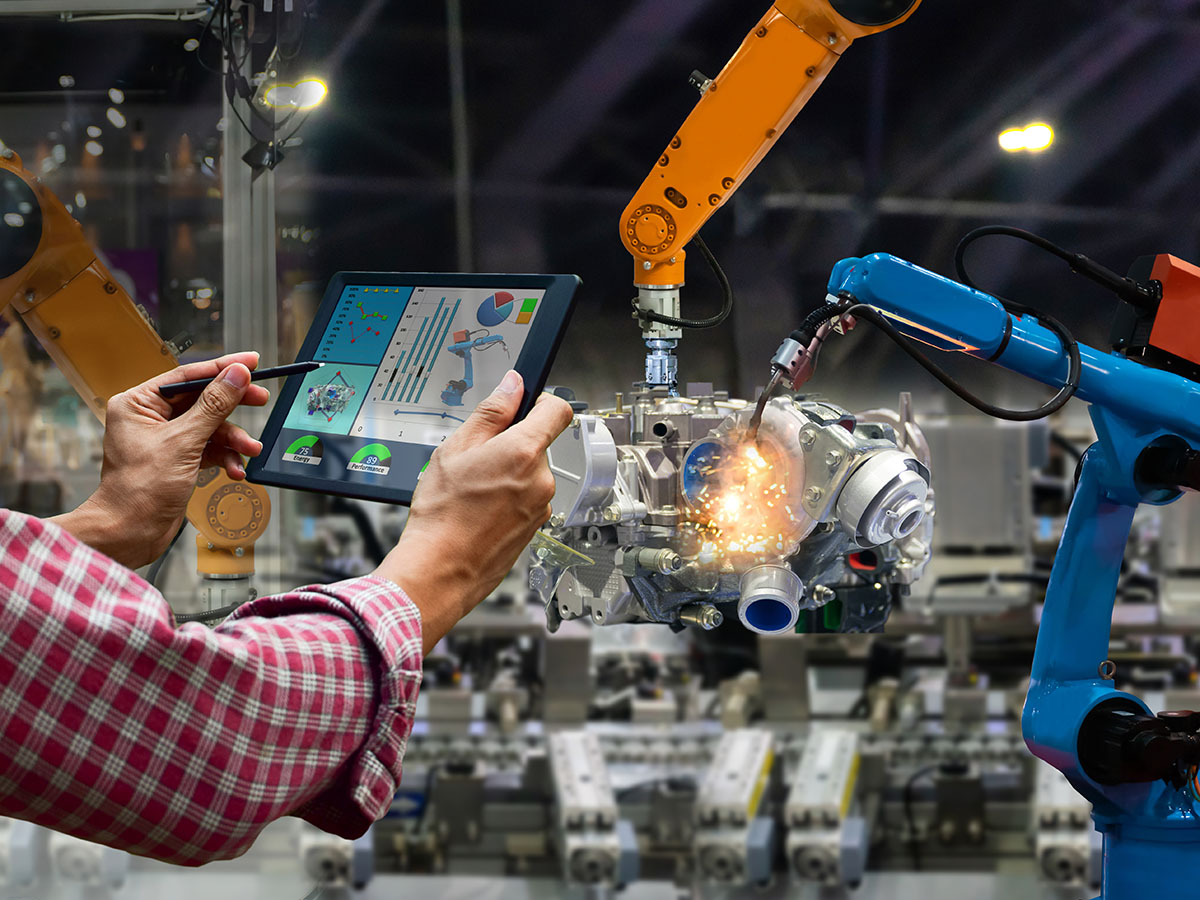
On-Demand Production Flexibility
Perfect for urgent needs, our agile low-volume services support part replacements, recalls, and just-in-time demands.
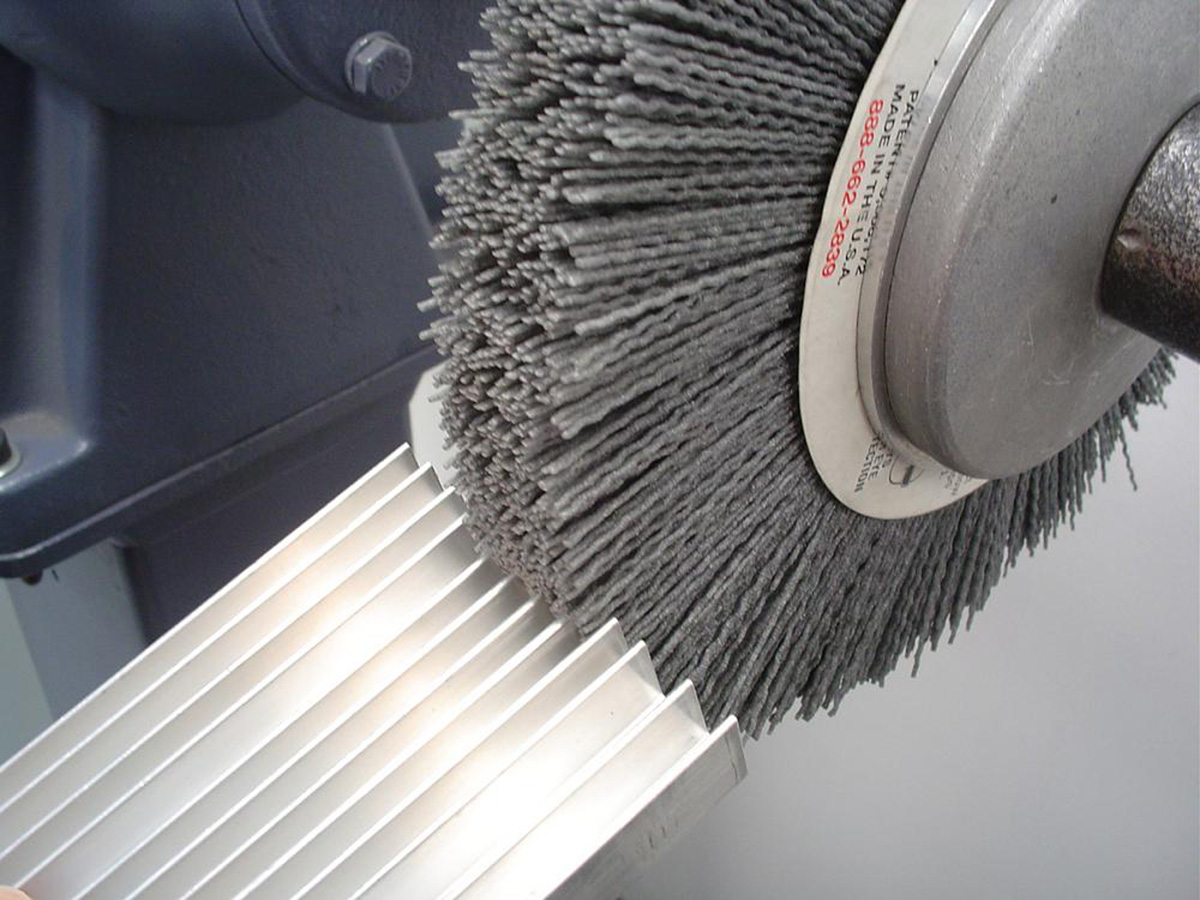
Custom Finishes & Variants
Choose from a wide range of finishes and custom options for enhanced part performance, appearance, or limited edition models.
Factory Gallery
Previous Auto Injection Molding Projects
We are injection molding designers and manufacturers for several leading automobile brands. Our factory facilities can produce 900-1000 automotive molds and thousands of plastic injection molding automotive parts in a year. Our services are also diversified to cater to manufacturers of baby products, buckets, home appliances, and furniture among many others.
KingStar Mold injection molding auto parts and production processes are certified by international regulatory bodies. Working with us would thus make your plastic auto parts industry-compliant by default.
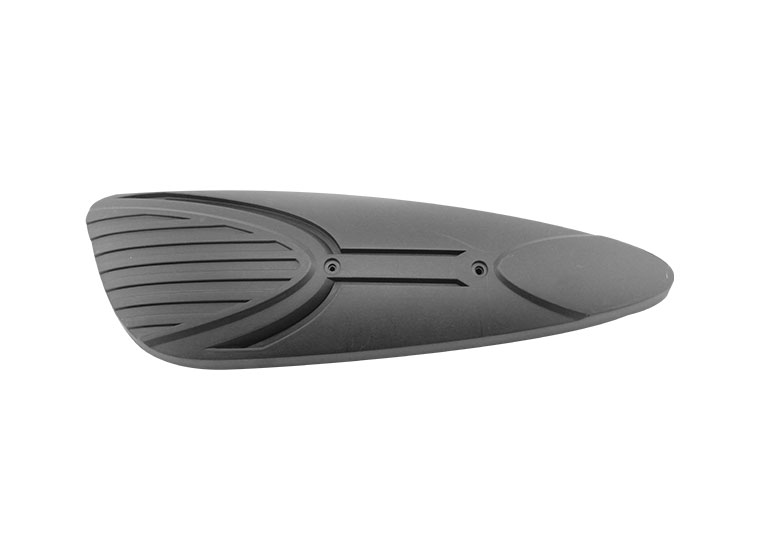
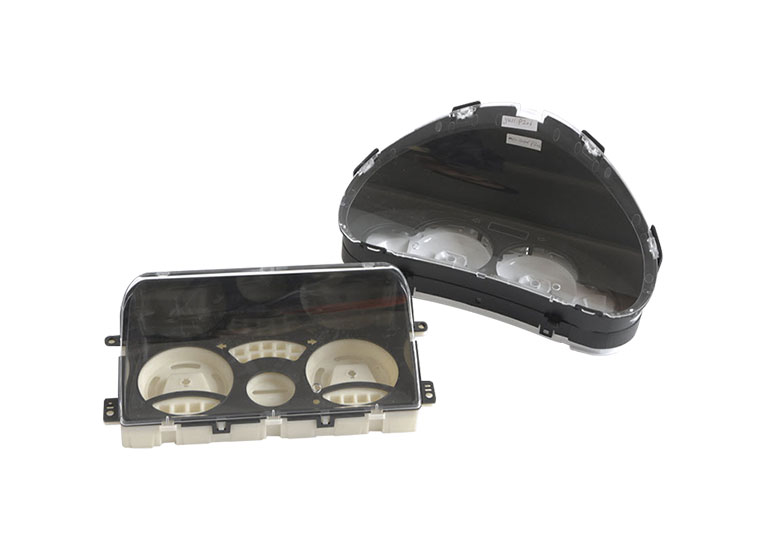
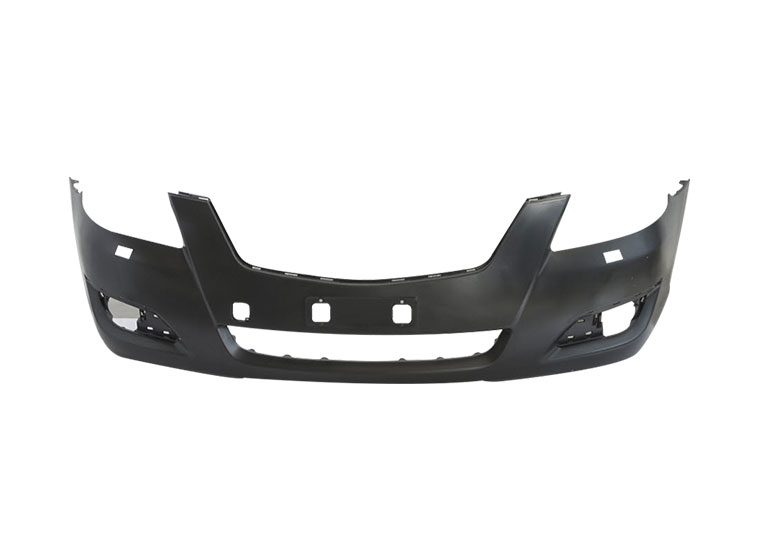
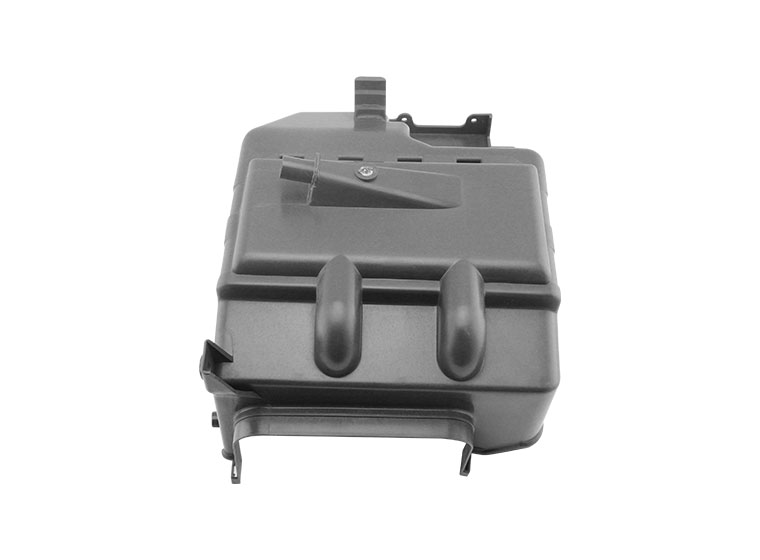
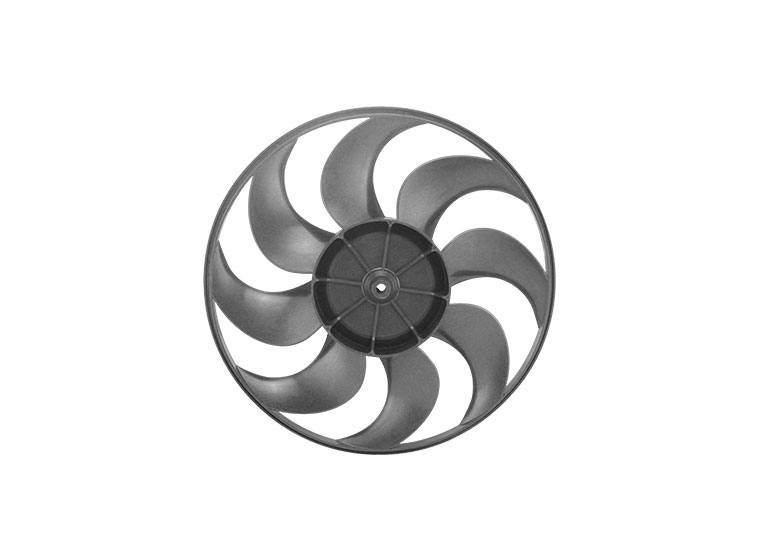
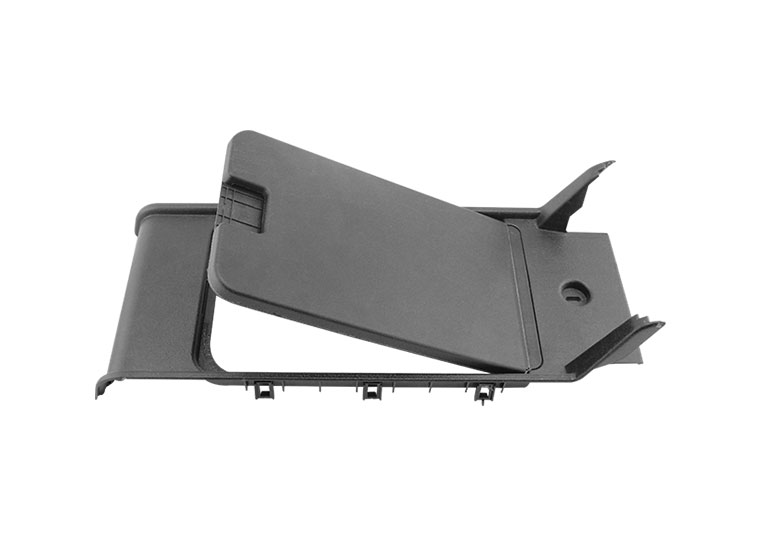
Material Options for Automotive Applications
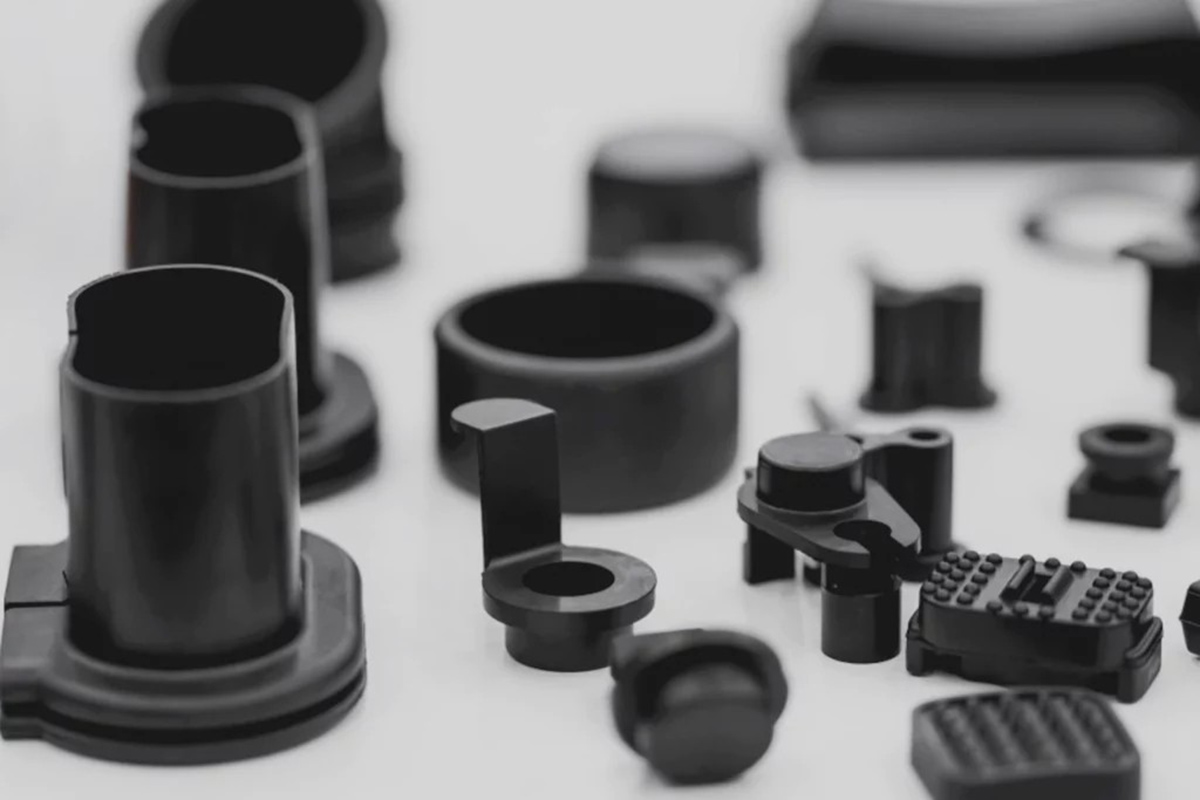
ABS
ABS is valued for its strength and surface quality, making it ideal for parts like interior trims, bumpers, dashboards, and light housings. It offers a great balance of durability and aesthetics.
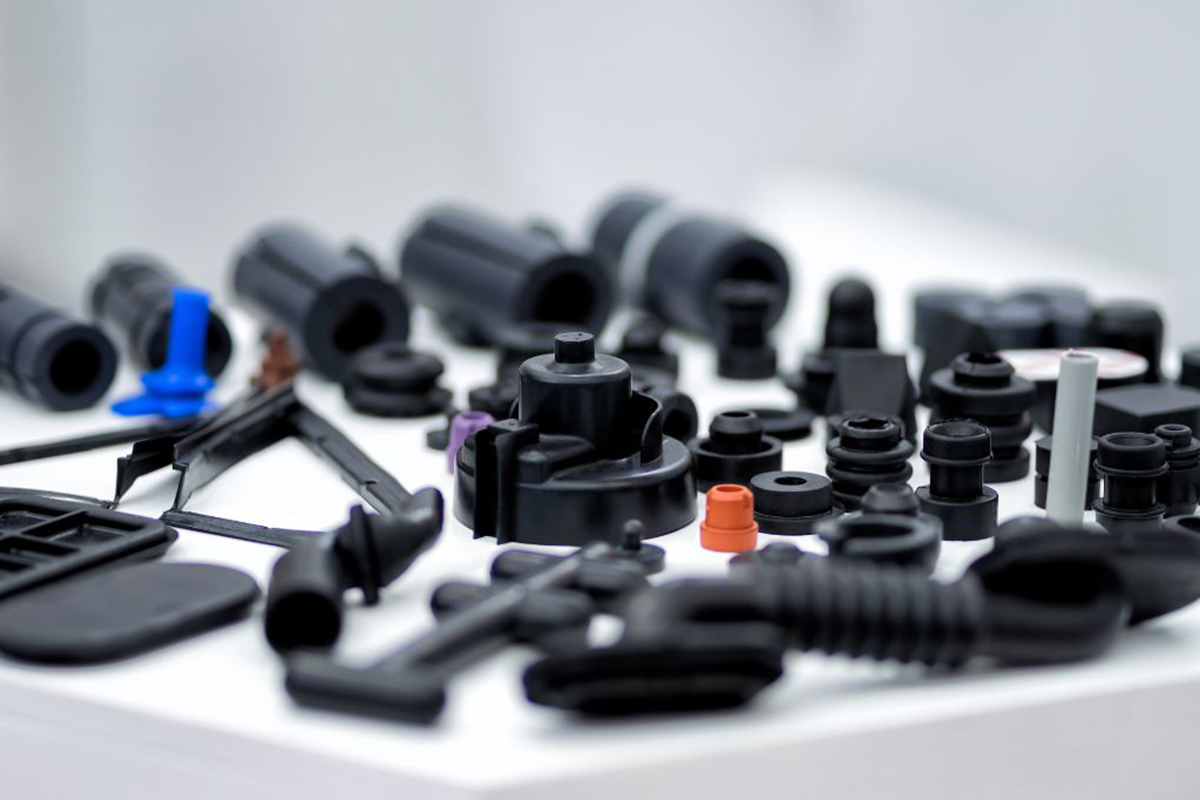
PA
PA (Nylon) is widely used for its strength, wear resistance, and heat tolerance. Common applications include mirror housings, gears, bushings, door handles, and intake manifolds.
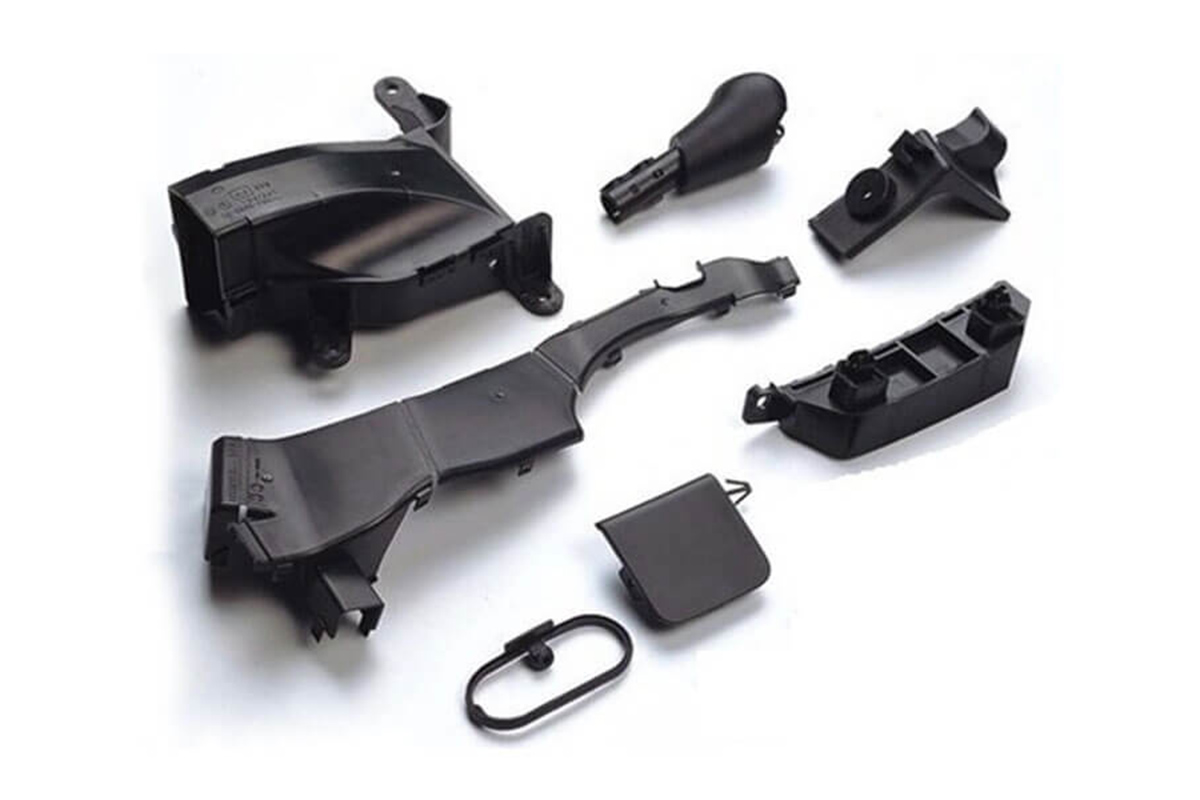
PBT
PBT is valued for its electrical insulation, durability, and resistance to heat and chemicals. It’s commonly used for producing connectors, housings, and sensor enclosures in automotive applications.
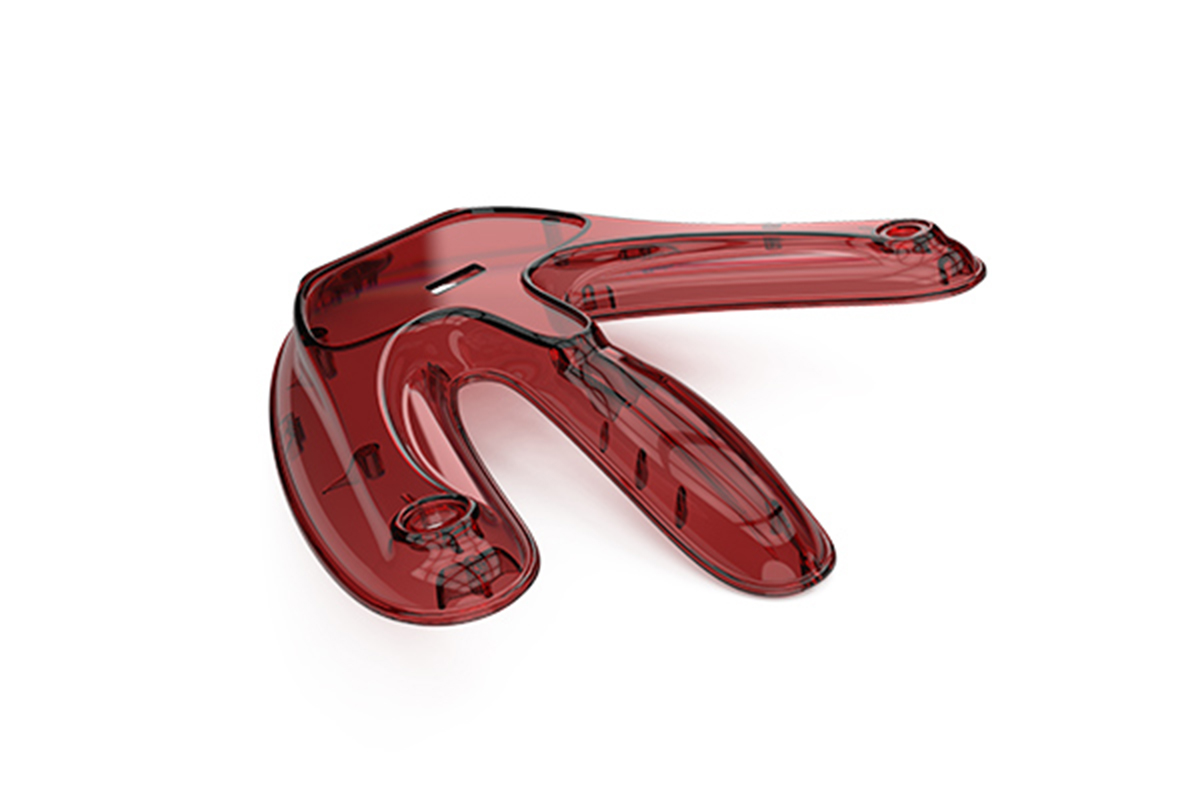
PC
PC is known for its impact resistance and optical clarity, making it ideal for automotive components like headlights, taillights, and instrument panels.
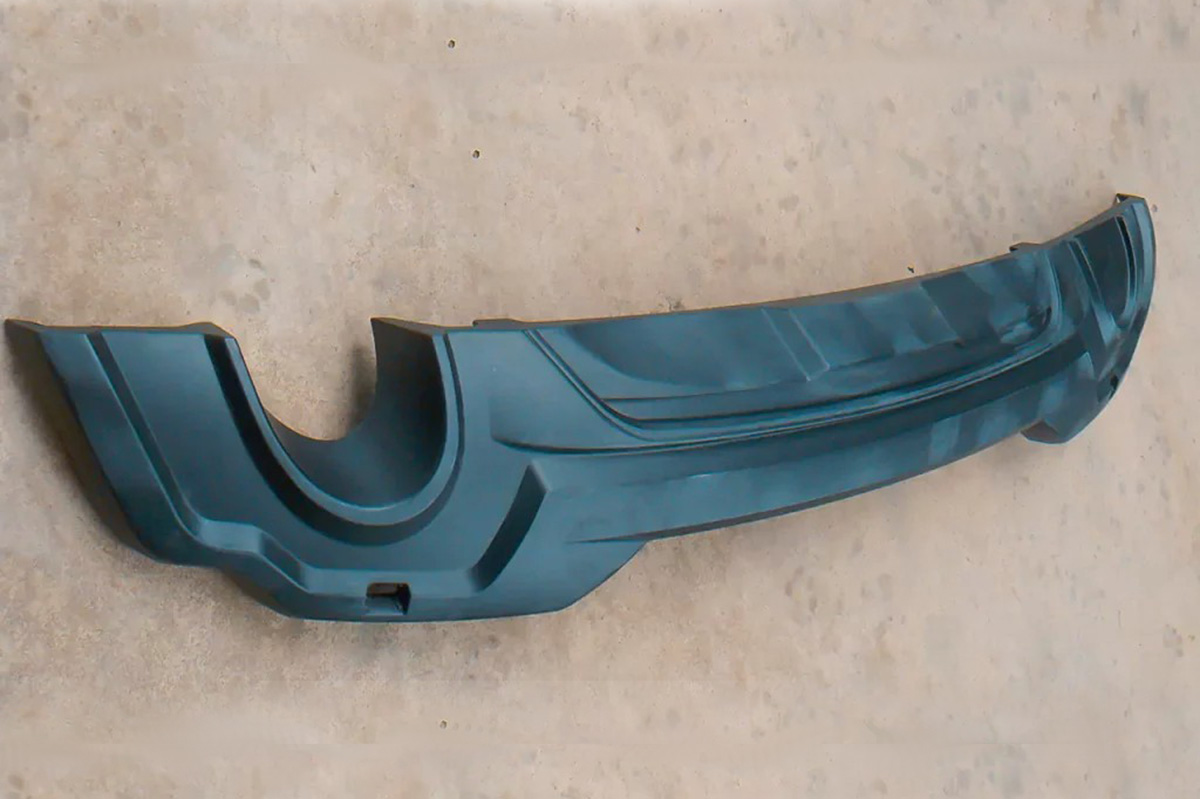
PE
PE offers excellent chemical resistance and flexibility, making it suitable for manufacturing automotive parts such as fuel tanks, water reservoirs, and underbody shielding.
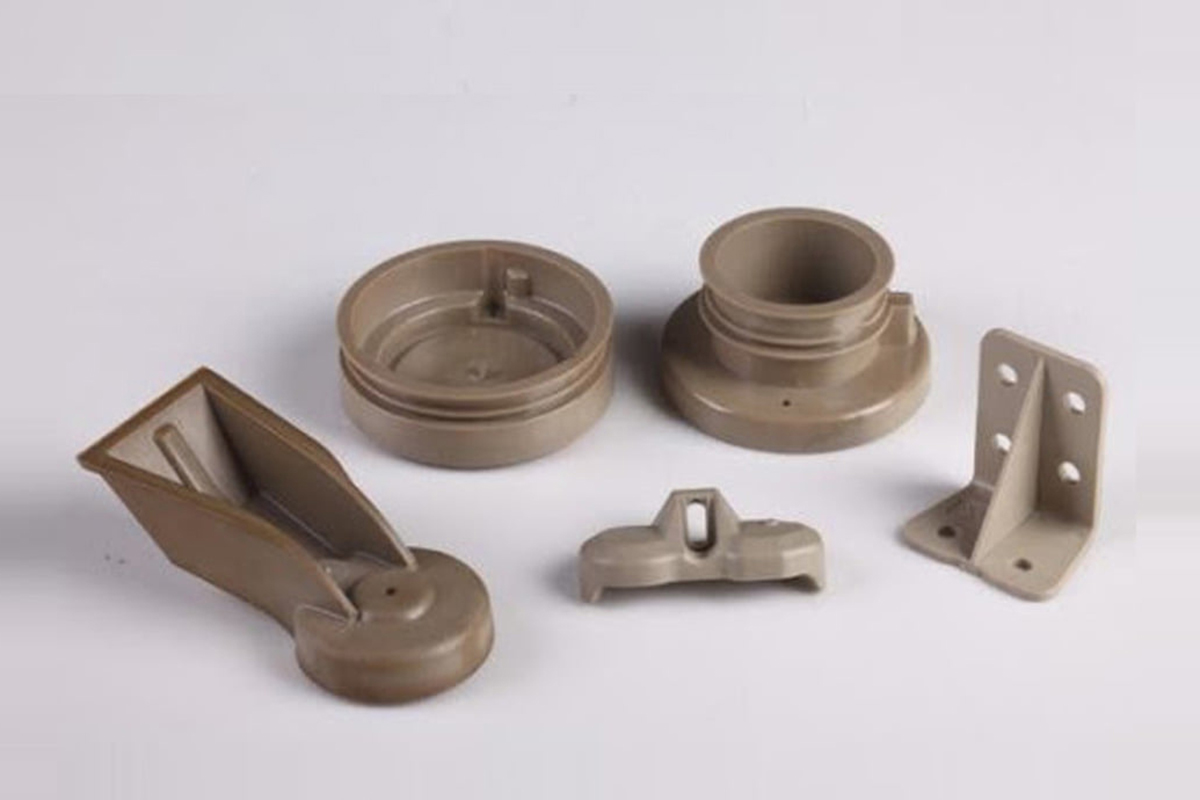
PEEK
PEEK is a high-performance thermoplastic known for its strength and thermal stability. It is commonly used to produce seals, bearings, and bushings for demanding automotive applications involving high temperatures and wear.
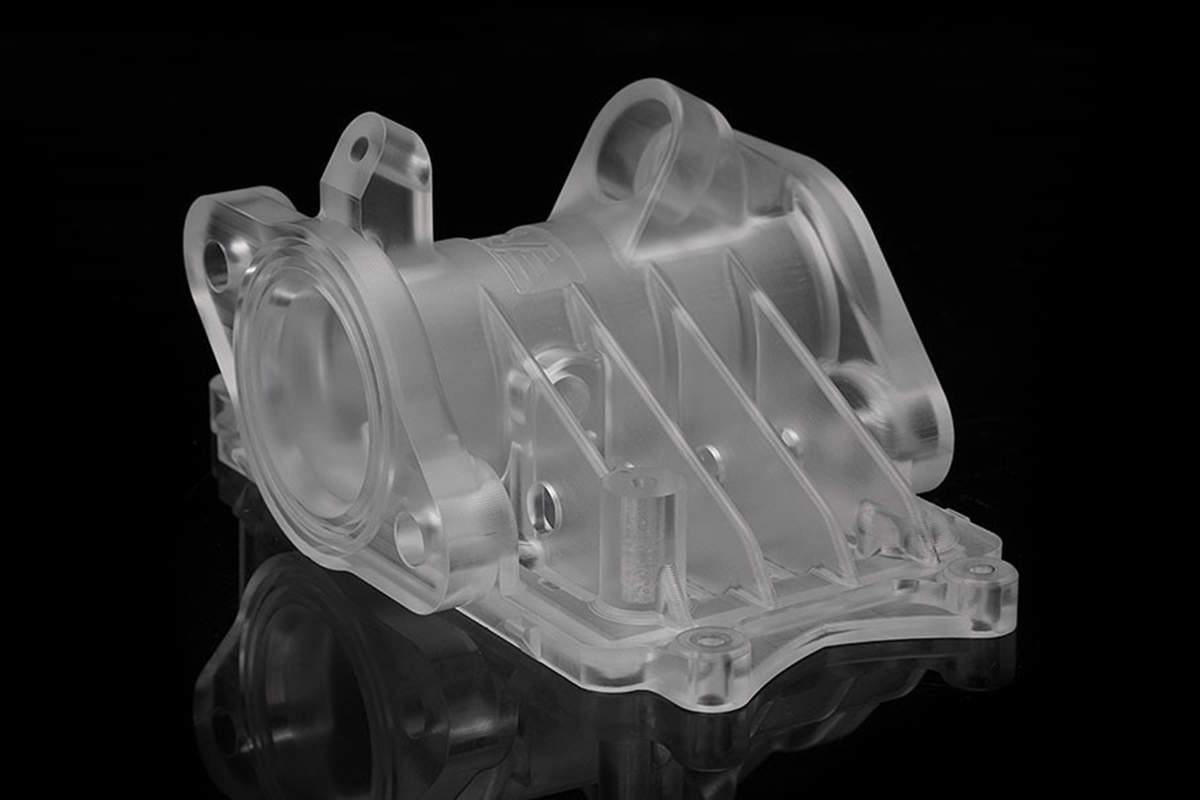
PMMA
PMMA, also known as acrylic, is valued for its optical clarity and UV resistance. It’s widely used in automotive parts like headlights, tail lights, and instrument cluster covers where transparency and weatherability are essential.
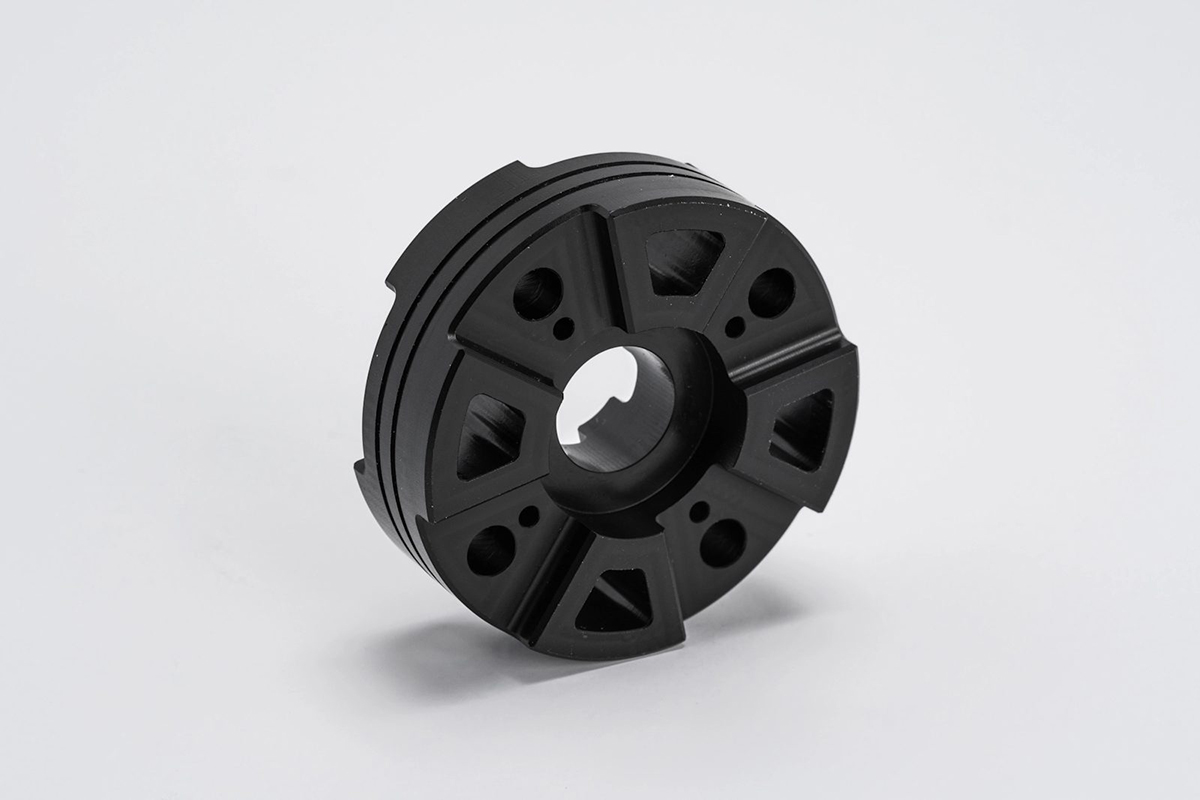
POM
POM, or acetal, is known for its excellent dimensional stability, low friction, and wear resistance. It is commonly used to manufacture automotive gears, bushings, clips, fasteners, and window regulators, where durability and smooth mechanical function are crucial.
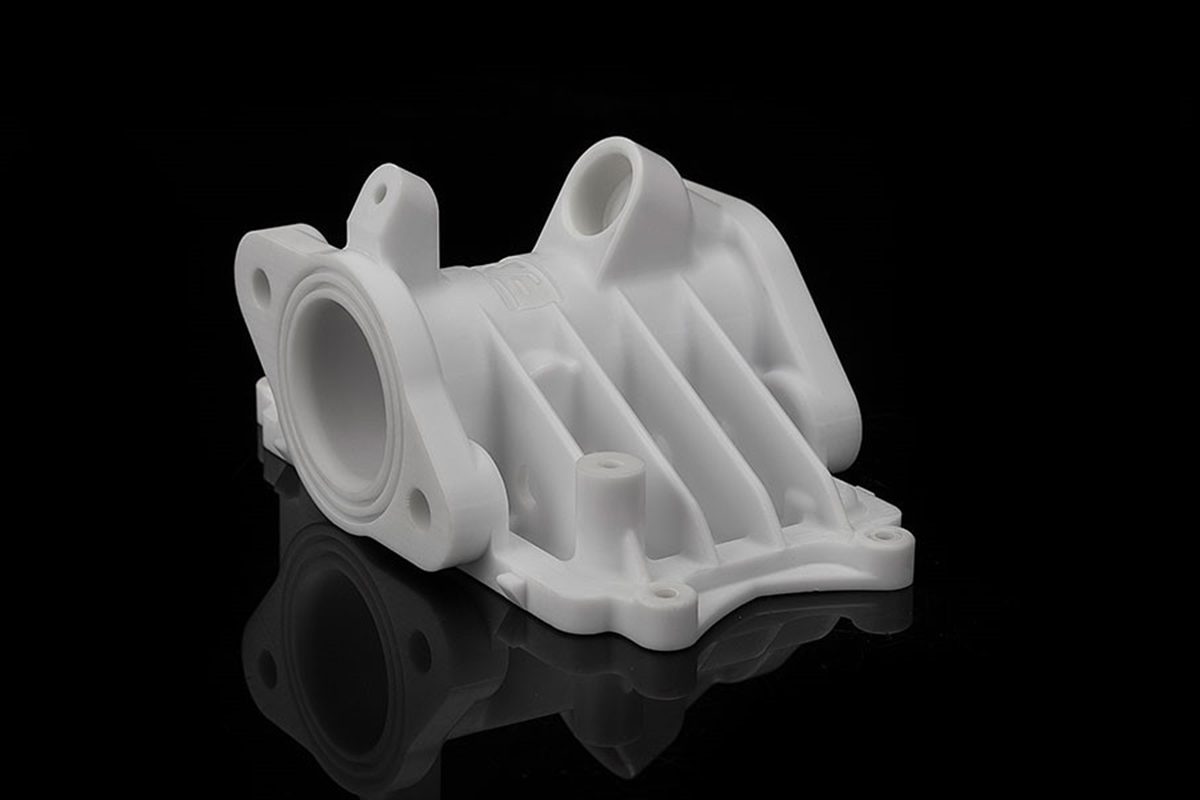
PP
PP (Polypropylene) is widely used in automotive applications due to its lightweight, chemical resistance, and durability. It is commonly used to manufacture components such as bumpers, interior trim panels, and battery cases, offering strength and flexibility for a variety of automotive needs.
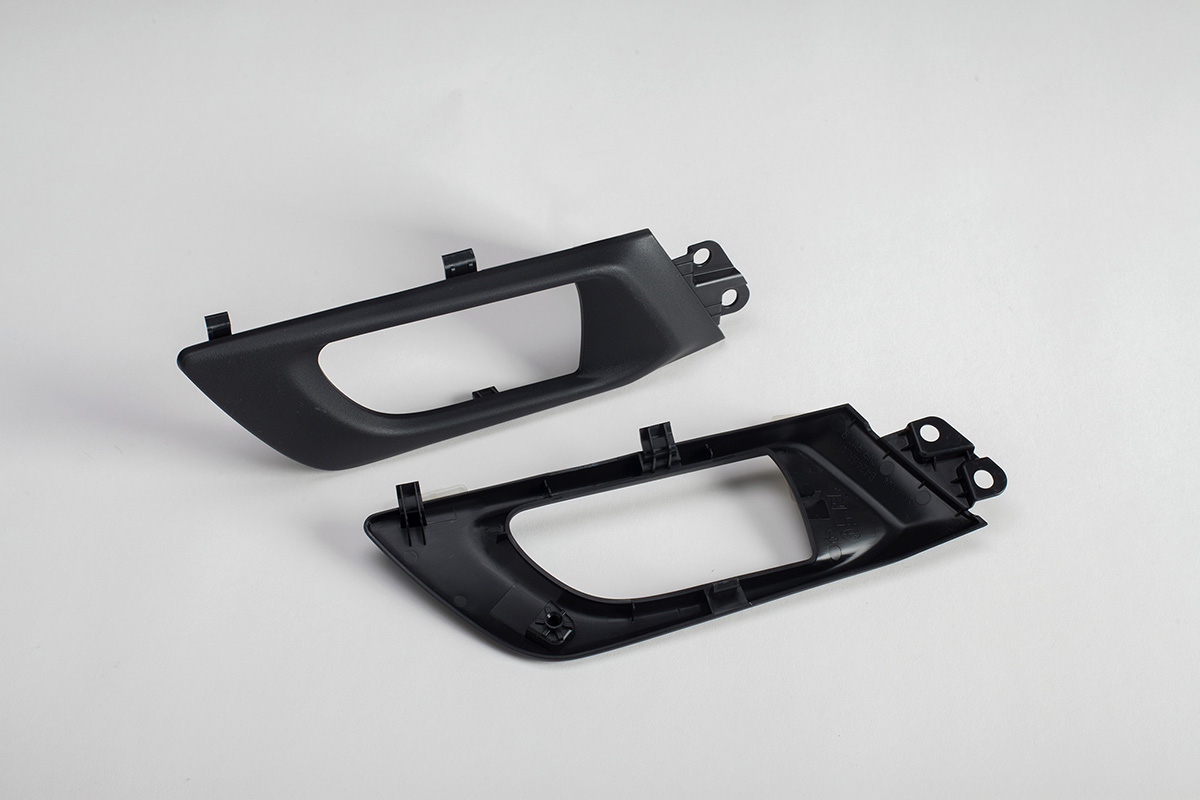
PVC
PVC (Polyvinyl Chloride) is a versatile material often used in automotive parts for its durability, strength, and resistance to wear. It is commonly used to produce components such as bumpers, interior trim panels, and battery cases, offering excellent impact resistance and versatility for a range of automotive applications.
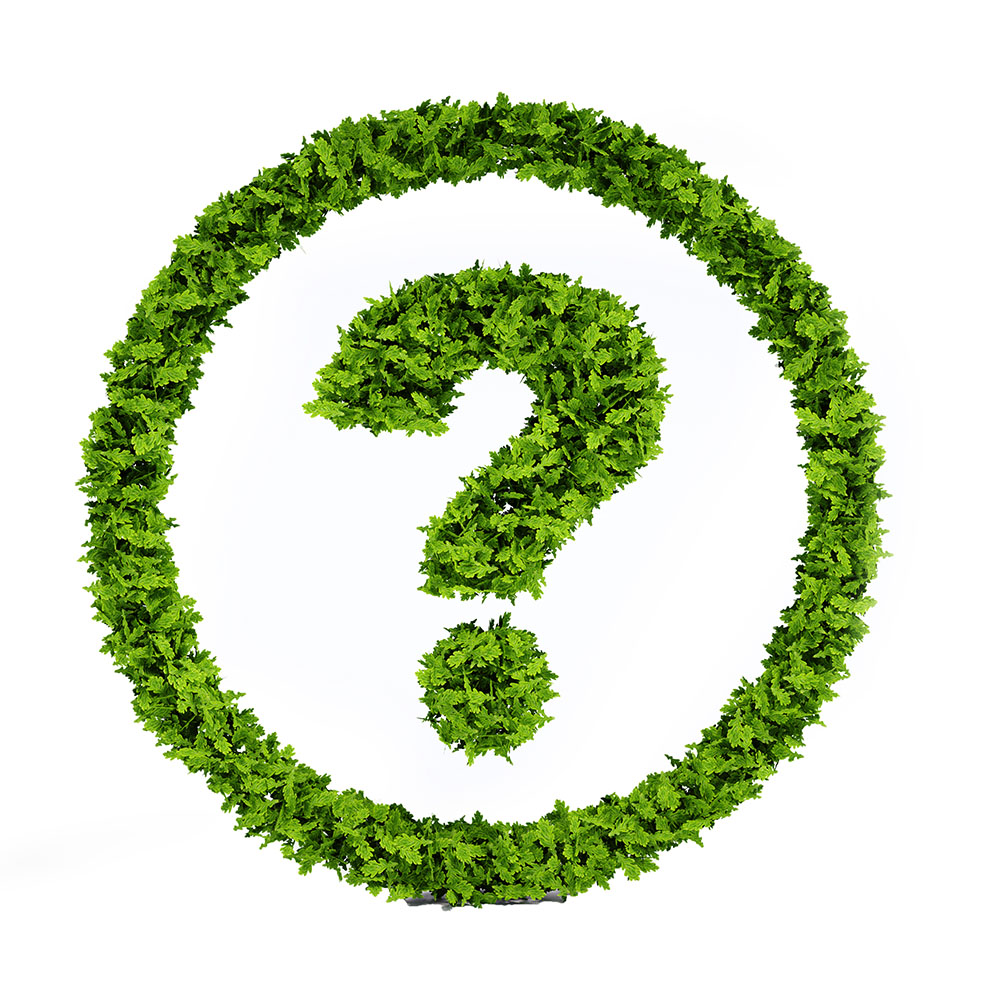
Frequently Asked Questions
We rigorously test all incoming materials to meet automotive standards, including environmental regulations like RoHS and REACH. We also provide full material certifications upon request.
Our automotive parts manufacturing strictly adheres to IATF 16949:2016 and ISO 9001:2015 certifications. We provide full inspection reports, certificates of conformity, and material traceability documentation.
KingStar Mold achieves tight tolerances up to ±0.001″ (±0.0254 mm) for critical components, meeting the demanding precision standards required in the automotive industry.
What materials are commonly used in automotive parts manufacturing, and how should they be selected?
Yes. KingStar Mold provides complete support from initial prototyping to low- and high-volume production. We utilize a variety of manufacturing methods such as injection molding, CNC machining, 3D printing, and mold making to meet different project needs. Whether you require rapid prototypes for design validation or full-scale production of automotive parts, we ensure seamless transitions, consistent quality, and on-time delivery at every stage.