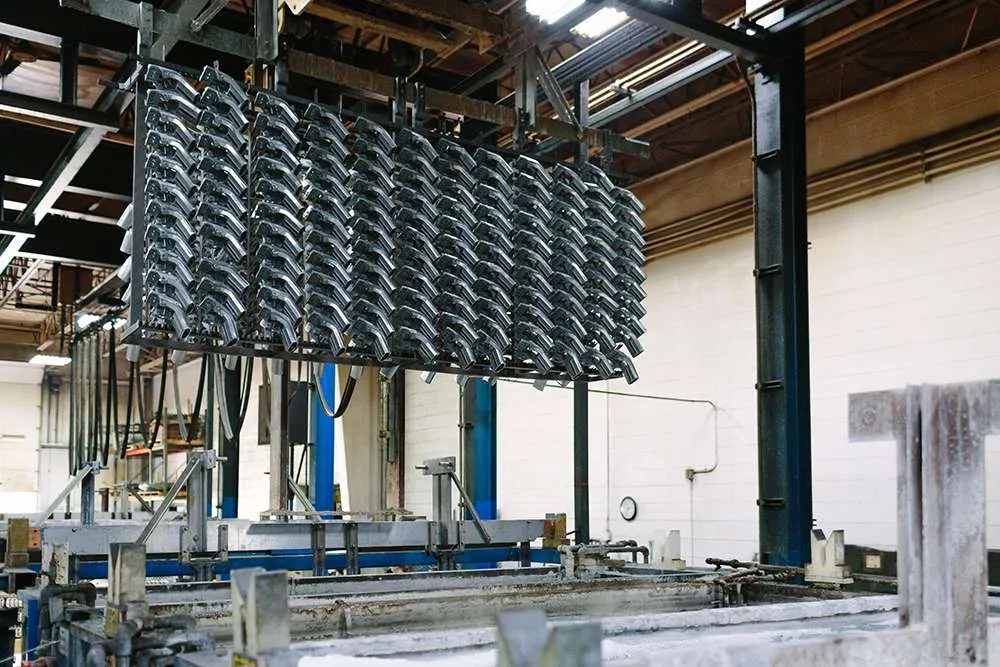
Overview of Alodine Finishing
What Is Alodine: Alodine, also known as Chem Film, is a chromate conversion coating applied to aluminum and its alloys to enhance corrosion resistance and surface adhesion. This name originally came from a trademark of Henkel, referring to a chromium oxide coating technology for aluminum surfaces. Now, Henkel has actually changed the original “alodine” trademark to Bonderite®, but due to its long-term popularity, it has been used as a proper noun ever since. It forms a thin, protective layer without altering the metal’s strength or weight, and is widely used as a base for paint or primer in aerospace, military, and industrial applications.
How Does It Work: The Alodine coating process relies on an electrochemical reaction between the metal surface and a chromate solution that typically contains chromium compounds like chromic anhydride, sodium fluoride, and tetrafluoroborate. When a metal part—usually aluminum—is immersed, sprayed, or brushed with this solution, a chemical conversion occurs that forms a thin chromium oxide film, usually just tens to hundreds of nanometers thick. This layer, while thinner than anodizing, creates a gelatinous protective barrier that effectively isolates the substrate from corrosive elements such as moisture, air, and chemicals. The result is a surface with improved corrosion resistance, enhanced adhesion for subsequent coatings, and in some cases, increased surface hardness and wear resistance.
Specifications for Alodine Finish Service
Parameter | Specification |
---|---|
Color | Golden, brown, transparent, or iridescent greenish-gold, depending on the Alodine type (e.g., Alodine 1000, 1001, 1200S, 5992) |
Thickness | Typically 0.00001 to 0.00004 inches (0.25–1 μm) |
Immersion Time | 1 to 5 minutes, depending on the size of the part and desired coating thickness |
pH Value | 1.5 to 2.0 |
Temperature | 70 to 100°F (21 to 38°C) |
Standard Types | - MIL-DTL-5541 Type 1A: Minimum thickness 0.0001 inches (0.1 mil) - MIL-DTL-5541 Type 3: Maximum thickness 0.00001 inches (0.01 mil) |
Special Types | - Alodine 1200S: Colorless or golden - Alodine 871: Hex-free, trivalent chromium-based - Alodine 5200, 5700, 5992: Other industrial applications |
Minimum Part Size (mm) | 2×2×2 |
Maximum Part Size (mm) | 3000×2200×1100 |
MIL-DTL-5541 Standard and Process We Apply for Alodine Finish
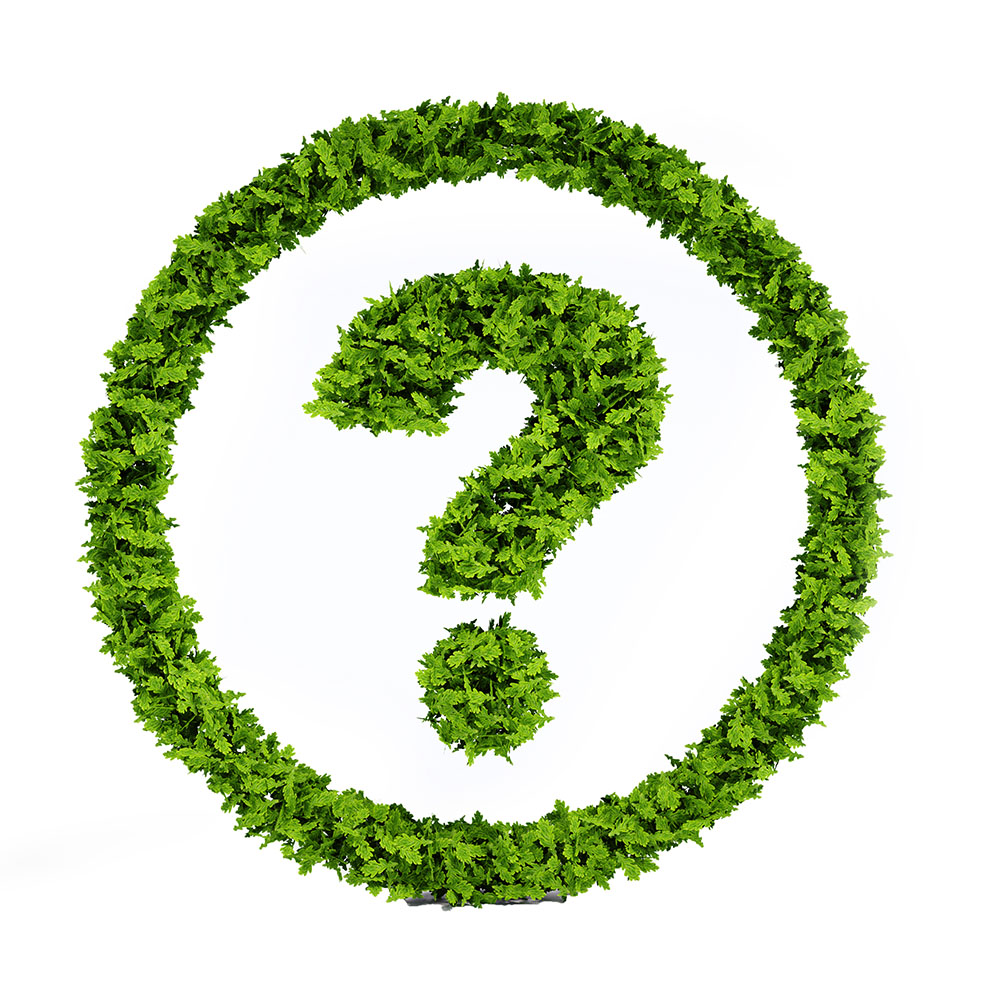
Frequently Asked Questions
Yes. One of Alodine’s key benefits is improving paint adhesion, making it an excellent base layer for subsequent painting or powder coating. But compared to Class 3, Class 1A provides better adhesion for the paint.
While both Alodine and anodizing protect aluminum, they differ in thickness, durability, and electrical conductivity. Alodine applies a thin, conductive chemical film ideal for corrosion protection and paint adhesion, whereas anodizing builds a thicker oxide layer for superior wear resistance and color variety but reduces conductivity.
[Read more about Alodine vs. Anodizing here.]