Aerospace Components Manufacturing & Production
Cooperative Partners
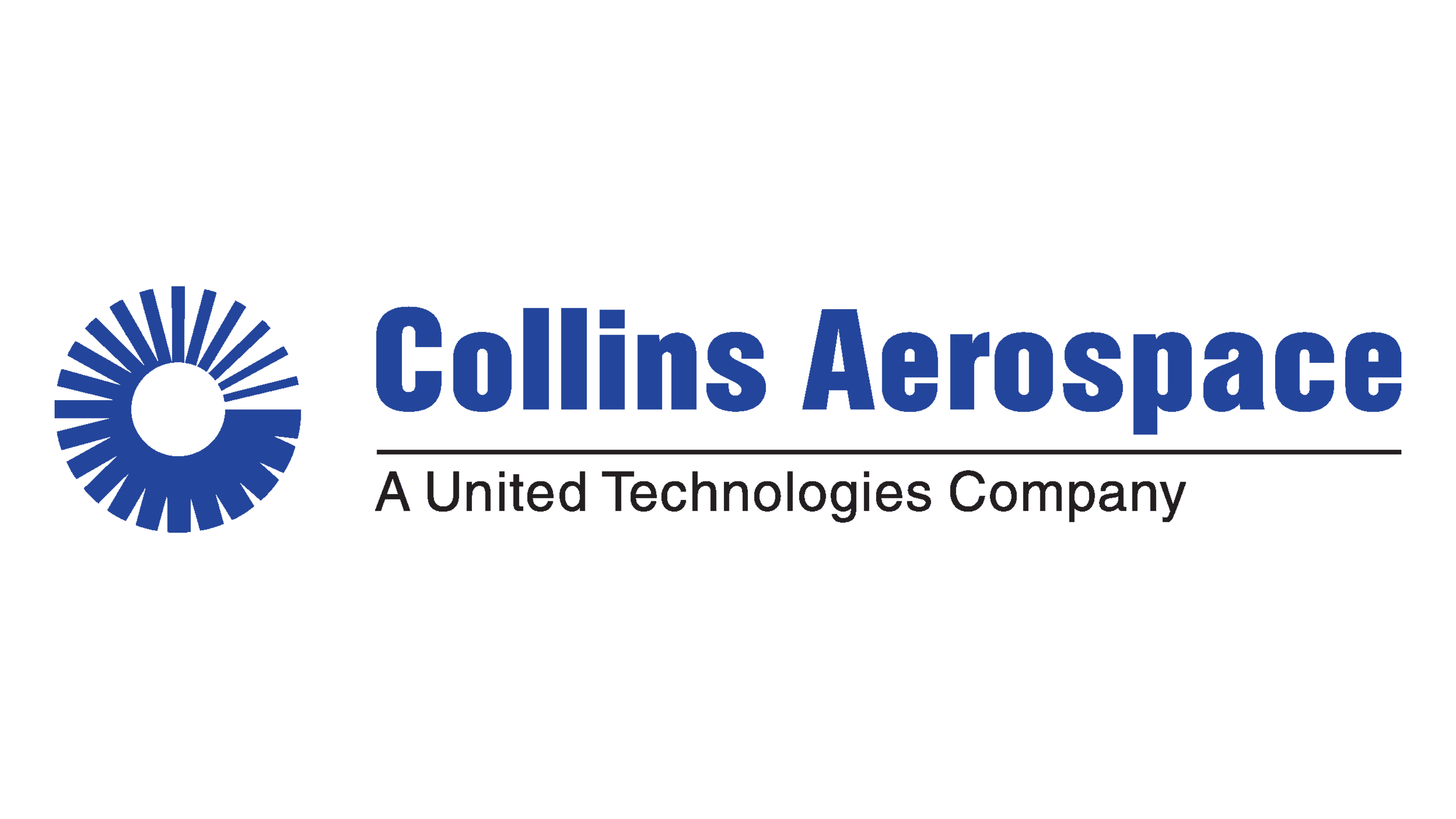
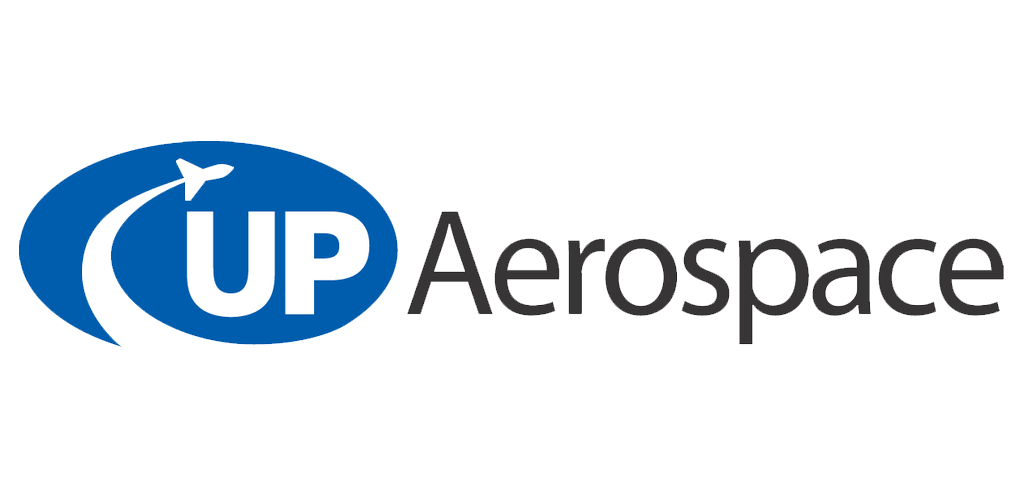
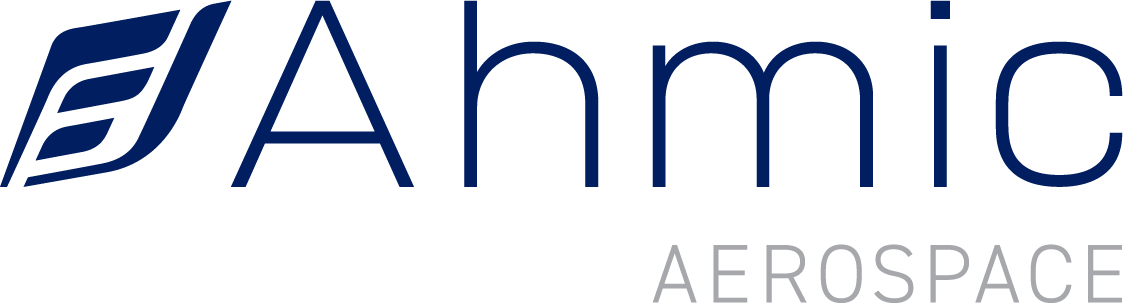
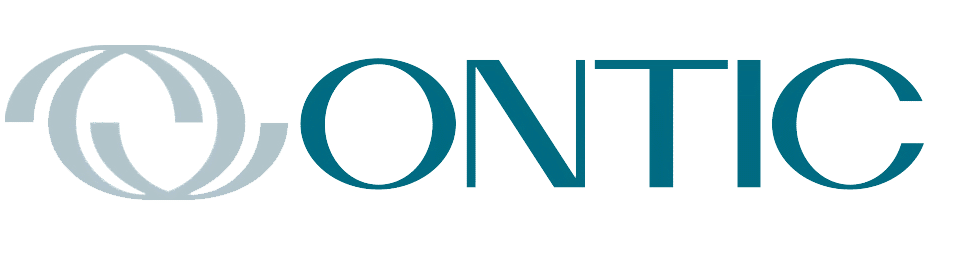
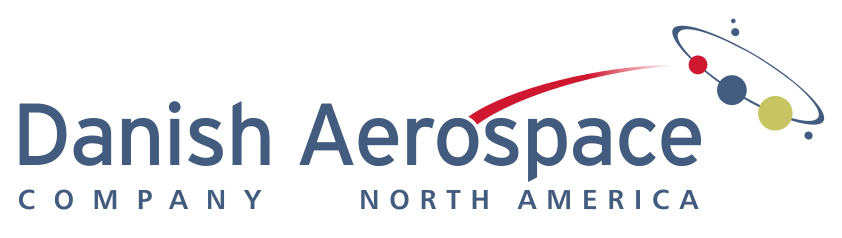
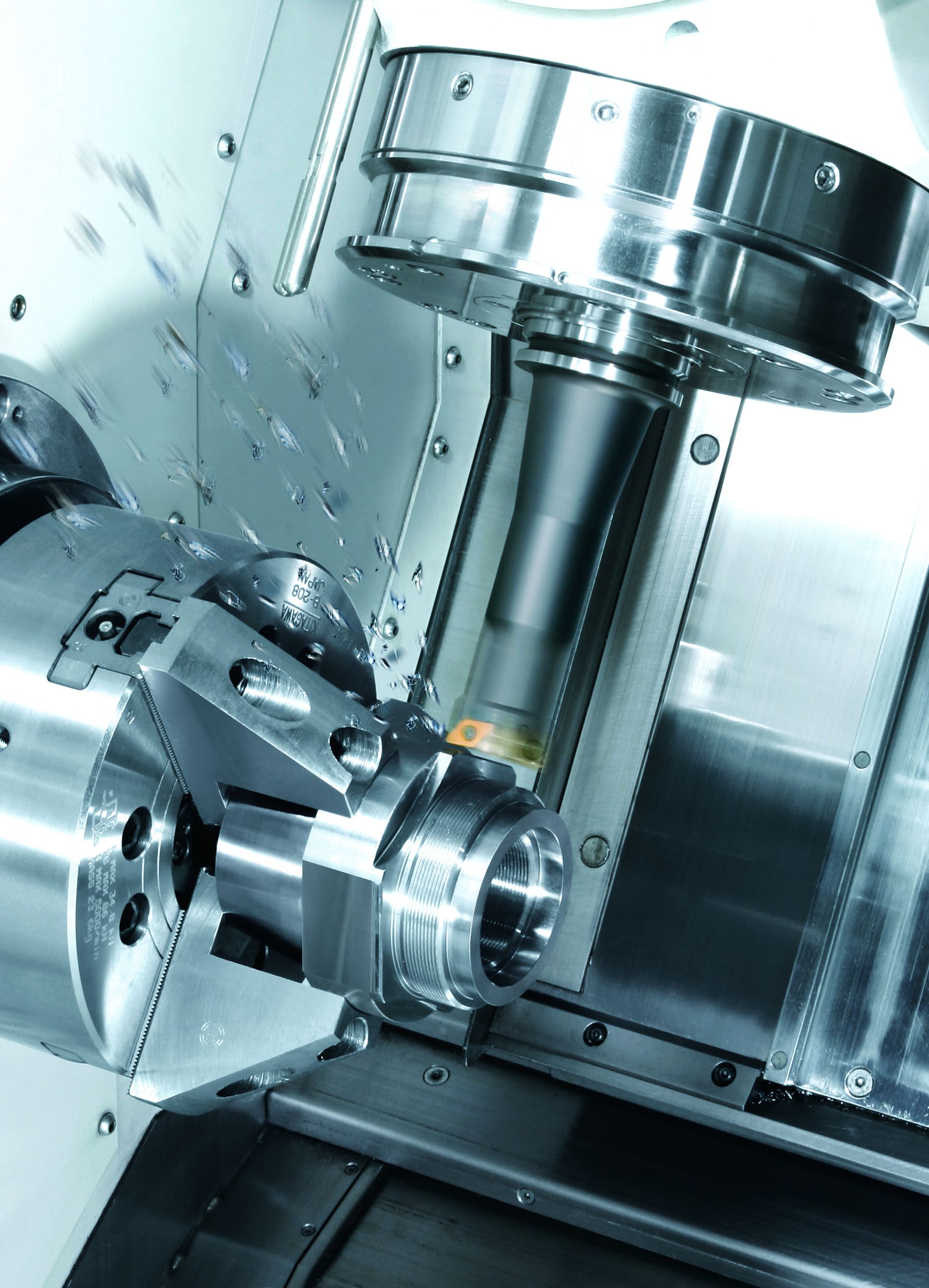
High-Precision Aerospace Manufacturing Solutions for the Global Market
10+ Years of Aerospace Manufacturing Experience
Certified Material Selection & Traceability
Fast Turnaround for Custom Orders
KingStar Mold provides custom, on-demand aerospace part machining and production services to clients worldwide. We stand out through rapid lead times, rigorous material verification, and strict quality control procedures integrated at every stage of the manufacturing process.
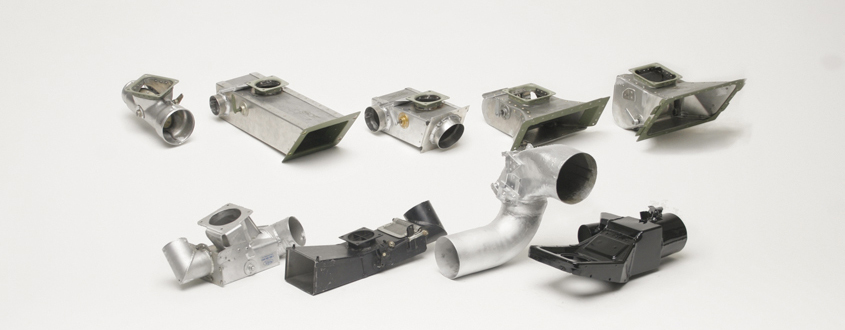
How We Support Aerospace and Defense Companies
Rapid Prototyping Support
At KingStar Mold, we help aerospace and defense clients accelerate development by providing fast and precise prototyping services. Our instant DFM (Design for Manufacturability) feedback allows engineers to refine designs early, ensuring smooth transitions from concept to early- and late-stage prototypes.
End-to-End Product Development
We streamline your product development process with flexible low-volume production and rapid prototyping solutions. Our experienced applications engineers work closely with your team to support every phase—from iterative development to the final production of end-use aerospace parts.
Jigs, Fixtures, and Tooling
Need production-grade tooling fast? We manufacture durable jigs, fixtures, and other custom aids within days, helping your assembly lines stay efficient and your development timeline on track.
Certifications and Traceability You Can Trust
KingStar Mold supports aerospace-grade quality through ISO 9001-compliant machining and advanced 3D printing. For high-requirement parts, we offer full documentation and material traceability—including aluminum traceability for qualifying projects.
Wide Selection of Aerospace Materials
We offer a diverse range of materials to meet aerospace and defense demands, including high-temperature plastics, medical-grade silicone rubber, and ultra-precise 3D-printed micro-resolution parts. Whether you need metals, plastics, or elastomers, we help you find the right fit for mission-critical applications.
100%+
Fortune 500 Aerospace Companies Served
750 Million
Parts Manufactured
300,000+
Customers Served Globally
80+
Countries Served Worldwide
What We Can Make for You
Aerospace Parts Manufacturing Capabilities
KingStar Mold offers a comprehensive range of manufacturing services tailored to the aerospace industry.
Our core processes include:
We specialize in the precision production of aerospace components through advanced techniques such as high-tolerance CNC machining, durable mold fabrication, and injection molding of high-performance polymers. We also support rapid prototyping and short-run manufacturing through 3D printing upon request.
*Note: Due to non-disclosure agreements with many of our clients, we only showcase selected aerospace parts with express permission.
Aerospace Interior Parts
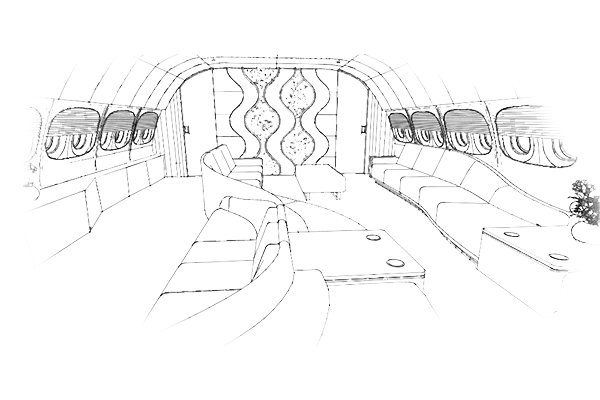
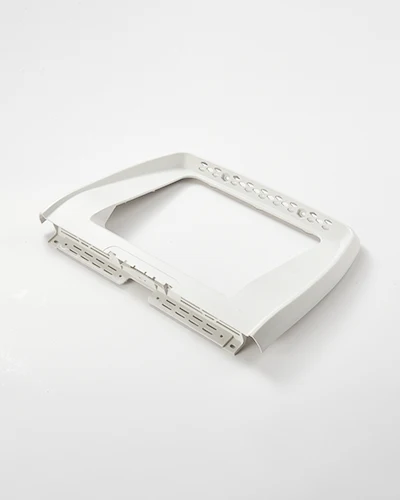
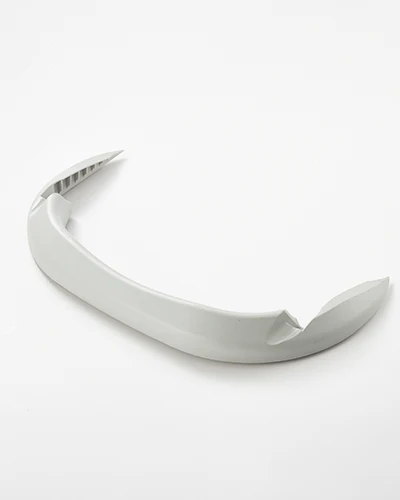
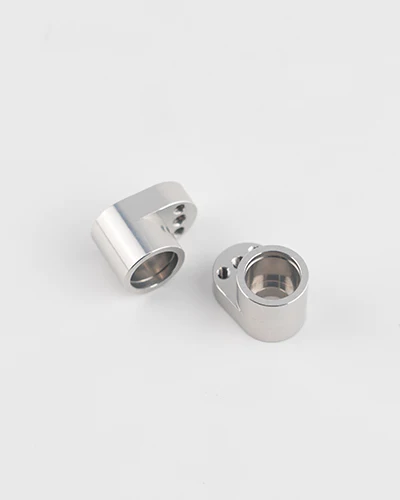
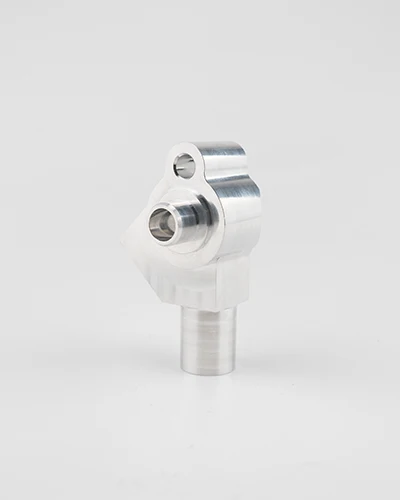
Aerospace Structural Components
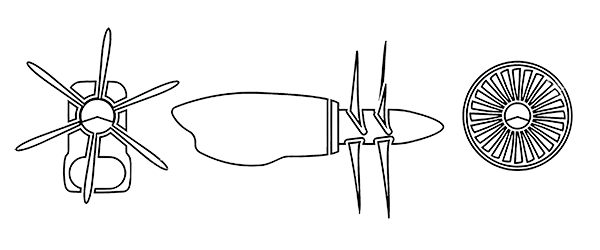
Electronics and Control System
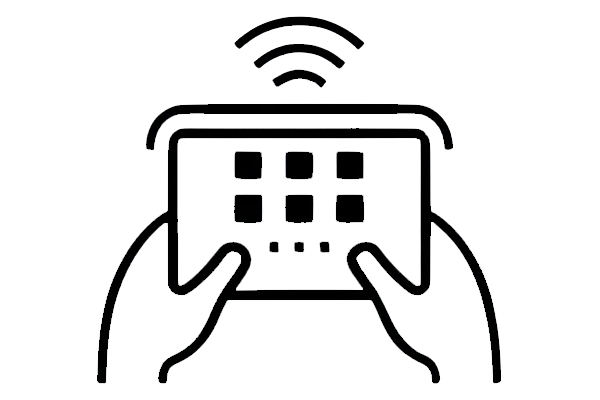
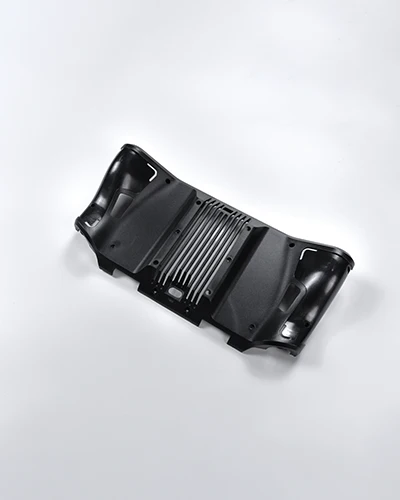
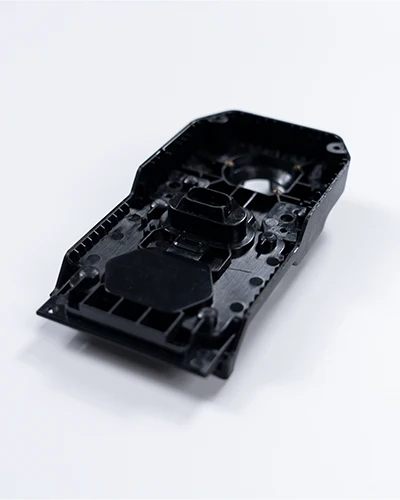
Dedicated Full-Scale Production Support
Our experienced manufacturing team oversees every stage of your production order, from start to finish. We handle the entire process with precision and efficiency—while keeping you informed with timely updates throughout.

Account Manager
Your dedicated account manager offers personalized assistance—from platform navigation to file uploads—ensuring smooth communication and project handling.
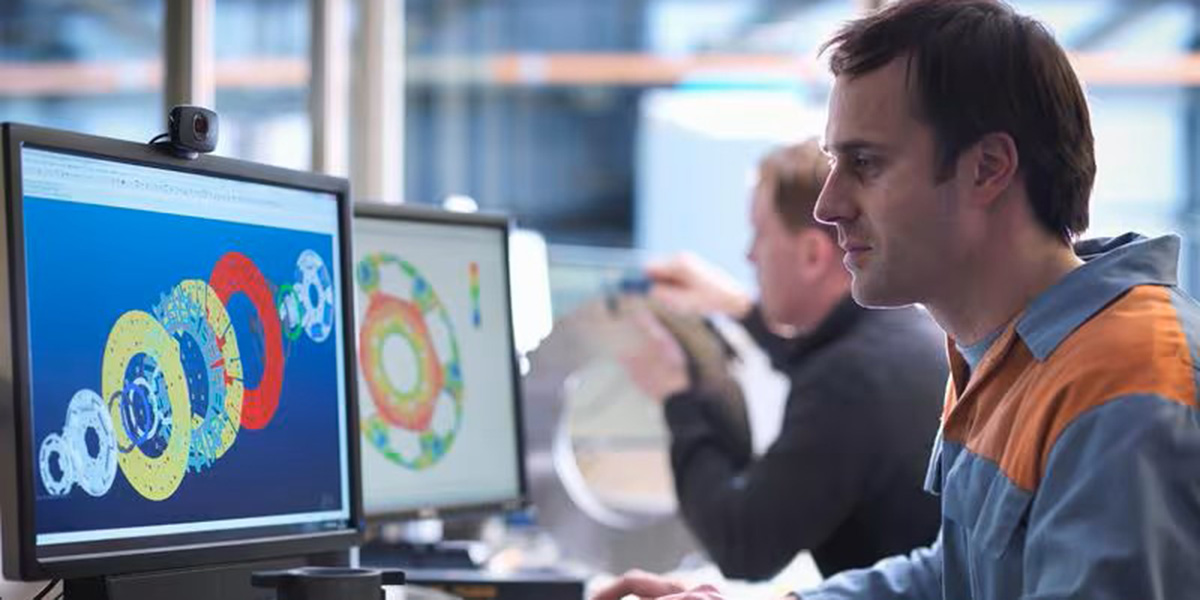
Application Engineers
Our in-house application engineers provide expert CAD support and design optimization, helping you reduce costs while maintaining performance and manufacturability.
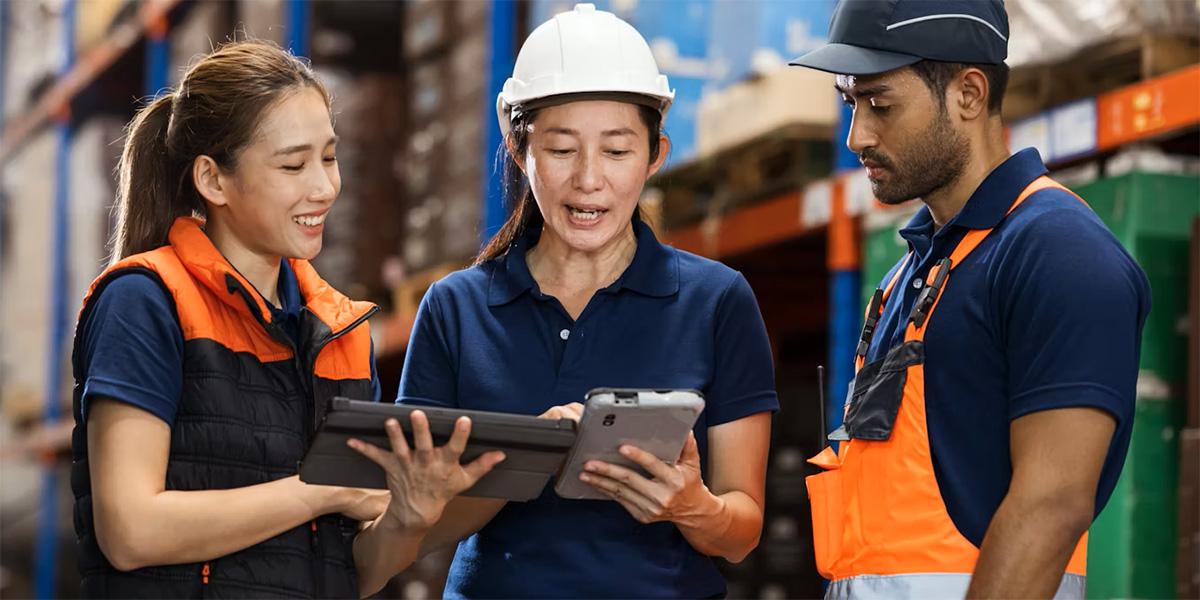
Logistics
Our operations specialists manage global logistics with precision, ensuring fast, reliable delivery and streamlined supply chain coordination.
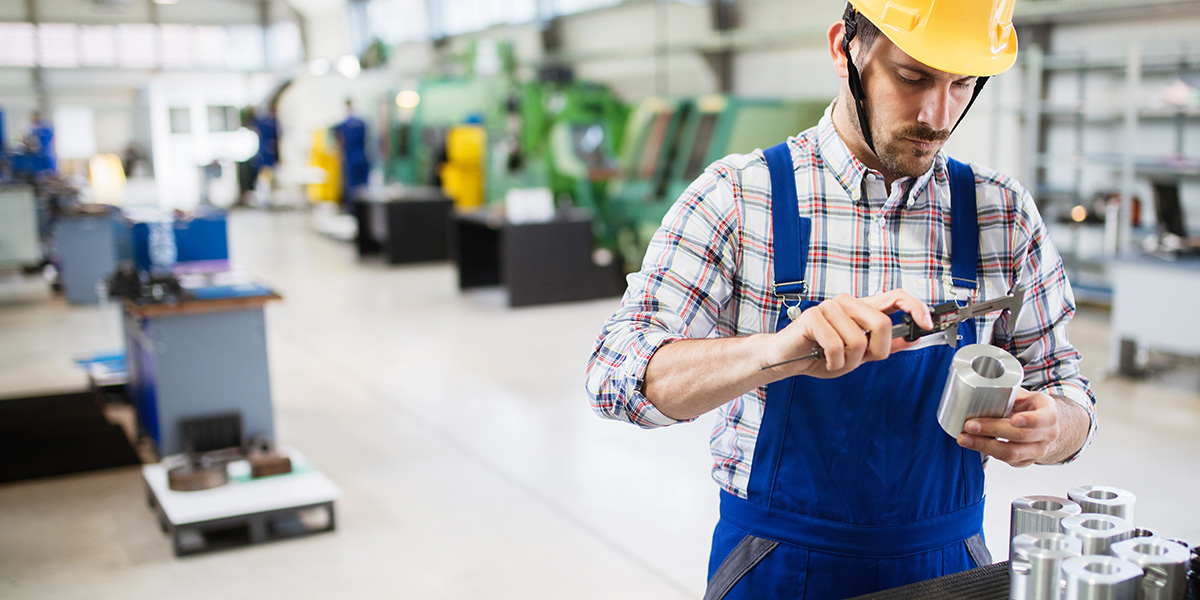
Recommended Aerospace Manufacturing Solutions
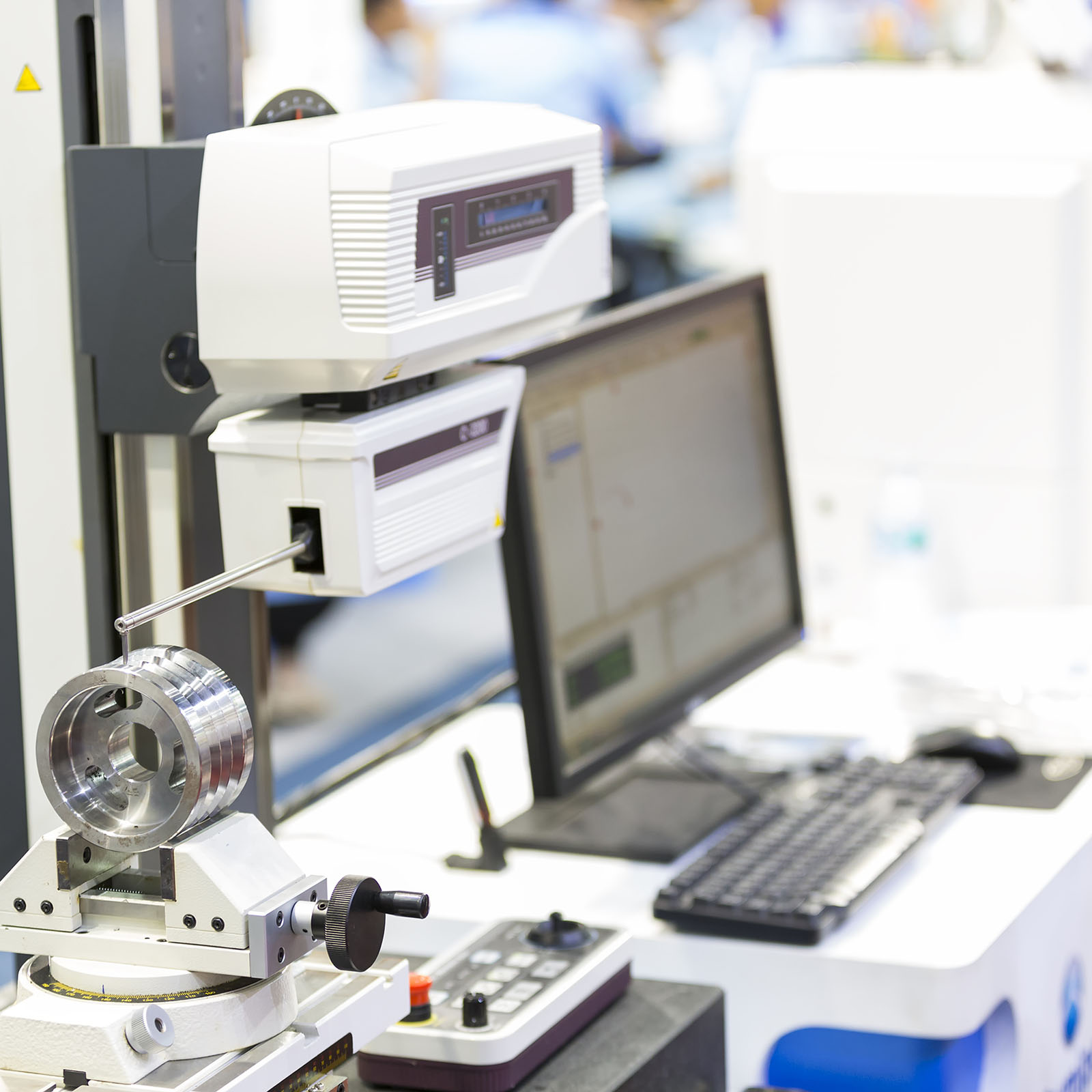
Aerospace Industry Quality Assurance
At KingStar Mold, we implement strict quality control procedures and maintain internationally recognized certifications to ensure every aerospace part meets both regulatory requirements and customer expectations.
KingStar Mold’s commitment to quality gives you the confidence to trust us with even your most demanding aerospace components.
Our Advantages in Aerospace Parts Production
1
Uncompromising Quality and Safety
We recognize the extreme performance and safety requirements of aerospace components. That’s why every project undergoes a strict, multi-stage quality control process designed to meet both regulatory standards and your internal benchmarks.
4
Optimized Performance Outcomes
With a decade of experience in aerospace part production, our engineering and production teams help you achieve more reliable and higher-performing parts that surpass expectations.
2
Rapid Turnaround Times
Working under tight deadlines? Our combination of in-house production capabilities and a trusted supplier network allows us to deliver high-quality aerospace parts quickly—helping you stay ahead of schedule and ahead of the competition.
5
Advanced Finishing Options
We offer a wide selection of functional and aesthetic surface finishes—from precision polishing to protective coatings—tailored to meet both appearance and operational demands of aerospace components.
3
Expert DFM Support
Our team provides in-depth Design for Manufacturing (DFM) analysis to identify possible design flaws, reduce manufacturing risks, lower costs, and enhance product performance—before production even begins.
6
Complete Traceability & Compliance
We maintain full production traceability, providing detailed process records and certifications for materials, processes, and inspections—ensuring every part meets AS9100, ISO 9001, and other aerospace-grade requirements.
Materials For the Aviation Components
Aerospace parts require a broad range of materials, and KingStar Mold is fully equipped to work with them—including metals, engineering plastics, and rubber compounds. Materials like Titanium, Aluminum, Inconel, and Stainless Steel are commonly used for structural and high-performance aerospace parts, processed through CNC machining or metal 3D printing. For flexible or sealing components, we also offer options like liquid silicone rubber and fluorosilicone with specialized chemical resistance.
In addition, plastics such as ABS, Nylon (PA), PBT, and Acrylic (PMMA) are widely used for housings, brackets, and interior parts. These materials are suitable for both injection molding and rapid prototyping via CNC milling.
For every aerospace project, we provide material certification documents to confirm the authenticity and quality of materials used. If clients have specific supplier preferences, we can source materials directly according to their requirements to meet strict aerospace compliance and performance standards.
Metal Materials
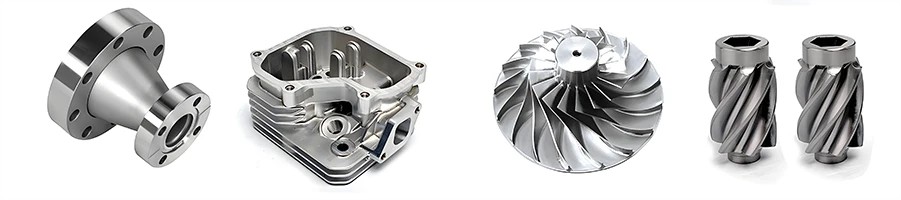
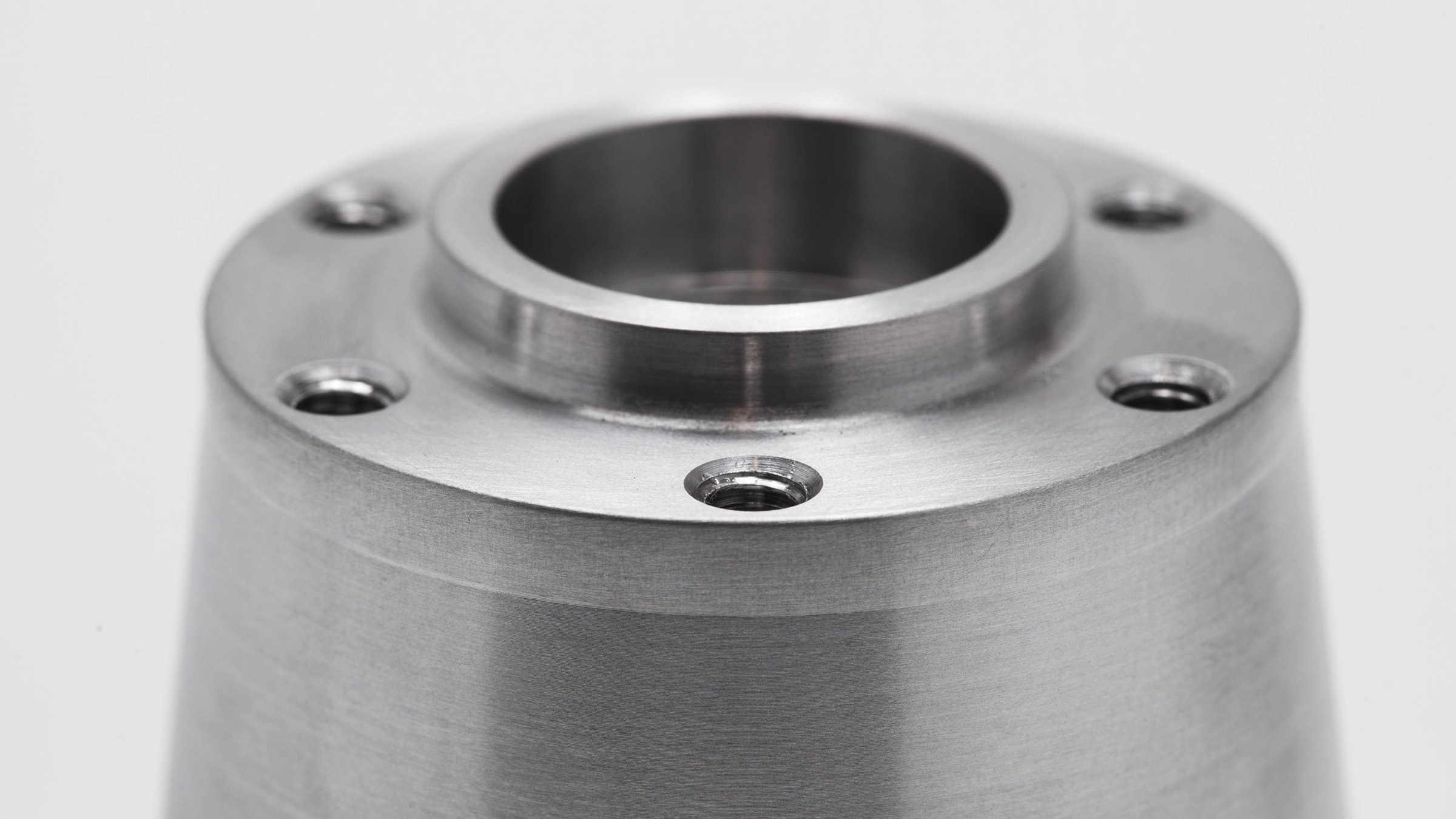
Aluminum
With an excellent strength-to-weight ratio, aluminum is a versatile choice for structural parts like housings and brackets that must endure heavy loads. It is available for both machined and 3D-printed aerospace applications.
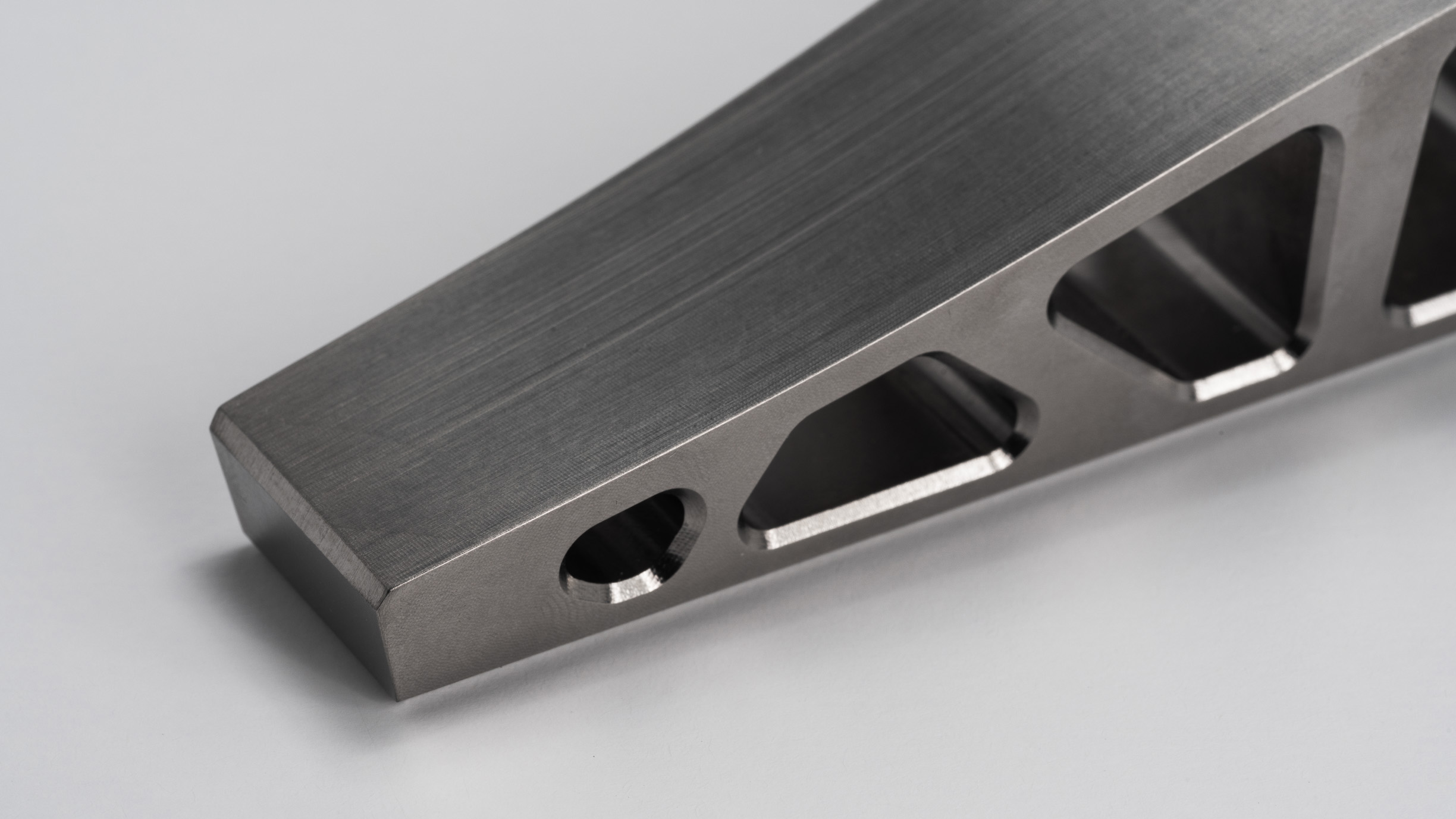
Titanium
Offered through both CNC machining and metal 3D printing, titanium is a lightweight yet high-strength material known for its exceptional resistance to corrosion and extreme temperatures—making it ideal for critical aerospace components.
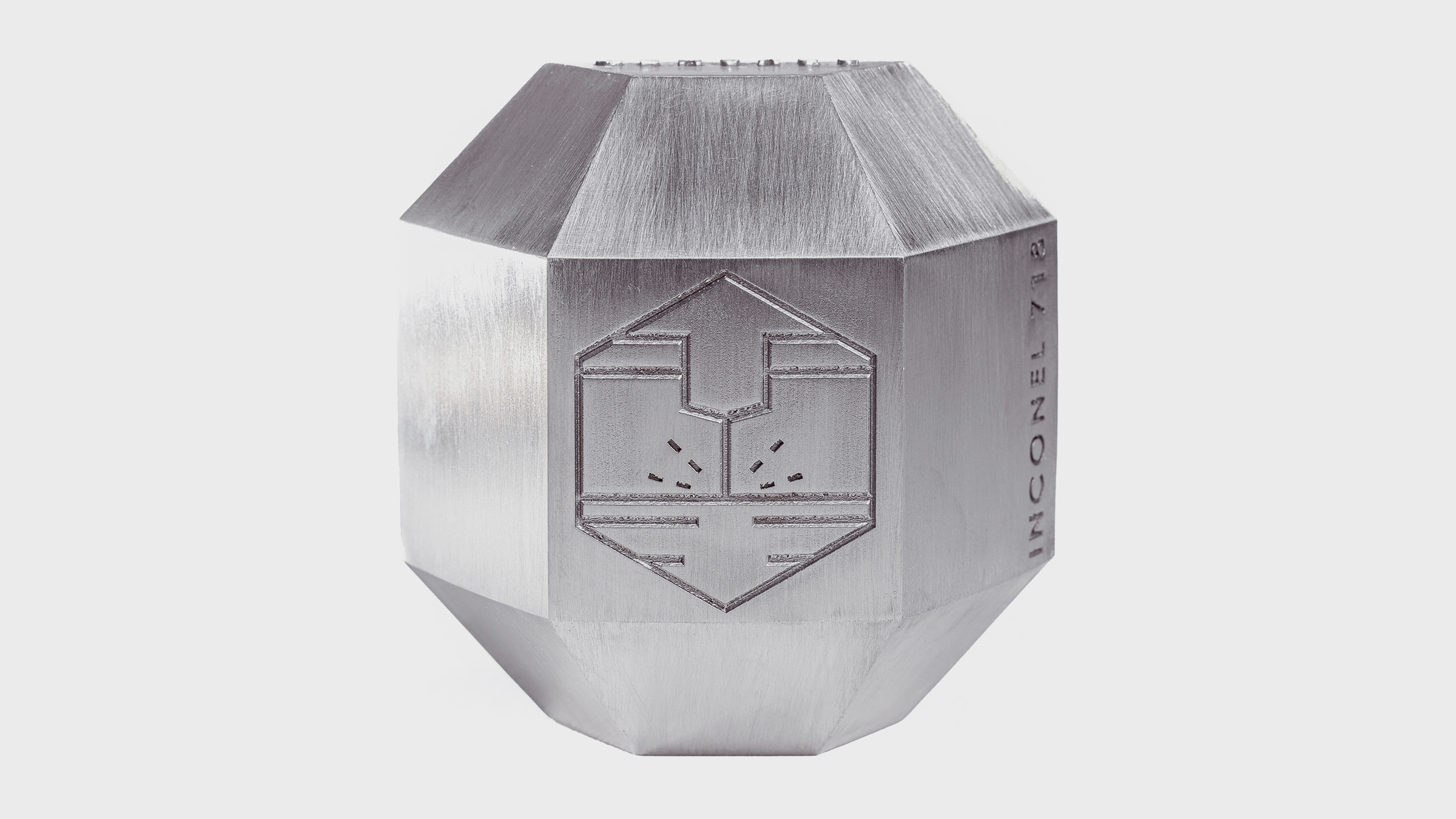
Inconel
Inconel is a high-performance nickel-chromium superalloy used primarily through 3D printing. Its outstanding heat resistance makes it perfect for demanding aerospace environments, including rocket engines and turbine components.
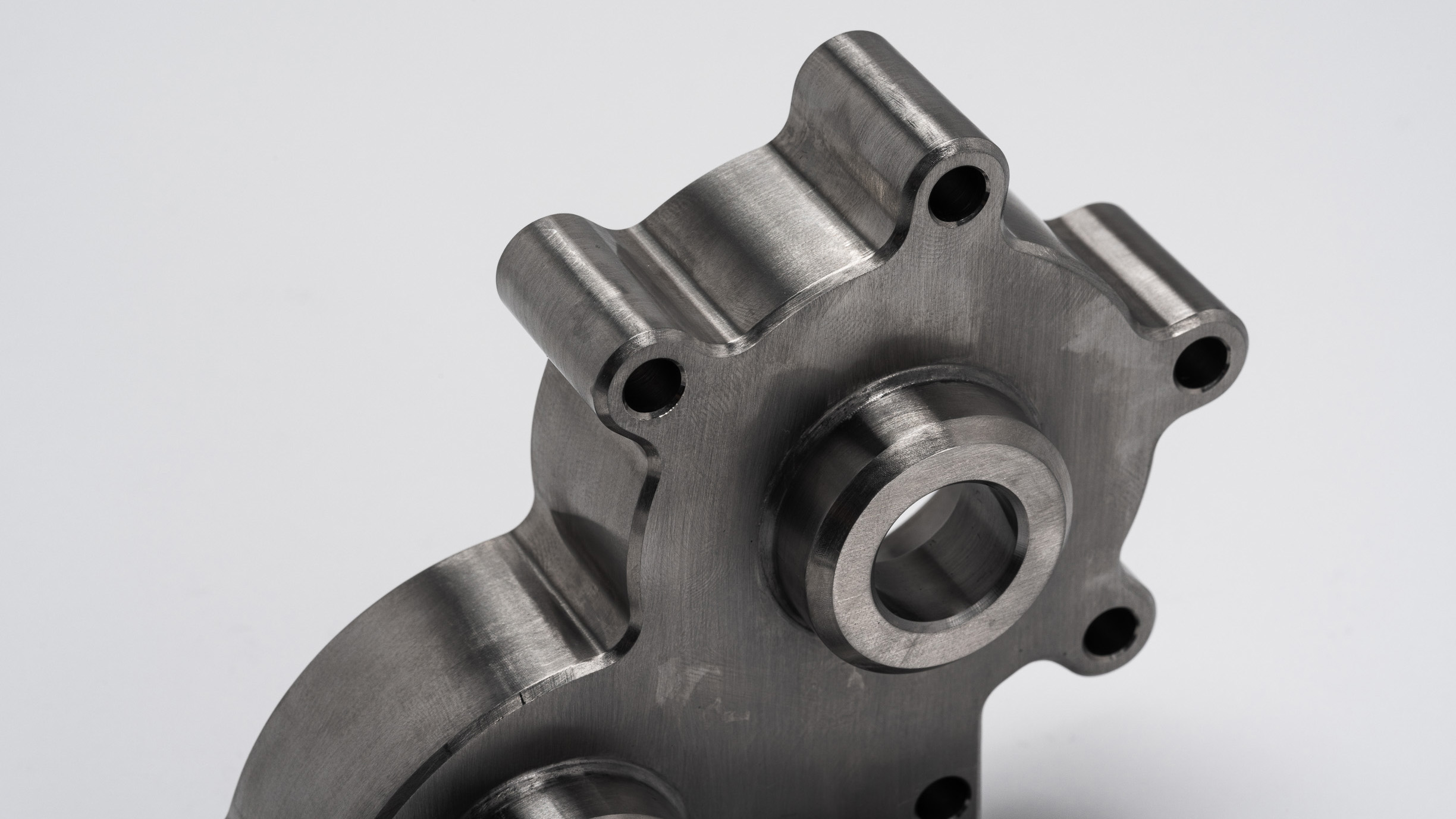
Stainless Steel (17-4 PH)
Renowned for its high strength, corrosion resistance, and reliable mechanical performance at elevated temperatures (up to 600°F), SS 17-4 PH is a trusted material in aerospace manufacturing for structural and high-load parts.
Plastic & Rubber Materials
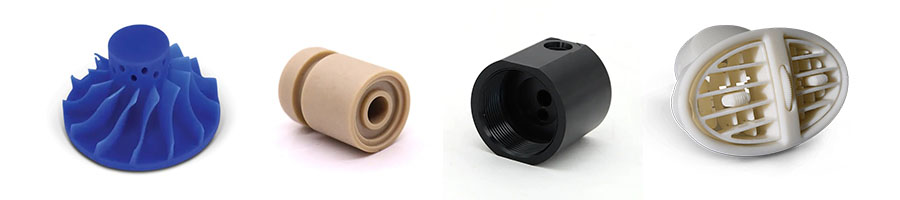
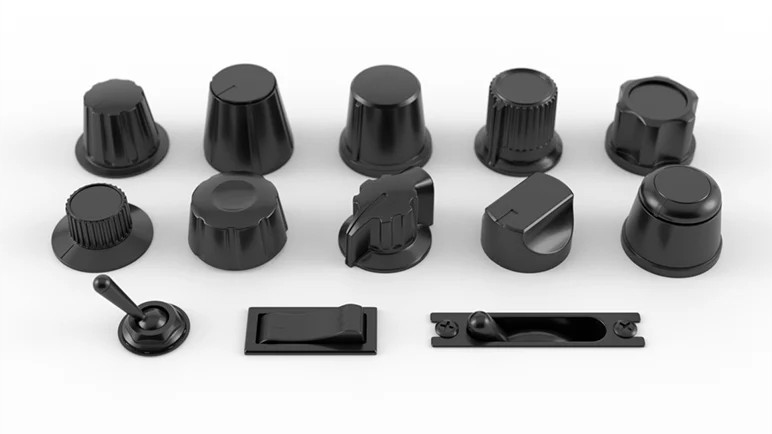
ABS (Acrylonitrile Butadiene Styrene)
ABS is a lightweight thermoplastic with good impact resistance, dimensional stability, and ease of processing. It is ideal for interior aerospace components such as panels, housings, and brackets.
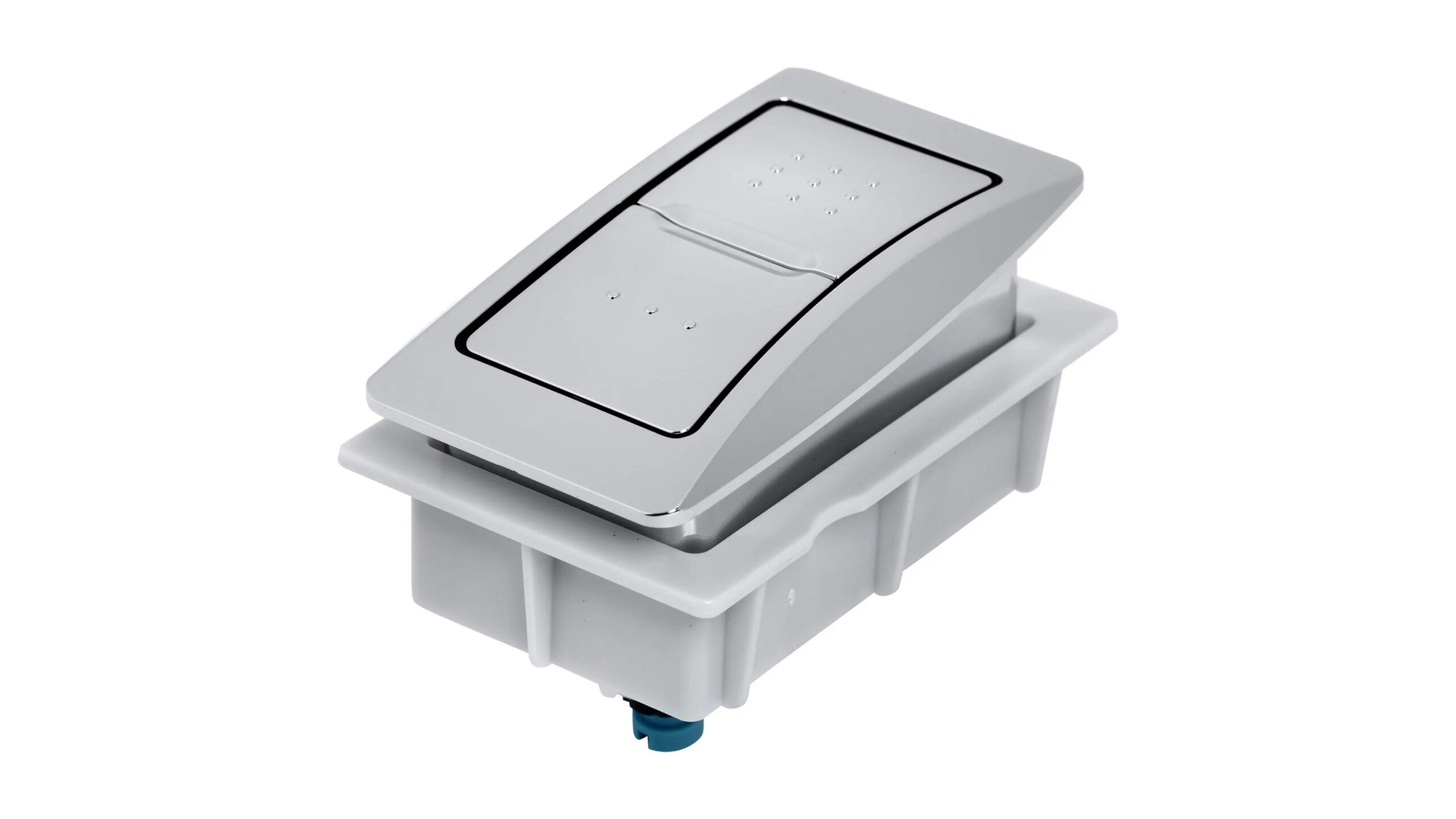
PBT (Polybutylene Terephthalate)
PBT offers high heat resistance, low moisture absorption, and good electrical insulation. This engineering-grade thermoplastic is commonly used in aerospace electrical components, connectors, and sensor housings.
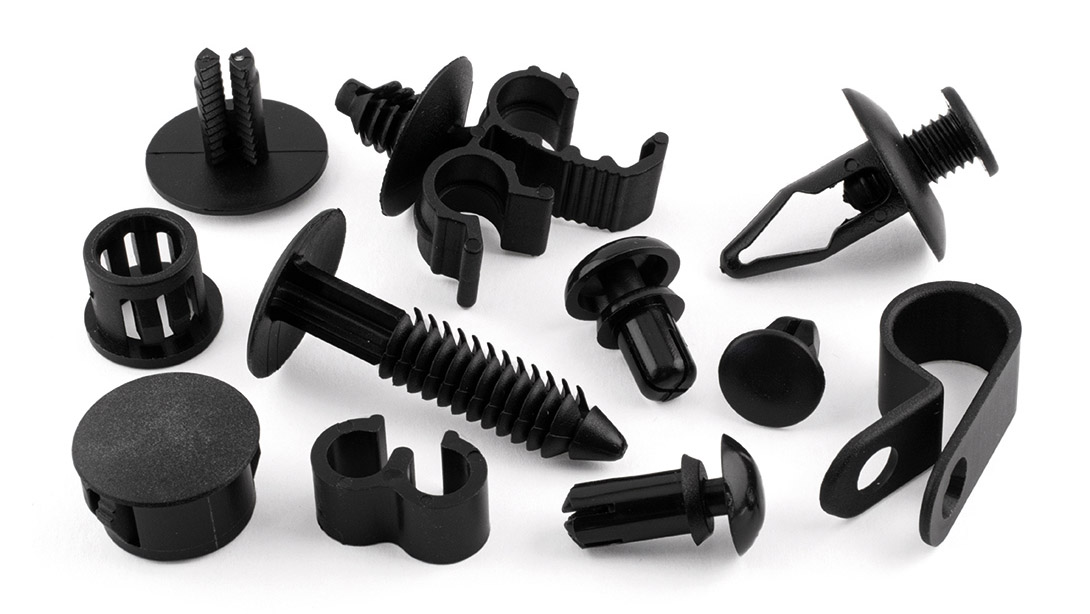
Nylon (Polyamide)
Known for its excellent mechanical strength, wear resistance, and chemical durability, nylon is suitable for aerospace applications that demand toughness and reliability—particularly for gears, bushings, and functional enclosures.
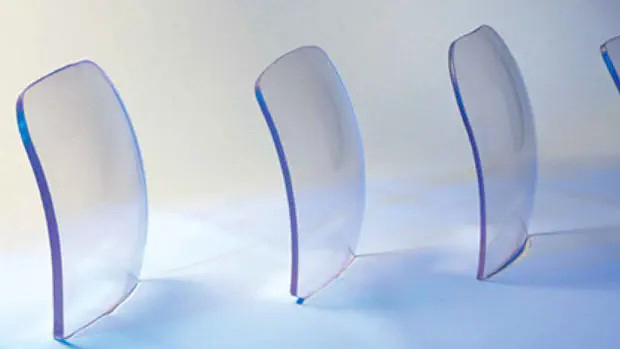
Acrylic (PMMA)
Acrylic provides outstanding optical clarity and weather resistance, making it a solid alternative to glass in aerospace lighting covers, instrument panels, and viewing windows.
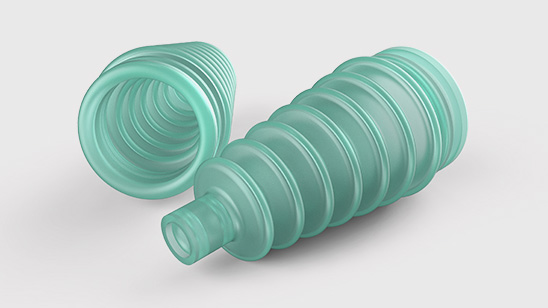
Liquid Silicone Rubber (LSR)
We offer specialized grades of liquid silicone rubber, including fluorosilicone for enhanced fuel and oil resistance, and optical silicone as a high-clarity alternative to PC or PMMA—suitable for aerospace seals, lenses, and enclosures.
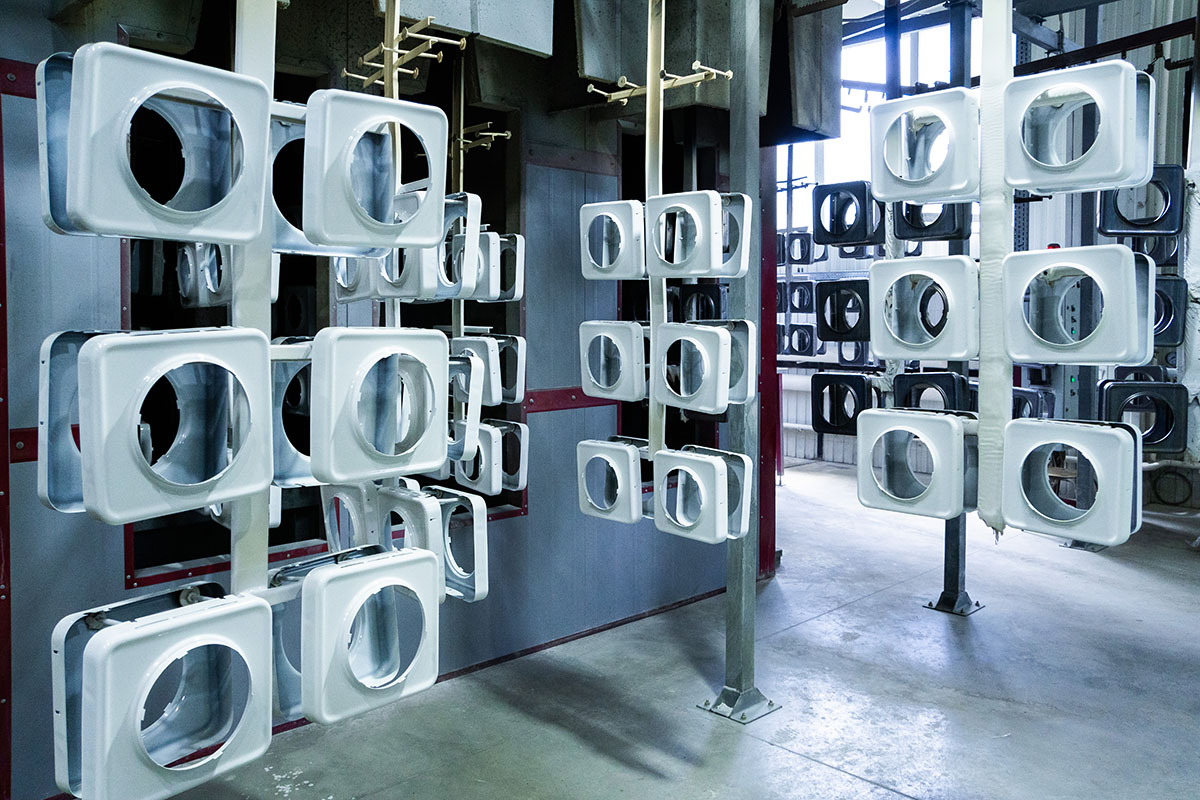
Surface Treatments for Aerospace Components
At KingStar Mold, we offer a wide range of surface finishing solutions tailored to the functional and visual requirements of aerospace parts. Depending on the material—metal or plastic—and the client’s specifications, we choose the most suitable treatment method. When no specific instructions are provided, a high-gloss finish is typically used as the default.
Here are the common surface treatments we provide for aerospace components:
Common Aerospace Applications
At KingStar Mold, our diverse manufacturing capabilities are tailored to meet the complex needs of the aerospace industry. From precision prototyping to full-scale production, here are some of the most frequent aerospace applications we support:
Factory Gallery
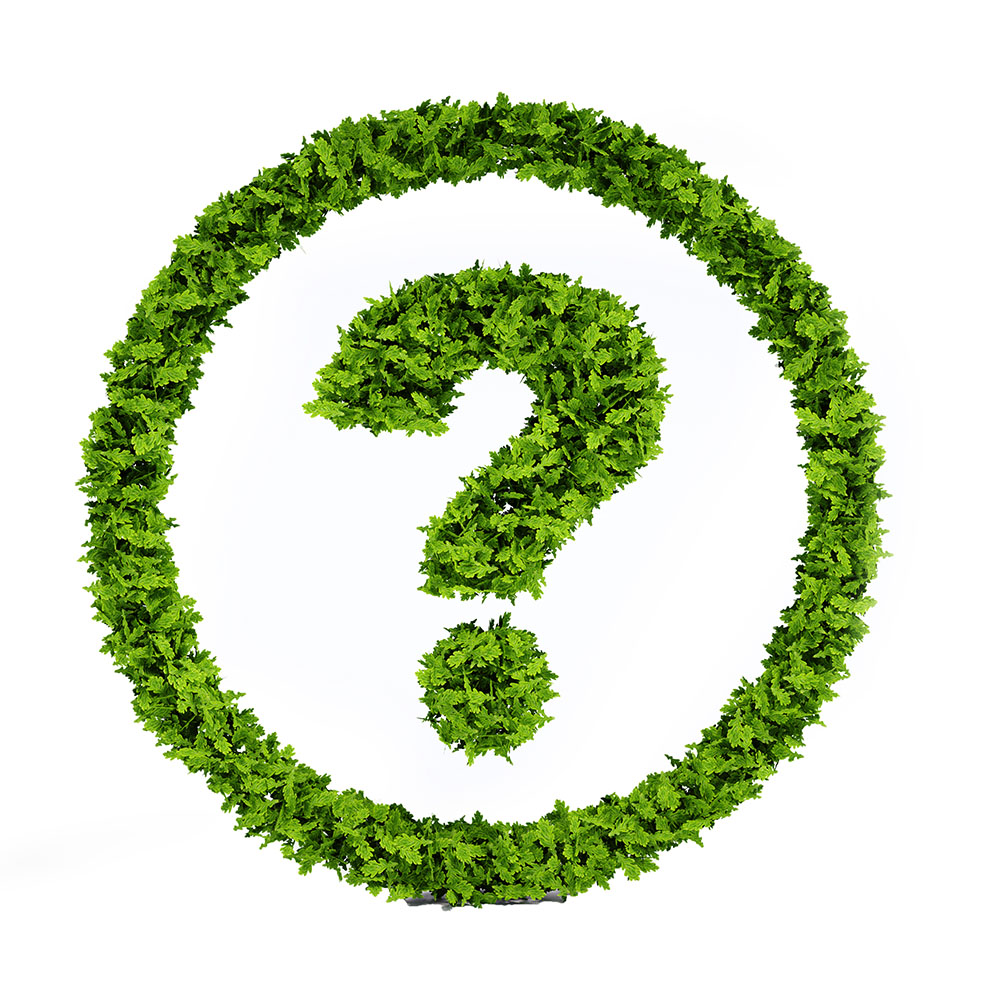
Frequently Asked Questions
Yes, our engineering team provides design-for-manufacturing (DFM) analysis to help optimize part geometry, reduce weight, improve performance, and minimize production costs—essential for meeting the demands of aerospace applications.
Yes, many customers provide material supplier details. We’re happy to source from approved suppliers to meet exact aerospace project needs.
Common certifications include AS9100, ISO 9001, and REACH/RoHS compliance, especially for traceability, safety, and environmental responsibility.
Yes, KingStar Mold fully supports both low-volume and prototype production for aerospace applications. For rapid prototypes, we can deliver parts in as fast as 3–7 working days, depending on the complexity and process. Low-volume production orders typically take 2–4 weeks, offering a balance between speed and quality. Our flexible capacity allows aerospace clients to move quickly from design validation to functional testing and short-run production—without long waits or tooling delays.
KingStar Mold specializes in producing a wide range of aerospace components, including housings, brackets, interior parts, and structural assemblies, using CNC machining, injection molding, die casting, and 3D printing.