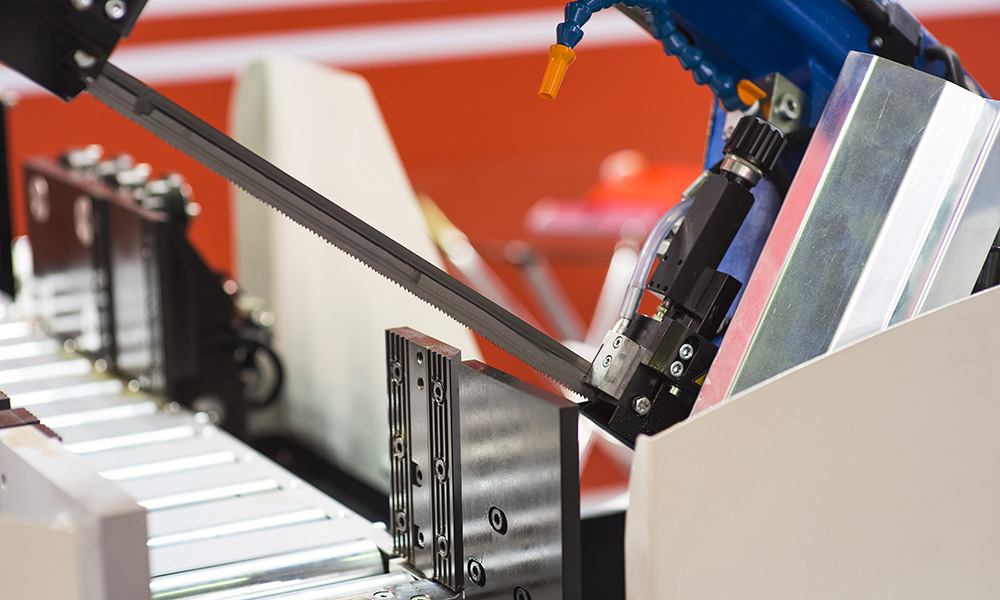
Versatile Applications of ABS Injection Molding Across Industries
ABS plastic’s durability, strength, and aesthetic appeal make it ideal for a wide range of industrial applications.
Consumer Electronics
Appliances

Medical Devices
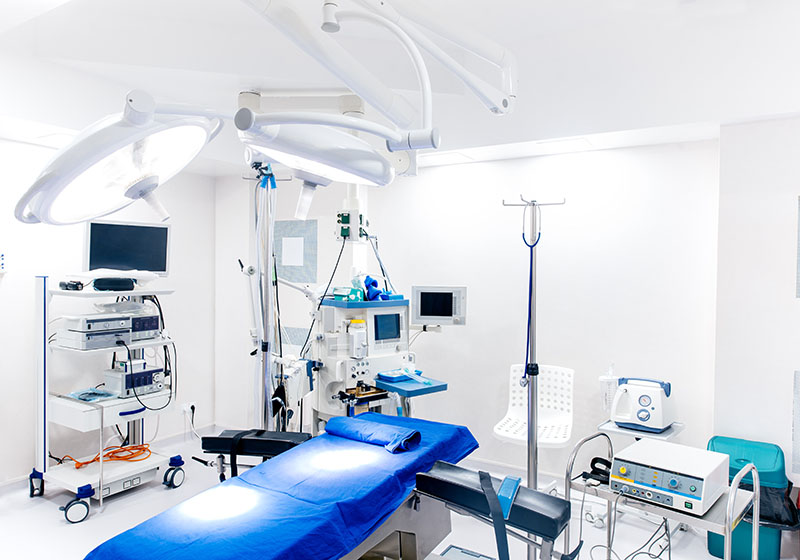
EV & Automotive
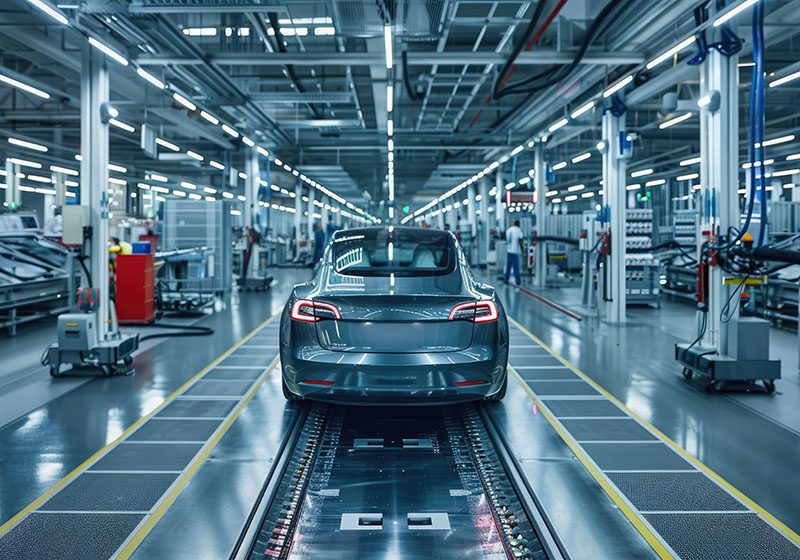
ABS plastic fabrication is commonly used in both everyday products and industrial applications, with the examples above representing just a fraction of its versatility. At KingStar Mold, we have extensive expertise in ABS injection molding, including working with modified ABS materials such as PC+ABS, ABS+PA, ABS/PBT, and Flame-Retardant ABS.
ABS Plastic Solutions
Our ABS Plastic Parts Production Capabilities
Tailored Material Solutions
At KingStar Mold, we provide customized ABS injection molding solutions designed to meet the specific requirements of our clients. We customize ABS to ensure optimal performance for your unique applications by adjusting properties such as toughness, fire resistance, and UV durability. Our team works closely with you to ensure the material properties align perfectly with your project’s demands, delivering high-quality, reliable results every time.
Expertise Across Industries
Our ABS composite molding serves a wide range of industries, including automotive, healthcare, consumer electronics, and more. From automotive parts to medical devices, we deliver ABS solutions that combine functionality with aesthetic appeal.
Precision Molding & Quality Assurance
With an integrated approach that includes in-house mold design, advanced finishing techniques, and stringent quality control, KingStar Mold ensures every ABS part is crafted with precision, exceptional aesthetics, and lasting quality.
Key Benefits of Choosing KingStar Mold for ABS Molding
ABS injection molding offers a range of advantages, making it an ideal choice for many applications.
Strength and Accuracy: ABS parts provide the impact resistance and dimensional stability needed for components such as dashboards, bumpers, and complex parts, ensuring both durability and precision.
Design Flexibility: ABS can be finished to a high standard, making it perfect for products that require both functionality and aesthetic appeal, such as toys, household appliances, and healthcare devices.
Cost-Effective for High-Volume Production: Thanks to its ease of processing and recyclability, ABS is an excellent material for industries like construction and packaging, where producing large quantities of durable, high-precision parts at a low cost is essential.
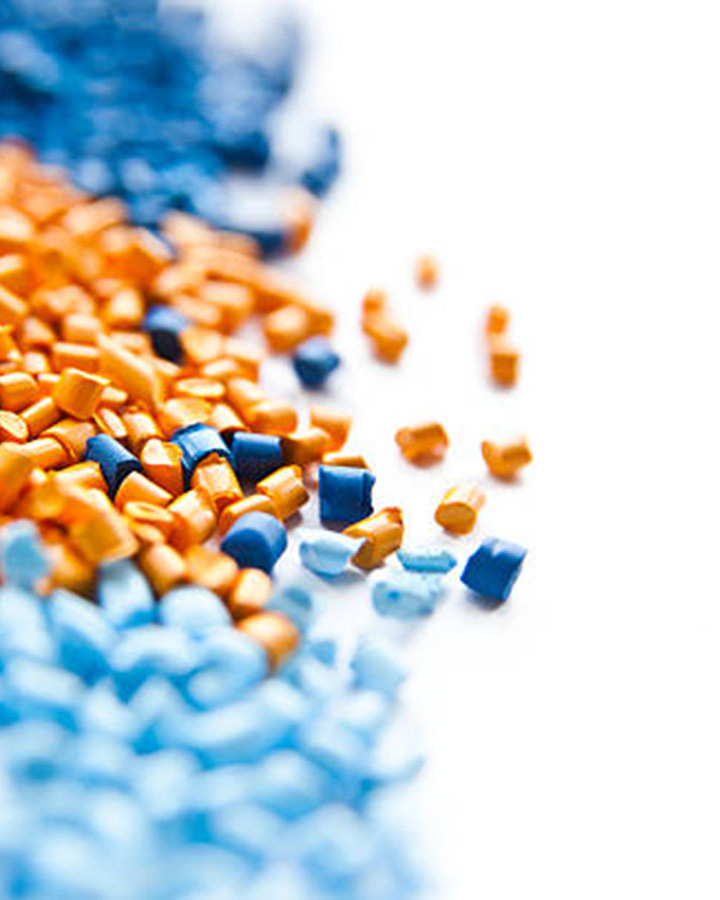
According to statistics, ABS is the most widely used material in all injection molding projects at KingStar Mold.
ABS Injection Molding Cases
Custom ABS molding requires careful drying and process control to prevent moisture-related defects, warping, and shrinkage, along with precise mold design to guarantee high-quality finishes and part integrity. This process demands the expertise of skilled engineers and advanced machinery to ensure optimal results.
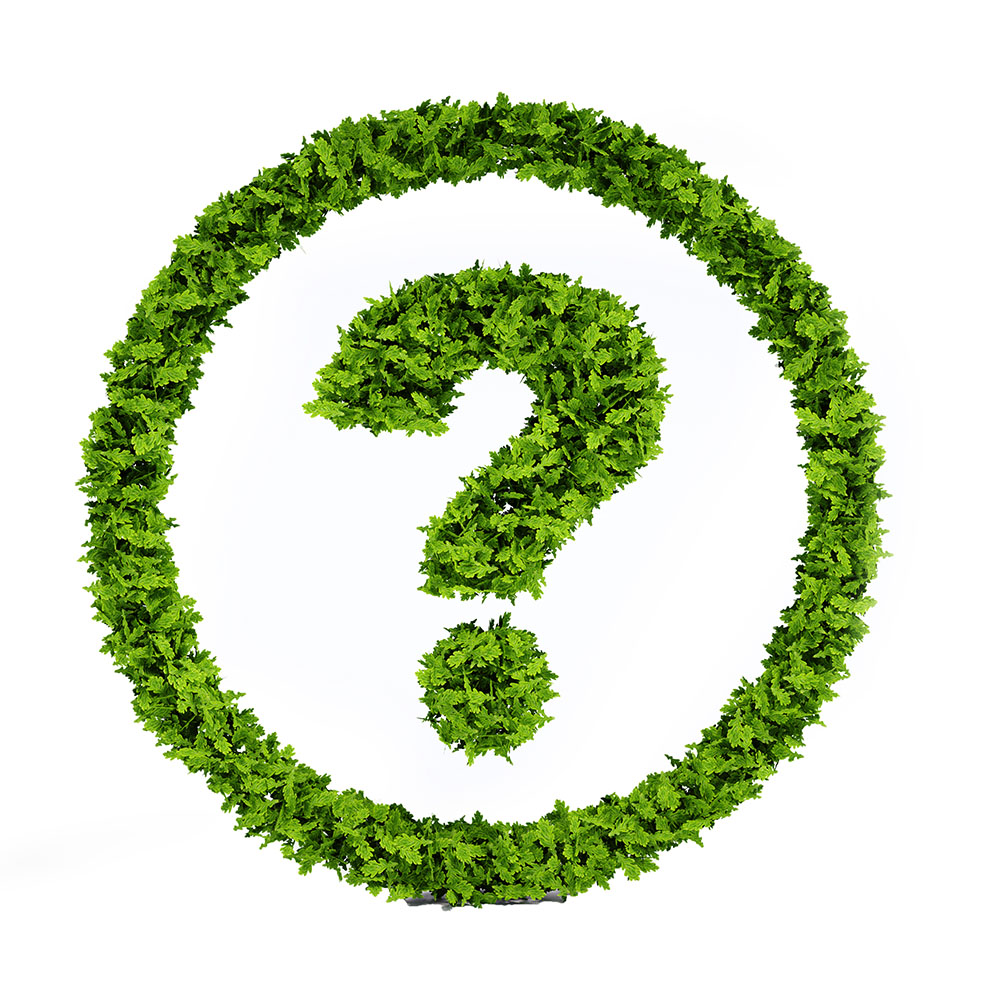
ABS is ideal for applications that require durability, strength, and a smooth finish, such as automotive components, electronic housings, and household appliances. Its excellent impact resistance and ease of processing make it a versatile choice across various industries, particularly for parts that need a high-quality appearance and structural resilience.
ABS on its own is not naturally UV resistant and may degrade when exposed to sunlight over time. For applications that require UV resistance, we recommend adding UV stabilizers or using UV-resistant grades of ABS. This ensures that the parts maintain their appearance and structural integrity even with prolonged exposure to UV rays.
To enhance impact resistance, selecting high-impact grades of ABS resin is a good starting point. Furthermore, modifying the mold and adjusting the cooling rate can help achieve the desired toughness. Our engineers work with clients to identify the right material grade and optimize processing conditions to meet specific impact requirements.
Inconsistent surface finishes in ABS parts can result from uneven cooling or inadequate mold temperature control. To improve this, we ensure precise control of mold temperatures and optimize cooling times. Regular mold maintenance and polishing also help in achieving smooth, uniform surfaces for a high-quality finish.
ABS injection molded products may face defects such as surface blemishes, weld lines, or warping. To address these, we suggest careful material preparation and pre-drying to reduce moisture, adjusting the molding temperature, and ensuring proper mold design to achieve smooth, uniform parts. Additionally, our engineers optimize processing conditions and cycle times to maintain high-quality standards.
Improving the ABS injection molding process can be achieved through several strategies, such as increasing injection speed, lowering mold temperature, and fine-tuning barrel temperature. These adjustments can boost production efficiency while maintaining high product quality. Further gains can be realized by optimizing mold design and refining raw material formulations. The goal is to maximize efficiency without compromising the appearance or performance of the final product.
Yes, ABS coloring can sometimes lead to slight variations or dullness if not handled correctly. We recommend choosing standard color formulas or conducting color tests prior to production. Our team also uses advanced color-matching techniques and carefully monitors the molding process to achieve vibrant, consistent colors in your products.
Yes, ABS is suitable for intricate and thin-walled designs. By adjusting injection pressure and ensuring a precise flow rate, we achieve optimal fill for complex designs. Our engineers carefully design the molds to prevent issues like short shots or incomplete fills in thin-walled or detailed areas.
ABS is widely used for high-impact applications, and KingStar Mold ensures optimal strength by selecting high-quality ABS grades and adjusting the molding parameters. By using slower cooling and appropriate injection pressures, we enhance the impact resistance of ABS parts, making them suitable for demanding applications such as automotive interiors and durable consumer goods.
ABS is versatile but has some limitations regarding thin-wall designs or parts with complex geometries. To accommodate these designs, we adjust the molding parameters and use advanced mold flow simulations. Our engineering team collaborates closely with clients to ensure that even complex designs are manufacturable without compromising the integrity or quality of the final product.