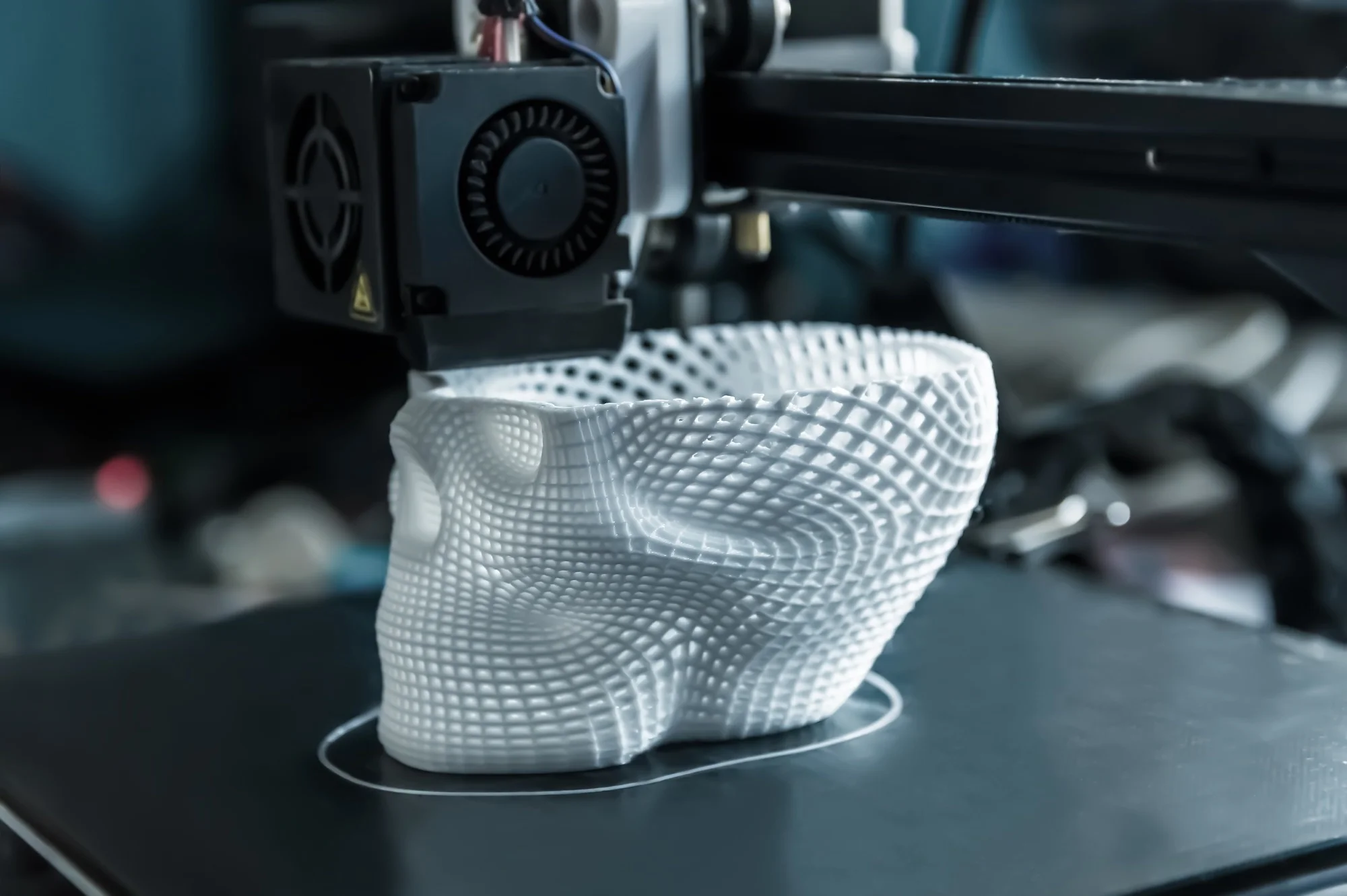
Advanced 3D Printing for Rapid Prototyping and Custom Parts
Precision, Flexibility, and Efficiency in Every Layer
At KingStar Mold, we provide cutting-edge 3D printing services for rapid prototyping and custom parts. Our technology ensures high precision, quick turnaround, and flexibility to work with a wide range of materials, enabling fast design validation and cost-effective production.
Ideal for low-volume runs, our 3D printing service delivers functional, high-quality parts with minimal lead time. Whether for automotive, medical, or consumer goods, we offer tailored solutions to meet your specific needs with precision and efficiency.
10Y+
Experience
10+
3D Printers
200+
Satisfactory Cases
Comprehensive 3D Printing Solutions
Precision, Speed, and Versatility for Every Project
Technology | Maximum Build Volume | Typical Lead Time | Dimensional Accuracy | Best for Prototyping | Suitable for End-Use |
---|---|---|---|---|---|
SLA | 533mm x 635mm x 736mm | 2 days | ± 0.2% with a minimum of ± 0.13 mm | High-detail visual models | Small, non-functional parts with aesthetic needs |
SLS | 482mm x 482mm x 431mm | 3 days | ± 0.3% with a minimum of ± 0.3 mm | Durable plastic prototypes for testing | Functional low-volume plastic components |
DMLS | 500mm x 800mm x 400mm | 3 days | ±0.3 mm | Metal parts with complex features | Strong, functional metal components in limited runs |
MJP | 294 x 211 x 144 mm | 2 days | ±0.1 mm | Highly detailed small-scale prototypes | Small batches of high-resolution parts |
FDM | 609.6mm × 914.4mm × 914.4mm | 2 days | ± 0.3% with a minimum of ± 0.3 mm | Proof-of-concept and utility prototypes | Non-aesthetic functional parts like fixtures and jigs |
MJF | 294 x 144 x 211 mm | 4 days | ±0.3 mm | Functional and accurate prototypes | Short-run plastic parts needing strength and precision |
Why Choose KingStar Mold
High Precision and Detail
Our 3D printing technology delivers exceptional accuracy and fine details, ensuring that even the most complex designs are faithfully recreated. Whether you’re prototyping or producing custom parts, you can rely on us for precise, high-quality results.
Fast Turnaround and Flexibility
We offer quick turnaround times for both prototypes and production parts, helping you meet tight deadlines without compromising on quality. Our versatile 3D printing services allow for rapid iteration and customization, adapting to the specific needs of each project.
Cost-Effective Solutions for Low-Volume Production
With 3D printing, you can produce high-quality parts in small quantities without the high upfront costs of traditional manufacturing methods. We provide cost-effective solutions for low-volume production, making it easier to bring your designs to market quickly and affordably.
3D Printing Materials
Process | Materials Commonly Used |
---|---|
SLA | Standard resins, heat-resistant resins, and other photopolymers (including digital photopolymers) |
SLS | PA12 (nylon), glass-filled nylon, thermoplastic elastomers like TPU |
DMLS / SLM | Aluminum alloy (AlSi10Mg), stainless steel (316L) |
FDM | PLA, ABS, ASA, polycarbonate, and similar thermoplastics |
MJF | Polyamide 12 (PA12) powder |
MJP | Clear rigid materials like MG2-CL |
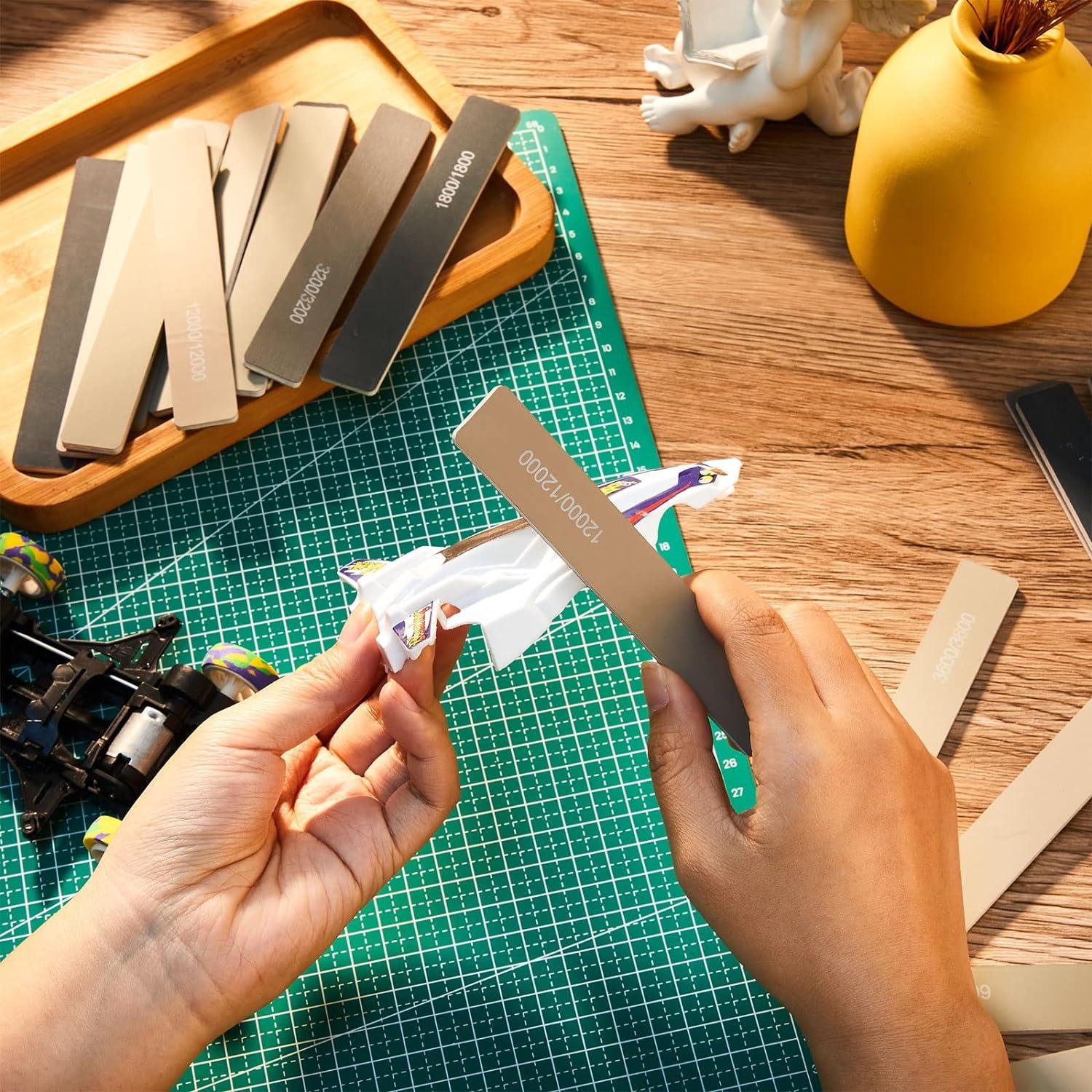
3D printing surface treatment
Available Treatment
Sanding and Polishing
Achieve a smooth, refined finish with sanding and polishing, removing layer lines for a professional, high-quality appearance. Ideal for prototypes and consumer-facing products.
Vapor Smoothing
Create a glossy, seamless finish with vapor smoothing, reducing layer lines for a sleek, high-quality surface ideal for detailed prototypes and consumer products.
Painting and Coating
Enhance the look and durability of your parts with our painting and coating services, providing vibrant color and added protection for both aesthetics and function.
Dyeing
Customize your 3D printed parts with vibrant, uniform colors using our dyeing services, perfect for materials like nylon without compromising strength or durability.
Electroplating
Add a durable metallic finish to your parts with electroplating, improving both appearance and strength for enhanced functionality in demanding applications.
Industrial 3D Printing with KingStar Mold
KingStar Mold offers a wide array of 3D printing solutions tailored for various applications, ranging from one-off rapid prototypes to batch production of functional parts and larger-scale manufacturing. Our advanced 3D printing services allow you to produce parts quickly and cost-effectively, accelerating your innovation process and reducing time to market. Whether you’re looking to create intricate components, test prototypes, or scale up production, we provide flexible and efficient solutions to meet your needs.
Criteria | SLA | SLS | DMLS | MJP | FDM | SLM | MJF |
---|---|---|---|---|---|---|---|
Material Options | ★★★ | ★★★★ | ★★★ | ★★ | ★★★★★ | ★★★ | ★★★★ |
Geometry Complexity | ★★★★ | ★★★★★ | ★★★★★ | ★★★ | ★★★ | ★★★★★ | ★★★★★ |
Batch Discount | ★★ | ★★★★ | ★★ | ★★ | ★★★★★ | ★★ | ★★★★ |
Scalability | ★★★ | ★★★★ | ★★★ | ★★ | ★★★★★ | ★★★ | ★★★★ |
Precision Tolerance | ★★★★ | ★★★ | ★★★★★ | ★★★★★ | ★★ | ★★★★★ | ★★★★ |
Fine Details | ★★★★★ | ★★★ | ★★★★ | ★★★★★ | ★★ | ★★★★ | ★★★★ |
Large Parts | ★★★★ | ★★★ | ★★ | ★★ | ★★★★★ | ★★★ | ★★★ |
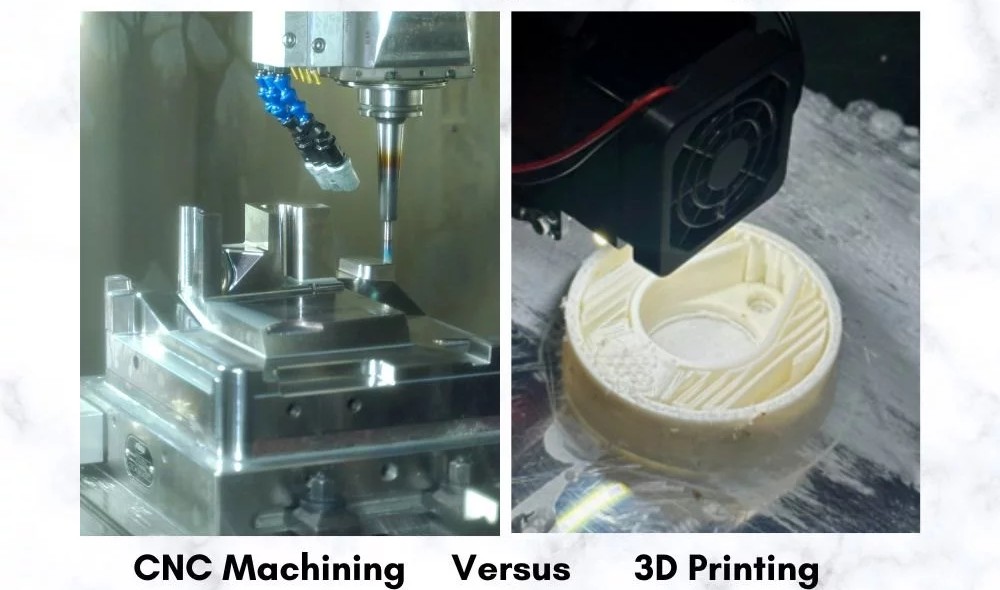
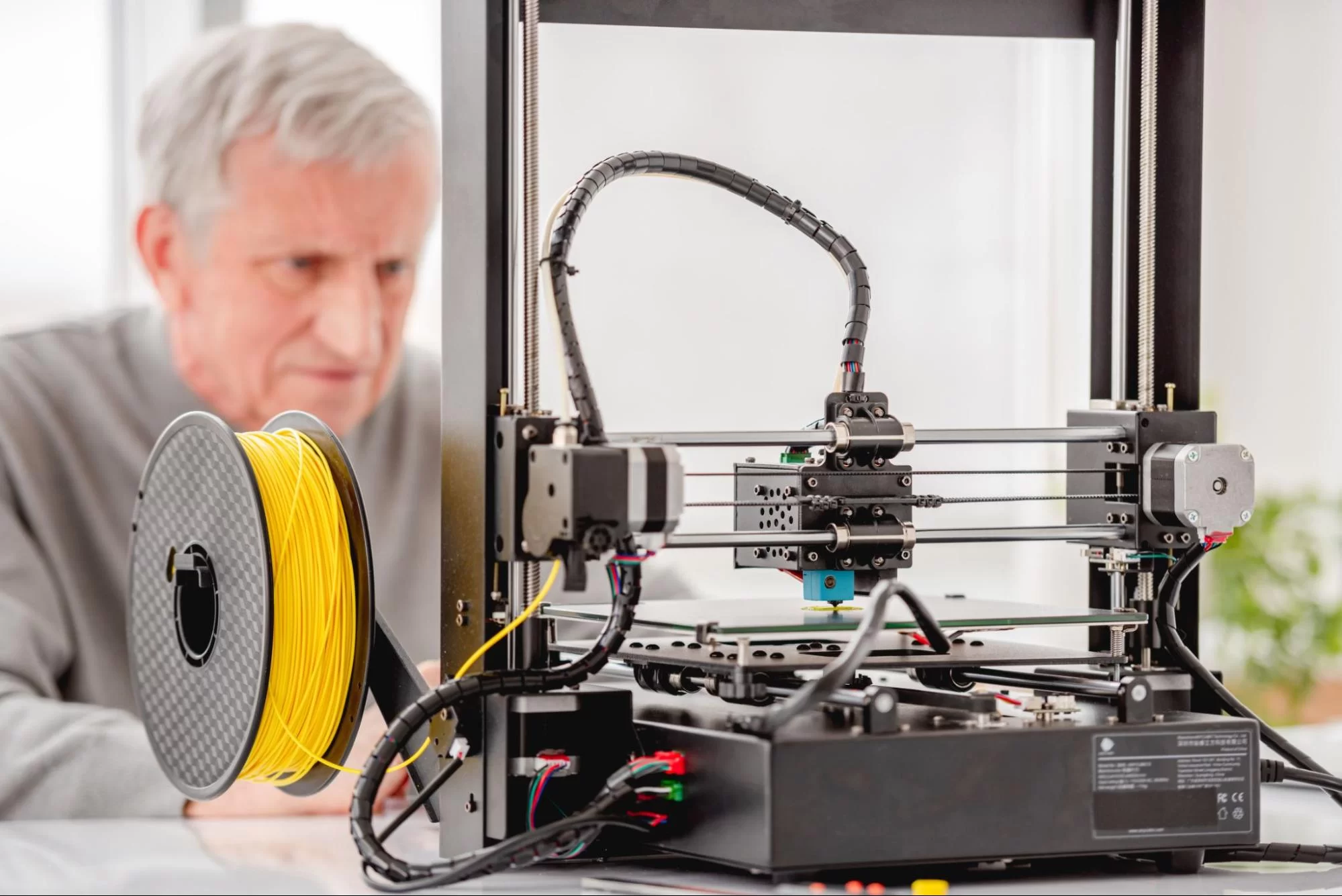
Design For 3D Printing
Thanks to its layer-by-layer approach, 3D printing offers far greater design flexibility compared to traditional methods. To fully leverage the capabilities offered by KingStar’s advanced 3D printing services, it’s essential to tailor your model specifically for additive manufacturing.
Design Guide for FDM (Fused Deposition Modeling) 3D Printing
Comprehensive Design Guidelines for SLA 3D Printing
Fused Powder Design Tips: SLS 3D Printing Guide
Best Practices for MJF (Multi Jet Fusion) Part Design
High-Resolution Design for MJP (MultiJet Printing) 3D Printing
Metal Additive Manufacturing: Design Considerations for DMLS
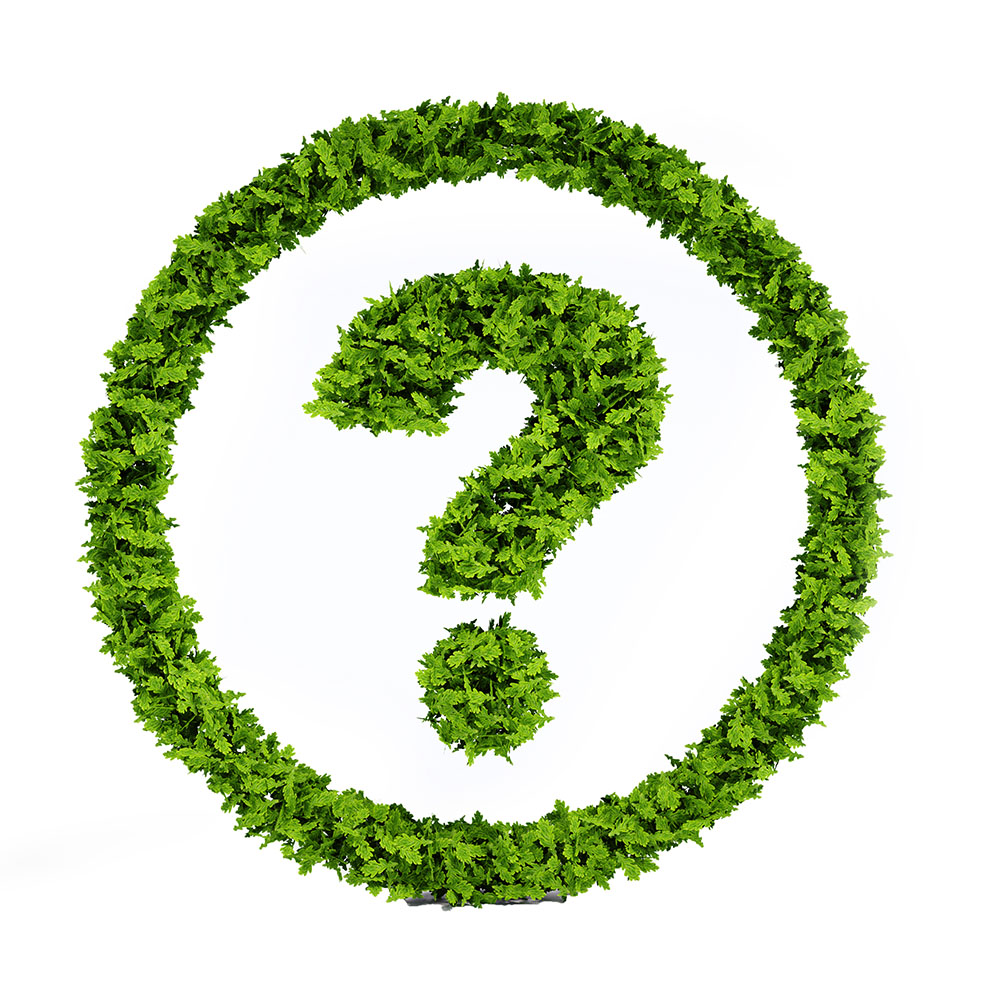
Frequently Asked Questions
After a metal part is 3D printed, it typically requires several post-processing steps to improve its surface finish, strength, and functionality. Common post-processing methods include support removal, heat treatment, surface polishing, and sometimes machining. Heat treatment is often necessary to relieve stresses and improve the material properties of the part. Depending on the application, these steps may be crucial to ensuring the part meets performance and aesthetic standards.
The cost of 3D printing metal parts varies depending on several factors, including the complexity of the design, the material used, and the size of the part. Generally, metal 3D printing can be more expensive than other forms of additive manufacturing due to the high cost of materials (metal powders), specialized equipment, and post-processing requirements. For a basic metal part, costs can start in the low hundreds of dollars, but more complex parts or larger volumes can increase the price significantly.
KingStar Mold offers fast turnaround, high-quality 3D printing solutions, and personalized service. Whether you need prototypes, functional parts, or small-batch production, KingStar Mold ensures precision and cost-effective solutions tailored to your needs.
SLA (Stereolithography) uses liquid resin that is cured by a laser, producing high-precision models. SLS (Selective Laser Sintering) uses a laser to sinter powdered material, often used for stronger parts. FDM (Fused Deposition Modeling) extrudes filament layer by layer, commonly used for prototyping and low-cost applications.
The lead time for 3D printed parts varies depending on the production type. For prototype production, you can expect a quick turnaround of 1 to 3 days, as it’s designed for rapid design validation using technologies like FDM or SLA. Functional prototyping typically takes 3 to 7 days, requiring higher precision and performance materials like those used in SLA, SLS, or metal 3D printing. Low-volume production takes a bit longer, generally 7 to 14 days, due to additional preparation and post-processing, with SLS, MJF, or MJP being ideal technologies. For high-volume production, the lead time is the longest, typically 2 to 4 weeks, as it involves larger quantities and more extensive post-processing, with technologies like metal 3D printing or SLS being commonly used. KingStar Mold provides 3D printing services for all types of production, delivering high-quality results with timely turnarounds.